- Mahindra & Mahindra
- Super League Kerala
- Mahindra Super League Kerala
STRATEGIC EVOLUTION
- by 0
- April 22, 2020
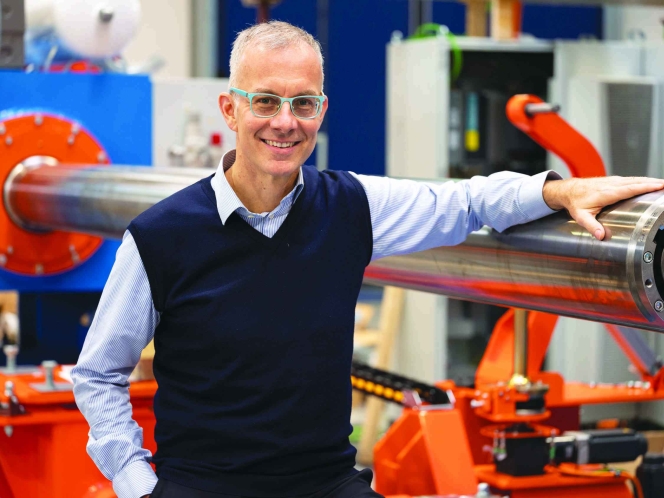
TT NEWS
Marangoni Meccanica, the leader in tyre assembly machinery design and production, has undergone a re-branding. It is now Marangoni Machinery. The new corporate brand identity comes at a time when the company, which was recently recapitalised and spun off from the Marangoni Group, is evolving through a strategic journey with the objective of offering to its customers an even more powerful support and commitment.
The company has been a leader in the market for long and has a unique brand identity. Marangoni says the new branding reflects the company’s market-leading position better and demonstrates the comprehensive lifecycle of machinery and services offered to its customers across the globe. The new brand Marangoni Machinery and its new logo work well across digital and physical channels. “They evoke a feeling of ideas, dynamism, collaboration, movement, positivity, speed—and velocity, which work all together for obtaining the highest quality and satisfaction for the customers,” Ricardo Mastronardi, the new CEO, says.
“Marangoni Machinery has a unique value proposition in the global tyre industry, especially in the big tyre segments like Agriculture and OTR. We are driven by a continuous Customers focus: each new feature is designed to support Customer’s growth and performance, oriented to best efficiency and quality, Mastronardi told Tyre Trends
Foreseeing and inventing new solutions
Research is an activity of fundamental importance for Marangoni Meccanica. The company’s collaboration with the Department of Industrial Engineering of the University of Trento - Laboratory of Maieutics, allows sharing knowledge and skills that can greatly improve the technical culture of its designers. The project ‘Marangoni Station - New Generation’ aims at creating software that can be used on a variety of IT media

The company’s main activity is the design and manufacturing of machines and technologies related to the production of new tyres, mainly machinery for tyre building of Agricultural and OTR tyres industry.
Within the flow of activities that lead to the creation of a product, research is an area of fundamental importance. The ability to match the customer's needs and, if possible, to foresee them by inventing new solutions is Marangoni Meccanica’s core strength.
The company designs around the customer’s needs, searching for new solutions to address improvements, optimisation and coming industry challenges an eventually find out new needs and anticipate what the market will require in the coming years.
Software solution

Most of the companies in its customer portfolio are not equipped with integrated supervision systems, especially for the production process. Those companies simply exchange data within their databases regarding the manufacturing process aspects, for example recipe data loading necessary for machine work, neglecting the aspects related to the plant components. Those topics are usually managed in a traditional way, not integrating the new production technologies that allow improving the working conditions by increasing the productivity and the production quality of the plants.
Being a partner who can cooperate, apart from being a mere supplier, even in the areas of plant management, is a distinctive aspect that no competitor is currently able to provide. The Company can customise and enhance the essential engineering functions for its applications, such as the total integration of external software tools developed with research institutions for satisfying the most demanding customers.
For the development of this new powerful software platform, Marangoni Meccanica has started an important collaboration with the Department of Industrial Engineering of the University of Trento - Laboratory of Maieutics, which will allow sharing knowledge and skills that can greatly improve the technical culture of its designers. The Department research group has been working for many years on the development of technologies, so it is an important reference in the industrial engineering field, having the advantage to count on the skills of all the project members within the company. The project consists of software writing for industrial automation components, characterised by a strong inter-disciplinarity among sectors such as user interfaces, industrial process engineering, communication networks and software design.

Reasons underlying the research
The modern scenario of industrial plants requires an ever-increasing level of integration of functions such as data communication management, operator-machine interfaces, data processing and connections to company systems for production and maintenance management. Industry 4.0 responds to the latter needs, as this new industrial revolution aims to develop data communication networks via the Internet and similar networks. This project adheres to the basic values of this new development context, namely the development of machine data management systems (SCADA - Supervisory Control And Data Acquisition), data analysis and communication on data networks, as well as creating interfaces for the operator of the production plants (HMI - Human Machine Interface).
Therefore, supervision and control software play a fundamental role in the management of complex machines and systems.
HMI and SCADA are two terms closely related to the extent to which an operator is an integral part of the components of a plant management system.
HMI and SCADA

Human-Machine Interface (HMI) is a control panel designed for interactive communication between the operator and the process / machine carrying out the tasks of entering orders, display the results connected to the process / machine status in real time. Moreover the Marangoni Machinery vision is to let HMI to become an effective gate to get access to the whole production machines even into a network and/or stand-alone mode: in such a way the Customers can have access to a variety of information (operations, maintenance, alarms etc.) to enhance the production lines to be in real-time controlled.
SCADA system is a Supervision, Control and Data Acquisition System. It is also referred to as 'telemetry,' a system having a full data communication and data control, which includes two-way communication (measurement and control) between the process system and the operator's position. In addition to this, the capacity of SCADA systems to control and monitor multiple devices, such as remote terminal units (RTUs) connected with process transmitters and final control devices, implementing basic control functions such as Start / Stop, or multiple regulation circuits including safety shutdowns, warning, notice, or PID controllers, allow the RTU devices to communicate digitally with a Master Unit (MTU) terminal in a central position where operators can monitor the process and intervene in it.
This HMI SCADA software is used in all sectors with the aim of providing a direct means of machine control, automation, security, data storage, analysis, and communications as well as allowing connectivity to a wide range of functions within the system.
In a few words the HMI software is used to monitor SCADA systems.
Customers have been increasingly demanding SCADA / HMI systems with the following features:
1. Improve control and monitoring of the process, system or plant.
2. Manage important information, such as warnings, alarms, machine shutdown, and increase productivity by decreasing shutdowns. Analysing data in real time in order to prevent unexpected stops, and resume activity more quickly.
3. Simplify the interaction between systems of different manufacturers with proper communication modes.
4. Optimise the effectiveness of user control on data and help with alarms or data groups to know the status of the system and the possible problems.
5. Enhance the quality for the correct functioning of the system.
6. Reduce operating costs through the integration and the maintenance of the process and plant.
It consists of additional software to complement our supply of machines and plants whose complexity requires systems allowing a more intuitive and quick management control, helping our customers to monitor the process in real time, especially remotely through communication networks (data, videos, etc.).
.jpg)
Aim of the Project
This project aims to create an HMI / SCADA software platform offering:
- A user-friendly application in terms of persistence, business logic, graphic interface;
- The use of technologies for the creation of architectures and software structures that guarantee the optimisation of software writing and maintenance, through proper software patterns;
- The creation of responsive software allowing their use on multiple web browsers and various platforms (PC, tablet, mobile);
- The creation of suitable documentation both for the upstream analysis of the engineering process and for the control of the final product.
Goals
The result of the project is the creation of a development environment consisting of a series of applications able to:
- manage basic recipes for each type of machine
- communicate with the PLC by managing the flow of information that starts and arrives from it.
- have a graphical interface (HMI) that can be easily used in all the application contexts (design, control, monitoring, visualizations, reporting).
- allow the use on multiple web browsers and various platforms (PC, tablet, mobile) at the highest possible application level.
Basically, Marangoni Meccanica customers ask for a support where, in addition to providing machines and systems, it can integrate product with their "company system," allowing an easy, functional use even by staff whose level of specialisation is not uniform. Hence the success of this project is to have a tool enabling the company to be for its customers more and more a partner, and not only supplier.
Interview
Perfectly in lane for era of transformations
Over the next five years, the industry is poised to enter a transformative era. Marangoni Machinery (MM), global tyre industry leader, especially in Agriculture and OTR segments, is perfectly positioned and prepared to play a leading role in this evolving context, “thanks to our creativity, flexibility and engineering innovation capabilities, assures the company’s CEO Riccardo Mastronardi
TT Report

What drives you to start afresh as a new entity? How much do you think Marangoni Machinery impact global tyre industry?
Marangoni Machinery (MM) has a great technological background and exceptional innovation and engineering capabilities. The new shareholders clearly perceived that this potential in the last years has been partially untapped and big opportunities were ahead of us, therefore they decided to invest. MM has a unique value proposition in the global tyre industry, especially in the big tyre segments like Agriculture and OTR. We are driven by a continuous Customers focus: each new feature is designed to support Customer’s growth and performance, oriented to best efficiency and quality.
How does Marangoni Machinery see the tyre industry evolving in the coming decade?
Technology innovations and developing end-user requirements are driving the off-the-road tyres market into unexplored territory, presenting fresh challenges to manufactures and suppliers. The global market for off-the-road (OTR) tyres is estimated to significantly grow in the next years.
Technological advancements and market changes in the OTR tyre industry are presenting several challenges to manufacturers and suppliers. From an end user’s perspective, the imperative is to continue to drive efficiency and productivity, even as equipment gets larger and places additional stress and performance demands on the tyre.
Over the next five years, the industry is poised to enter a transformative era and we in MM believe to be perfectly positioned and prepared to play a leading role in this evolving context, thanks to our creativity, flexibility and engineering innovation capabilities.
What is your added strength in R&D and also in business development?
MM R&D is oriented to a new Customer’s experience approach. The new machines are tailor designed according to Customer’s needs and requirements in order to achieve the best quality output, and at the same time best reliability, safety and productivity.
.jpg)
As customer demand and technology developments change, what challenges do you foresee in providing tyre making machinery?
Main challenges are about time to market and installed base refurbishment: nowadays Customers are looking for renewal plans to get new machines within short lead times, plus new equipment oriented to increase productivity for premium products as well, so our challenge is to be ready for both business needs by serving Customers on reduced lead-time and on increased quality output.
What new products do you plan to offer?
MM is mainly oriented to “turn-key systems”: from complete Tyre Building Machines up to all comprehensive “Production Site” composed by multiple production units with software supervision platform to get an integrated and efficient management manufacturing system architectures. About new products MM is offering new tyre building core technologies (drums, toolings and robotics) to enhance the tyre productivity and quality by proprietary patents and proven solutions, mostly oriented to Agro and OTR industry areas (Stage-1, Stage-2 and Unistage solutions with Strip-Winding embedded architectures).
Any move to widen your network of sales and after-sales services?

We are definitely strengthening our Sales and After Sales Organisation in order to better satisfy our growing Customer Base. We are also planning to internationalize our After Sales Services to be closer to our Customers’ production facilities and serve them better and quicker.
Are there any new areas in tyre industry that Marangoni Machinery plans to cover?
As said above, our company is characterised by our strong and distinctive engineering capabilities. Those capabilities allow us to tackle disparate challenges and solve them in a creative, effective and efficient way. Our deep knowledge of the Tyre Industry together with our distinctive capabilities, open for us unexploited opportunities that we plan to explore in the next years.
What other new elements have been included in the new entity?
We are in the process of transforming a family owned business into a structured and managerial modern company where M&A opportunities will be also explored.
What is your take on the general economic slowdown, particularly in the Asian markets?
Frankly speaking, till now, we are not experiencing any slowdown in our business leads, especially in Asia. In our Agriculture and OTR segments in Asia we experience a significant growth led by China and India, supported by all end-use sectors; much of the gain in radialisation is seen in this region; mechanisation of agriculture is definitely a major growth driver. We need to carefully consider the significant threat to global economic growth amid coronavirus outbreak
Do you see the new regulations in import/export in some markets impacting your business?
Not yet, potentially yes, even if our solutions are not so easily replaceable and customers loyalty is very high.
- Apollo Tyres
- R&D
- EV
- Daniele Lorenzetti
Apollo Tyres: Driving the Future Of Mobility Through Cutting-Edge R&D
- by Daniele Lorenzetti
- March 03, 2025
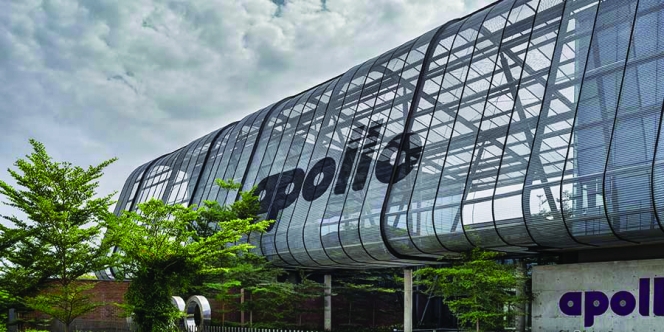
The future of mobility is poised for a revolutionary transformation driven by emerging technologies and changing consumer demands. With an increasing shift towards electrification, autonomous driving and connected ecosystems, the automotive industry is evolving rapidly. Electric vehicles (EVs) are becoming more mainstream, reducing carbon footprints and promoting sustainability. At the same time, advancements in artificial intelligence (AI), machine learning and data analytics are enabling smarter vehicles that can adapt to real-time conditions, enhance safety and provide seamless user experiences. Additionally, the integration of shared mobility solutions, such as ridesharing and autonomous fleets, promises to reshape urban transportation, making it more efficient and reducing congestion. As sustainability becomes a central focus, the future of mobility will also involve the development of greener materials, eco-friendly technologies and circular economy practices that minimise waste and maximise resource efficiency, paving the way for a cleaner, smarter and more connected world.
As the automotive world embraces transformative trends like electrification, sustainability and digital connectivity, Apollo Tyres stands at the forefront, driving innovation with its cutting-edge R&D. With a legacy of pioneering breakthroughs, Apollo’s commitment to shaping the future of mobility is grounded in a holistic approach that blends advanced technologies, sustainability and performance excellence.
Historically, Apollo Tyres has consistently delivered products tailored to diverse market demands. Its R&D operations in India and Europe synergise global expertise to innovate solutions for traditional and electric vehicles. Today, Apollo leads the industry with adaptable tyre platforms and technologies designed to meet the unique requirements of EVs, featuring low rolling resistance, noise reduction, traction and durability enhancements. Innovations such as real-time tyre sensors and noise-cancelling technologies further define the company’s reputation for excellence.
Looking ahead, Apollo Tyres is championing a sustainable future through material innovation and digital transformation. The company integrates renewable and recycled materials, collaborates with leading universities to explore eco-friendly alternatives and advances tyre retreading and circular economy principles. These efforts culminate in passenger vehicle prototype tyres composed of 75 percent sustainable materials, showcasing Apollo’s commitment to environmental stewardship. Meanwhile, digital tools such as virtual prototyping and AI-powered analytics accelerate R&D cycles, ensuring responsiveness to emerging trends.
Apollo Tyres envisions a mobility landscape where tyres transcend their functional role, becoming integral to vehicle connectivity and safety. By leveraging intelligent technologies like Tyre Pressure Monitoring Systems and sensor-enabled diagnostics, Apollo is redefining the tyre’s role in connected ecosystems. Through relentless innovation, Apollo Tyres not only aligns with the future of mobility but actively drives it forward. The R&D vision is to create value to customers by developing products and technologies that are best in class in performance while being profitable to business and sustainable to environment.
THE STRATEGY FOR 2026 IS BUILT ON THE FOLLOWING THREE PILLARS
- 1. Developing advanced tyre technology tailored for traditional and electric vehicles.
- 2. Embracing circular economy principles by integrating renewable and recycled materials.
- 3. Harnessing AI and virtual development tools to accelerate innovation in testing and material science.
Apollo’s investment in R&D has grown to around 2 percent of revenue. With a relentless focus on innovation, sustainability and customer satisfaction, Apollo is poised to continue its journey as a global leader in the tyre industry.
GLOBAL R&D TEAM: A SYNERGISTIC APPROACH
Our global R&D operations are strategically located in Chennai, India and Enschede, The Netherlands. These two centres integrate local expertise with advanced global technologies, addressing diverse market needs. Whether it’s the tropical climate and varied road conditions in India or the high-performance demands of European consumers, our R&D team tackles challenges with a unified approach. With state-of-the-art infrastructure, including advanced material research facility, raw material, predevelopment and simulation technologies, design, testing, advanced engineering, intellectual property, process and product development, Apollo Tyres delivers innovative tyre designs that address both regional and global demands.
ADVANCED MATERIAL RESEARCH AND SUSTAINABILITY INNOVATIONS
At Apollo, sustainability begins with material innovation. We are replacing conventional tyre components with eco-friendly alternatives. Collaborations with leading universities explore nano cellulose as a sustainable substitute for carbon black. Partnerships with Tyromer have revolutionised the quality of recycled rubber through cutting-edge devulcanisation techniques. On top we have signed collaboration projects with Asian premier institutes on bio degradation of ELT. Additionally, we promote natural rubber sustainability through plantation certifications, traceability programmes and education initiatives, achieving ISCC certification in our plants. Our material research extends to bio-based and recycled raw materials that enhance material sustainability. Advanced analytical tools enable precise characterisation of smart materials, supporting breakthroughs in polymer and filler technologies. Our tailored compounds ensure low rolling resistance, high traction and noise reduction, while delivering superior performance across all applications.
PREDEVELOPMENT AND VIRTUAL PROTOTYPING TECHNOLOGIES
Innovation is the heartbeat of Apollo Tyres. Our predevelopment teams integrate groundbreaking technologies, setting new benchmarks in the industry. FOAM technology exemplifies this spirit, reducing cavity noise for EVs without compromising on durability. This technology addresses the evolving needs of OEMs. Our sustainability-driven initiatives include ultra-low rolling resistance tyres with a rolling resistance coefficient of just 5.5 kg/tonne. Lightweight Truck Bus Radial tyres with a 10 percent weight reduction highlight our focus on environmental stewardship and performance innovation. Across all R&D locations, our focus on high performance drives tyre innovation. Advanced Computer-Aided Design (CAD) tools and real-world simulations help optimise tyre designs for diverse terrains. Detailed aerodynamic analyses further enhance fuel efficiency in vehicles, ensuring superior grip, handling and noise reduction. By leveraging virtual prototyping, we accelerate development cycles, optimising characteristics like rolling resistance, grip, comfort and noise.
INTELLECTUAL PROPERTY
Our Intellectual Property (IP) teams has played a crucial role in safeguarding and advancing the prosperity of our company. Our IP team is tasked with recognising, securing and utilising our intellectual property assets to strengthen our competitive edge and generate lasting value for our stakeholders.
The following are some of the key achievements:
- 1. 25 patent applications were filed in FY24.
- 2. A total of 200+ active patents across geographies.
- 3. 29 design registrations filed in FY24.
- 4. A total of 300+ design registrations across geographies.
Our Intellectual Property (IP) team has cultivated an innovative culture within our organisation by encouraging employees to adhere to best IP practices, leading to the creation of high-value patents and designs. Consequently, we have generated new intellectual property assets and bolstered our product development capabilities.
ADVANCED TESTING EXCELLENCE
Testing is integral to ensuring the safety, performance and durability of our tyres. Our test facilities feature cutting-edge equipment that validates products under diverse conditions:
Flat-Trac Machine: This sophisticated tool measures force and moment properties, aiding in the design of high-performance tyres.
Anechoic Chamber: Simulating various road conditions, this chamber evaluates tyre noise levels, ensuring quieter and more comfortable rides. We have developed dedicated testing protocols for EVs, focusing on rolling resistance and noise reduction. The newly established Cut and Chip track at NATRAX, Indore, is designed to test tyres under extreme conditions, evaluating durability, uptime and grip. Through experiential drives, we showcase our technological prowess to fleet owners, business partners and media.
INTEGRATING TYRES INTO FUTURE MOBILITY THROUGH ADVANCED ENGINEERING
Apollo Tyres is at the forefront of revolutionising mobility through advanced engineering aligned with key megatrends like sustainability, connected vehicles and autonomous driving. Our intelligent tyres, equipped with sensors, telematics and software, enable seamless communication of vehicle conditions. Tyre Pressure Monitoring Solutions (TPMS), deployed in our tyre as service AVOLVE programme, enhance safety, reduce fuel consumption and provide remote diagnostics. The tyre of tomorrow will not just be a component but a critical element in the vehicle’s connectivity and safety systems.
ADVANCING INNOVATION THROUGH STRATEGIC COLLABORATION
Our R&D endeavours are grounded in robust partnerships with prestigious academic institutions that include both Indian and European universities. Apollo Tyres is also participating in consortium research on pre-competitive technologies. It is also worth mentioning that Apollo Tyres is also actively engaging with our supplier partners and customers to deliver cutting-edge technologies, products and services.
ADDRESSING TECHNICAL CHALLENGES AND INDUSTRY TRENDS
The automotive sector is undergoing rapid regulatory changes, including Europe’s Green Deal and Euro 7 standards. These developments demand stricter compliance with emission and mileage requirements, accelerating the adoption of EVs. Apollo’s R&D efforts address these challenges by focusing on sustainable materials and advanced technologies. Circular economy initiatives, such as tyre retreading and recycling-friendly compounds, reduce waste and maximise resource efficiency. Our development of passenger vehicle prototype tyres containing 75 percent sustainable materials underscores our commitment to innovation and environmental responsibility.
CONCLUSION
Apollo Tyres’ unified R&D operations in India and Europe are more than innovation hubs; they are the pillars of the company’s vision to lead in technology and sustainability. By addressing global challenges and leveraging cutting-edge tools, Apollo Tyres continues to shape the future of mobility, delivering technology excellence with operational excellence to customers worldwide.
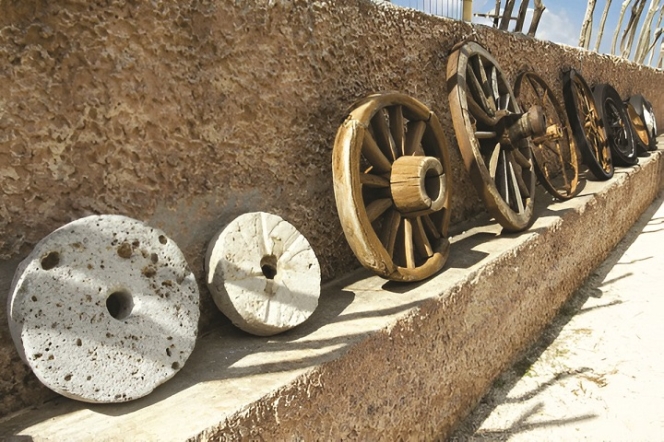
A SYNERGISTIC ALLIANCE
If my fading memory serves me right, I think I may have written at least two articles during past four years on the theme of tyres and mobility. When I step aside from the technologist’s mentality and look at tyres and mobility from a bystander’s perspective, I am convinced that it leads to some interesting insights. The connotations on the subject seem inexhaustive, which reminds of the different reflections from the different facets of a well-polished red ruby or a blue sapphire, some precious stones for which my country Sri Lanka has been famous from the ancient times.
Right from the dawn of life on earth, mobility has been a key driver for progress and survival, not only for humans but for all living beings. The ability to move has significantly changed the course of history and the evolution. Mobility is deeply embedded in every life form, from the lowest, starting from viruses and bacteria, to the highest form of life, presumably the humans. Even the stationary plants depend on mobility for their sustenance and propagation, as we learned in our lessons of Botany a very long time ago. Pollination and the distribution of seeds by wind, water and animals enable plants to colonise new locations. And through intricate vascular systems within the plants, water and nutrients are transported, which demonstrates the importance of internal mobility for their growth.
The inherent capacity of animals to move has offered them a definite advantage by enabling them to search for food, mates and seek safety. Animal migrations such as birds flying to warmer climates during winter, salmon returning to their spawning grounds and the breathtaking migration of wilder beast in East Africa, which I have personally witnessed in Kenya, shows the critical role served by mobility for their survival – an evolutionary trend transmitted to the early humans for their survival. Epic migrations of the humans have led to the spreading of humanity across the continents and establishment of the ancient civilisations in the Indus Valley and Mesopotamia etc. Thus, it can be seen that mobility has played an intrinsic role on life on earth, fostering diversity and adaptation.
From another perspective, mobility on earth is not confined to life forms only but is influenced by extraterrestrial or celestial phenomena such as gravitational forces and the influence of cosmic bodies such as the solar system. It is known that the early human communities depended on the patterns of the tides for fishing, and the travellers and traders relied on the movements and the positions of the stars for their navigational purposes, demonstrating how the cosmic bodies influenced the early earth’s mobility dynamics. The need for mobility has been intricately linked with human civilisation, impacting political, social, economic and cultural dynamics. Ancient epics like the Mahabharata and the Ramayan have vivid descriptions of horse-driven chariots, which, emphasises the importance of wheels in mobility. The wheels apparently made of wood and iron rims can be considered as the forerunners of the modern-day tyres.
Mobility has always helped in shaping civilisations, politically by enabling the expansion of empires and socially and culturally by the exchange of ideologies, traditions and goods. For instance, the Silk Road was not just a trade route but played the role of a cultural bridge between the East and the West. Economically, it enabled the gradual emergence of the foundation for the global trade systems by enabling transportation of goods over long distances.
And coming to the relatively modern times, the impact of the Newtonian Laws of Motion on practically every aspect of human mobility and mechanisation including the locomotion and the development of the internal combustion engine and eventually the automotives is widely accepted.
Man’s never-ending quest for making life more comfortable and the role of mobility and transportation has served as a key driver in many areas such as political, economic, social and cultural aspects. The increased efforts in producing synthetic rubber to develop a substitute for natural rubber (NR), which was in short supply during World War 2, for catering to the demand for tyres to be used for military purposes is a good example. Even in the ancient times, mobility has played a vital and critical role in warfare, where in addition to the infantry, horses, elephants and horse-driven chariots have been used to develop a comparative edge, as depicted in the great Indian epics.
The subject of tyre technology has always been a realm of mystique intrigue to us the students from the non-tyre sector during our study days in the late sixties. Pneumatic tyre was introduced to us as the most complicated and composite rubber product developed in the rubber industry during those days, a fact which I think still holds true despite the later developments in aerospace and bio-medical applications etc. The Ceylon Tyre Corporation, which was set up with Russian assistance, was the only pneumatic tyre manufacturing company available in Sri Lanka during those times, and this provided us facilities for learning about the practical aspects of tyre technology. It was a used plant relocated from Russia, and some of the newly selected staff were given an initial training and familiarisation in Russia. What was impressive and puzzling to us the non-tyre people was the vastness of the scope of processing and operations, and it was no secret that I skipped answering the questions on tyre technology in examinations.
The term ‘technology’, often used to have a connotation of elatedness, and some distancing or isolation from the norm, even in the modern times of mass communications. I feel that specialisation in the rapidly expanding disciplines, especially related to ICT, has further caused the deepening of this apparent chasm. The widely accepted view in the industry or in running a country is that technology is the panacea for solving our current problems and for achieving development. This latter view, of course, is open for a further deliberation at a later occasion.
Technology is very often regarded as an invention of the modern day, emerging mainly during the industrial revolutions of the 18th and 19th centuries and accelerating during the recent periods of Industry 3.0 and 4.0. While there is no doubt that these eras brought remarkable advancements in technology, the concept of technology can be considered to have been intrinsic to the human evolution. In very basic terms, technology is about finding methods to perform tasks and accomplish outcomes more efficiently, making the processes easier, faster, safer and cheaper. We are very familiar with how the early humans developed stone tools and fire-starting techniques, which may have marked the dawn of technological thinking, and hence the name given to them ‘Homo sapiens’.
Among the most significant technological breakthroughs, the invention of the wheel stands out as the cornerstone of mobility. The wheel was invented in the 4th millennium BC in the lower Mesopotamia (modern day Iraq) during what historians identify as the Bronze Age by the Sumerians, and by this time, humans have already mastered the domestication of animals and plants and were living within social hierarchies.
As the various human societies evolved technologically based on their specific socio-political, economic and cultural backgrounds, so were their mobility needs, and sometimes it becomes incomprehensible to decide which came first, technology or mobility, where we are faced with the ‘hen and the egg’ scenario.
The earliest wheels were made of wood and later reinforced with metal rims for stability and durability. I can still vividly remember our school days when we used to travel in oxen-driven ‘buggy carts’.
Charles Goodyear’s discovery of vulcanisation in 1844 had a profound effect on the manufacture of rubber products and would certainly have been contributory to the development of the first pneumatic tyre by Dunlop in 1888, which was first used on bicycles. Pneumatic tyres paved way for tyres to become more flexible, resilient and durable – the ideal prescription for modern transport systems. In the 20th century, pneumatic tyres became the standard, offering improved performance, comfort, safety and reliability. Tyres evolved further with the subsequent advances in the automotive technology, and today’s tyres are designed and engineered with new developments such as runflat technology, eco-friendly materials, smart sensors that monitor tyre performance in real-time, self-sealing tyres, non-pneumatics and advanced tyres for EVs and autonomous driving.
The development of tyre technology and emerging needs of societies for improving mobility needs are synergistic as changes and advancements of one area very often seem to drive the progress of the other. It is also an inevitable trend that the prioritisation of sustainability, a movement that has emerged over the past four decades, is rapidly influencing all the areas of tyre technology and the mobility requirements.
Societal needs are instrumental in inspiring technological advancements, and tyre innovations in turn are empowering societies to strive for sustainable and efficient mobility, and both seem to work hand in hand to face the challenges of a rapidly changing world.
From the rudimentary wooden wheels of ancient chariots to the high-tech tyres of today, the journey of tyre technology mirrors humanity’s relentless quest for progress. As we continue to explore new frontiers in mobility, the humble tyre remains a testament to the enduring relationship between technology and human innovation. Understanding the historical significance of tyres and their technological evolution enables us to gain deeper appreciation for the intricate ways mobility has shaped our world, politically, socially, economically and culturally. It is not just a narrative or episode of technological advancement but also a chronicle of human ingenuity and mankind’s timeless desire to move forward.
The author is a Management Counsellor from Sri Lanka.
- CEAT
- Kamal Suhalka
- R&D
- tyre testing
- sensors
- virtual test
Transition From Physical To Virtual Testing: Navigating The Next Frontier
- by Kamal Suhalka, Head – Testing, R&D, CEAT Limited
- January 01, 2025
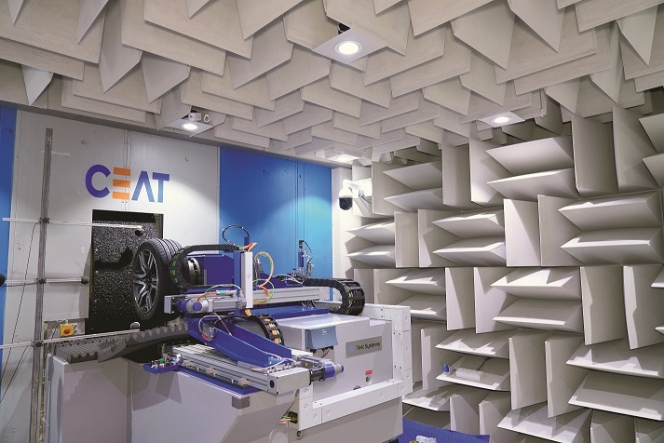
Why the need for this transition?
Tyre testing is an ongoing process critical to ensuring the quality, reliability and performance of tyres throughout their lifecycle – from design to end of life. As tyres are developed to meet ever-evolving customer and consumer needs, traditional validation methods are no longer sufficient. To stay competitive, there’s a growing need to predict tyre performance at the earliest stages of development, before physical testing begins. By leveraging advanced analytics and simulations, manufacturers can identify performance patterns, minimise risks and accelerate the development process.
The key to this shift is data and cutting-edge virtual software. With vast amounts of information now available – from sensors, testing, test tracks and consumer feedback – analytics and machine learning offer powerful tools for making data-driven predictions and optimising performance. This ability to forecast and validate tyre performance early not only speeds up time-to-market but also reduces errors, ensuring first-time-right products.
However, technology alone isn’t enough. To fully capitalise on these advances, investment in human capital is essential. Empowering teams with the skills to harness emerging technologies and encouraging a culture of continuous learning is vital for driving innovation and maintaining a competitive edge.
In essence, this transition is necessary to remain agile in an increasingly complex market, with reduction in developmental cycle time and ensure that both products and teams are primed for success.
How do we do this?
The path to transformation requires striking a balance between depth and breadth of knowledge – similar to the way a banyan tree’s deep roots support its wide canopy. It’s a two-step process: first, we deepen our expertise in specific domains, then we expand our knowledge to integrate cross-disciplinary insights.
In tyre testing, this means creating specialised expertise in critical areas such as Noise, Vibration, Harshness and Handling. Achieving this requires a comprehensive study of both the broader vehicle dynamics and the finer details of tyre performance. This is done through extensive measurements on outdoor test tracks, where vehicle dynamics are observed and linked to tyre performance data from advanced indoor equipment. Tools-like Design of Experiments (DoE) and attribute sensitivity studies help optimise tyre performance by turning subjective ‘feel’ into measurable data.
This meticulous approach, focusing on both deep specialisation and data-driven insights, forms the core of predictive testing and sets the stage for more advanced, integrated testing methodologies in the future.
Why we need virtual testing or testing 4.0?
For predictive testing to sustain, specialisation of capability and specific domain expertise needs to be nurtured. However, there are limitations to it such as learning scalability, domain specific data complexity, horizontal deployment challenges, skilled manpower dependency and longer lead times. This includes the dependency on tools that are commercially available.
Hence, predictive testing needs extension with a contemporary approach of deploying newer technologies like tyre modelling and multi body dynamics, data analytics, machine learning and artificial intelligence. This is where, testing 4.0 is conceived.
When can we start virtual testing transformation?
After domain expertise is deepened, it aids expert teams to validate a tyre with a synergised cross-functional perspective. This forms the basis of widening of knowledge. This is when the boundaries of specific domains fade and merge as a collective breadth of know-how in tyre development and testing.
A step closer to virtual tyre development
Accurate tyre modelling is critical for predicting important vehicle performance factors such as stability, braking, ride comfort and durability. By capturing the complex, non-linear behaviour of tyres, engineers can better understand and predict vehicle dynamics early in the design process, ultimately shortening development timelines. While building a full vehicle simulation used to involve modelling various subsystems like the chassis, suspension, engine and tyres, research has shown that a precise tyre model is key to improving the accuracy of vehicle dynamics predictions.
The tyre is a complex, non-linear component crucial to vehicle behaviour. With the growing number of vehicle models and use cases, there is an increasing reliance on simulation over physical testing to reduce development times. Tyre modelling requires expertise in test methods, data acquisition and conversion to accurately represent tyre forces for vehicle simulations. Advanced software tools help engineers adjust tyre properties like inflation, stiffness and friction, enabling the creation of customised vvirtual tyres’ for more precise performance analysis.
Future of virtual development: Driving simulators
Driving simulators are crucial for car manufacturers, allowing up to 70-80 percent of development work to be done virtually, saving time and money by refining designs before physical prototypes are made. These simulators help enhance the driving experience and accelerate vehicle development.
For tyre manufacturers, simulators enable early testing and validation of tyre models, ensuring optimal performance before prototypes are built. They offer advantages such as reproducibility, easier data collection and the ability to simulate dangerous conditions safely, significantly reducing development time.
The horizon of possibilities
Driving simulators will be able to accurately calculates the driving dynamics of both tyres and the vehicle. It is engineered to deliver an immersive, cutting-edge driving experience, replicating the exact sensations and performance data test drivers would encounter on a high-performance test track – "pushing the boundaries of tyre testing and performance evaluation in a virtual environment.”
- Natural rubber
- elasticity
- tyre testing advancements
- tyre
The Uniqueness Of Rubber Testing
- by PP Perera
- December 25, 2024
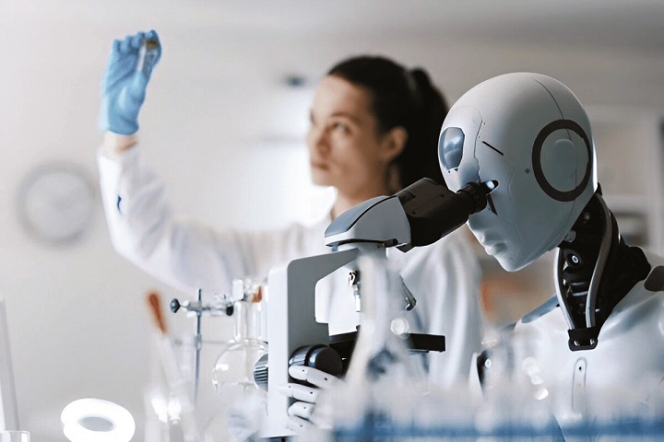
When I was informed that the theme for the December/January issue of Tyre Trends will be Tyre Testing Advancements, I was a little confused at first as to what should be a suitable entry point in bringing forth some insights into a subject that has seen significant advances during the past two decades. Finally, I thought it would be useful to the young managers if I relate some of my own experiences and viewpoints on rubber and tyre testing. It has been about 16 years since I retired form employment and from my active involvement in rubber testing directly or indirectly. However, during my ISO 9001, 14001 and ISO 45001 consultancies, I have been involved in conducting third party audits in the testing laboratories also.
From the time I embarked on my learning and the career in rubber technology, I should say that testing was not my forte. I was more affiliated towards rubber chemistry, molecular structures, compounding ingredients and compounding, probably due to my affinity to organic and inorganic chemistry during my college days. However, due to some reason, which is not clear to me even to date, I happened to be associated with testing throughout the entire period I was working in rubber products manufacturing companies, either by way of managing the quality control and assurance or handling the product development activities. As a young trainee, way back in the late sixties, my first experience in rubber testing was the basic latex tests such as DRC, total solids, ammonia content and pH. On the dry rubber side, the only available test was the Shore A pocket hardness tester, which also was indicative of the status of cure and the durability of footwear. During the next decade or so at Batas, I was in charge of the laboratory, which handled the rubber formulations, and in-process quality control. The basic tests performed were on melting point, plasticity, hardness, abrasion, flexing, peel test for bonding, colour fastness for textile materials and the solid content for adessives. During our study days, we visited the Sri Lanka Tyre Corporation (currently CEAT Kelani) as part of the study programmes, and this was the only place in Sri Lanka to possess a wide range of conventional rubber testing equipment during those days.
In later years, (1981-1998 intermittently) I had the opportunity to work in Kenya with Vaculug Traction Tyres, (re-treading of OTR and TBS tyres) and Avon Rubber ( LT/TBS tyre retreading, manufacture of bicycle tyres and tubes/ moulded rubber goods}, and the level of testing facilities at both companies were minimal, but they were doing substantially profitable operations, notwithstanding the completion. During my subsequent engagement (1999-2008) at the process control laboratory at Associated Motorways, a fairly comprehensive range of testing equipment such as the Monsanto Rheometer, Tensile Tester, Rebound Resilience, DIN Abrader and Dispersion Analyzer were in use. The company manufactured a diverse range of rubber products such as re-treading of all tyre sizes and OTR, motor cycle and three-wheeler tyres, in addition to mixing custom compounds for some large pneumatic and solid tyre manufacturing companies in Sri Lanka and exporting re-cured tread in a small way to a few countries, and testing played a more important and sometimes critical role, in its efforts to stay competitive with respect to product quality, cost effectiveness and delivery schedules. I do not think that the term ‘cutting edge technologies’ was in the standard jargon, at least in the developing countries during those years. On looking back, it is my present realisation that testing is circumstantial or situational and ‘fitness for use’, as Joseph Juran defined, quality is the prime criterion, and the role played by testing too is relative.
It could be my limited exposure to other contemporary disciplines, or my long exposure experience and perhaps the obsession in the rubber industry, that I am inclined to think of rubber technology as addictive. Perhaps exponents of other disciplines with long experience may be holding similar perceptions about their own fields of expertise. I remember with reverence my first lecturer in rubber technology, Mr Nadaraja (deceased ), an ANCRT and the Head of Rubber Chemistry Dept of the Rubber Research Institute of Sri Lanka, who devoted his entire professional life for the development of the rubber industry in Sri Lanka, a pioneer celebrated for his role in the deployment of oil extended NR for winter tyres, commercialisation of cyclised rubber in Sri Lanka during the lean years and the work on developing low-ammonia zinc oxide stabilised latex. Discussions with him were exciting and invigorating because he virtually breathed rubber, thought rubber and walked rubber in a literal as well as the metaphorical sense. Testing and test methods were invariable parts of the numerous discussions we had with him during the lectures or at the various meetings, including chats at his humble house over a cup of tea.
On contemplating broadly, one can infer that rubber and the testing associated with it has a life cycle or a cradle-to-cradle perspective. It commences with the tapping of field latex at the plantation latex processing and conversion in the plantation grades of raw rubber, centrifuging, TSR manufacture, which are the primary processing operations. These are followed by latex and dry rubber products manufacture, which again consists of upstream and downstream processes, culminating in the finished products, their subsequent usage and service performance and finally the end-of-life disposal, or more aptly, re-use and re-cycling in this era of circular economy.
Composite nature of most rubber products, including tyre and even the apparently simple moulded rubber products with a range of diverse applications, from simple door mat to O-rings and seals in aerospace applications and bio-medical devises, makes testing an integral component of rubber technology. During our study days, the pneumatic tyre was recognised as the most complex rubber product, a fact that still holds true even in these high-tech days. Since then, every aspect of rubber chemistry and physics, technology, compounding methodology and processing techniques have undergone unprecedented evolution, driven by the unending, ever thirsting quest and search for creating new product requirements and manufacturing new products or improving the existing products to meet the emerging stringent service requirements, as well the rapidly changing environmental and other regulatory compliance obligations. Modern rubber testing methods combine traditional and advanced techniques to evaluate the physical, chemical and mechanical properties. These methods are crucial for ensuring that the rubber components and finished products meet specific standards for performance durability and safety.
My knowledge in other structural materials, e.g. metals/ceramics and plastics (to some extent) is rather Ilimited. However, even with that limited knowledge, I am convinced that rubber is truly a singularity, which, leaving aside the astronomical jargon, simply means an unusual or distinctive manner or behaviour.
The macromolecular structures and the viscoelastic nature of natural as well as synthetic rubbers, which has necessitated an illogical series of breaking and re-making using physical and chemical processes and reactions, has made rubber a truly unique material. This complexity is further aggravated by the widely heterogeneous nature of the rubber additives with their own physical and chemical dispositions and interaction during the rubber processing operations. The processing conditions and parameters, including temperature, pressure, deforming forces and stresses, further contribute to the variability and unevenness lack of uniformity, or MURA, in the jargon of the Toyota Production System (TPS). To this, add the ever-increasing product performance requirements coupled with stringent environmental and safety regulations driven by the ongoing sustainability movement and the resulting emerging scenario is really complex and complicated, and testing along the entire value chain has become an integral and indispensable ingredient in the modern-day rubber products manufacturing.
Historically, rubber testing has evolved since the initial discovery of rubber and its use, particularly as it became integral to industrial applications in the 19th and 20th centuries. Initially, the testing was basic, focusing on strength and elasticity to evaluate the suitability of rubber for applications such as tyres, hoses and seals. However, with the advent of synthetic rubbers and the development of new product applications, more advanced testing became necessary. Some key milestones in the history of rubber testing can be identified as follows:
Early testing (19th Century): Era of natural rubber and basic methods such as elongation and crude tensile testing.
Development of standardised testing such as tensile, abrasion and ageing tests.
Introduction of systemic rubber and World War II (1930s-1940s): Testing for chemical resistance temperature tolerance and durability essential for military and industrial uses.
Modern testing standards: (1950s to present): Measuring properties like hardness, elasticity, resistance to chemicals, UV and Ozone, development of advanced testing equipment and standardised test methods, ASTM and ISO.
Advanced Testing (21st Century): Computerised equipment such as dynamic mechanical analysis (DMA) and thermogravimetric analysis (TGA)
In this era, where AI has become the catchword in almost every facet of human activity, we cannot ignore the potential and helping role of AI in current and futuristic rubber testing, especially in the following areas:
Predictive Modelling and Simulation
Detection of Defects
Process Optimisation
Non-Destructive Testing (NDT)
Data Driven Insights
Automated Testing and Quality Control
The current tendency of embracing new surges of waves such as automation, digital interphases and AI sometimes made us to speculate if the current generation is witnessing the last remnants of human integrity and skills, in rubber testing in areas such as:
Interpretation and analysis
Technical expertise
Trouble shooting
Quality assurance.
Adaptability and decision-making
Continuous improvement
However, it is a demonstrated fact that the combination of human expertise and modern rubber testing leads to better and more accurate testing outcomes. Human skills ensure that technology is used more effectively in obtaining meaningful results and establishment of continuously optimised testing procedures.
I am curiously inclined to look for parallels between the rubber testing and the modern medical tests, where both seem to deal with complex systems, with a strong interdependency of the subsystems and components. The basic scientific concept of ‘test, observation and inference’ seems to be applicable to both disciplines. Testing can be predictive or diagnostic, and we are sometimes astounded by the array of tests that the medical specialists recommend before they arrive at a specific conclusion, even in the case of trivial illnesses. Unlike in the old days, where keen observation and intuition was the norm, there seem to be an over dependency on testing, perhaps ostensibly due to commercial reasons. I can remember that about sixty years ago, the practitioners of Western medicine had a habit of feeling the pulse of the patients. This was unmistakeably the practice used by the native physicians.
I sometimes as a person of the older generation tend to wonder if we as rubber technologists have become overly dependent on rubber testing equipment, which has become a multi- million dollar business. Are we doing things right (efficiency) or are we doing the right things (effectiveness) is an issue I would wish the readers to contemplate.
The author is a Management Counsellor from Sri Lanka.
Comments (0)
ADD COMMENT