Goodyear Introduces Industry’s First Tyre To Use Carbon Black Produced Via Methane Pyrolysis
- By TT News
- May 15, 2023
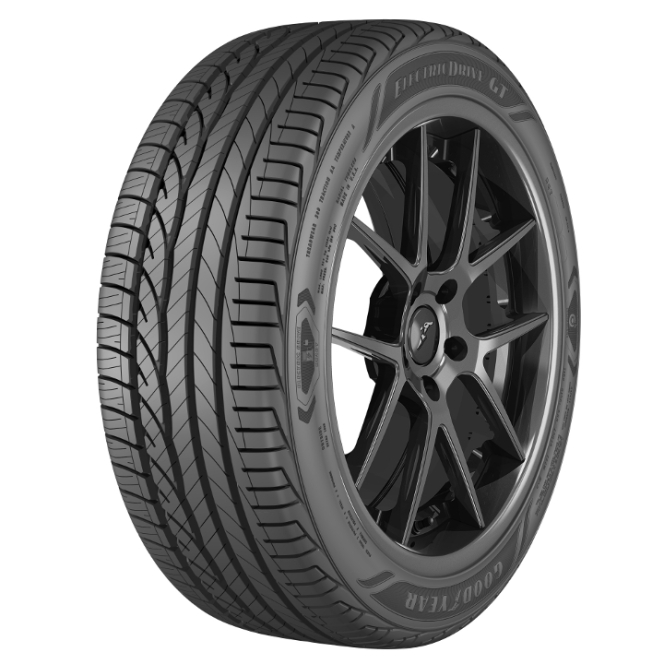
Goodyear Tyre developed a unique tread compound that contains Monolith carbon black produced from methane pyrolysis as part of its zero-emission carbon black in the tyre production programme.
The US tyre manufacturer and Monolith, a global leader in creating clean hydrogen and materials, entered into a collaboration agreement in December 2021 for the development and potential usage of carbon black made from methane and/ or biomethane for its tyres.
Its ultra-high performance, all-season ElectricDriveTM GT tyre, designed for electric vehicles, in size 235/40R19, will feature the new tread formulation.
This tyre, which will be made with this particular carbon black, is the first one available for purchase in the market that uses Monolith’s brand of carbon black.
Traditional carbon black typically comes from burning fossil fuels, but Monolith’s plasma-based process uses renewable power to complete methane pyrolysis, producing only carbon and hydrogen with no need for combustion. Methane can be broken down into its carbon and hydrogen atoms through a process called methane pyrolysis.
“At Goodyear, we are continually looking at and working with our supply base to understand and discover innovations and technologies to use in our products,” said Chris Helsel, senior vice president of Global Operations and Chief Technology Officer. “The use of carbon black produced by methane pyrolysis is an example of how we are collaborating with our suppliers, like Monolith, to utilize sustainable materials in our consumer products without compromising on performance and safety.”
“Working with innovative partners to incorporate sustainable ingredients is at the core of what we do, and Goodyear has been at the forefront of that mission,” said Rob Hanson, co-founder and CEO, Monolith. “We’re thrilled for the tire made with Monolith carbon black to launch and excited for the continued product research and development in this industry-leading partnership.”
The company plans to explore expanding the Monolith carbon black produced via methane pyrolysis across additional product lines in the coming years.
Goodyear also plans to continue to investigate with Monolith the potential use of new technologies, such as the use of carbon black produced from methane derived from waste sources.
Yokohama Rubber Eliminates Counterfeit Wheel Operation In China With Local Authorities’ Support
- By TT News
- June 25, 2025
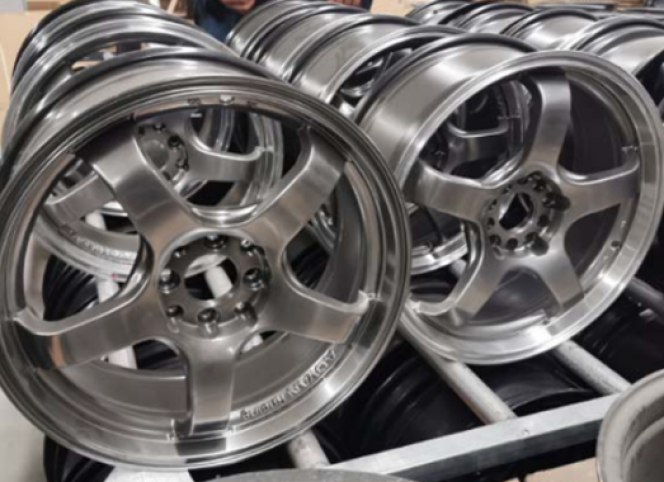
Yokohama Rubber completed enforcement action to halt the production and distribution of counterfeit versions of its “ADVAN Racing” aluminium wheels in China following a coordinated investigation with local authorities.
The Japanese tyre and wheel manufacturer filed an administrative complaint with the Municipal Administration for Market Regulation in Anlu City, Hubei Province, after uncovering a local manufacturer producing unauthorised copies of its high-performance wheels for sports cars.
Authorities in Anlu conducted a raid at the site in November 2024, seizing all counterfeit wheels. A subsequent investigation led to the identification of another company that had commissioned the counterfeit production. Administrative penalties were imposed on the ordering party, including a fine and an order to cease all illegal activity and surrender any remaining fake products.
This marks Yokohama Rubber’s latest successful enforcement action in China. The company had previously filed complaints targeting distributors of counterfeit wheels, resulting in the removal of fake products from the market.
“Yokohama Rubber remains resolute in its stance against the infringement of intellectual property rights, including the production and sale of counterfeit goods, and will strengthen its efforts against such illegal activities in Japan and overseas to ensure that its customers around the world are confident and secure in the knowledge that they are using genuine YOKOHAMA products,” the company said in a statement.
Tosoh Corporation to Build Second Chloroprene Rubber Plant in Japan with £460 Mln Investment
- By TT News
- June 13, 2025
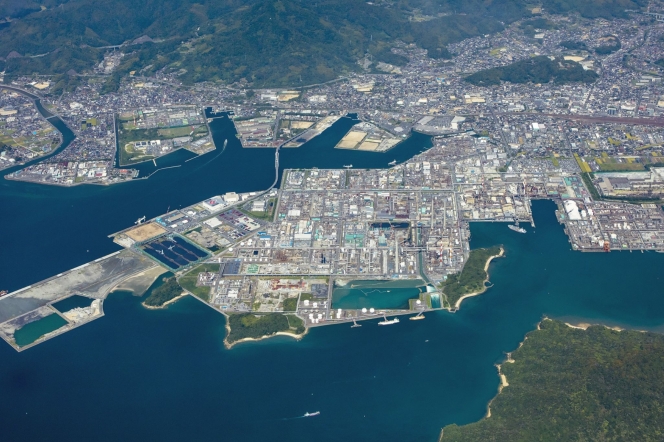
Japanese chemical manufacturer Tosoh Corporation announced plans on Wednesday to construct a second chloroprene rubber production facility at its Nanyo Complex, representing an investment of approximately ¥75 billion (£460 million) to meet rising global demand for the speciality polymer.
The new facility, scheduled to begin construction in spring 2027, will add 22,000 metric tonnes of annual production capacity for Tosoh’s SKYPRENE chloroprene rubber brand. Commercial operations are expected to commence in spring 2030 at the Shunan City site in Yamaguchi Prefecture.
Chloroprene rubber serves as a critical component across multiple industries, from automotive manufacturing to medical applications. The synthetic rubber’s popularity stems from its exceptional resistance to oil, weather conditions, and flame exposure, making it suitable for demanding applications, including automotive hoses, industrial belts, adhesives, and medical gloves.
The expansion comes as global demand for high-performance polymers continues to grow, driven by increasing automotive production and stricter safety requirements across industrial sectors. Medical applications have also seen increased demand following heightened awareness of the requirements for protective equipment.
Tosoh’s decision to double down on chloroprene rubber production reflects the material’s position within what the company terms its “Chemical Chain Business” - a strategy focused on value-added speciality chemicals rather than commodity products.
The investment represents one of the larger capacity expansion projects announced by Japanese chemical companies this year, signalling confidence in long-term demand fundamentals despite current global economic uncertainties.
The Nanyo Complex already houses Tosoh’s existing chloroprene rubber operations alongside other chemical production facilities. The site’s established infrastructure and logistics capabilities influenced the decision to expand at the existing location rather than develop a greenfield facility.
Industry analysts note that the three-year construction timeline reflects the technical complexity of chloroprene rubber production, which requires specialised equipment and stringent safety protocols due to the chemical processes involved.
The expansion aligns with broader trends in the Japanese chemical industry, where companies are increasingly focusing on high-margin speciality products to offset competitive pressures in traditional commodity chemicals from lower-cost Asian producers.
Epsilon Carbon Launches N134 Specialised Hard Grade Carbon Black In India
- By TT News
- June 12, 2025
Epsilon Carbon, a leading global manufacturer of carbon black, has launched N134, which it claims is a specialised ‘Hard Grade’ carbon black known for its superior abrasion resistance and durability.
At present, the high-quality N134 grade is being imported due to the lack of consistent quality and supply chain issues in the Indian market. As a result, the tyre makers have to modify their formulations using other grades of carbon black, which it shared often leads to reduced performance.
But now, Epsilon Carbon has become the first company in India to install a dedicated manufacturing unit designed for N134 grade hard carbon. The company is expanding its existing Vijayanagar Carbon complex facility to produce 215,000 tonnes of carbon black.
This will not only ensure consistent supply of N134 carbon black for tyre makers in the country, reduce import dependency, but also open up export potential to markets such as Europe and USA. Epsilon Carbon will also focus on integrate advanced processing techniques to ensure batch consistency for durability and performance.
Vikram Handa, Managing Director, Epsilon Carbon, said, “This is a proud moment for us and for India’s carbon black manufacturing sector as the high quality N134 black will significantly reduce import dependency and provide tire manufacturers in India and abroad with a reliable, high-quality product. Our goal is to match global standards while building India’s capability to serve premium markets.”
Lummus Technology And InnoVent Renewables Partner To Advance Global Tyre Pyrolysis Solutions
- By TT News
- June 11, 2025
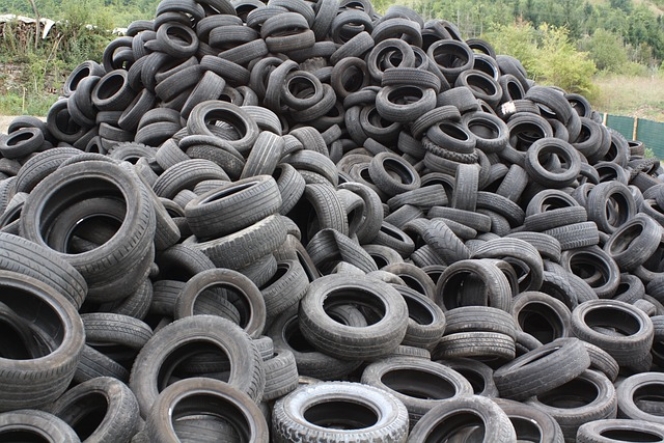
Lummus Technology, a leading provider of process technologies and energy solutions, has signed a memorandum of understanding (MoU) with InnoVent Renewables to collaborate on the global licensing and deployment of InnoVent’s continuous tyre pyrolysis technology.
Under the proposed agreement, Lummus will become the exclusive licensor for InnoVent’s proprietary pyrolysis process, which transforms end-of-life tyres into valuable outputs, including pyrolysis oil, gas, recycled carbon black and steel. Additionally, Lummus will offer integrated technology packages that combine InnoVent’s pyrolysis system with its own downstream processing solutions, enhancing the value of fuel and chemical products derived from waste tyres.
InnoVent’s technology provides a fully scalable, end-to-end solution for converting discarded tyres into renewable fuels and high-value petrochemicals, covering everything from pre-processing to purification. The company currently operates a commercial-scale facility in Monterrey, Mexico, with an annual processing capacity of up to one million passenger tyres, and has the capability to expand further.
Leon de Bruyn, President and Chief Executive Officer, Lummus Technology, said, “This is another significant step in expanding and strengthening our portfolio for the circular economy. By combining InnoVent’s tyre recycling technology with Lummus’ global licensing and engineering expertise, we will be addressing the global challenge of waste tyres and creating new pathways for sustainable product development.”
Vibhu Sharma, Chief Executive Officer, InnoVent Renewables, said, “Partnering with Lummus has the potential to accelerate the global deployment of our technology and help us address the environmental and public health challenges of one billion end-of-life tyres that are disposed of annually. Together, we can transform waste into valuable resources, reduce carbon emissions and support the transition to a more sustainable future.”
Comments (0)
ADD COMMENT