Need for scrap tyre disposal policy
- By Rahul Shringarpure
- February 22, 2021
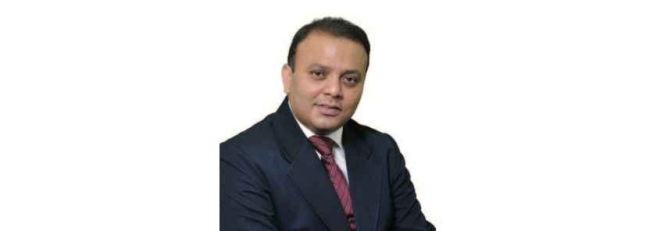
The year 2020 has been a year like no other. The pandemic has brought everyone on the same platform. We all have been a mute witness to the rage of Nature and the apocalypse it can create. The question which persists in my mind is ‘Have we really learnt any lessons from the same?’ Are we going to treat Mother Earth better and build a sustainable planet for our future generation?
On a brighter note, most economies are showing signs of phenomenal recovery. The automobile sector looks to be one of the biggest beneficiaries. Vehicular traffic on the road and the number of new vehicle registrations are a big indicator of the same. In fact, an Indian two-wheeler manufacturer broke its own export record in December 2020. Our belief has proved true again. The human race has endured many such pandemics throughout the years of evolution and evolved better, stronger, smarter.
Processing ELTs
Indogreen Enviro has been involved in the process of ELTs (End of life Tyres) for about a decade.
We have been witnessing the growth of the tyre recycling industry. From the 1970-2000, the majority of organised ELT recycling was about making ‘Devulcanised rubber reclaim sheets.’ These sheets are used in a wide range of applications like tyre re-treads, bicycle tyres, conveyor belts, rubber compounds to name a few.
From 2000 onwards the market started changing due to the introduction of radial tyres. The radial tyres had high tensile steel in them and now could not be grinded directly like the nylon tyres. They need new technology Shredders, Raspers, Granulators to make it ready for grinding. This decade saw many high technology shredding and granulation plants coming up across the country. This included India’s largest and fully automated 100 Mt/annum plant till date Vapi, Gujarat. These granulation plants created a new market for ELT granules-based playground tiles and mats. The CRMB(Crumb Rubber Modified Bitumen) also gained acceptance in large national road construction projects.
Batch type pyrolysis plants
From 2005 onwards, there was a new tyre recycling technology introduced to the Indian market - ‘Batch type pyrolysis plants.’ These plants were initially imported from China. Though profitable, they were extremely unstable, environmentally non-compliant and unsafe for operation. Due to their profitability ,By the year 2019,India had more than 1000 batch type-pyrolysis plants installed. The combined tyre requirement per day for these plants was about 10,000 Mt/day. That would mean a requirement of 10,00,000 passenger car tyres every day, to give a perspective. This monster had a huge appetite that could not be met with tyres from India. So these pyrolysis companies started looking for imported tyres with a perpetual supply possibility from round the globe.
There was only one challenge. The pyrolysis plants are not allowed to import tyres. The shredding companies were allowed to import with a license from DGFT. The batch type pyrolysis companies started buying container loads of tyres from the shredding companies. India started importing about 900,000 MT annually making it the largest importer of ELT in the world until July 2019.The Public Interest Litigation filed against the ‘Batch type pyrolysis plants’ put the brakes on these transactions. The government was forced to take cognisance of the humungous nature of the impending matter at hand.
This is the India story, but could be a similar story for any country from Asia where the Scrap Tyre disposal policy is not yet framed or implemented. I am taking the stance of the agitator than just being a mute spectator. There is so much that can be done than what is being done today.
Scrap tyre disposal policy
There is a strong buzz about ‘Circular Economy’ in Europe and the US. Large tyre companies and chemical giants are investing in various tyre technologies to bring the derivatives from the tyres to be reused in manufacturing new tyres. In India, we don’t even have a national scrap tyre disposal policy. Most local tyre companies are still waiting for an ‘EPR’ to start thinking of sustainable disposal.
In fact, we as a country need ‘Circular economy.’ The responsibly recycled ELT can create high quality reclaim rubber, High calorific value oil with possibility on further hydro treatment to distil commercial grade diesel & petrol, commercial grade carbon black for manufacturing pigments, etc, liberated fibre to make thermoplastics, liberated gases that can be further processed, this can go on and on. There is so much of interest from large companies to set up plants to process this waste but they hesitate because of the lack of a government framework to support the huge capital investment required.
Despite all odds, some companies from India have done some amazing work in developing innovative ELT recycling technologies. A fine example would be Radhe Renewable Energy Development Ltd, Rajkot. They conceived, developed and now operate the ‘World Largest 100 MT Per Day Single Reactor Continuous Pyrolysis Plant ‘ for the last 8 years in Bhilwara, Rajasthan. No other company from around the globe can boast of this feat.In fact some of the large global giants who were looking for a commercial scale large continuous plant could not believe that such a plant and technology existed, that too from a non-descript town from India. This company now supplies ASTM grade Carbon Black and High Calorie fuel to Indian tyre industry beginning the ‘Circular Economy.’
Another interesting Company is Hotfut Sports, an award-winning sports infrastructure development and management company that has been one of the largest consumers of turf technology and synthetic turf products across its various formats. These products have a primary infill requirement of SBR rubber. HotFut has consciously been adapting its procurement process to ensure all SBR and infill / shock-pad requirements are sourced responsibly using recycled ELT’s / rubber scrap making all their facilities more environmentally friendly. They have structured solutions for forward thinking tyre companies wanting to pro-actively process their ELT with a win -win proposition. Many major tyre companies have found their solution very sustainable as well as profitable.
Last year, Internet was abuzz about this start up ‘Blink Green’ from Pune, India. They used ELT for making attractive ladies’ footwear and purses. They have found the utility of this wonderful waste and now is utilising her designing skill and the expertise of the cobble community to churn out beautiful, durable items for the domestic and global market.
These kinds of stories are emerging from all across the continent Imagine the power of scalability of these kind of products with the right kind of financial and marketing support.
I look forward to the day (soon) when we have the ‘Scrap tyre disposal policy’ is finally rolled out and the top tyre companies wait for the EPR policy is over. With a sizeable contribution coming out of their respective CSR budgets and ATMA’s able guidance, a national body to look at new & innovative sustainable disposal practices for ELT could be established. This would be a giant first step taken in the Asian subcontinent towards sustainable recycling of this incredible waste and thus setting a precedence for other countries to follow.
Yokohama Rubber Eliminates Counterfeit Wheel Operation In China With Local Authorities’ Support
- By TT News
- June 25, 2025
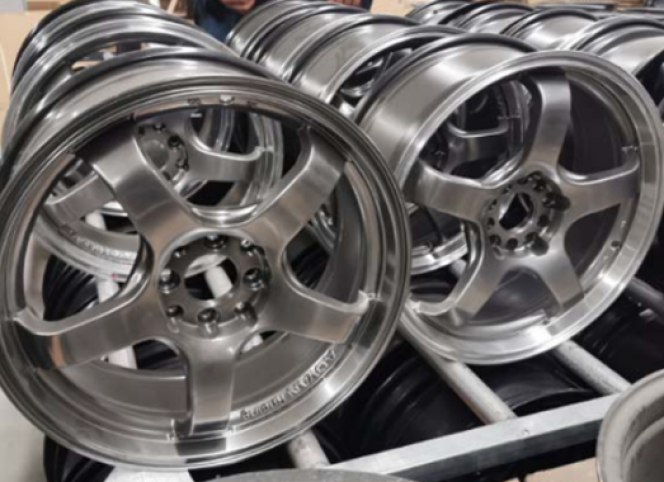
Yokohama Rubber completed enforcement action to halt the production and distribution of counterfeit versions of its “ADVAN Racing” aluminium wheels in China following a coordinated investigation with local authorities.
The Japanese tyre and wheel manufacturer filed an administrative complaint with the Municipal Administration for Market Regulation in Anlu City, Hubei Province, after uncovering a local manufacturer producing unauthorised copies of its high-performance wheels for sports cars.
Authorities in Anlu conducted a raid at the site in November 2024, seizing all counterfeit wheels. A subsequent investigation led to the identification of another company that had commissioned the counterfeit production. Administrative penalties were imposed on the ordering party, including a fine and an order to cease all illegal activity and surrender any remaining fake products.
This marks Yokohama Rubber’s latest successful enforcement action in China. The company had previously filed complaints targeting distributors of counterfeit wheels, resulting in the removal of fake products from the market.
“Yokohama Rubber remains resolute in its stance against the infringement of intellectual property rights, including the production and sale of counterfeit goods, and will strengthen its efforts against such illegal activities in Japan and overseas to ensure that its customers around the world are confident and secure in the knowledge that they are using genuine YOKOHAMA products,” the company said in a statement.
Tosoh Corporation to Build Second Chloroprene Rubber Plant in Japan with £460 Mln Investment
- By TT News
- June 13, 2025
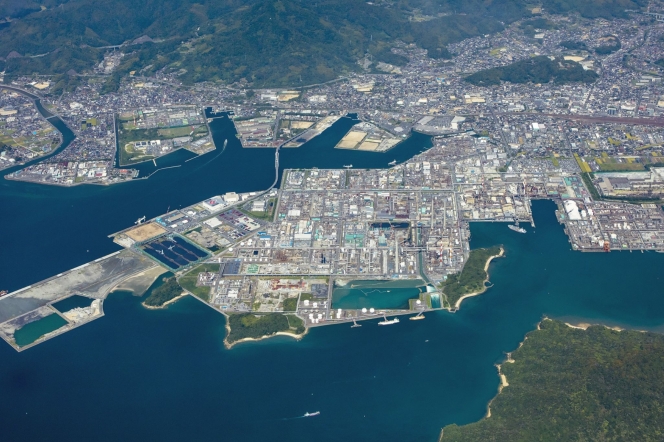
Japanese chemical manufacturer Tosoh Corporation announced plans on Wednesday to construct a second chloroprene rubber production facility at its Nanyo Complex, representing an investment of approximately ¥75 billion (£460 million) to meet rising global demand for the speciality polymer.
The new facility, scheduled to begin construction in spring 2027, will add 22,000 metric tonnes of annual production capacity for Tosoh’s SKYPRENE chloroprene rubber brand. Commercial operations are expected to commence in spring 2030 at the Shunan City site in Yamaguchi Prefecture.
Chloroprene rubber serves as a critical component across multiple industries, from automotive manufacturing to medical applications. The synthetic rubber’s popularity stems from its exceptional resistance to oil, weather conditions, and flame exposure, making it suitable for demanding applications, including automotive hoses, industrial belts, adhesives, and medical gloves.
The expansion comes as global demand for high-performance polymers continues to grow, driven by increasing automotive production and stricter safety requirements across industrial sectors. Medical applications have also seen increased demand following heightened awareness of the requirements for protective equipment.
Tosoh’s decision to double down on chloroprene rubber production reflects the material’s position within what the company terms its “Chemical Chain Business” - a strategy focused on value-added speciality chemicals rather than commodity products.
The investment represents one of the larger capacity expansion projects announced by Japanese chemical companies this year, signalling confidence in long-term demand fundamentals despite current global economic uncertainties.
The Nanyo Complex already houses Tosoh’s existing chloroprene rubber operations alongside other chemical production facilities. The site’s established infrastructure and logistics capabilities influenced the decision to expand at the existing location rather than develop a greenfield facility.
Industry analysts note that the three-year construction timeline reflects the technical complexity of chloroprene rubber production, which requires specialised equipment and stringent safety protocols due to the chemical processes involved.
The expansion aligns with broader trends in the Japanese chemical industry, where companies are increasingly focusing on high-margin speciality products to offset competitive pressures in traditional commodity chemicals from lower-cost Asian producers.
Epsilon Carbon Launches N134 Specialised Hard Grade Carbon Black In India
- By TT News
- June 12, 2025
Epsilon Carbon, a leading global manufacturer of carbon black, has launched N134, which it claims is a specialised ‘Hard Grade’ carbon black known for its superior abrasion resistance and durability.
At present, the high-quality N134 grade is being imported due to the lack of consistent quality and supply chain issues in the Indian market. As a result, the tyre makers have to modify their formulations using other grades of carbon black, which it shared often leads to reduced performance.
But now, Epsilon Carbon has become the first company in India to install a dedicated manufacturing unit designed for N134 grade hard carbon. The company is expanding its existing Vijayanagar Carbon complex facility to produce 215,000 tonnes of carbon black.
This will not only ensure consistent supply of N134 carbon black for tyre makers in the country, reduce import dependency, but also open up export potential to markets such as Europe and USA. Epsilon Carbon will also focus on integrate advanced processing techniques to ensure batch consistency for durability and performance.
Vikram Handa, Managing Director, Epsilon Carbon, said, “This is a proud moment for us and for India’s carbon black manufacturing sector as the high quality N134 black will significantly reduce import dependency and provide tire manufacturers in India and abroad with a reliable, high-quality product. Our goal is to match global standards while building India’s capability to serve premium markets.”
Lummus Technology And InnoVent Renewables Partner To Advance Global Tyre Pyrolysis Solutions
- By TT News
- June 11, 2025
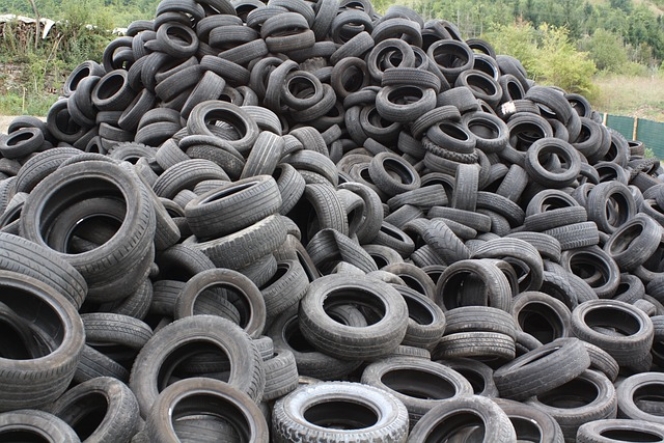
Lummus Technology, a leading provider of process technologies and energy solutions, has signed a memorandum of understanding (MoU) with InnoVent Renewables to collaborate on the global licensing and deployment of InnoVent’s continuous tyre pyrolysis technology.
Under the proposed agreement, Lummus will become the exclusive licensor for InnoVent’s proprietary pyrolysis process, which transforms end-of-life tyres into valuable outputs, including pyrolysis oil, gas, recycled carbon black and steel. Additionally, Lummus will offer integrated technology packages that combine InnoVent’s pyrolysis system with its own downstream processing solutions, enhancing the value of fuel and chemical products derived from waste tyres.
InnoVent’s technology provides a fully scalable, end-to-end solution for converting discarded tyres into renewable fuels and high-value petrochemicals, covering everything from pre-processing to purification. The company currently operates a commercial-scale facility in Monterrey, Mexico, with an annual processing capacity of up to one million passenger tyres, and has the capability to expand further.
Leon de Bruyn, President and Chief Executive Officer, Lummus Technology, said, “This is another significant step in expanding and strengthening our portfolio for the circular economy. By combining InnoVent’s tyre recycling technology with Lummus’ global licensing and engineering expertise, we will be addressing the global challenge of waste tyres and creating new pathways for sustainable product development.”
Vibhu Sharma, Chief Executive Officer, InnoVent Renewables, said, “Partnering with Lummus has the potential to accelerate the global deployment of our technology and help us address the environmental and public health challenges of one billion end-of-life tyres that are disposed of annually. Together, we can transform waste into valuable resources, reduce carbon emissions and support the transition to a more sustainable future.”
Comments (0)
ADD COMMENT