AUTOMATED TYRE MANUFACTURING: NO TURNING BACK
- By Sharad Matade & Juili Eklahare
- October 14, 2022

There couldn’t be any industry that isn’t implementing, or at least knowing about, automation. And if there’s actually one, then it has probably been living under a rock. The tyre industry has already opened its doors to automation, and this helps make tyre manufacturing more sophisticated and reliable. The tyre manufacturing process itself has been experiencing constant changes – from different tyre sizes and constructions to targeting less usage of energy. Automation must be on every tyre company’s to-do list, if it hasn’t adopted it already. Don Heelis, Sales Manager, Cimcorp, gave Tyre Trends more insights on the different aspects of automation in the tyre industry and its absolute requirement, when we met him at the Tire Technology Expo 2022 in Hannover, Germany. Read on…
The philosophy of tyre manufacturing has changed dramatically. A part of the change in that philosophy relates to automation implementation in the tyre manufacturing process. However, we also find more technical perspectives being adopted and taken into account at new, modern tyre factories today.
This technical perspective can be considered to be coming from a few different areas, one of them certainly being from the actual production part of the tyre factory. Therefore, with production machinery, mixers, extruders and tyre building machines, the level of technology being implemented in these processes is increasing. Moreover, these processes are getting more sophisticated.
The other aspect of this is integrating the production across all the different areas (another factor for the dramatic change in the modern tyre factory). In the past, the different areas of production were not necessarily well connected. However, today we see them getting connected a lot more – and this is being driven and enabled by technology.
This is where companies like Cimcorp come in – who happen to provide material handling and automation technology so that different tyre manufacturing processes are better integrated.
Explaining this, Don Heelis, Sales Manager, Cimcorp, said, “When you produce your work in process, what you’re producing is in synchronisation with what’s being produced in other areas of the factory. This helps minimise the work in process and have a manufacturing process that’s more efficient.”
Going the modular way
But how does one integrate different machines and processes in the plant with all the different machines and manufacturing processes involved? Heelis let us in on this.
“The trick is to implement the automation and connectivity in a modular way,” he revealed and went on, “That way, the connectivity is physical and mechanical but involves software as well. Thus, we take an approach where the modules are flexible and can connect to various inputs and outputs; however, the module is in itself standardised. Hence, the modules can work for different factories – only the interconnection needs to be flexible.”
The green tyre
While implementing automation, one, of course, would want to implement it where they get the biggest value. “Traditionally, that has been in the palletising area – in managing and handling the finished product. Basically, palletising, storing and retrieving the finished product,” Heelis informed us and continued, “This is where everyone has traditionally looked in the past. However, a lot of focus has been put on the green tyre area in the past 10 years. That includes green tyre handling, storage and retrieval and its automatic delivery to the curing process.”
A green tyre is work in process – simply put, a tyre that has not been cured. “A green tyre is made up of a number of components. It’s built on a tyre-building machine,” Heelis further told us. “Once a green tyre is built, it is buffered, followed by being cured – and automation machines are required in order to do this. Hence, this is a key element of the modern tyre factory.”
He added, “This has been an area of key focus where productivity and simplicity can be gained. In fact, the whole process can be done with less plant floor space. Ultimately, factories that want to be competitive have to implement automation technologies in that area.”
Increased efficiency
There are many brownfield factories out there that have to modernise and be viable for the future. One of the key areas that they need to modernise and automate in is green tyre handling. Heelis asserted, “By having an automated storage and retrieval system, one can track and trace all of the work in process. Plus, one is able to store in a manner that maximises the quality of the green tyres. And then, one can deliver them from the storage system to the curing process in a very systematic and accurate way. This way, when a particular green tyre is needed in the curing area, it can be delivered there in the appropriate amount of time.”
“In this methodology, when the green tyre arrives at curing, it is at that point in time when it is needed, and the production does not have to stop,” Heelis further shared. “If this can be achieved, then the curing process can be run more efficiently; the efficiency can go from 80 percent to over 95 percent. In theory, one can increase the output of their factory by 10 percent. In such a case, one can imagine how many tyres can be produced in a factory by following this methodology.”
Automation – its role during the pandemic and inflation
While automation tends to bring in efficiency, how have companies managed to keep up their competence and productivity during the thorny period of the Covid pandemic? The pandemic has definitely brought some insights to the tyre industry from a management point of view, like it did to many other sectors. According to Heelis, automation has come to the rescue of the tyre industry in the pandemic as well.
“One important thing that the industry learnt from the pandemic was that it has a risk to its ability to produce products,” he mentioned and went on, “The absence of automation will make any company in the industry highly dependent on the labour force, which might not be available to keep the production going. On the other hand, with automated processes, a company is less at risk to events like a pandemic.”
Another issue we are dealing with right now in the global economy is inflation. Inflation equals to costs going up – from the cost of materials to the cost of labour. “Nonetheless, a company can mitigate some of the impacts of inflation if it has embraced automation. In fact, the ones who automated their brownfield factories three to four years ago are in a much better position today than their competitors who had not,” Heelis pointed out and went on, “This is because the former can mitigate some of the inflation costs, is less dependent on the workforce and is able to produce better-quality products – and at a higher level of efficiency at that. We know that there is a tremendous shortage of people in the workforce in the US right now. Therefore, automated companies have a significant competitive advantage.”
From the tyre industry’s challenges due to the pandemic and inflation, we turned to the challenges Cimcorp itself faces on the commercial side. Heelis responded that, commercially, the current challenge for them is being a low-cost, high-quality producer – which one has to be in order to compete in the market. “Furthering this challenge is how we become a low-cost, high-quality producer and stay that way. And from our perspective, the way to get there is through innovation and technology,” he stated.
Automation in the Asian tyre industry
CIMCORP opened up an office in India roughly three years ago. With its presence in the country and Asia, Heelis told us that the tyre companies in Asia are no stranger to automation and are implementing it. “As a move forward, the mentality is that if you want to be a world-class manufacturer and build a new factory, then you build the factory with automation. And this is a global perspective,” Heelis asserted.
Cimcorp’s customers in Asia range from traditional tyre manufacturers to new manufacturing entrants in the industry, so it’s a mix. Throwing further light on this, Heelis said, “We all know the traditional manufacturers like Bridgestone, Michelin, Goodyear, Continental and more. But beyond these, there are new companies emerging. And these new companies have an advantage in some ways because they are not constrained by the old ways of thinking. They are forward thinking, with a clearer mindset to do things in the current environment – the environment of automation and technology.”
“Moreover, the manufacturers who don’t invest in automation, and try to run the company with practices that were developed in the 1960 and 70s, will not be able to survive or compete,” he further added. “Their market will eventually consider them to be non-competitive, non-global and unable to produce the quality expected of them.”
Cimcorp has plans for India as well. “Our strategy is to continue to grow our business in India with the domestic tyre manufacturers, and we have been successful at that,” Heelis shared and went on, “When I say domestic, that goes for manufacturing facilities within India, from Apollo Tyres to MRF to JK Tyre to Goodyear to Michelin. Thus, we plan to continue to build our business with those factories and customers from an automation perspective, and then from a full customer service point of view.”
The other aspect comes to brownfield factories. Heelis averred, “With brownfield factories, whether in North America or Asia, the cost of automation is the same; there may be different payback scenarios between the two. However, it stands true that no matter where a company is present in the world, if it is operating a brownfield factory, then it needs a strategy to modernise. And the strategy to modernise is based on implementing automation.”
Automation in brownfield factories – what will it take?
The strategy to modernise when automating a brownfield factory is especially challenging in an already existing system. Therefore, when automating a brownfield factory, one of the most important considerations is to not interrupt their day-to-day production, Heelis cited. He mentioned that the factory has to continue making its certain number of tyres each day. Hence, a strategy that enables the factory to do that is needed – while concurrently implementing automation there.
“Besides, when you implement automation, you have to be able to do it in a standardised way,” Heelis further enlightened and continued, “This can be done with the help of flexible automation modules that can work in a lot of different scenarios. Therefore, you can deal with different brownfield factories depending just on how you arrange your automation modules. Thus, you can come up with a custom solution for every different brownfield factory out there with the help of a modular approach and on the basis of how you connect those automation modules together.”
Service provided
From providing standard modular systems to hardware to software, Cimcorp strategically has a service aspect to its business – Success Services. Therefore, the approach from its service side is to enable its customers to be as successful as possible.
“That could be achieved by providing a 24/7 support. So if the customers contact us due to an issue they are facing in the solutions provided by us, we are available at any time of the day or night to support them,” Heelis revealed and added, “We can do it remotely. In fact, as technologies emerge further, we’ll see how we can do this more remotely with virtual techniques. Here, their serviceperson could be using special tools, which enables our people (who are remote) to actually be in virtual situations in our customers’ plants. In such wise, we can be more responsive and be as if we are in place in real-time in order to provide a service.”
Tyre warehouse automation or manual operation – making the choice
Nevertheless, Cimcorp does not just stop at its 24/7 services or providing its automation solutions for tyre manufacturing processes. It goes beyond that – to the finished product warehouses. However, interestingly, that depends to a degree on which part of the world the automation is needed in; while some areas will need automation that is well advanced, some areas will use a more manual operation.
Heelis explained, “There are some key factors that determine whether the facility/area in question needs to be automated or not. For example, the cost of real estate. If it’s a manual operation, then that typically involves a very large warehouse, say around 100,000 sq mt.”
“For automating, on the other hand, you require lands that are much smaller,” Heelis further highlighted. “For instance, land is very expensive in Japan. Thus, one wouldn’t want a very big footprint warehouse over there. Which means, you go vertical wherever land is expensive.”
“On the flip side, land is very cheap in some areas and inexpensive to build the generic building (like in some areas of the US). So there is less incentive to go vertical with automation there,” he added. “But there might be other factors that could dominate.”
Choosing automation over manual operation – why?
While some main factors do influence the decision if a warehouse is going to be a fully automated one or a semi-manual one, an automated one is always preferred. For clear reasons.
“The benefit of an automated warehouse is that everything is extremely well controlled,” Heelis informed. “What’s more, you have complete control of your product – you know exactly where it is, how much of it you have and you can get on-demand access.”
“As for a semi-manual warehouse, there are fork trucks, people moving things around and putting them in different storage locations,” Heelis further clarified. “This process is much more manual, involves a lot more interaction and is time consuming. Therefore, you have much less control over the process.”
Automation – a need not to be confused as a luxury
The automotive industry has been one of the earliest industries to adopt automation. So it’s high time that tyres, an integral component of any vehicle, did so too. It’s clear that automation, today, is not a luxury but a need. No company can afford to not have it. No tyre company must be limited to older technologies, and they must invest in automation for the long term. This would not just help tyre manufacturers meet their customers’ demands without any delay, but also help modernise the industry with the world’s rapidly changing technologies.
MESNAC Demonstrates 35-Second Tyre Production At Media Briefing
- By TT News
- August 29, 2025
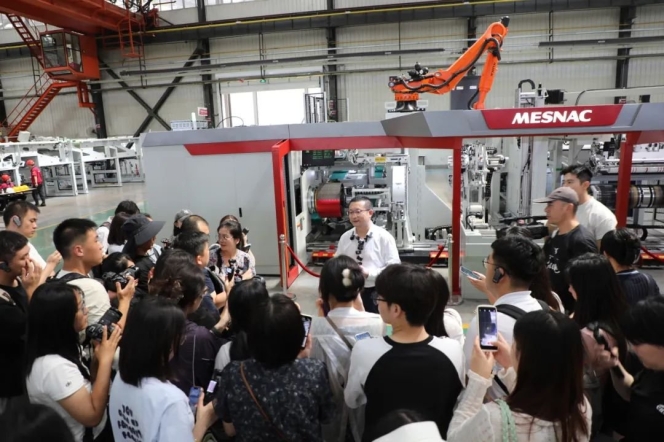
The Qingdao Municipal Government Information Office recently hosted a media briefing on ‘Shandong's Top Brands on the Industrial Chain – Intelligent Equipment Industrial Chain’ at the MESNAC Jiaozhou Equipment Industrial Park. Senior leaders from MESNAC and three other prominent firms were in attendance to present their advancements and field questions from journalists.
A central focus was on MESNAC's proprietary ROC R&D platform, a unique modular system engineered specifically for the rubber equipment sector. This platform is fundamentally structured around client requirements, integrating comprehensive product design, technological development and rigorous testing protocols. This architecture facilitates a configurable development process, allowing for both large-scale customisation and remarkably agile product delivery. The company's operational philosophy was explained as a dedicated team model, where a single unit focuses its expertise on one product for its entire lifecycle. This meticulous approach has generated significant industry innovations in recent years, including fully automatic material weighing systems, unmanned tire building machinery and intelligent tyre curing press workshops capable of operating as fully unmanned ‘lights-out’ facilities.
The event included a practical demonstration of this technology in action. Attendees witnessed the NPS Semi-steel One-stage Building Machine, which achieves a single-tyre production cycle of just 35 seconds through complete automation. This system boasts world-class efficiency, requiring only one person to supervise multiple machines simultaneously. It embodies a new generation of intelligent manufacturing by seamlessly integrating cutting-edge technologies such as precision machine vision, industrial robotics, sophisticated industrial IoT software and autonomous learning capabilities.
NEXEN TIRE Inaugurates High Dynamic Driving Simulator
- By TT News
- August 28, 2025
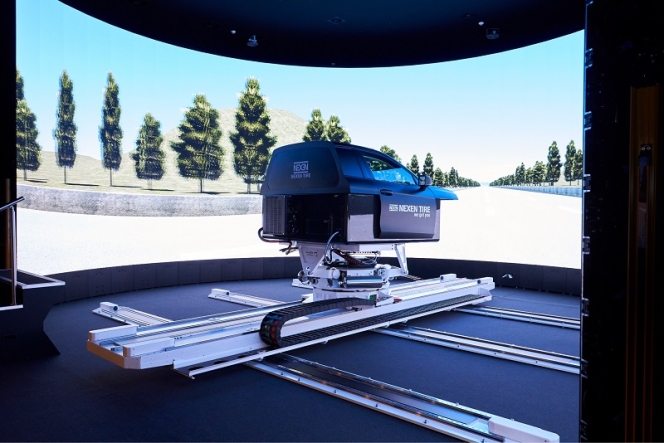
NEXEN TIRE has inaugurated a cutting-edge High Dynamic Driving Simulator at its Magok-based NEXEN UniverCity R&D centre in Seoul. A first-of-its-kind installation within the South Korean tyre industry, this advanced system represents a pivotal step in modernising tyre development by leveraging virtual reality and artificial intelligence.
The simulator functions by creating a highly realistic virtual driving environment. Engineers can input specific vehicle data and parameters to conduct precise testing of performance metrics such as acceleration, braking and handling across a diverse range of simulated road conditions, all within a controlled laboratory setting.
This technological advancement is expected to significantly streamline NEXEN TIRE’s research and development operations. It will reduce the need for physical prototypes and extensive real-world vehicle tests, which in turn accelerates development cycles and lowers associated costs. A major strategic benefit is the enhanced ability to meet the exacting performance standards required by global automakers for original equipment tyres, especially for new and high-performance vehicle models.
The shift towards virtual testing also supports the company's sustainability objectives by diminishing the fossil fuel consumption typically involved in traditional road testing, thereby supporting its broader environmental, social and governance (ESG) commitments. This move aligns with a larger industry trend where automakers are rapidly adopting virtual processes to improve efficiency.
Looking forward, NEXEN TIRE plans to build upon this simulator to establish a comprehensive Full Virtual Development Process. This long-term strategy aims to integrate advanced simulation with finite element method analysis and AI, ultimately working towards a future where physical testing is largely replaced by virtual validation.
John Bosco (Hyeon Suk) Kim, CEO, NEXEN TIRE, said, “Ahead of the industry trend towards virtual development of vehicles and tyres, the establishment of our High Dynamic Driving Simulator is a strategic investment to lead the future mobility sector. By combining VR and AI technologies, we will enhance both the efficiency and precision of our R&D while contributing to ESG management, thereby strengthening our global competitiveness.”
Anyline Bets On AI To Drive Innovation For Automotive & Tyre Inspections
- By Nilesh Wadhwa
- August 25, 2025
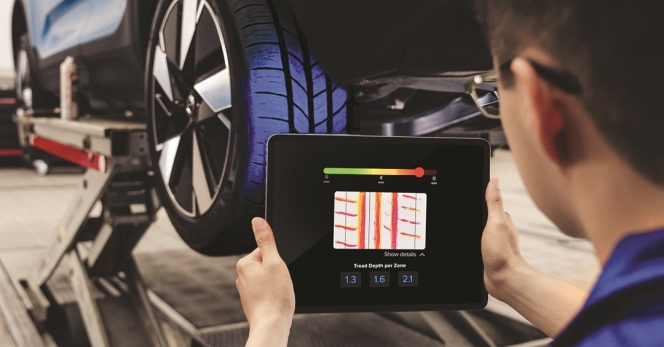
Anyline, a global leader in AI-powered mobile data capture, is disrupting industries by enabling instant scanning of everyday data with smartphones.
In an era where data is king, Vienna-based Anyline aims to carve out a significant niche, transforming everyday data capture into a seamless, mobile-first experience. What began as a computer vision research project, exploring the intricate ways machines could ‘see and interpret the world’, has blossomed into a global commercial platform.
This evolution was driven by a clear recognition of how urgently businesses across various sectors needed reliable, efficient and mobile-first data capture solutions. Anyline’s innovative approach now empowers frontline workers across diverse industries, from the complexities of logistics and the precision of manufacturing to the dynamic environments of retail and public safety and, notably, the high-stakes world of the automotive sector.
“Anyline was founded with the vision of making everyday data – like barcodes, serial numbers, IDs and tyre codes – instantly scannable using nothing more than a smartphone,” explained Peio Elustondo, VP of Inside Sales and Growth Marketing at Anyline. “We quickly saw how urgently businesses needed reliable, mobile-first data capture. The demand was undeniable, and our technology provided a straightforward, scalable answer.”
The company’s advanced AI-powered technology is now extensively deployed in over 100 countries, serving a distinguished roster of leading brands such as Discount Tyre, a giant in the automotive aftermarket; PepsiCo, a global food and beverage leader and IBM, a technology and consulting powerhouse. Elustondo highlighted their core mission, which remains steadfast despite their expansive growth, “Whether it’s helping technicians inspect tyres, retailers manage inventory or police verify vehicle data, our mission remains the same: to empower frontline workers with smart, scalable technology that makes everyday tasks faster, more accurate and more efficient. We believe in putting powerful tools directly into the hands of those on the ground, enabling them to work smarter, not harder.”
Anyline’s global footprint and tangible impact speak volumes, with millions of scans performed each month and a continuously expanding ecosystem of enterprise partners who place their trust in its software to digitise critical operations in the field, at the point of action.
REVOLUTIONISING TYRE INSPECTIONS WITH TIREBUDDY
One of Anyline’s most impactful and strategically significant innovations in the automotive space is TireBuddy, a dedicated mobile application meticulously designed to streamline the often-cumbersome process of tyre inspections. Traditional manual methods, which have long been the industry standard, are frequently plagued by inconsistencies, subjective interpretations and outright errors. These issues present a significant and persistent challenge for businesses striving for efficiency and accuracy.
“Tyre inspections are often manual, time-consuming and prone to errors – from misreading DOT codes to inconsistent tread depth checks,” Elustondo noted, painting a clear picture of the industry’s struggle and underscoring the dual nature of the problem. “The challenge is not only speed but also standardisation. Without reliable digital tools, even experienced technicians can struggle to deliver consistent results, especially under pressure or in high-volume environments.”
TireBuddy directly and comprehensively addresses these pain points, bringing powerful, AI-driven capabilities directly to the workshop floor, all without the need for expensive, dedicated hardware.
“It was built specifically for the needs of independent tyre dealers and service teams who want to modernise their workflows without investing in costly hardware or infrastructure,” Elustondo stated, highlighting the app’s accessibility and cost-effectiveness. The app empowers technicians to effortlessly scan and capture crucial data points such as DOT codes, tyre size, brand and Vehicle Identification Numbers (VINs) instantly.
Furthermore, TireBuddy provides precise tread depth measurements through a guided mobile workflow, ensuring that tyre health is assessed consistently and accurately, eliminating the need for traditional, often inaccurate, physical gauges. Remarkably, all of this critical data capture and verification happens in under a minute per tyre, with the results being rigorously AI-verified for unparalleled accuracy and reliability.
“All of this happens in under a minute per tyre and the results are AI-verified for accuracy and reliability,” Elustondo confirmed, emphasising the speed and precision that define TireBuddy.
He then explained the broader and more profound benefits that extend far beyond mere operational efficiency, “Beyond just speed and convenience, the true value of TireBuddy lies in what it unlocks. It gives technicians a digital record of each tyre’s condition, streamlines compliance documentation and enables more transparent conversations with customers about when a tyre truly needs to be replaced. This boosts customer trust and opens the door to more confident service recommendations.”
This digital record not only enhances internal record-keeping but also serves as a powerful tool for customer education, allowing technicians to visually demonstrate wear and tear and clearly justify service recommendations, thereby fostering greater confidence and loyalty. Because TireBuddy is mobile-based and cloud-connected, it also integrates seamlessly into existing backend systems – whether those are inventory management platforms, Customer Relationship Management (CRM) tools or point-of-sale systems. For businesses, this translates into a cascade of benefits, superior data quality, a significant reduction in manual errors and enhanced overall efficiency across their entire operational spectrum. Ultimately, TireBuddy empowers tyre shops of all sizes, from small independent garages to large chains, to offer a more modern, professional and data-driven customer experience – a capability that is fast becoming essential in today’s increasingly competitive and digitised service landscape.
ACCURACY AND IMPACT ACROSS INDUSTRIES
Anyline claims its AI-powered visual inspection offers a significant and demonstrable leap in consistency and reliability when compared to traditional manual methods. The inherent variability in human performance, particularly in repetitive and detailed tasks, often leads to discrepancies.
“Manual inspections often vary from technician to technician, especially when it comes to tasks like reading DOT codes or estimating tread depth. Our technology standardises these processes, capturing data instantly and removing the risk of human error, typos or misinterpretation. This means every inspection, regardless of who performs it, adheres to the same high standard of accuracy,” said Elustondo.
While acknowledging that real-world factors such as challenging lighting conditions or extreme tyre wear can influence accuracy, he assured that “our tools are continuously trained and tested on a wide range of conditions to ensure performance is reliable in the environments where they’re used most. The result is not only faster inspections, but repeatable, verifiable outcomes that technicians and service managers can trust implicitly.”
The profound impact of solutions like TireBuddy is clearly evident in Anyline’s impressive client base, which spans a wide array of automotive industry players, including leading automotive original equipment manufacturers (OEMs), extensive aftersales networks and crucial logistics providers. One of their most significant and long-standing partners is Discount Tyre, which stands as the largest independent tyre and wheel retailer in the US.
Discount Tyre leverages Anyline’s cutting-edge technology to streamline their tyre inspection processes and digitise key vehicle data across their vast service network, significantly enhancing their operational efficiency and customer service.
“Our ability to serve both independent dealers and enterprise-scale players is a key strength. Whether it’s through our TireBuddy app or via custom integrations using the Anyline SDK, we help clients bring mobile inspection capabilities directly into the hands of technicians – no matter the size or complexity of their operation. This flexibility ensures that businesses of all scales can benefit from our advanced AI,” averred Elustondo, highlighting Anyline’s versatile approach.
Beyond the automotive sector, Anyline’s solutions are also used by government agencies for vehicle data verification, rental fleets for efficient vehicle check-ins and commercial vehicle operators seeking to improve safety, compliance and overall operational efficiency through AI-driven inspections. This broad applicability underscores the universal need for accurate, mobile data capture.
A GLOBAL FOOTPRINT AND FUTURE VISION
Anyline’s global reach extends significantly to India, a market Elustondo described as “important for us – both in terms of talent and innovation partnerships.”
He highlighted a particularly significant collaboration that exemplifies Anyline’s impact in the region: a partnership with Tata Power Delhi Distribution (Tata Power-DDL). Through this collaboration, Anyline launched an industry-first mobile meter reading solution utilising OCR (Optical Character Recognition) and AI-powered anti-spoofing technology. This innovative solution was deployed across North Delhi, dramatically improving billing accuracy, reducing non-technical losses and streamlining field operations for an astounding 1.9 million metres.
“That collaboration showcased how AI and mobile data capture can solve real-world infrastructure challenges at scale,” Elustondo added, pointing to the measurable impact on operational efficiency and data quality. This project marked a pivotal moment, being the first time Tata Power-DDL had adopted mobile OCR for utility meter reading, demonstrating a clear shift towards digital transformation in critical infrastructure.
Looking ahead, Anyline remains steadfastly committed to its software-first approach, a strategic decision that deliberately avoids the need for specialised, proprietary hardware.
“Our focus is on delivering AI-powered software solutions that run seamlessly on everyday mobile devices like smartphones and tablets. This software-first approach eliminates the need for specialised hardware, making our technology far more accessible, scalable and cost-effective for users around the world. It means businesses don’t have to invest in new, expensive equipment; they can leverage the devices their teams already use, significantly lowering the barrier to adoption,” Elustondo affirmed.
This philosophy ensures that Anyline’s solutions are not just technologically advanced but also practically viable for a wide range of businesses globally.
The company’s future plans involve a continuous and ambitious expansion of its AI-powered capabilities specifically tailored for the automotive industry. “Expect more integrations, real-time diagnostics and predictive maintenance features – all accessible via mobile,” Elustondo revealed, hinting at a future where vehicle maintenance is more proactive and data-driven. These advancements promise to further empower technicians with instant insights, enabling them to identify potential issues before they escalate and provide even more precise recommendations to customers.
The company shared that TireBuddy, in particular, stands as a powerful testament to its responsiveness to genuine industry needs and its ability to rapidly develop and deploy effective solutions.
“One development we are especially proud of is TireBuddy. It was built in direct response to feedback from the field, where independent dealers and service teams told us they needed a faster, more accurate way to assess tyre health without investing in expensive equipment or retraining their teams. We listened and we delivered,” Elustondo stated.
The app’s success has been resounding, with positive feedback echoing across the industry. “The response so far has been incredibly positive. Dealers are telling us it is improving the professionalism of their service while also reducing the friction that often comes with inspection-based upselling. It transforms a traditionally manual process – DOT code reading, tread depth measurement, VIN capture – into a digital workflow that’s intuitive, consistent and verifiable. It helps technicians provide clearer documentation, make more confident recommendations and ultimately earn greater trust from customers,” Elustondo said.
He envisions TireBuddy as far more than just a single product: “We see TireBuddy not just as a product, but as the foundation of a broader ecosystem of AI-powered tools designed to support the future of vehicle service – where data, transparency and customer trust take centre stage. This is about building a more efficient, reliable and customer-centric automotive service industry for tomorrow.”
BendPak Launches Compact 10AP-SRT Two-Post Lift For Specialised Service Shops
- By TT News
- August 19, 2025
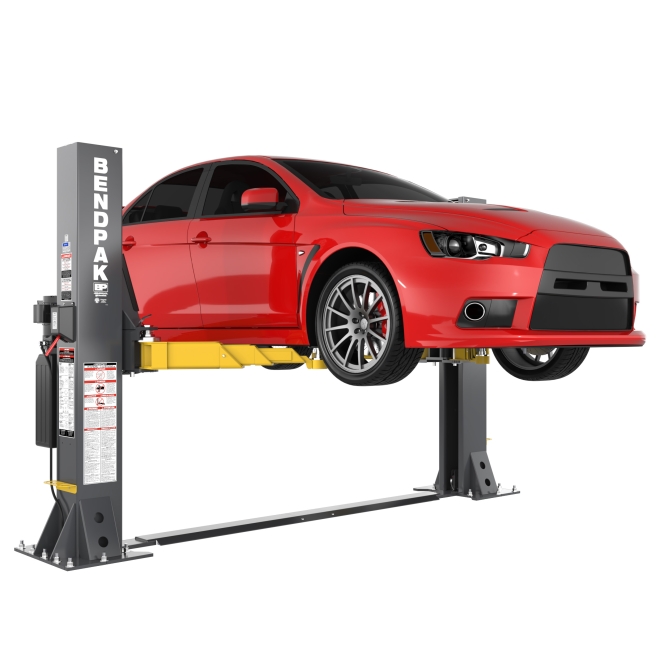
BendPak has added a 10,000-pound capacity model to its innovative AP-SRT Series of short-rise two-post lifts, following the successful launch of the 12,000-pound 12AP-SRT earlier this year. Designed for tyre shops, brake service centres and detailing operations where full-height lifts are unnecessary, these compact solutions combine productivity with space efficiency.
Standing just 93.5 inches tall with a 46.25-inch maximum lift height, the AP-SRT Series enables ergonomic vehicle access without the bulk of traditional lifts. The new 10AP-SRT features BendPak’s triple-telescoping swing arms for versatile positioning and low pad heights, while the Automatic Swing Arm Restraint System (ASARS) ensures stability with 2,000+ pounds of locking force.
Optimised for fast-paced environments, the lift’s high-performance power unit accelerates cycle times, and its symmetric/asymmetric configuration options accommodate diverse vehicles. ALI Gold Certified for safety, the 10AP-SRT comes with BendPak’s 5-2-1 Warranty, covering structural components for five years, hydraulics for two and parts/labour for one.
Sean Price, Director of Product Development, BendPak, said, “Many shops lift vehicles only partway, yet they’re forced to buy full-rise lifts that cost more, take up more space and get used at half capacity. Our 10AP-SRT and 12AP-SRT models are purpose-built to fill that gap – giving shops a cleaner layout, better efficiency and a safer overall working environment. From sedans to light-duty trucks, the BendPak 10AP-SRT delivers the performance, efficiency and safety today’s shops demand, without the excess height or cost of a full-rise lift.”
Comments (0)
ADD COMMENT