WHEN ADDITIVES BECOME FUNCTIONAL, NEW POSSIBILITIES EMERGE!
- By Colin Clarke
- December 23, 2020
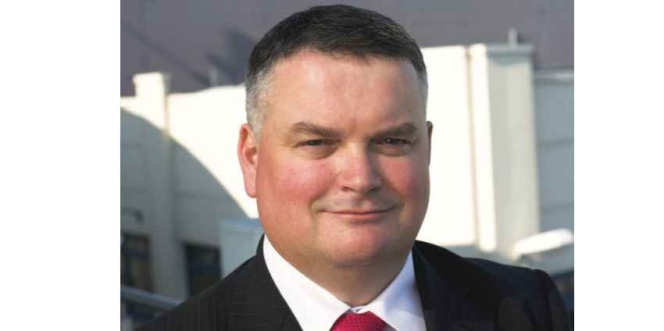
Polymer producers have responded to the changing tyre industry expectations, their innovations take into account a more reactive functionality within polymer architecture, and this is closely matched by increasingly greater degrees of filler surface chemistry. As a result, tyre compound properties may now be tailored to meet quite specific tyre performance targets.
Tyre processing methods also underwent progressive stages of modernisation in recent years, for example, more sophisticated reactive mixing technology together with high-speed extrusion systems allowing for direct extrusion onto the building drum become established as cost effective production routes for many of the major producers.
These advancements however bring about their own conflicts, processing pathways involving multiple stages, often with the ability to rework compound or adjust rheological properties by additional time or energy input during the process are no longer viable options for most tyre producers. It has thus become necessary to achieve processability through an increasingly narrow operating window.
Formulations optimised to achieve peak tyre performance in most cases also tend towards more challenging processing characteristics. This is to be expected; the use of high and narrow molecular weight reactive polymers alongside fillers having high surface area and chemistry, often in loadings above that of the polymer are the norm. The trend towards usage of high loading of plasticiser and resinous materials to adjust tyre tread grip and traction response all contribute to a less forgiving processing nature. Often those compounds that are highly reinforced appear the most fragile during processing and poor green strength with an easily tearing or crumbly compound appearance are often-discussed processability issues. By contrast, the use of high loadings of resins and plasticisers, for example in winter or high-performance tyre formulations, results in compounds that during processing can more resemble chewing gum than tyre treads!
The use of process additive chemicals in an attempt to overcome the processing limitations observed gives rise to further conflicts; Lubricant additives might improve compound surface appearance; however, green strength will probably further reduce due to the unwanted softening effect. The same is true for release additives where lower tack unfortunately remains at a higher value than the also lowered tensile strength of the compound. Filler dispersion is often targeted by additives, however higher loading of fillers mandate equally higher additive loadings, we should more accurately discuss loading as “parts per hundred of filler” not rubber, and under the appropriately higher additive loading, the risk of interference with vulcanisation properties or even additive migration leading to surface bloom become realistic concerns.
Conflicting performance characteristics
The development team at Schill + Seilacher has recognised the need to decouple conflicting performance characteristics found within conventional process additive chemistries. As a result, innovation within our Struktol® range offers tyre compounders opportunities to achieve processability without compromise.
Reduced viscosity leading to better extruder flow properties and improved surface appearance, whilst at the same time achieving an increased compound green strength can be realised by use of Struktol HT 300, a new generation of reactive process additive.
An extract of key processing and property influence in a typical highly silica filled sSBR tread compound are highlighted in the following data.
|
Control |
Struktol HT 300 6 phr |
Struktol HT 300 12 phr |
Mooney ML (1+4) 100 °C (MU) |
75 |
65 |
53 |
Loss of batch weight due to sticking in the mixer (%) |
1.9 |
0.6 |
0.4 |
Significantly lowered Mooney viscosity as well as better mixer batch off with reduced sticking to the mixer rotor and gate with Struktol HT 300 are observed.
An increase in compound green strength was obtained by the addition of Struktol HT 300; this is the opposite of expectation for conventional process additive chemistry, where reduced viscosity is obtained. In addition, the filler dispersion as evidenced by a reduction in the so-called “Payne Effect” as tested in uncured compound by means of RPA strain sweep, is also improved.
Lab extrusion trials, using cold feed extruder demonstrate improved surface appearance and lower compound pressure achieved by use of Struktol HT 300, both desirable processing conditions.
|
Control |
HT 300 6 phr |
HT 300 12 phr |
Hardness |
66 |
67 |
65 |
Abrasion loss (DIN) |
113 |
102 |
106 |
Physical properties are also acceptable, with a progressive increase in tensile strength an elongation and maintenance of stiffness with loading of 6 phr of process additive, only at higher loading of 12 phr would a balancing slight reduction in process oil be required.
Compound hardness remained unchanged alongside improved wear resistance, as measured by DIN abrasion loss testing, even when using higher loading of process additive, are important aspects.
The ability to decouple the relationship between lubrication, important for improved rheological behaviour, and the maintenance of strength and stiffness in both the uncured and vulcanised condition is only possible with such new and innovative class of process additive. This departure from conventional thinking offers the tyre compounder significant degree of freedom to retain the benefits in terms of easier processability without sacrifice of key tyre performance properties.

In this example, the use of Struktol HT 300 prioritised green strength alongside reduced viscosity. By contrast, our new Struktol HT 250 decouples release from other properties, especially effective for winter tyre tread; compound stickiness is resolved without compromise of viscoelasticity.
Ensuring that migration and ultimately bloom within rubber compounds is kept to the lowest level is important for final article aesthetics, for tyres additional considerations arise; they are composite structures, therefore it is imperative that chemicals do not migrate across boundary layers in an uncontrolled manner, which could result in changed behaviour or interfacial adhesion failure over time. In order to limit migration, the compatibility, solubility and concentration of chemicals are carefully considered. However, one method of ensuring long-term stability involves chemically binding the additive within the vulcanisation network.
At Schill + Seilacher, we have achieved this degree of crosslinking capability for a number of new-generation Struktol process additives. Their usage allows the compounder to avoid completely the risk of migration and bloom due to additive presence.
Photographs of two vulcanised rubber sheets based on the same formulation. On the left-hand side, evidence of typical surface bloom, which may occur due to migration of a conventional process additive, on the right, containing reactive additive Struktol HT 600 as replacement, it can be seen that bloom was eliminated.
This technology also opens tremendous opportunities to “fix” process additives in place within the respective component, the role of additives withinthe cross-linking mechanism may additionally lead to vulcanisate performance characteristics.

One interesting tyre related example involves the development of a superior tyre curing bladder performance, here we have developed new reactive plasticisers called Struktol HT 815 and Struktol HT 820, their use is directed towards resin-cured butyl rubber. This combination of polymer and curing system provides for superior heat resistance with excellent flex fatigue resistance and is used as the basis for tyre curing bladders. Here the replacement of widely used castor oil as plasticiser with new Struktol HT 800 series product leads to a significantly improved bladder performance life, with greater stability in viscoelastic properties. Reduced stiffening of the bladder, due to lower degree of plasticiser migration translated into a much lower flex-cracking rate, especially after high temperature steam ageing.
Reactive Struktol plasticisers, HT 815 and HT 820 exhibit a significantly reduced flex cracking rate when compared to the widely used castor oil, which readily migrates from the bladder; as a result, significant extension of bladder service life is possible.
New reactive process additives, with tailored functionality to closely match the specific chemistry of polymers, fillers and cure systems are actively developed. These innovative products under the Struktol brand offer tyre compounders a more comprehensive toolkit in order to tailor compound performance to meet tyre performance demands. The conflicts of property versus processability diminish and new possibilities emerge!
Evonik to Boost Asia Supply Chain with Shanghai Production Expansion
- By TT News
- June 30, 2025
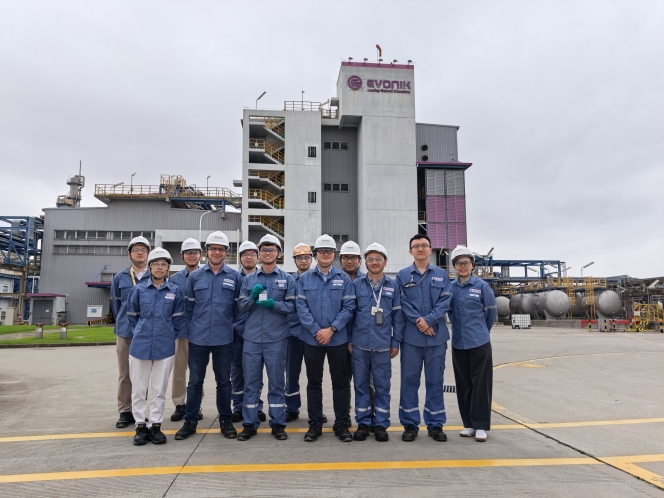
Evonik Industries will localise production of a key tyre additive in Shanghai, marking a strategic shift to enhance supply security across Asia amid growing regional demand.
The Essen-based company announced plans to establish the final production step of its POLYVEST ST-E 60 product at its Shanghai facility, with operations expected to commence by the third quarter of 2025. The expansion will significantly increase the global production capacity of silane-functionalised polybutadienes.
The move represents Evonik’s latest effort to strengthen supply chains and reduce dependency on European manufacturing for Asian markets. POLYVEST serves as a reactive plasticiser in tyre formulations and is also used in rubber compounds, adhesives, tyres, coatings, and sealants.
“This strategic investment will enhance our production capabilities and ensure that our customers in Asia benefit from improved supply security and shorter lead times,” said Dr Anna Maria Ickert, Head of Evonik Coating & Adhesive Resins. “In today’s environment, fostering independent supply chains and bringing our products closer to our customers is essential, enabling us to respond more effectively to their needs.”
The Shanghai expansion comes as global chemical companies reassess manufacturing footprints following supply chain disruptions experienced during the pandemic and ongoing geopolitical tensions. China remains a crucial market for speciality chemicals, particularly in the automotive and construction sectors.
Evonik’s decision reflects broader industry trends towards regionalisation of production, with companies seeking to reduce logistics costs whilst improving responsiveness to local market demands. The tyre industry, a key end-market for POLYVEST, has experienced robust growth in Asia driven by expanding automotive production.
Dr Jürgen Herwig, Head of Evonik’s polybutadienes and speciality acrylics business, emphasised the expansion’s strategic importance. “This expansion aligns with our long-term strategy to strengthen our global footprint while maintaining a strong focus on sustainability and operational excellence,” he said. “The new capacity will enable Evonik’s customers to achieve their business goals while participating in the region’s growth.”
POLYVEST products utilise rubber-based chemistry to ensure compatibility with tyre tread compounds, thereby addressing performance requirements in an increasingly demanding automotive market. The localisation strategy aims to reduce lead times whilst maintaining product quality standards.
Collaboration Is A Growing Need!
- By Sharad Matade & Gaurav Nandi
- June 30, 2025
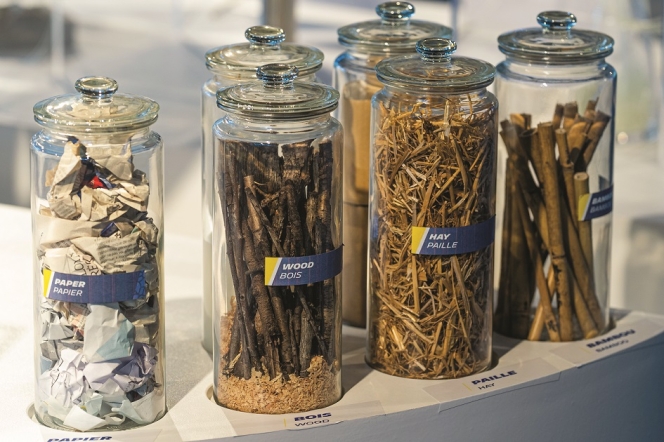
The tyre industry has undergone significant changes over the past century, particularly in material composition and performance optimisation. While the external appearance of tyres may remain similar, advancements in rolling resistance and the integration of sustainable materials have reshaped the sector. Michelin, alongside its competitors, has been embracing innovation through collaborations to meet its ambitious 2050 sustainability goals, focusing on using 100 percent renewable and recycled materials. However, the challenge lies in scaling up recycling technologies and ensuring effective sorting. As the industry shifts, RFID technology and extended producer responsibility (EPR) regulations are emerging as critical tools for achieving material circularity and enhancing recycling efficiency.
Tyres have changed in the last 100 years. While the basic shape and colour might look the same, the internal composition has evolved significantly. Over the past century, and especially in the last 30 years, there have been major advances. One of the most significant has been the improvement in rolling resistance. Achieving lower rolling resistance without compromising grip has been a major technical challenge, and it has had a direct impact on fuel efficiency. In parallel, there’s been increasing focus on using more sustainable materials in tyre manufacturing. So, while it might not be obvious from the outside, there’s been substantial innovation under the surface.
However, it is a well-known fact that the tyre industry is secretive. Companies keep their research and development as tight as possible, but endeavours for including recyclable materials seem to break that ceiling, prompting towards collaborations.
Speaking exclusively to Tyre Trends, Sander Vermeulen, Vice President for End-of-life Rubber Products Recycling Business at Michelin, said, “There is a growing need and momentum for tyre companies to work more closely together, particularly around sustainability and materials innovation. Many companies have set ambitious goals for 2050, which include using 100 percent sustainable materials, achieving full recyclability or becoming carbon neutral. While each company may define these goals differently, the overarching direction is very similar.”
“A good example of this shift is our recent collaboration with Bridgestone through the ‘Call for Action’ initiative. We discovered that both companies shared similar long-term ambitions. One major challenge we identified was the scalability of innovations, especially from recycling companies. Many of these innovations work well at small scale, but scaling them up to meet the needs of the global tyre industry is a different story. What’s promising is that instead of working in silos, we began engaging in open dialogue. Both Michelin and Bridgestone were receiving proposals for new materials but often found them unsuitable for tyre applications. Rather than simply rejecting these proposals, we asked that how we can help these suppliers improve the products,” he added.
He noted that together the tyre makers started defining shared specifications that outline the minimum criteria a new material must meet to be viable for tyre manufacturing. “It’s not a guarantee of adoption, but it provides a clear, transparent benchmark. And if a material doesn’t fall within that box, we can save time for ourselves and the suppliers,” added Vermeulen.
He also quipped that he had never imagined working so openly with a competitor like Bridgestone whilst strictly respecting antitrust rules. But the experience has been incredibly constructive.
Michelin’s 2050 target is bold as it seeks to make 100 percent of its tyres from renewable, recycled or sustainable materials. Recycling sits at the core of that ambition. Internally, the company is aligning efforts across departments to meet this goal with a near-term milestone of 40 percent sustainable content by 2030.
That percentage includes both recycled and bio-based materials. However, Michelin isn’t developing recycling technologies in-house. Instead, it’s working with a network of external partners to identify and scale promising innovations.
Among its collaborators are Enviro and Infiniteria as well as broader initiatives like Biobutterfly and the WhiteCycle consortium, which focuses on recovering textile fibres for tyres. The company remains open to any solution that can help close the loop on tyre materials.
As of the most recent annual report, Michelin reported that 31 percent of the materials used in its tyres are either renewable or recycled. This figure reflects the combined share of both categories, not recycled content alone.
Opining on whether recycled materials are easier to use in commercial or passenger tyres, Vermeulen said, “It really depends on the specific application. Some applications allow for a higher percentage of renewable or recycled content than others. But we don’t break down our targets or current performance by tyre category. The current figure we’ve communicated in our annual report is a global average across all types of tyres.”
EVOLVING VALUE CHAIN
As tyre companies remain steadfast towards the respective goals of using recycled and renewable materials, a glaring question that remains is the fate of current suppliers. Explaining how the value chain will be impacted once tyre companies reach the goals, Vermeulen stated, “They will also need to adapt. The entire value chain must evolve. That means synthetic rubber producers and oil suppliers need to develop renewable or recycled versions of the materials they currently provide. Everyone, from upstream raw material providers to downstream manufacturers, will need to contribute if we’re going to meet these ambitious goals.”
Commenting on whether such shift will restructure the entire tyre industry, he said, “It’s hard to make specific predictions, but one thing is clear that the entire value chain is already beginning to change. All raw material suppliers now understand the direction tyre manufacturers are heading. We’re already seeing many traditional suppliers exploring new approaches to reduce the reliance on fossil-based materials. Some are developing recycled alternatives, while others are exploring biobased feedstocks.”
“In this effort, a concept we explored in a large-scale European project was called BlackCycle. It brought together various actors from the entire tyre industry value chain including raw material suppliers and other stakeholders to map out how we can extract maximum value from end-of-life tyres. It looked at viable recycling pathways including how pyrolysis oil can be integrated into chemical supply chains. We all need to work together to co-create solutions based on renewable and recycled materials,” he added.
Michelin doesn’t plan to produce recycled materials itself. Instead, its focus is on defining performance and quality specifications, then partnering with companies ranging from start-ups to established suppliers that can deliver materials meeting those standards.
Commenting on the same lines, he added, “The entire tyre industry has a strong interest in gaining access to recycled materials that can be reused in new products. And to achieve that, partnerships are essential. There’s no way we can meet these ambitions if every company stays within its traditional boundaries and works in isolation. We believe in collaborating across the value chain. Often, smaller companies have breakthrough technologies or innovative ideas but lack the resources or infrastructure to scale. In those cases, if we can help them access funding or industrialise the processes, it’s a win-win for the industry as a whole.”
While performance gaps between recycled and virgin materials are a known concern, Michelin sees scalability as the more critical barrier. Many recycling innovations show promise at the lab or prototype level, but few are ready for industrial-scale production.
To bridge that gap, Michelin and others in the sector are working closely with innovators to help mature these technologies to meet industry demands.
REGULATION & TECHNOLOGY
The extended producer responsibility (EPR) has been a staunch advocate for recycling end-of-life tyres across countries. The regulation is not only limited to European markets but has expanding into countries like India too.
Commenting on whether EPR regulations will help drive more effective recycling, Vermeulen said, “Extended producer responsibility plays a key role in tyre recycling by making manufacturers responsible for collecting and recycling tyre after use. In countries with EPR laws, such as most of Europe, producers and importers must ensure proper tyre collection and recycling. This legally mandates tyre producers to manage the end-of-life stage of the products. However, EPR is not the only model that can ensure effective recycling. In regions without EPR, like the United States, tyre recycling is still managed through a free-market system driven by industry and service providers. Even in Germany, which lacks an EPR law, tyres are still collected and managed properly through industry-driven solutions.”
“While EPR can certainly help in places with limited infrastructure, the key to effective tyre recycling lies in how well the system is organised. Whether through EPR or free-market models, both can be effective as long as the collection and recycling infrastructure is well established,” he added.
Vermeulen also views RFID technology as a crucial enabler for achieving material circularity in the tyre industry. By embedding RFID tags, tyres can be tracked and identified with precise information about its composition, helping to streamline the recycling process. This technology allows for better sorting of tyres based on specific material make-up, which is critical for maximising the quality of recycled materials.
Just as with household recycling, the challenge is to ensure that materials are sorted effectively. With too many sorting categories, costs rise without guaranteeing better quality. RFID makes it easier to identify the correct ‘bin’ for each tyre, whether it’s a winter, truck or passenger car tyre.
Additionally, RFID can help differentiate between new, retreaded and partially worn tyres, which often have varying materials and recycling needs. This enables more efficient sorting, improving the overall quality of the recycling output while keeping costs manageable. Michelin sees RFID as an essential tool in making the recycling process more effective and economically viable.
Pyrum Advances Construction Plans For New Tyre Recycling Plant In Perl-Besch
- By TT News
- June 28, 2025
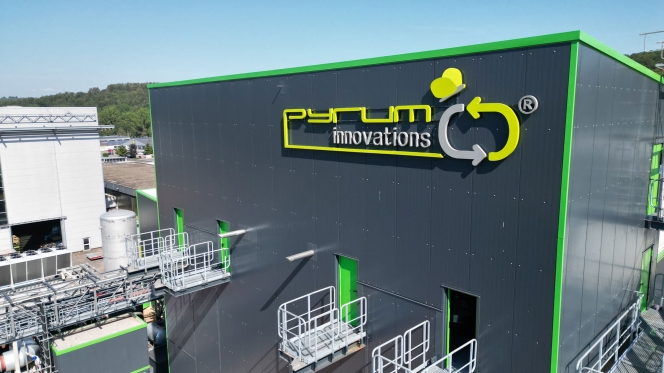
Pyrum GreenFactory II GmbH, a wholly owned subsidiary of Pyrum Innovations AG, has secured approval to begin early construction of its new tyre recycling plant in Perl-Besch. This marks Pyrum’s second independently operated facility, expanding its recycling footprint in Saarland. The plant will occupy a 25,000 m² site near the Germany-France-Luxembourg border, with an annual capacity to process 22,400 tonnes of end-of-life tyres.
The location offers strategic logistical advantages, including access to the Moselle River, existing rail connections and nearby highways, facilitating efficient transport of raw materials and recycled products. Pyrum is currently evaluating multiple delivery routes to optimise operational efficiency and minimise environmental impact.
With the early construction approval now in place, the company can immediately initiate tender processes. A groundbreaking ceremony is planned for July 2025, with commissioning targeted for the first quarter of 2027, assuming construction stays on schedule. The new plant reinforces Pyrum’s commitment to sustainable tyre recycling and circular economy solutions in the region.
Pascal Klein, CEO, Pyrum Innovations AG, said, “Now that the permits have been granted, nothing stands in the way of breaking ground. Our second own plant marks the next important step in our rollout plan. We are delighted to finally be able to move on to the construction phase. With the new plant, we are not only doubling our recycling capacity, but also setting another example for sustainable tyre recycling.”
Kai Winkelmann, CFO, Pyrum Innovations AG, said, “The first part of the EUR 25 million credit line from BASF, which was agreed at the end of 2023, will be used in particular to finance the equity share of the new plants in Perl-Besch and the Czech Republic. In addition, we are in advanced, positive discussions with various financing partners, including a major European bank. If the financing talks are successfully concluded, both projects would be fully financed and the basis for accessing the second part of the loan granted by BASF in the amount of an additional EUR 25 million would also be established. This would provide the company with additional financing in the high double-digit million range for further projects in the rollout plan.”
Orion Honoured With 10 ICBA Safety Awards
- By TT News
- June 27, 2025
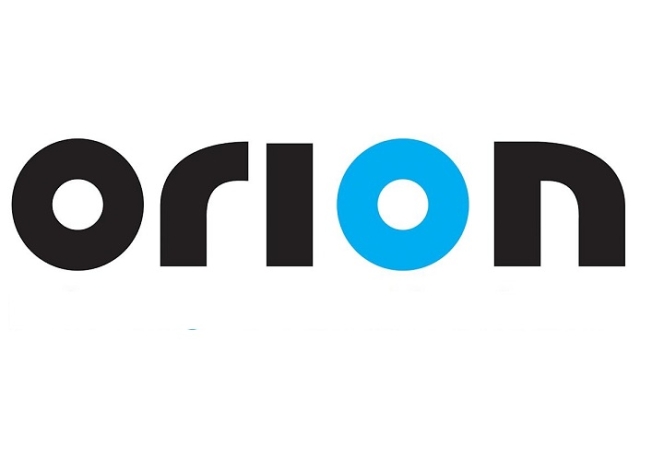
Orion S.A., a leading global speciality chemicals producer, has been honoured with 10 safety awards by the International Carbon Black Association (ICBA) for outstanding workplace safety performance across its manufacturing facilities. The ICBA praised Orion for setting industry benchmarks in employee health and safety through its Safety Recognition Programme, which evaluates verified operational data from the previous year.
Eight Orion plants received Gold Awards, meeting stringent criteria including global safety certifications and zero regulatory citations. These facilities are located in Belpre (Ohio, USA), Berre-l’Étang (France), Huaibei (China), Ivanhoe (Louisiana, USA), Jaslo (Poland), Paulinia (Brazil), Ravenna (Italy) and Yeosu (South Korea). Additionally, Orion’s Orange (Texas, USA) and Qingdao (China) plants earned Bronze Awards for achieving zero ‘Lost Work Day’ cases – a key metric for occupational safety.
Orion CEO Corning Painter said, “Safety is our highest priority at our sites and throughout our company. As we continue to focus our capital investments more on maintenance and reliability across our global operations, we expect to build on our success with safety.”
Carlos Quinones, Senior Vice President of Global Operations at Orion, said, “The ICBA’s recognition reflects our employees’ unwavering commitment and belief that achieving a consistently injury-free workplace is both attainable and a core value of our company.”
Comments (0)
ADD COMMENT