- Bridgestone
- Tokai Carbon
- Kyushu University
- Okayama University
- Recovered Carbon Black
- Carbon Black
- Eco Carbon Black
- Virgin Carbon Black
Joint Project Launched To Advance Performance Properties And Production Of Recovered Carbon Black
- By TT News
- January 31, 2025
Tokai Carbon Co., Ltd., Bridgestone Corporation, Kyushu University and Okayama University have started a technology development project to perform secondary processing on recovered carbon black (rCB) extracted from polymer products like end-of-life tyres containing rubber in order to create new eco carbon black (eCB) from these and other sources. With rubber reinforcing qualities comparable to those of virgin carbon black (vCB), which is made from coal and petroleum, the initiative seeks to transform these resources into eCB. Through the development of cutting-edge recycling technologies, the collaborative project partners want to contribute to the attainment of a circular economy and carbon neutrality.
This project is a component of the ‘Technology Development for Carbon Recycling from Polymer Products Including End-of-Life Tires’ demonstration programme, which was put out by Tokai Carbon in collaboration with Bridgestone, Kyushu University and Okayama University. The New Energy and Industrial Technology Development Organisation (NEDO) chose the project on 23 December 2024, under the heading of ‘Green Innovation Fund Project/Technology Development for Manufacturing Plastic Raw Materials Using CO₂ etc’.
In order to recover and utilise rCB, efforts are already in progress to pyrolyse polymer materials, including rubber from tyres that are nearing the end of their useful lives. Nevertheless, there are still obstacles to overcome before rCB may be used practically in new tyres. Because it contains so many contaminants, rCB performs worse than vCB when it comes to rubber reinforcement. Additionally, heat recovery produces CO2 emissions even if many end-of-life tyres are successfully used as fuel. The demand for tyres is predicted to increase in tandem with the projected expansion in the automotive and transportation sectors. The goal of these initiatives is to improve resource circulation by making it easier to recycle vCB, a crucial component of tyres.
Bridgestone, Kyushu University and Okayama University's knowledge and technologies will be combined with Tokai Carbon's own technologies and skills gained from manufacturing carbon black. The goal of the collaborative project is to create technologies that will eliminate impurities from rCB and create eCB with better rubber reinforcing qualities. By fiscal year 2032, the initiative aims to set up a demonstration unit that can produce 5,000 tonnes of eCB annually. The research will also concentrate on creating unique polymer/carbon composites that allow carbon black to be reused without pyrolysing tyres that have reached the end of their useful lives. With these efforts, the collaborative project participants hope to achieve enhanced recycling of scarce materials and contribute to lowering the CO2 emissions linked to the manufacturing of carbon black and the recycling of end-of-life tyres.
Tosoh Corporation to Build Second Chloroprene Rubber Plant in Japan with £460 Mln Investment
- By TT News
- June 13, 2025
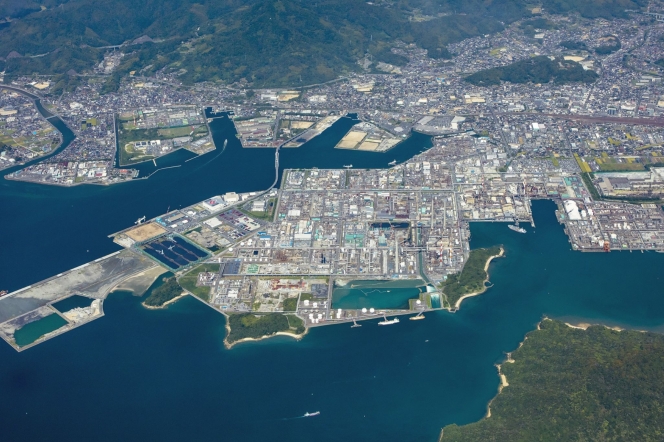
Japanese chemical manufacturer Tosoh Corporation announced plans on Wednesday to construct a second chloroprene rubber production facility at its Nanyo Complex, representing an investment of approximately ¥75 billion (£460 million) to meet rising global demand for the speciality polymer.
The new facility, scheduled to begin construction in spring 2027, will add 22,000 metric tonnes of annual production capacity for Tosoh’s SKYPRENE chloroprene rubber brand. Commercial operations are expected to commence in spring 2030 at the Shunan City site in Yamaguchi Prefecture.
Chloroprene rubber serves as a critical component across multiple industries, from automotive manufacturing to medical applications. The synthetic rubber’s popularity stems from its exceptional resistance to oil, weather conditions, and flame exposure, making it suitable for demanding applications, including automotive hoses, industrial belts, adhesives, and medical gloves.
The expansion comes as global demand for high-performance polymers continues to grow, driven by increasing automotive production and stricter safety requirements across industrial sectors. Medical applications have also seen increased demand following heightened awareness of the requirements for protective equipment.
Tosoh’s decision to double down on chloroprene rubber production reflects the material’s position within what the company terms its “Chemical Chain Business” - a strategy focused on value-added speciality chemicals rather than commodity products.
The investment represents one of the larger capacity expansion projects announced by Japanese chemical companies this year, signalling confidence in long-term demand fundamentals despite current global economic uncertainties.
The Nanyo Complex already houses Tosoh’s existing chloroprene rubber operations alongside other chemical production facilities. The site’s established infrastructure and logistics capabilities influenced the decision to expand at the existing location rather than develop a greenfield facility.
Industry analysts note that the three-year construction timeline reflects the technical complexity of chloroprene rubber production, which requires specialised equipment and stringent safety protocols due to the chemical processes involved.
The expansion aligns with broader trends in the Japanese chemical industry, where companies are increasingly focusing on high-margin speciality products to offset competitive pressures in traditional commodity chemicals from lower-cost Asian producers.
Epsilon Carbon Launches N134 Specialised Hard Grade Carbon Black In India
- By TT News
- June 12, 2025
Epsilon Carbon, a leading global manufacturer of carbon black, has launched N134, which it claims is a specialised ‘Hard Grade’ carbon black known for its superior abrasion resistance and durability.
At present, the high-quality N134 grade is being imported due to the lack of consistent quality and supply chain issues in the Indian market. As a result, the tyre makers have to modify their formulations using other grades of carbon black, which it shared often leads to reduced performance.
But now, Epsilon Carbon has become the first company in India to install a dedicated manufacturing unit designed for N134 grade hard carbon. The company is expanding its existing Vijayanagar Carbon complex facility to produce 215,000 tonnes of carbon black.
This will not only ensure consistent supply of N134 carbon black for tyre makers in the country, reduce import dependency, but also open up export potential to markets such as Europe and USA. Epsilon Carbon will also focus on integrate advanced processing techniques to ensure batch consistency for durability and performance.
Vikram Handa, Managing Director, Epsilon Carbon, said, “This is a proud moment for us and for India’s carbon black manufacturing sector as the high quality N134 black will significantly reduce import dependency and provide tire manufacturers in India and abroad with a reliable, high-quality product. Our goal is to match global standards while building India’s capability to serve premium markets.”
Lummus Technology And InnoVent Renewables Partner To Advance Global Tyre Pyrolysis Solutions
- By TT News
- June 11, 2025
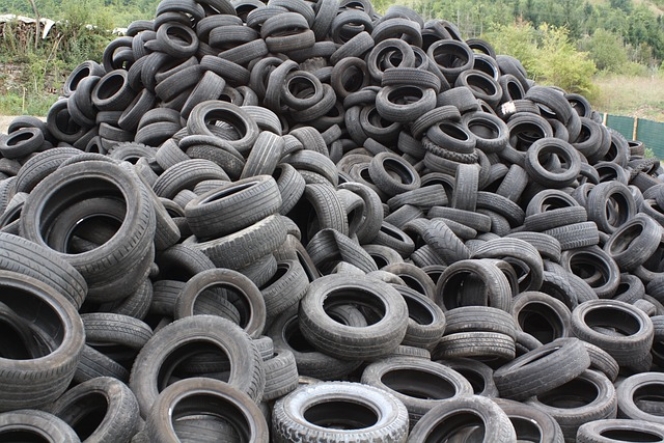
Lummus Technology, a leading provider of process technologies and energy solutions, has signed a memorandum of understanding (MoU) with InnoVent Renewables to collaborate on the global licensing and deployment of InnoVent’s continuous tyre pyrolysis technology.
Under the proposed agreement, Lummus will become the exclusive licensor for InnoVent’s proprietary pyrolysis process, which transforms end-of-life tyres into valuable outputs, including pyrolysis oil, gas, recycled carbon black and steel. Additionally, Lummus will offer integrated technology packages that combine InnoVent’s pyrolysis system with its own downstream processing solutions, enhancing the value of fuel and chemical products derived from waste tyres.
InnoVent’s technology provides a fully scalable, end-to-end solution for converting discarded tyres into renewable fuels and high-value petrochemicals, covering everything from pre-processing to purification. The company currently operates a commercial-scale facility in Monterrey, Mexico, with an annual processing capacity of up to one million passenger tyres, and has the capability to expand further.
Leon de Bruyn, President and Chief Executive Officer, Lummus Technology, said, “This is another significant step in expanding and strengthening our portfolio for the circular economy. By combining InnoVent’s tyre recycling technology with Lummus’ global licensing and engineering expertise, we will be addressing the global challenge of waste tyres and creating new pathways for sustainable product development.”
Vibhu Sharma, Chief Executive Officer, InnoVent Renewables, said, “Partnering with Lummus has the potential to accelerate the global deployment of our technology and help us address the environmental and public health challenges of one billion end-of-life tyres that are disposed of annually. Together, we can transform waste into valuable resources, reduce carbon emissions and support the transition to a more sustainable future.”
Continental Steps Up Shift To Renewable, Recycled Materials In Tyres
- By TT News
- June 10, 2025
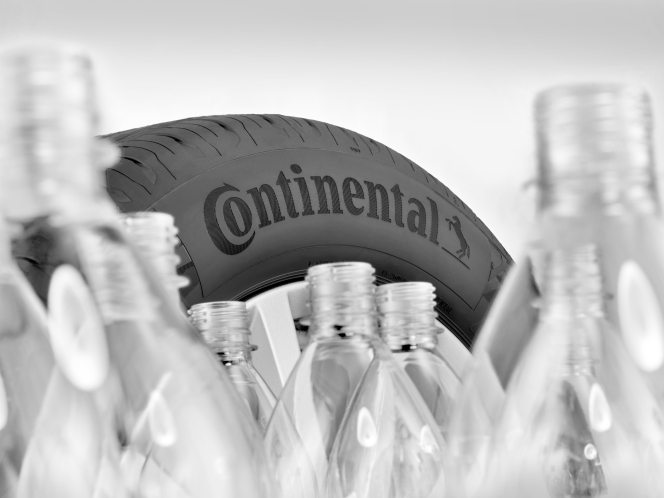
Continental is accelerating its efforts to make tyre production more sustainable, with the German tyre manufacturer expecting the share of renewable and recycled materials in its tyres to rise by up to three percentage points in 2025.
The average share stood at 26 percent in 2024, and Continental said it anticipates a further increase this year due to the expanded use of materials such as synthetic rubber derived from renewable sources, recycled PET polyester, recycled steel, and silica made from rice husk ash — a by-product of rice production.
“We are systematically increasing the share of renewable and recycled materials in our raw material portfolio. In five years, we aim to surpass the 40 percent mark,” said Jorge Almeida, Head of Sustainability at Continental Tires. “To achieve sustainable mobility, we are constantly searching for even more environmentally friendly materials. After extensive testing, we integrate them into production as quickly as possible.”
The company has set a goal of using over 40 percent renewable or recycled materials in its tyres by 2030, without compromising on performance or safety.
A key pillar of this transformation is the adoption of mass balance-certified materials. This approach, certified under ISCC Plus, enables Continental to mix certified and non-certified materials during production while maintaining strict accounting procedures to ensure traceability.
The company has already secured ISCC sustainability certification for its tyre plants in Lousado (Portugal), Hefei (China), Púchov (Slovakia) and Korbach (Germany). Continental is also scaling up its use of recycled steel, silica from rice husk ash, and PET yarns made from recycled plastic bottles via its proprietary ContiRe.Tex process.
Other sustainable innovations include COKOON, an adhesive coating system co-developed with Kordsa that replaces formaldehyde and resorcinol in bonding textile components with rubber. Continental also continues to explore alternative additives derived from renewable sources to improve the tyre vulcanisation process.
“We have developed a comprehensive portfolio of diverse, more sustainable materials and are continuously integrating them into all our products after extensive testing,” Almeida said. “In doing so, we ensure that there is no compromise in safety or performance. With this portfolio, we are getting closer and closer to our ambitious, long-term sustainability goals.”
Comments (0)
ADD COMMENT