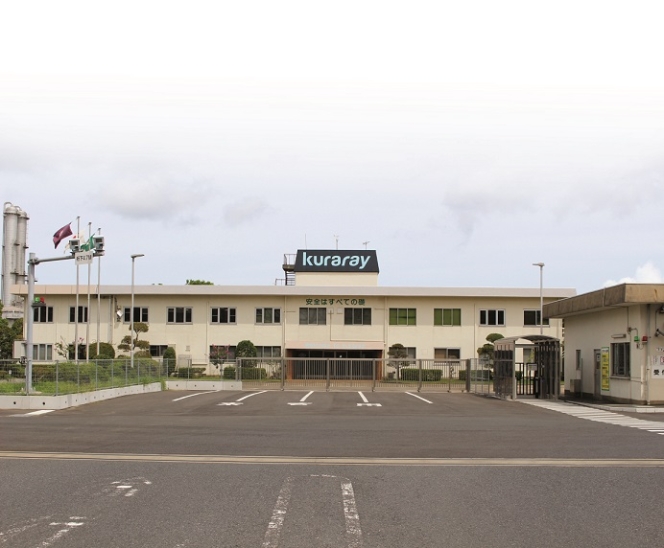
The most basic difference between an electric vehicle (EV) and internal combustion engine (ICE) tyre is that the former demands lower rolling resistance, quieter tread patterns and higher load bearing capacity. While there have been innovations within the tyre industry to meet the current demand for EV tyres, at the molecular level, research and development continues to achieve enhanced compound efficiency as tyre mixtures are complex.
As electric vehicles redefine performance benchmarks, tyre technology is undergoing a molecular-level overhaul. While the industry has focused on rolling resistance, noise reduction and load capacity, Japan’s Kuraray is pushing the boundaries deeper into the chemistry of rubber itself. By integrating silane-functionalised liquid rubbers into natural rubber-silica systems, the company aims to resolve longstanding formulation challenges. These innovations not only offer measurable improvements in abrasion resistance and wet grip but also open the door to broader adoption of sustainable materials in EV tyres. Kuraray’s work signals a strategic shift towards more efficient, adaptable and environmentally aligned tyre compounds.
Japan-based chemicals manufacturer Kuraray has dismissed all odds to achieve a more efficient molecular chemistry in tyres with its silane-functionalised liquid rubbers. In an earlier issue, Tyre Trends had reported how the company’s silane-modified rubber marked a major leap in tyre technology as it enhanced polymer interaction within the tyre, especially in natural rubber and silica-based formulations.
Coming to the present, its silane-functionalised liquid rubbers offer the reduction of rolling resistance (RR) and the resulting compound shows excellent balance of low RR, abrasion resistance and wet grip performance.
Speaking to Tyre Trends exclusively on the development, Technical Service Engineer for Quality and Product Development Department, Elastomer Division, Kuraray Co., Naoto Takahashi, divulged, “We propose to incorporate natural rubber (NR) for silica-based PCR treads. NR is preferable for its high strength and from the viewpoint of sustainability. However, the combination of NR and silica has typically been considered unusual as compounds for PCR treads. One of the reasons is that NR and silica have poor interaction, which causes decrease of physical properties.”
“Our silane-functionalised liquid rubbers can react with silica in the mixing stage and with NR in the vulcanisation stage. Using this technology, NR or silica-based compounds have been proven to have an excellent balance of lower RR and competitive abrasion resistance and wet grip compared to typical styrene-butadiene rubber, butadiene rubber and silica compounds. So we believe it has the potential for EV tyres, which require these properties,” he added.
Furthermore, using silane-functionalised liquid rubber in tyre manufacturing offers several advantages. Firstly, it provides a plasticising effect during the mixing stage, leading to lower torque and electricity consumption.
Secondly, the improved rolling resistance itself contributes to the sustainability goals by extending the driving range of EVs. Long-range EVs significantly reduce carbon dioxide emissions compared to fossil fuel-powered vehicles. This helps mitigate global warming and other climate changes. In addition, EVs with extended range reduce the burden on charging infrastructure and promote efficient energy use. Less frequent charging means reduced strain on the power grid.
Additionally, the improved performance of NR and silica compounds sheds light on the utilisation of NR, which is a kind of sustainable material. “We believe this technology could expand the potential of NR. If you are considering using more NR in your products, then this type of liquid rubber could be useful,” added Takahashi.
MIXING THE MIXTURE
Typically, it has been said that conventional silane coupling agents have poor reactivity with NR. This is not the case for silane-functionalised liquid rubbers. The liquid rubbers react with silica at the mixing stage by hydrolysis and condensation, in the same manner as silane coupling agents. As a result, the silica would be surrounded by hydrophobic liquid rubber chains. This helps silica to disperse well in the rubber matrix.
In the subsequent stage of vulcanisation, the reaction of liquid rubber chains and NR occurs. This forms bonds between two types of rubbers, effectively resulting in reinforcement of silica-NR interaction.
“We believe that these mechanisms contribute to maximising the potential of NR and silica combination,” said Takahashi.
The molecular weight of rubber is another key factor in determining the characteristics of liquid rubbers, alongside the glass transition temperature and monomer components.
Explaining how the molecular weight range of Kuraray’s liquid rubbers affect its compatibility and performance in tyre applications, the executive said, “Our liquid rubbers’ molecular weight range is strategically positioned between typical plasticisers and solid rubbers, ensuring an optimal balance of enhanced processing and physical properties.”
“Each grade’s molecular weight is precisely controlled and tailored to specific purposes and applications. Generally, liquid rubbers with lower molecular weights offer superior compatibility with other ingredients, while those with higher molecular weights provide better physical properties. Interestingly, the viscosity of liquid rubber alone does not determine the processability of compounds. We are glad to support you in selecting the ideal grade of liquid rubber to achieve your objectives,” he added.
He also noted that liquid rubbers have a low tendency to bleed out as a plasticiser because of their higher molecular weight and ability to be vulcanised. The low migration property directly affects the life span of the tyres.
Additionally, the improved abrasion resistance compared to traditional plasticisers also offers the long-term liability of tyres. “Wear particle is one of the biggest issues in today’s tyre industry because it has been recognised that it has a severe impact on the environment. The new regulation to handle this matter has been under discussion for a long time. Our silane-functionalised liquid rubbers would offer the solution to these challenges,” noted Takahashi.
COMPETITIVE EDGE
One of the characteristics of the material is its narrow molecular weight distribution. This provides the benefit of suppressing reduced physical properties due to the low molecular weight fraction. Another is that it has functional groups grafted onto the polymer chain. These functional groups seem to have different reactivity compared to other types of modification.
These features have a positive effect on the storage stability and other performances as tyres. The company highlighted that it has already found that the material would not deteriorate so much for 1-2 years in a bulk container under air.
Besides, the silane-functionalised liquid rubber technology is applicable to various types of tyres including winter and all-season tyres, and high-performance tyres. It is particularly beneficial in improving the dispersion of silica fillers, reducing compound viscosity and enhancing overall tyre performance. This technology helps achieve a balance between grip, low RR and abrasion resistance, making it suitable for a wide range of tyre applications.
Considering the characteristics of the material, another application of this type of material is TBR. Most TBR tyres use NR and carbon black (CB) compounds with less or no oils. However, using silica in place of CB in TBRs is getting more and more attention to achieve the high level of rolling resistance and wet grip performance. Here emerges the problem of NR and silica combination. As mentioned above, the silane-functionalised liquid rubbers would act as the effective additive for these kinds of compounds.
Commenting on the role of the liquid rubbers in enhancing wet or ice grip performance on winter tyres, Takahashi explained, “We have two types of silane-functionalised liquid polybutadiene with relatively higher glass transition temperature (Tg) and lower Tg. Initially,
we only commercialised the former one. However, in response to customer demand, we have developed another grade with lower Tg and are now fully equipped to mass-produce.”
“Liquid rubbers with lower Tg provide flexibility to the compounds even at low temperatures, which is particularly beneficial for the ice-grip performance of winter tyres. This flexibility ensures that the rubber remains pliable and maintains good contact with icy surfaces, enhancing traction and safety. Since the compound Tg is also highly affected by other components such as solid rubbers, plasticisers and resins, we think that our product lineup with different Tg offers freedom of choice for users’ compound formulation,” he added.
MEETING DEMANDS
The company continuously spoke with tyre manufacturers during the development of its liquid rubber. “We have instruments in our laboratory for measuring not only compound properties but also tyre performances such as wet grip and abrasion resistance. This allows us to have close and detailed technical communication with our customers,” said Takahashi.
He added, “The wet grip performance is usually expressed by the value of tanδ at 0 deg.C as an index from the viscoelasticity measurement. But the actual compound’s grip performance often shows a different result from the viscoelasticity. We have equipment to measure the friction coefficient of compounds on wet and icy surfaces, allowing us to minimise the discrepancy between viscoelasticity and grip performance.”
Alluding to how the use of silane-functionalised liquid rubber in EV tyres aligns with current trends and future directions in tyre technology, he said, “We recognise the growing trend towards sustainability as well as the importance of reducing rolling resistance and wear particles. Here, we recommend using NR more to address these issues. While the combination of NR and silica may not be the conventional choice for PCR tread compounds, we believe that our innovative approach demonstrates the potential of this formulation. The use of silane-functionalised liquid rubber offers the excellent dispersion and reinforcement of NR and silica compounds, paving the way for the solution to address future challenges in tyre technology.”
Takahashi indicated that the silane-functionalised liquid rubber can play a role in reducing the carbon footprint of tyre production. The key driver, he explained, is a measurable drop in rolling resistance, which translates into lower fuel consumption for internal combustion vehicles and reduced electricity use in EVs.
The firm also highlighted its broader sustainability efforts, noting that its liquid rubber plant is ISCC Plus-certified. From this year, Kuraray has started producing sustainable materials under a mass-balance approach – an initiative that includes its latest silane-functionalised grades, though the product range is still expanding.
On managing cost-performance trade-offs, he acknowledged that liquid rubber typically commands a higher price than traditional plasticisers. However, the benefits tend to supplement the cost.
The company pointed to challenges like dispersing high-surface-area silica in tread compounds – an area where its liquid rubber grades can provide a processing advantage. It also emphasised the potential of NR and silica combinations, made feasible with its silane-modified products, as an example of how formulation innovation can justify the premium.
Kuraray’s silane-functionalised liquid rubber represents a critical inflection point for tyre formulation – technically and environmentally. By enabling stable silica dispersion in natural rubber and forming durable crosslinks during vulcanisation, it addresses both performance and sustainability imperatives.
While the cost remains a consideration compared to traditional plasticisers, the material’s added value, such as reduced energy use, lower rolling resistance and extended tyre life, could redefine return on investments calculations for manufacturers. Its compatibility with evolving regulations on wear particles and carbon footprint reduction positions it not just as an additive but as a strategic material. The challenge ahead lies in scaling adoption without compromising economic efficiency.
Retreading’s Stubborn Struggle
- By Gaurav Nandi
- August 29, 2025
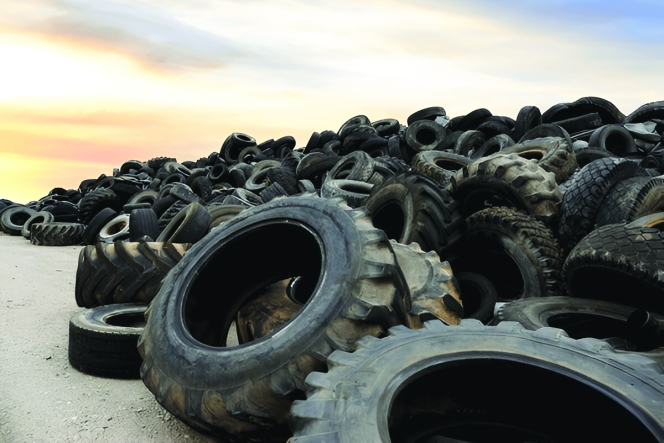
Despite decades of presence and proven sustainability benefits, the global truck tyre retreading industry remains mired in perception problems and systemic inertia. As raw material costs rise and environmental pressures mount, retreading should be a no-brainer. Yet, it continues to be sidelined by outdated mindsets, customer ignorance and a lack of cohesive industry messaging. Tirecore CEO Garry Drisdelle, in a candid interview with Tyre Trends, paints a picture of a sector at risk – not because it lacks value, but because it has failed to communicate it. The stakes, he warns, are too high for complacency.
Despite decades of existence, the retreading industry still wrestles with fundamental challenges across the world – not least the stubborn perception among customers and stakeholders about the true value of retreaded truck tyres. Tirecore Chief Executive Officer Garry Drisdelle pulls no punches in diagnosing the sector’s issues and outlining the uphill battle ahead.
Speaking to Tyre Trends, he said, “Tirecore is primarily a supplier of quality truck tyre casings to the retread industry. But while retreading should logically form the cornerstone of sustainable tyre use, the industry remains far from mainstream acceptance.”
“Educating the customers really as to how much upcycling, how much can we save – it’s beyond the pennies or pounds you save on the initial purchase,” Drisdelle said. Yet, frustratingly, many customers remain fixated on upfront costs instead of the total lifecycle value of a tyre.
This fixation, he implies, represents a systemic failure within the industry. “The industry has to do a better job towards educating the consumers, which primarily are fleet owners, beyond the initial purchase,” said Drisdelle. The inability to shift consumer mindset threatens to leave retreading as a niche rather than a necessity.
Tirecore positions itself primarily as a global supplier of high-quality truck tyre casings to the retread industry, operating across markets that include the United States, Canada and India. Rather than manufacturing or retreading tyres directly, the company serves as a critical node in the circular economy of commercial tyres, ensuring that valuable casings find extended life through retreading.
“We are in the business of preserving 85 percent of the tyre components existing material’s value saving valuable resources,” said Drisdelle.
The company’s operational model is rooted in the principle of upcycling over replacement, focusing on longevity and material reuse rather than disposability. While Tirecore’s precise logistical affiliations remain unspecified, its strategic direction is clearly aimed at aligning with sustainability mandates and evolving global market demands.
DISPOSABLE TREATMENT
Drisdelle highlights a critical contradiction. Tyres are one of the most safety-critical components on the road, yet they are taken for granted at a staggering scale. “Picture a truck is rolling down the highway at 100km/h pulling 20,000 kilogrammes of freight, riding on just 6-8-10 rolling rubber contact points. Tyres are one of the most critical transportation components, yet we treat them like disposable goods. How taken for granted is that product?”
Even as raw material prices surge and truck tyre costs climb, the entrenched perception treats tyres as disposable consumables. “We need to reframe the conversation – a tyre should be seen as an asset and not a consumable,” Drisdelle emphasises.
This disconnect reveals deeper issues prevalent within the industry. Retreading has not been effectively communicated as a financial and environmental beneficial in the long tome. Moreover, legislative inconsistency and lack of incentives for the industry as a whole is a deterrent that needs to be addressed immediately.
Drisdelle insists that retreading should be the environmental rallying point for the sector. “We have 85 percent of the material in the original product that is quite capable of being reprocessed and upcycled many times,” he said.
He contrasts upcycling favourably with recycling, which he argues requires more energy and effort than the original production process, especially in plastics and other materials: “By the time you just recycle something, the energy to recycle it is more than the process.”
Yet these arguments come with an implicit critique that the industry has failed to effectively translate this environmental rationale into a compelling value proposition for customers and regulators alike.
LEGISLATIVE MOMENTUM
Drisdelle points to potential legislation requiring truck tyres to be recyclable or retreadable as a possible catalyst for change. “Picture if legislation comes out that you’re not allowed to sell truck tyres unless they’re recyclable from their ingredients unless they’re retreadable,” he noted.
However, he quickly tempers this with realism stating, “We can never get to zero. That’s a cool little marketing thing but it’s an impossibility in the world of physics and science.”
This admission highlights the gap between aspirational sustainability goals and practical realities, a gap that leaves retreading vulnerable to accusations of greenwashing or insufficient progress.
ADAPT OR STAGNATE
Looking to the future, Drisdelle’s plan is pragmatic but cautious. “Our future plans are to keep up with the market demand, to evolve as the market evolves. Pivot and prosper,” he said.
Such a measured approach reflects the uncertainty and fragmentation within the industry. The promise of retreading remains strong, but without decisive action on education, regulation and innovation, the sector risks losing ground to cheaper, new tyres or alternative technologies.
The recurring theme throughout Drisdelle’s commentary is education, or rather, the lack of it. “The education of the fleet owners is primary to everything. The education of the industry to build a better tyre is somewhat secondary,” he stated.
This stark admission speaks volumes. Despite retreading’s environmental and economic advantages, a fundamental communication failure continues to hobble the industry.
Drisdelle points out the irony stating, “Without a widespread cultural shift in perception, retreading will struggle to move beyond a cost-saving niche for price-sensitive fleets to a mainstream standard.”
Drisdelle’s blunt assessment of the retread industry reveals a sector caught between its potential and its persistent shortcomings. Tirecore’s role as a global supplier to retreaders is clear but the wider challenge remains.
Without significant progress on education and regulatory backing, the retread industry risks remaining on the margins, overshadowed by the convenience of new tyres and the pressures of market inertia.
Retreading’s promise is substantial. But, as Drisdelle’s comments underscore, fulfilling that promise demands a candid reckoning with the industry’s educational failures and a relentless push for change or face stagnation in a rapidly evolving tyre market. n
India’s Tyre Recycling Industry Enters New Era With Gujarat’s Green Light To Continuous Pyrolysis
- By Gaurav Nandi
- August 28, 2025
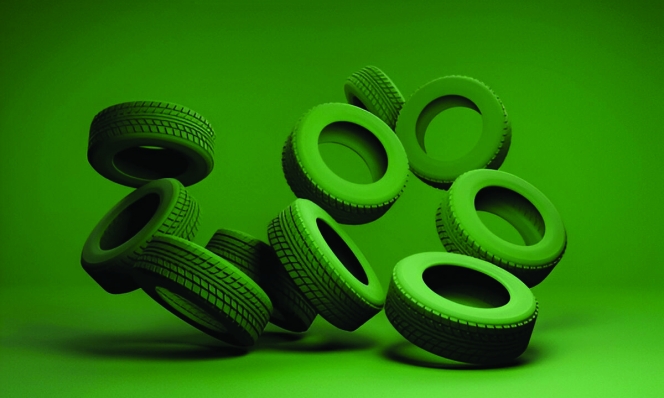
India’s tyre recycling sector, long plagued by fragmented operations and lax compliance, is undergoing a critical overhaul. With Gujarat’s recent approval for continuous pyrolysis plants, the industry is moving decisively towards cleaner, scalable and regulation-driven solutions. This shift signals more than a technological upgrade and it’s a rebuke of outdated batch systems and a call for formalisation, traceability and environmental accountability. As global demand for sustainable materials rises, India’s pivot positions it as a potential leader in circular economy practices. In conversation with TRRAI President Chetan Joshi, we explore how this development could redefine the future of tyre waste management at home and abroad.
India’s tyre recycling sector is on the cusp of a transformational shift with the Gujarat Pollution Control Board (GPCB) approving the establishment of continuous pyrolysis plants in the state. The move marks a significant departure from traditional batch-based tyre processing systems, promising to boost efficiency, environmental compliance and resource recovery at an industrial scale.
“This shift is nothing short of revolutionary,” said President of the Tyre and Rubber Recyclers Association of India (TRRAI) Chetan Joshi. “We’re moving from outdated, fragmented batch operations to streamlined, automated continuous pyrolysis systems. This is going to uplift the entire industry, from cleaner emissions to higher resource recovery, better traceability and serious investor interest. It sets a new national standard and will accelerate formalisation, industrial-scale operations and a far more sustainable approach across India.”
The approval has been met with optimism by recyclers and environmental advocates alike as it signifies a structural change in how end-of-life tyres will be handled in India, which is home to more than 1.8 million tonnes of tyre waste annually.
The Gujarat model mandates stringent adherence to environmental standards, particularly concerning air quality and emissions. Continuous pyrolysis plants approved under the new framework are required to incorporate top-tier pollution control mechanisms.
“We see compliance not as an obligation but as a core design principle. Our plants are being built with advanced air pollution control devices (APCDs), real-time emissions monitoring and automation that ensures consistent performance. We’re aligning with both GPCB and CPCB regulations through pro-active design, third-party audits and integrating global best practices. It’s not just about meeting today’s standards but staying ahead of tomorrow’s,” said Joshi.
The approach reflects a broader shift in the recycling sector, where regulatory compliance is no longer viewed as a hurdle but as a strategic advantage and market differentiator.
Industrial scale
Under the new directive, each continuous pyrolysis facility must operate at a minimum capacity of 60 tonnes per day (TPD). This scale reflects the government’s push to industrialise tyre recycling and eliminate inefficient, informal practices.
“Scaling to 60 TPD is a serious industrial commitment and it means heavy investment in automation, utilities, safety systems and logistics. But it’s also the only way forward. India generates over 1.8 million tonnes of end-of-life tyres annually. This scale allows us to handle the problem responsibly while creating traceable and economically viable recycling ecosystems,” Joshi said.
With India’s growing automotive base, the urgency to develop sustainable, high-capacity recycling infrastructure has never been higher.
One of the key advantages of continuous pyrolysis lies in its outputs that include valuable petrochemical byproducts like pyrolysis oil, sustainable fuels and recovered carbon black (rCB). These materials are increasingly in demand across a range of industries, from rubber manufacturing to renewable energy.
“These by-products are entering a new phase of global relevance. Recovered carbon black is being adopted in rubber, plastics and even pigments. Pyro oil, when upgraded, is a viable alternative fuel. We’re actively engaging with global buyers and certifiers to standardise and integrate these outputs into international supply chains. The world is ready for sustainable alternatives and it’s up to us to deliver with consistency and quality,” averred Joshi.
India’s entry into this global supply chain positions it not just as a recycler of waste but as a producer of sustainable industrial materials.
Circular economy
TRRAI views this milestone as more than an environmental success. It’s a step towards realising India’s vision of a circular economy, where tyre waste is fully reintegrated into the production cycle.
“We aim to be more than recyclers. We want to be circular economy enablers. That means building systems where tyre waste is traceable from collection to output, where value is recovered and re-injected into the economy. We’re developing collection infrastructure, digital traceability and offtake agreements with industries globally. This is not just about waste; it’s about resource optimisation and environmental stewardship,” Joshi explained.
Such a shift could significantly reduce the country’s carbon footprint while fostering job creation and industrial growth.
Despite the enthusiasm, industry leaders acknowledge that challenges remain, particularly in terms of adoption among legacy operators and infrastructure gaps.
“The biggest challenge is inertia as many operators are still working in the unorganised sector with outdated setups. Then there’s infrastructure as a hurdle as tyre collection networks are underdeveloped in many parts of India. To overcome this, we’re advocating policy changes, investing in reverse logistics and training the workforce. Regulatory clarity and enforcement will be key and we’re working closely with industry associations and government bodies to drive this,” said Joshi.
Stakeholders believe that education, investment and enforcement will be pivotal to ensuring widespread transition to continuous pyrolysis systems.
Global trends
Globally, countries like those in Europe and North America have already adopted advanced tyre recycling technologies. But Joshi believes India has a unique opportunity to leapfrog older systems and build world-class facilities from scratch.
“Europe and North America have a head start, especially in policy frameworks and end-use applications. But India’s opportunity lies in scale and adaptability. We can leapfrog legacy systems and build efficient, tech-driven plants from the ground up. If we get the ecosystem right – collection, compliance and capital – we can set new benchmarks, not just catch up. India could become a global hub for tyre recycling technology,” he said.
The industry’s fast pace of development combined with India’s manufacturing and engineering capabilities could make the country a case study in sustainable industrial transformation.
Innovations in emission reduction
In line with global best practices, TRRAI and its partners are integrating innovations to ensure safety and minimal environmental impact.
“We’re integrating closed-loop systems, AI-driven control logic and multi-stage gas cleaning technology. Real-time emissions data will be available both internally and to regulators. Safety protocols are built into every operational layer, from material feeding to shutdown procedures. We’ve also prioritised workforce training and regular third-party safety audits. The goal is to operate with zero compromise on health or the environment,” Joshi explained.
Such innovations are crucial not only to maintaining regulatory compliance but also to building public and investor confidence.
The entry of advanced technologies is expected to catalyse foreign investment and technical collaboration.
“Our approach is partnership-driven. We’re already working with European and Australian technology providers and are in discussions with institutional investors. We see India as a platform for co-creation, where global IP meets local scale and agility. Through industry associations like TRRAI, we’re building collaborative networks to ensure knowledge sharing, investment facilitation and joint innovation,” Joshi noted.
This strategy could help India become a global innovation hub for recycling technologies applicable across other emerging markets.
The vision
Looking to the long term, the industry’s goals extend far beyond domestic waste management. TRRAI envisions exporting its model to developing nations facing similar challenges.
“Our vision is bold but simple. It is to create a fully circular, scalable and replicable tyre recycling ecosystem. India should not only solve its own tyre waste crisis but become a global model for how emerging markets can tackle resource recovery. We see this model being exported to Southeast Asia, Africa and Latin America. With continuous pyrolysis, India can move from reactive recycling to proactive resource management on a global stage,” Joshi concluded.
As Gujarat lights the way with its approval of continuous pyrolysis plants, India’s tyre recycling sector is poised to become a beacon of innovation and sustainability – one that could shape the future of global recycling practices. n
Selling To Sellers
- By Gaurav Nandi
- August 27, 2025
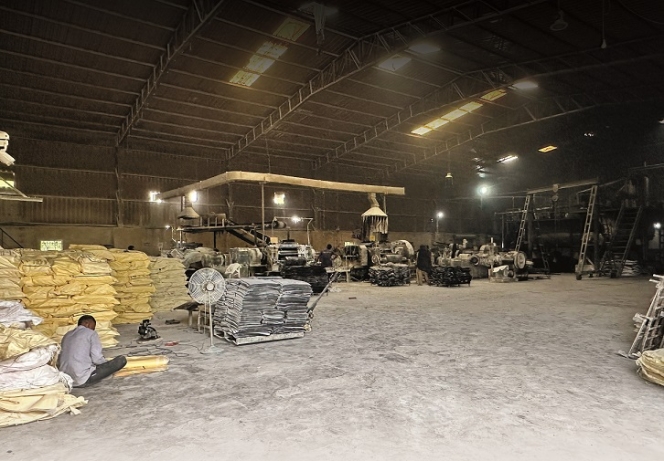
For decades, China has stood as the world’s dominant supplier of raw materials across industries, making it a significant player in the global supply chain. However, Gujarat-based Lead Reclaimed Rubber, an Indian MSME, has achieved a remarkable feat by exporting reclaimed rubber crumb to Chinese manufacturers. The company capitalised on India’s abundant scrap tyre supply and favourable policies, tapping into China’s massive demand for reclaimed rubber. As Lead Reclaimed Rubber continues to expand its production capacity and export markets, the company also faces challenges such as labour shortages, supply delays and regulatory concerns. Despite these obstacles, it remains optimistic about its growth prospects.
China has been the largest supplier of raw material for every industry known to man since decades. While there are many companies in different markets trying to sell back to China, an Indian MSME has unachieved the feat of selling to the ‘seller’.
Gujarat-based end-of-life tyre (ELT) recycler Lead Reclaimed Rubber has been exporting its reclaimed rubber crumb to Chinese manufactures. Commenting on how the company achieved this feat, Chief Executive Officer Jayeshh Patel told Tyre Trends in an exclusive interview, “China is the largest importer of reclaimed rubber, sourcing the material not only from India but also from countries like Vietnam and Sri Lanka. This demand is driven by a vast domestic market for tyres and inner tubes, with numerous brands operating in the aftermarket segment as well as in OEM manufacturing. As a result, the growth potential is significant.”
“While China has its own reclaim rubber plants, it faces limitations due to inadequate scrap tyre availability. In contrast, India has an abundant supply of scrap tyres supported by both domestic generation and strong import volumes. Additionally, India’s favourable government policies and the availability of skilled labour further enhance its position as a competitive and reliable supplier of reclaimed rubber to China. Hence, our company capitalised on the situation and started exporting,” he added.
Lead Reclaim Rubber was established in 2012 and is an NSE-listed company. It operates both in domestic and export markets with plans to grow its current production capacity as the reclaimed rubber market unfolds its potential.
Moreover, Patel noted that the Extended Producer Responsibility (EPR) framework by the Indian Government is playing a crucial role for the recycling industry for reaching greater heights.
EPR IMPACT
According to Patel, EPR has emerged as a transformative force in the recycling industry. Given the industry’s dynamic nature and its drive to adopt advanced technologies, EPR presents a timely and impactful mechanism to support growth particularly for micro, small and medium enterprises (MSMEs).
“While the recycling sector is evolving, recyclers often operate on thin profit margins, which limits investment in new technologies and process upgrades. EPR has helped bridge this gap. Under the scheme, we are awarded green credits for every kilogramme of end-of-life tyres we recycle. These credits are a compliance requirement for tyre manufacturers, who purchase them from registered recyclers like us. For every 100 kilogrammes of tyre recycled, we receive approximately 130 green credits, each valued at INR 2.5, resulting in a direct financial incentive. This additional income strengthens our balance sheet and can be reinvested in research and development, capacity expansion and technology upgrades. In this way, EPR indirectly fosters innovation and scaling in the recycling ecosystem,” said Patel.
To maintain accountability and transparency, the Central Pollution Control Board (CPCB) has developed a digital portal where all stakeholders must report data.
“We record our incoming feedstock (purchase data) and outgoing materials (sales invoices) on the CPCB portal. This data forms the basis for calculating green credit eligibility. Our operations are routinely audited by both government agencies and the tyre industry. These audits verify that we meet all technical and environmental standards before credits are approved. The government has also established baseline electricity usage norms for tyre recycling. We are required to submit our electricity bills to demonstrate compliance. If our energy consumption does not meet the defined threshold, we are ineligible for green credits, preventing fraudulent claims,” he Patel.
He optimistically contented that EPR is rapidly becoming the backbone of the tyre recycling industry. For over a decade, recyclers have struggled with limited access to capital. EPR is now enabling financial stability, paving the way for recyclers to professionalise operations, scale sustainably and drive forward-looking initiatives. This policy is not just a support mechanism but a growth enabler.
AN OVERVIEW
The recycling company focuses on sustainable practices and high-quality output. “Our core operation involves sourcing EOL tyres and tubes from various states across India for recycling into value-added rubber products. Our recycling process begins with a proprietary feedstock checking system to ensure quality. The tyres are then sorted, cut and processed into crumb rubber powder. Currently, we produce crumb in 30–40 mesh sizes with plans to expand into finer 80 and 120 mesh grades in the near future,” explained Patel.
For the domestic industry, crumb rubber serves a wide range of applications. Finer meshes (80 and 120) are used in various rubber and dye industries, while 30–40 mesh is commonly used in bitumen modification for road construction, in line with the Central Government’s CRMB 30 guidelines.
Furthermore, the company employs a green devulcanisation system that utilises steam, oil and pressure to break down and re-bond the rubber polymers from EOL tyres. This method is 100 percent sustainable, producing zero discharge and zero wastage. Even the steam generated during the process is condensed and reused. “We are in the process of acquiring a Z-Certificate for our zero-waste operations,” divulged Patel.
Post-devulcanisation, the rubber material becomes soft and slightly sticky due to the restructured cross-linking. It then undergoes further processing in the reclaim section, which includes refiners, mixing mills and a cleaning stage.
During cleaning, all metallic and non-rubber impurities are extracted using strainers with 60-millimetre wire mesh. The purified compound is extruded into noodle form and sent to the refiners to produce the final reclaimed rubber product, typically in seed form.
“We tailor our reclaimed rubber to meet the specific requirements of our customers including thickness, size and performance properties. Each product is made to specification. The reclaimed rubber is used across various industries including tyre and tube manufacturing, conveyor belts, packaging and other rubber-based products. As industries increasingly shift from virgin to reclaimed rubber, we position ourselves as a reliable and environmentally responsible supplier,” noted Patel.
PRODUCTION AND SUPPLY
According to Patel, virgin rubber contains about 90–100 percent RSPL, while reclaimed rubber has around 50–52 percent. It’s more affordable than virgin rubber, but the use of 100 percent reclaimed rubber in tyre manufacturing is still a distant thought.
However, it’s widely used in rubber mats. Tyre manufacturers are gradually increasing reclaimed rubber usage, encouraged by government directives to reduce dependence on natural resources and imports. Since local virgin rubber production is insufficient, it’s being imported from countries like Vietnam.
Currently, large tyre manufacturers in India use only a small percentage of reclaimed rubber, around two to three parts per hundred
rubber (PHR). For cycle and three-wheeler tyres, it goes up to 20 PHR. Conveyor belts use up to 30 percent, and in non-critical applications with almost no performance impact, reclaimed rubber can be used up to 95 percent.
The company’s plant is located in Katlal, Kheda, near Ahmedabad, and it uses Indian machinery sourced from Punjab. “We started production at 250 metric tonnes per month. After Covid, we scaled up to 490 metric tonnes and recently reached 960 metric tonnes per month. Within the next year, we plan to expand further to 2,000 metric tonnes per month,” said Patel.
He added, “We run our plant with TBR tyres both nylon and radial. We’re centrally located in Ahmedabad and as Gujarat shares borders with Rajasthan, Madhya Pradesh, Maharashtra, and the southern states, it helps us with tyre sourcing. We collect tyres through a three-layer supply chain consisting puncture shops, rag pickers and aggregators. The aggregators sort the tyres as per our requirements.”
For nylon tyres, the company only uses the centre portion, specifically from 1020 tyres and discards the sidewalls. For radial tyres, it recycles the entire tyre. The recycling technology is the same for both, but the processing recipe differs. Radial tyres have cords in the centre, so the devulcanisation process is slightly modified to handle the added strength. Its research and development facility are located inside the plant.
Commenting on what sets the company apart from competitors, Patel explained, “Our focus on consistency and timely delivery sets us apart from competitors. We maintain a 95 percent consistency ratio. From raw material to the final product, everything is monitored and controlled by our control plant, which is also a key differentiator. We also have an in-house development department that not only ensures quality consistency but also works on improving the benefits for our customers. On top of that, we conduct awareness programmes to educate our customers on which materials are best suited for different use cases. That’s something others in the industry usually don’t do.”
MARKET SPREAD
Lead Reclaim Rubber serves both domestic and international markets. Among the industries it caters to, conveyor belts account for 30 percent of its business, tyres for 20 percent and the remainder comes from rubber products and packaging. Although the tyre and tube segments currently represent a smaller share of revenue, Patel anticipates significant growth in these areas. Over the next five years, it expects tyres and tubes to become its largest consumer segment followed by conveyor belts.
The company attributes this projected growth to the government’s strong emphasis on the circular economy and the rapid expansion of the automobile industry, both of which are likely to increase demand for reclaimed rubber.
The company exports to several countries including Sri Lanka, China, Bangladesh, Turkey and Philippines. China is currently the largest consumer in its export portfolio, followed by Sri Lanka. According to the Patel, export markets generally use more reclaimed rubber due to their larger production capacities.
The export market continues to show strong demand and the company currently has pending orders from China.
However, as European nations vie for restricted EOL tyre exports to India, the scenario for indigenous recyclers can be precarious. Commenting on the potential impact of such restriction, Patel highlighted, “India recycles a significant portion of the scrap tyres it generates. However, unregulated and illegal pyrolysis operations remain a critical concern. These units often operate without environmental compliance, posing risks to public health and the environment. Stronger government intervention and regulatory enforcement are urgently needed to eliminate such practices and ensure sustainable recycling.”
“India’s tyre recycling ecosystem is diverse and imbalanced. While there are numerous recyclers, the segment is dominated by pyrolysis players (approximately 70 percent), with reclaim rubber manufacturers constituting only around 30 percent. This heavy skew towards pyrolysis is problematic, especially since many of these players depend on imported scrap tyres for feedstock. If the import of scrap tyres into India is disrupted, it will create a significant supply shortage, driving up the price of ELTs. Currently, the price of scrap tyres ranges between INR 18–21 per kilogramme, but a halt in imports could potentially increase this to INR 40 per kilogramme, a nearly 50 percent spike, which would severely impact the entire recycling value chain,” cautioned Patel.
Besides this looming issue, Patel highlighted several pending challenges for the industry. One of the primary issues is a shortage of skilled labour. Interestingly, even as the industry moves towards greater automation, the demand for labour continues to rise.
Another challenge is supply delays caused by aggregators, who often fall behind on delivery timelines due to their own labour shortages. Additionally, maintaining quality consistency is difficult as scrap tyres vary in composition from batch to batch. As a result, the company must closely monitor and control its processes.
A significant concern affecting future growth is the regulatory environment. The company remains cautious about expanding production because of the current ban on scrap tyres.
Although the business is regulated, there’s an underlying fear that stricter government action could further limit the supply of scrap tyres. Such restrictions could leave newly built expansion units underutilised.
Patel believes that unless government policies become more supportive, major investments and expansions will remain risky.
Looking ahead, Lead Reclaim Rubber is planning both forward and backward integration. On the forward side, the company aims to start manufacturing rubber tiles made entirely from rubber granules, a by-product of its current process. It also plans to enter the cycle tyre industry.
As part of its backward integration strategy, the company intends to set up more tyre collection centres both internationally and within various Indian states to secure a more consistent supply chain.
Challenges That Hinder Progress
- By Gaurav Nandi
- August 26, 2025
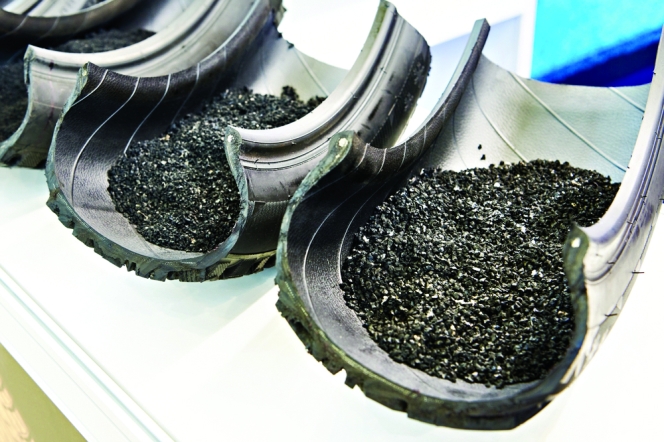
Despite two decades of reform, Europe’s tyre recycling ecosystem remains mired in regulatory inertia and market fragmentation. While the EU successfully curbed tyre landfilling in the early 2000s and achieved high collection rates, true circularity remains elusive. Over half of collected tyres are still incinerated rather than recycled into new products. The lack of mandatory recycled content targets, harmonised end-of-waste criteria and coherent eco-design regulations continue to stall progress. As environmental stakes rise and end-markets like artificial turf face bans, EuRIC’s latest manifesto lays bare the urgent need for systemic reform, spotlighting persistent policy voids, legal ambiguities and missed opportunities across the value chain.
Europe’s tyre recycling challenges have been building for over two decades. Back in 1999, the European Union banned tyre landfilling under Directive 1999/31/EC. This forced a major shift, and by 2003, landfilling tyres was officially prohibited. At that point, Europe still struggled to manage the sheer volume of end-of-life tyres (ELTs), often resorting to incineration or exporting them for disposal elsewhere.
Since then, collection rates improved dramatically, from around 25 percent in the mid-1990s to nearly 95 percent by 2010, but recycling quality remained substandard. Although most ELTs were collected, half were used for energy recovery, not material recycling. True circular solutions like reusing rubber in new tyres have lagged due to technological and regulatory hurdles
Complex EU regulations, limited mandates on recycled content and ecological concerns slow innovation. Over the past few years, initiatives like Life Green Vulcan, BlackCycle and policy push from the European Recycling Industries’ Confederation (EuRIC) show growing momentum, but real impact is yet to be seen.
EuRIC has been constantly advocating reforms that would change the course of the continent’s tyre recycling space with its recent manifesto delving into the immediate steps that ought to be undertaken to strengthen the tyre recycling industry.
EuRIC, through its Mechanical Tyres Recycling Branch (MTR), outlined a comprehensive vision for strengthening Europe’s tyre recycling sector. With over five million tonnes of tyres produced annually in the EU and around three million tonnes becoming ELTs, only about half are recycled – the rest are incinerated. EuRIC underscores the environmental advantages of mechanical tyre recycling and advocates for prioritising it over energy recovery to align with circular economy goals.
Speaking to Tyre Trends on the biggest obstacles to implementing mandatory recycled rubber content targets in new tyres and how industry collaboration can help overcome them, EuRIC’s Technical Advisor for tyres, Gabriel Gomez, mentioned, “Currently, the main regulatory challenge is the lack of a mandate from the authorities to define how and when the mandatory recycled content targets are to be implemented. We have received good feedback from the manufacturers in Europe regarding their willingness to include these targets. However, there is a need for a solidly defined regulatory framework that guarantees a level playing field in the tyre value chain and promotes innovation in this area.”
“The main risk of failing to implement harmonised end-of-waste criteria lies in the growing, practical need for a defined set of criteria to determine end-of-waste status. If the EU delays further in the creation of harmonised end-of-waste criteria, this will push member states to create their own national criteria, which could vary significantly and prove incompatible. This fragmentation would lead to market disruption, create confusion across the value chain and introduce legal uncertainty – all of which would ultimately weaken the European recycling industry and its competitiveness,” he added.
He noted that EuRIC strongly supports a complete ban on the export of tyres and tyre shreds for incineration or landfilling. These practices represent a misuse of valuable resources that should be reintegrated into the economy and clearly contradict the waste hierarchy in the European Waste Framework Directive.
“EuRIC, representing Europe’s tyre recyclers would welcome swift implementation of such a ban, especially since existing tools such as the Waste Shipment Regulation are already being used to prevent exports to operators and facilities that do not ensure environmentally sound treatment of these materials,” noted Gomez.
THE MANIFESTO
The recently published manifesto by EuRIC proposes five key policy actions to address systemic barriers and unlock the potential of tyre recycling. First, it calls for mandatory recycled content targets – 10 percent for new tyres and 20 percent for automotive parts – to stimulate demand and reduce reliance on virgin rubber. Public procurement and financial incentives like VAT reductions are also suggested to support this demand shift. Currently, artificial turf accounts for a major share of ELT-derived rubber, but impending bans on micro-plastics threaten this end-market, making policy support more critical.
Second, EuRIC demands a ban on the export of unprocessed and shredded waste tyres outside the EU. ELTs are often exported to regions with weak environmental controls, where they are landfilled or incinerated. Countries like India have become significant importers, raising environmental and regulatory concerns. To counter this, EuRIC stresses the need for strict enforcement of the EU’s Waste Shipment Regulation and advocates for EU-wide end-of-waste (EoW) criteria to facilitate trade within the EU and promote high-value recycling.
Thirdly, the manifesto emphasises the importance of eco-design in tyres, urging that tyres be made retreadable, recyclable and free from hazardous substances. Innovations like self-sealing and noise-reducing foams, while performance-enhancing, impede recycling and can even cause fires during shredding. EuRIC supports the Ecodesign for Sustainable Products Regulation (ESPR) and wants tyre manufacturers to bear the cost of non-recyclable designs.
Fourth, EuRIC promotes the Digital Product Passport (DPP) as a key enabler of recycling efficiency. Current data on tyres is insufficient; hence, they propose leveraging RFID technology to track chemical composition and recyclability through a centralised database. This transparency would help recyclers better handle materials and comply with chemical regulations.
Lastly, the manifesto addresses the need for a science-based chemicals policy that supports recycling rather than undermining it. The current trend towards hazard-based regulation with near-zero thresholds for certain chemicals risks sidelining recycled materials. EuRIC urges a shift towards risk-based assessments, transparent
testing methods and harmonised standards to ensure recycled materials remain viable in the EU’s green transition.
TOWARDS RECYCLABILITY
According to Gomez, mechanical tyre recycling is a recycling method for rubber that has stood the test of time. It remains the most common and best-established route for recycling tyres in Europe with the technology offering high-quality output. It also has the added value that it can serve as a reliable supplier for further processing technologies dealing with vulcanised rubber. Recycled rubber from ELTs offers significant potential for technologies that require a uniform and predictable input to maintain control over industrial processes.
Nonetheless, over three years after rubber from ELTs was prioritised, no regulation has materialised yet. Commenting on what lead to the stalling, Gomez noted, “The past year has brought major changes at EU level with the start of a new Commission mandate, which may explain the shift in priorities. However, at EuRIC we are working closely with manufactures and policymakers to keep the issue high on the agenda. We see harmonised EoW criteria as a key opportunity to align the interests of recyclers and manufacturers. Harmonised EoW criteria would bring significant benefits for the entire value chain, from boosting investment and legal certainty to increasing the uptake of recycled materials.”
Alluding to whether the current EU chemicals legislation, especially restrictions on substances like PAHs, appropriately balances environmental protection with the needs of a circular economy or does it unintentionally favour virgin materials, he stated, “It is not a matter of favouring virgin materials. The main issue is that the current legislation is not designed to consider that the materials in an article may have more than one life. Whenever the legislation targets the content of a substance in a recycled material, sometimes it fails to consider the real exposure to the substance based on the application and the nature of the material.”
Digital Product Passport is another vital tool for the entire industry’s circularity goals. While it is still in its early stages, EuRIC notes that there are projects that target the implementation of the DPP in tyres and it is optimistic about the possibilities this tool offers to the industry. Amongst the information that the DPP should make available for recyclers is the contents of substances of concern and hazardous substances as well as any substances or features that would hinder the recycling of the tyres. With this information in hand, the recyclers will be able to sort the tyres in a manner that allows for safer recycled products and more efficient processing.
PERSISTENT HURDLES
According to Gomez, illegal or poorly regulated exports of tyres create serious problems both economically and environmentally. They drain valuable raw materials from the EU and risk harming the environment and public health in importing countries if ELTs are not treated in an environmentally sound manner.
Furthermore, the loss goes beyond the economic aspect when it comes to the materials used on tyres. Incinerating ELTs destroys a valuable resource like rubber and locks us into a linear economy model that’s no longer fit for purpose. Recycling, on the other hand, and overall circularity of tyres, keeps materials in the loop, boosts resilience and contributes to EU sustainability and competitiveness.
A strong starting point to combat illegal exports would be the rigorous enforcement of the Waste Shipment Regulation, specifically targeting ELT exports. If recyclers can count on a steady, reliable supply of materials, they will invest. Increased availability of material and supply security are essential to encourage investments in recycling.
“An important take-away of the policy related to tyre recycling is that tyres should be treated as strategic resources, not just waste. Tyres are essential to every economy activity and inevitably reach its end-of-life stage. This makes it critical to regulate the full lifecycle, from design to disposal, with circularity in mind. Aligning on principles, like prioritising recycling over landfilling or incineration, would already be a big step forward globally,” averred Gomez.
Commenting whether Europe’s mechanical recycling infrastructure is equipped to handle a sharp increase in ELTs if exports are banned, he mentioned, “The mechanical tyre recyclers in Europe are determined to meet the challenge and tackle the increase in ELTs if an export ban is implemented. However, unlocking further capacity and investments in future development projects depend on regulatory certainty. That means a guaranteed level playing field through harmonised EoW criteria, recycled content targets and eco-design for improved recyclability. With the right framework and tools, uncertainty can be removed and investments will follow.”
While the mandatory recycled content requirements are essential to boost recycling, complementary short-term financial incentives, whether market-based or fiscal, are equally necessary to close the price gap between primary and recycled materials. Fiscal incentives, such as reduced VAT rates for recycled materials and products made from recycled materials, can play a major role in encouraging uptake. Green public procurement also holds substantial potential to stimulate demand for more sustainable and circular products.
Recycled materials from ELTs have real potential in the EV supply chain. Interest is growing, and EuRIC is confident that recycled rubber can be a reliable, high-quality material to support the shift to greener mobility.
Gomez noted that there are many encouraging examples of manufacturers incorporating recycled and sustainable materials into tyre design. A great advantage that recycled materials from ELTs offer is the availability of high-quality recycled raw materials that reliably allow manufacturers to experiment and innovate as they know that the recycling industry is capable and ready to deliver.
Comments (0)
ADD COMMENT