Collaboration Is A Growing Need!
- By Sharad Matade & Gaurav Nandi
- June 30, 2025
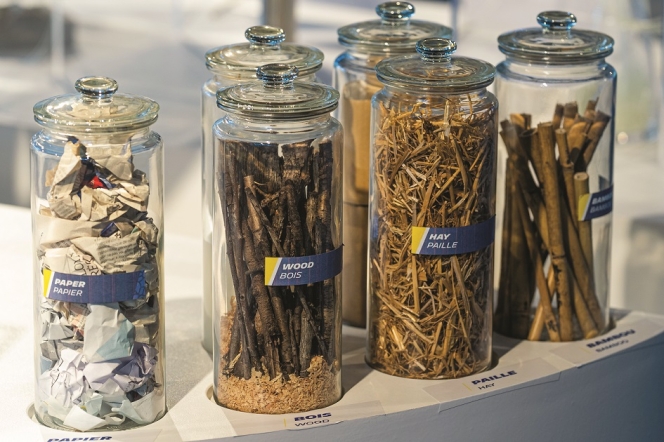
The tyre industry has undergone significant changes over the past century, particularly in material composition and performance optimisation. While the external appearance of tyres may remain similar, advancements in rolling resistance and the integration of sustainable materials have reshaped the sector. Michelin, alongside its competitors, has been embracing innovation through collaborations to meet its ambitious 2050 sustainability goals, focusing on using 100 percent renewable and recycled materials. However, the challenge lies in scaling up recycling technologies and ensuring effective sorting. As the industry shifts, RFID technology and extended producer responsibility (EPR) regulations are emerging as critical tools for achieving material circularity and enhancing recycling efficiency.
Tyres have changed in the last 100 years. While the basic shape and colour might look the same, the internal composition has evolved significantly. Over the past century, and especially in the last 30 years, there have been major advances. One of the most significant has been the improvement in rolling resistance. Achieving lower rolling resistance without compromising grip has been a major technical challenge, and it has had a direct impact on fuel efficiency. In parallel, there’s been increasing focus on using more sustainable materials in tyre manufacturing. So, while it might not be obvious from the outside, there’s been substantial innovation under the surface.
However, it is a well-known fact that the tyre industry is secretive. Companies keep their research and development as tight as possible, but endeavours for including recyclable materials seem to break that ceiling, prompting towards collaborations.
Speaking exclusively to Tyre Trends, Sander Vermeulen, Vice President for End-of-life Rubber Products Recycling Business at Michelin, said, “There is a growing need and momentum for tyre companies to work more closely together, particularly around sustainability and materials innovation. Many companies have set ambitious goals for 2050, which include using 100 percent sustainable materials, achieving full recyclability or becoming carbon neutral. While each company may define these goals differently, the overarching direction is very similar.”
“A good example of this shift is our recent collaboration with Bridgestone through the ‘Call for Action’ initiative. We discovered that both companies shared similar long-term ambitions. One major challenge we identified was the scalability of innovations, especially from recycling companies. Many of these innovations work well at small scale, but scaling them up to meet the needs of the global tyre industry is a different story. What’s promising is that instead of working in silos, we began engaging in open dialogue. Both Michelin and Bridgestone were receiving proposals for new materials but often found them unsuitable for tyre applications. Rather than simply rejecting these proposals, we asked that how we can help these suppliers improve the products,” he added.
He noted that together the tyre makers started defining shared specifications that outline the minimum criteria a new material must meet to be viable for tyre manufacturing. “It’s not a guarantee of adoption, but it provides a clear, transparent benchmark. And if a material doesn’t fall within that box, we can save time for ourselves and the suppliers,” added Vermeulen.
He also quipped that he had never imagined working so openly with a competitor like Bridgestone whilst strictly respecting antitrust rules. But the experience has been incredibly constructive.
Michelin’s 2050 target is bold as it seeks to make 100 percent of its tyres from renewable, recycled or sustainable materials. Recycling sits at the core of that ambition. Internally, the company is aligning efforts across departments to meet this goal with a near-term milestone of 40 percent sustainable content by 2030.
That percentage includes both recycled and bio-based materials. However, Michelin isn’t developing recycling technologies in-house. Instead, it’s working with a network of external partners to identify and scale promising innovations.
Among its collaborators are Enviro and Infiniteria as well as broader initiatives like Biobutterfly and the WhiteCycle consortium, which focuses on recovering textile fibres for tyres. The company remains open to any solution that can help close the loop on tyre materials.
As of the most recent annual report, Michelin reported that 31 percent of the materials used in its tyres are either renewable or recycled. This figure reflects the combined share of both categories, not recycled content alone.
Opining on whether recycled materials are easier to use in commercial or passenger tyres, Vermeulen said, “It really depends on the specific application. Some applications allow for a higher percentage of renewable or recycled content than others. But we don’t break down our targets or current performance by tyre category. The current figure we’ve communicated in our annual report is a global average across all types of tyres.”
EVOLVING VALUE CHAIN
As tyre companies remain steadfast towards the respective goals of using recycled and renewable materials, a glaring question that remains is the fate of current suppliers. Explaining how the value chain will be impacted once tyre companies reach the goals, Vermeulen stated, “They will also need to adapt. The entire value chain must evolve. That means synthetic rubber producers and oil suppliers need to develop renewable or recycled versions of the materials they currently provide. Everyone, from upstream raw material providers to downstream manufacturers, will need to contribute if we’re going to meet these ambitious goals.”
Commenting on whether such shift will restructure the entire tyre industry, he said, “It’s hard to make specific predictions, but one thing is clear that the entire value chain is already beginning to change. All raw material suppliers now understand the direction tyre manufacturers are heading. We’re already seeing many traditional suppliers exploring new approaches to reduce the reliance on fossil-based materials. Some are developing recycled alternatives, while others are exploring biobased feedstocks.”
“In this effort, a concept we explored in a large-scale European project was called BlackCycle. It brought together various actors from the entire tyre industry value chain including raw material suppliers and other stakeholders to map out how we can extract maximum value from end-of-life tyres. It looked at viable recycling pathways including how pyrolysis oil can be integrated into chemical supply chains. We all need to work together to co-create solutions based on renewable and recycled materials,” he added.
Michelin doesn’t plan to produce recycled materials itself. Instead, its focus is on defining performance and quality specifications, then partnering with companies ranging from start-ups to established suppliers that can deliver materials meeting those standards.
Commenting on the same lines, he added, “The entire tyre industry has a strong interest in gaining access to recycled materials that can be reused in new products. And to achieve that, partnerships are essential. There’s no way we can meet these ambitions if every company stays within its traditional boundaries and works in isolation. We believe in collaborating across the value chain. Often, smaller companies have breakthrough technologies or innovative ideas but lack the resources or infrastructure to scale. In those cases, if we can help them access funding or industrialise the processes, it’s a win-win for the industry as a whole.”
While performance gaps between recycled and virgin materials are a known concern, Michelin sees scalability as the more critical barrier. Many recycling innovations show promise at the lab or prototype level, but few are ready for industrial-scale production.
To bridge that gap, Michelin and others in the sector are working closely with innovators to help mature these technologies to meet industry demands.
REGULATION & TECHNOLOGY
The extended producer responsibility (EPR) has been a staunch advocate for recycling end-of-life tyres across countries. The regulation is not only limited to European markets but has expanding into countries like India too.
Commenting on whether EPR regulations will help drive more effective recycling, Vermeulen said, “Extended producer responsibility plays a key role in tyre recycling by making manufacturers responsible for collecting and recycling tyre after use. In countries with EPR laws, such as most of Europe, producers and importers must ensure proper tyre collection and recycling. This legally mandates tyre producers to manage the end-of-life stage of the products. However, EPR is not the only model that can ensure effective recycling. In regions without EPR, like the United States, tyre recycling is still managed through a free-market system driven by industry and service providers. Even in Germany, which lacks an EPR law, tyres are still collected and managed properly through industry-driven solutions.”
“While EPR can certainly help in places with limited infrastructure, the key to effective tyre recycling lies in how well the system is organised. Whether through EPR or free-market models, both can be effective as long as the collection and recycling infrastructure is well established,” he added.
Vermeulen also views RFID technology as a crucial enabler for achieving material circularity in the tyre industry. By embedding RFID tags, tyres can be tracked and identified with precise information about its composition, helping to streamline the recycling process. This technology allows for better sorting of tyres based on specific material make-up, which is critical for maximising the quality of recycled materials.
Just as with household recycling, the challenge is to ensure that materials are sorted effectively. With too many sorting categories, costs rise without guaranteeing better quality. RFID makes it easier to identify the correct ‘bin’ for each tyre, whether it’s a winter, truck or passenger car tyre.
Additionally, RFID can help differentiate between new, retreaded and partially worn tyres, which often have varying materials and recycling needs. This enables more efficient sorting, improving the overall quality of the recycling output while keeping costs manageable. Michelin sees RFID as an essential tool in making the recycling process more effective and economically viable.
CARBIOS Strikes Multi-Year Deal With Indorama Ventures For Tyre Textile Recycling
- By TT News
- August 07, 2025
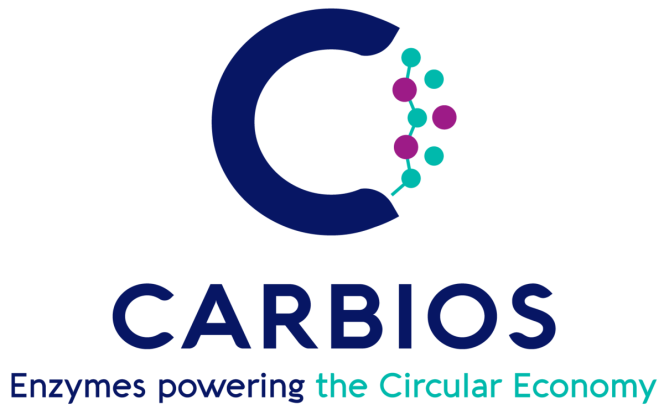
French biotech firm expands into industrial fabrics market through enzymatic PET recycling technology
French biotechnology company CARBIOS has signed a multi-year commercial agreement with Thailand's Indorama Ventures to supply recycled materials for tyre manufacturing, marking the firm's expansion into the industrial fabrics sector.
Under the deal, CARBIOS will provide biorecycled monomers from its planned Longlaville industrial plant to Indorama Ventures, the world's largest polyester producer. The Thai company will transform these materials into recycled polyethylene terephthalate (r-PET) filaments for use in tyre reinforcement by French tyre manufacturer Michelin.
The partnership represents CARBIOS's entry into a new market segment beyond its existing focus on cosmetic packaging applications. The company uses proprietary enzymatic recycling technology to break down complex PET waste into high-quality recycled materials.
"This commercial agreement with Indorama Ventures marks a new step in the realisation of our industrial project," said Vincent Kamel, chief executive of CARBIOS. "It confirms the trust of Indorama Ventures and Michelin in our PET biorecycling technology."
The deal comes weeks after CARBIOS signed its first sales contracts for biorecycled PET with two unnamed global cosmetics companies, as the firm builds momentum ahead of the commercial launch of its Longlaville facility.
Michelin, which has committed to using 100 percent renewable and recycled materials by 2050, said the partnership advances its circular economy objectives.
"This partnership is a tangible expression of our commitment to turning complex waste into high-performance materials," said Fabien Gaboriaud, director of circularity and renewable & recycled materials at Michelin Group. "By integrating enzymatically recycled r-PET into our tyres, we are marking a new milestone on our journey toward achieving 100 percent renewable and recycled materials by 2050."
Indorama Ventures, which generated $15.4 billion in revenue last year, said the alliance underscores its commitment to circular economy principles. The company employs approximately 25,000 people across manufacturing operations in Europe, Africa, the Americas, and Asia Pacific.
"This alliance with both, CARBIOS and Michelin, underlines our commitment to plan ahead and take a leading role in shifting the industry towards circularity," said Renato Boaventura, global market head mobility at Indorama Ventures.
CARBIOS, founded in 2011, has developed enzyme-based biological processes to break down plastics as part of efforts to prevent plastic pollution and accelerate the transition to a circular economy. The company operates an industrial demonstration plant for biorecycling that has been operational since 2021.
Construction of what the company describes as the world's first biorecycling plant is expected to resume in the second half of 2025, subject to securing additional funding.
Cabot Launches LITX 95F Conductive Carbon For Energy Storage Systems
- By TT News
- August 06, 2025
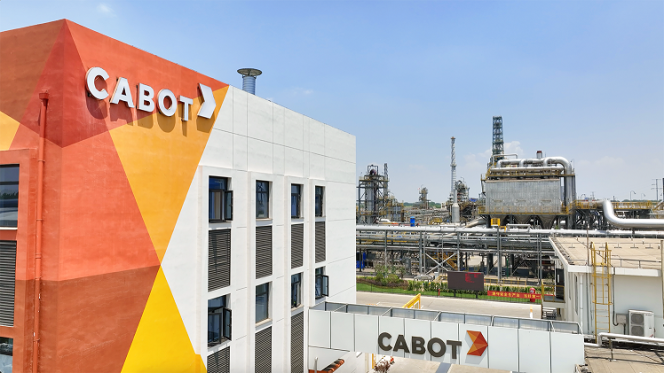
Cabot Corporation has launched LITX 95F, a high-performance conductive carbon additive designed for lithium-ion batteries in energy storage systems (ESS). Optimised for residential, commercial and industrial ESS applications, this advanced material enhances conductivity, extends cycle life and improves processability – critical for systems requiring durability under frequent charging and discharging.
With the global ESS market expanding due to renewable energy adoption and demand for grid stability, battery manufacturers need cost-effective, high-performance solutions. LITX 95F meets these needs by boosting energy density and cycle life while maintaining stability. Pouch cell tests with thick electrodes confirm its superior capacity retention, offering manufacturers greater flexibility in ESS design.
The material’s high-structure morphology strengthens conductivity and stability over repeated cycles. Additionally, its compatibility with thick cathode designs helps lower material costs without sacrificing performance. This innovation supports the growing ESS sector by enabling more efficient, reliable and scalable battery solutions.
Jeff Zhu, Executive Vice President and President, Carbon & Silica Technologies, Battery Materials and Asia Pacific Region, said, “As the global energy landscape continues to evolve, the ESS market requires advanced materials that deliver both performance and efficiency. Our new LITX 95F product is a direct response to the needs of the market and our battery customers – leveraging our deep industry expertise with proven performance to help scale ESS applications faster and more efficiently. This launch reflects our commitment to enabling a more sustainable future by delivering innovative solutions for battery technologies that support the energy transition at a global scale.”
- Association of Natural Rubber Producing Countries
- ANRPC
- Monthly NR Statistical Report
- Natural Rubber
ANRPC Publishes Monthly NR Statistical Report For June 2025
- By TT News
- August 06, 2025
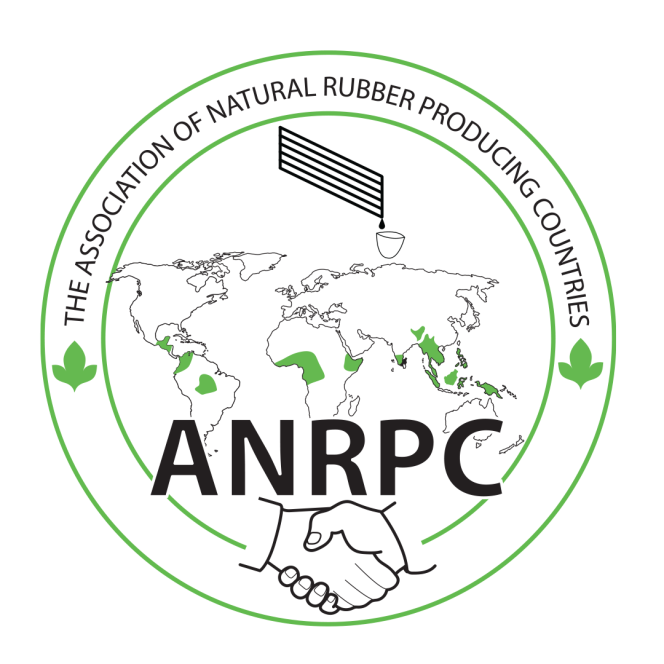
The Association of Natural Rubber Producing Countries (ANRPC) has released its Monthly NR Statistical Report for June 2025, providing an overview of key developments in the global natural rubber sector. The latest data indicates a sustained downward price trend, primarily driven by improving supply conditions in major producing nations, elevated stockpiles at key ports and ongoing trade policy uncertainties.
Market analysts attribute the bearish sentiment to a combination of factors, including increased output from leading rubber-producing countries and subdued industrial demand, particularly from tyre manufacturers. These conditions have contributed to mounting pressure on prices, with limited signs of immediate recovery. The ANRPC notes that while production levels remain stable, cautious demand projections persist due to broader macroeconomic concerns, including potential trade disruptions and slowing global economic growth.
Projections for 2025 suggest a modest 0.5 percent increase in worldwide natural rubber production compared to the previous year. Meanwhile, consumption is anticipated to grow by 1.3 percent, reflecting a slight but uneven recovery across key markets. However, analysts warn that external factors, such as shifting US tariff policies and weaker-than-expected industrial activity, could further dampen demand growth in the coming months.
Cabot To Acquire Bridgestone’s Mexico Carbon Manufacturing Facility
- By TT News
- August 05, 2025
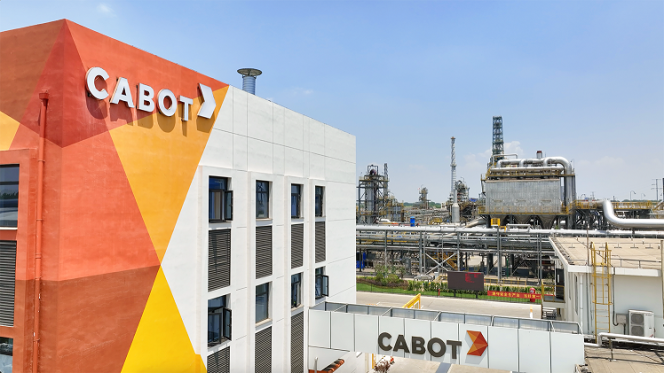
Cabot Corporation has signed a definitive agreement to purchase Mexico Carbon Manufacturing S.A. de C.V. (MXCB) from Bridgestone Corporation for USD 70 million on a debt-free, cash-free basis, pending standard closing adjustments. The deal, which requires regulatory approval in Mexico, is anticipated to finalise within three to six months.
The MXCB facility, established in 2005, produces reinforcing carbons and is strategically located near Cabot’s existing Altamira plant, operational since 1990. This acquisition reinforces Cabot’s partnership with Bridgestone, ensuring long-term supply of reinforcing carbon products while expanding Cabot’s production capacity and global footprint. The facility’s versatility allows for the manufacture of additional reinforcing carbon products, enabling Cabot to meet diverse customer demands and pursue future growth opportunities.
By integrating MXCB, Cabot strengthens its position as a leading global supplier of carbon black, reaffirming its commitment to delivering high-quality, reliable materials to key markets. Bridgestone’s decision to sell MXCB to Cabot reflects confidence in Cabot’s expertise and consistent performance as a trusted industry partner. This move aligns with Cabot’s long-term growth strategy and enhances its ability to serve customers worldwide.
Sean Keohane, President and CEO, Cabot Corporation, said, “We are excited to expand our global reinforcing carbons network and deepen our collaboration with Bridgestone. This acquisition aligns with our strategy to grow in core markets and reinforces our commitment to operational excellence, innovation and customer value. Our long-standing experience in the region and cultural alignment with the local team supports a smooth integration and long-term success. Importantly, this acquisition also further strengthens our position as a global leader in reinforcing carbons, enabling us to deliver innovative solutions and dependable supply to customers.”
Comments (0)
ADD COMMENT