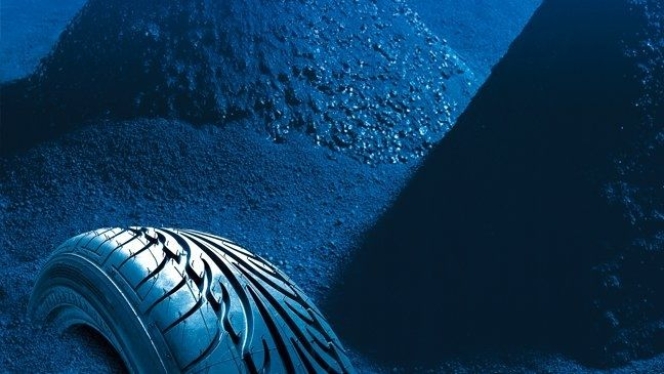
Zeppelin Systems has been awarded the engineering contract for constructing a second ReOil pyrolysis plant, with construction slated to commence in February 2024.
By establishing this new pyrolysis plant, ReOil has significantly expanded its annual recycling capacity, now capable of processing approximately 60,000 tons per year. This state-of-the-art facility, covering roughly 27 acres, is a testament to the ingenuity and engineering expertise provided by Zeppelin Systems.
Having already supplied the initial engineering groundwork for the new plant in 2019, Zeppelin Systems has been awarded the completion contract, underscoring the high level of customer satisfaction. As the primary engineering partner, Zeppelin Systems delivers comprehensive turnkey solutions, encompassing plant technology, process engineering, and final plant planning, all from a single source.
“A flagship project for Zeppelin Systems with a signalling effect. Only a few companies can implement such complex and extensive projects virtually anywhere in the world,” says Dr Markus Vöge, CEO of Zeppelin Systems GmbH, adding: “The aim is to offer process solutions in the future that can be provided as part of license models. For example, the ELT pyrolysis plant as a turnkey product from Zeppelin Systems.” Guido Veit, Vice President of Sales, Plastic and Rubber at Zeppelin Systems GmbH, adds: “ReOil’s engineering contract is the first project as part of the Zeppelin Sustainable Tyre Alliance. This makes us proud and demonstrates the strength of the alliance. In addition, we will continue to work hard to bring additional processes to technological maturity and strengthen the network in terms of the circular economy.”
ReOil Managing Director Paweł Mikuśkiewicz is also delighted with the very successful partnership between Zeppelin Systems and ReOil: “We knew that this major project could only be planned and built with the help of an experienced and internationally active plant engineering partner. That’s why we chose Zeppelin Systems, and we really appreciate our long-standing, trusting business relationship.”
Zeppelin Systems, a trusted partner in plant engineering for the rubber and tyre industry, has taken a significant step towards a more sustainable future by launching the Zeppelin Sustainable Tire Alliance in March 2023. This collaborative initiative aims to work alongside global partners in reshaping the tyre production and recycling process in a more environmentally conscious manner.
Among the esteemed members of this technology alliance is the Polish firm ReOil, known for establishing Europe’s largest pyrolysis plant dedicated to recycling old tyres in 2015. Over the years, ReOil has successfully recycled approximately 20,000 tonnes of old tyres annually. Once operational, this colossal plant is expected to reintegrate about 60,000 tonnes of old tyres into the sustainable circular economy annually.
ReOil, a leading operator in raw material recycling, employs continuous pyrolysis to break down rubber from discarded tyres into valuable substances like gas, oil and recovered Carbon Black (rCB). These recycled materials find application in various industries, including textiles, tyre manufacturing, rubber components, plastics, steel production, and even aviation fuel. Since its commissioning in 2015, ReOil has effectively recycled around 70,000 tonnes of old tyres, reaching a stable and profitable operational state in 2020.
Tosoh Corporation to Build Second Chloroprene Rubber Plant in Japan with £460 Mln Investment
- By TT News
- June 13, 2025
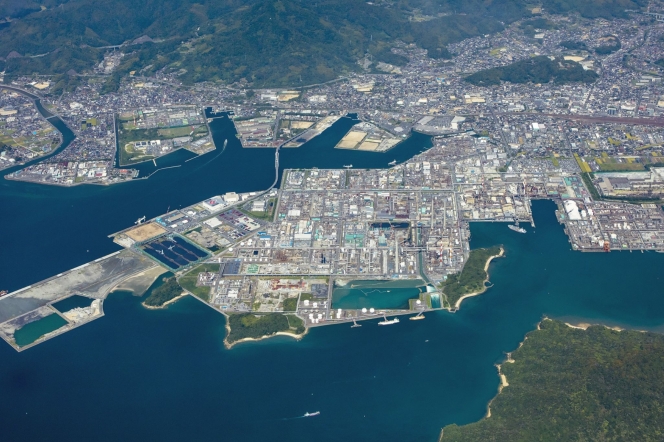
Japanese chemical manufacturer Tosoh Corporation announced plans on Wednesday to construct a second chloroprene rubber production facility at its Nanyo Complex, representing an investment of approximately ¥75 billion (£460 million) to meet rising global demand for the speciality polymer.
The new facility, scheduled to begin construction in spring 2027, will add 22,000 metric tonnes of annual production capacity for Tosoh’s SKYPRENE chloroprene rubber brand. Commercial operations are expected to commence in spring 2030 at the Shunan City site in Yamaguchi Prefecture.
Chloroprene rubber serves as a critical component across multiple industries, from automotive manufacturing to medical applications. The synthetic rubber’s popularity stems from its exceptional resistance to oil, weather conditions, and flame exposure, making it suitable for demanding applications, including automotive hoses, industrial belts, adhesives, and medical gloves.
The expansion comes as global demand for high-performance polymers continues to grow, driven by increasing automotive production and stricter safety requirements across industrial sectors. Medical applications have also seen increased demand following heightened awareness of the requirements for protective equipment.
Tosoh’s decision to double down on chloroprene rubber production reflects the material’s position within what the company terms its “Chemical Chain Business” - a strategy focused on value-added speciality chemicals rather than commodity products.
The investment represents one of the larger capacity expansion projects announced by Japanese chemical companies this year, signalling confidence in long-term demand fundamentals despite current global economic uncertainties.
The Nanyo Complex already houses Tosoh’s existing chloroprene rubber operations alongside other chemical production facilities. The site’s established infrastructure and logistics capabilities influenced the decision to expand at the existing location rather than develop a greenfield facility.
Industry analysts note that the three-year construction timeline reflects the technical complexity of chloroprene rubber production, which requires specialised equipment and stringent safety protocols due to the chemical processes involved.
The expansion aligns with broader trends in the Japanese chemical industry, where companies are increasingly focusing on high-margin speciality products to offset competitive pressures in traditional commodity chemicals from lower-cost Asian producers.
Epsilon Carbon Launches N134 Specialised Hard Grade Carbon Black In India
- By TT News
- June 12, 2025
Epsilon Carbon, a leading global manufacturer of carbon black, has launched N134, which it claims is a specialised ‘Hard Grade’ carbon black known for its superior abrasion resistance and durability.
At present, the high-quality N134 grade is being imported due to the lack of consistent quality and supply chain issues in the Indian market. As a result, the tyre makers have to modify their formulations using other grades of carbon black, which it shared often leads to reduced performance.
But now, Epsilon Carbon has become the first company in India to install a dedicated manufacturing unit designed for N134 grade hard carbon. The company is expanding its existing Vijayanagar Carbon complex facility to produce 215,000 tonnes of carbon black.
This will not only ensure consistent supply of N134 carbon black for tyre makers in the country, reduce import dependency, but also open up export potential to markets such as Europe and USA. Epsilon Carbon will also focus on integrate advanced processing techniques to ensure batch consistency for durability and performance.
Vikram Handa, Managing Director, Epsilon Carbon, said, “This is a proud moment for us and for India’s carbon black manufacturing sector as the high quality N134 black will significantly reduce import dependency and provide tire manufacturers in India and abroad with a reliable, high-quality product. Our goal is to match global standards while building India’s capability to serve premium markets.”
Lummus Technology And InnoVent Renewables Partner To Advance Global Tyre Pyrolysis Solutions
- By TT News
- June 11, 2025
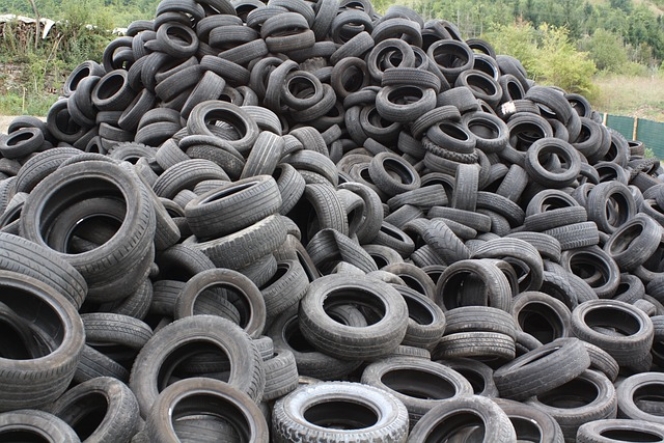
Lummus Technology, a leading provider of process technologies and energy solutions, has signed a memorandum of understanding (MoU) with InnoVent Renewables to collaborate on the global licensing and deployment of InnoVent’s continuous tyre pyrolysis technology.
Under the proposed agreement, Lummus will become the exclusive licensor for InnoVent’s proprietary pyrolysis process, which transforms end-of-life tyres into valuable outputs, including pyrolysis oil, gas, recycled carbon black and steel. Additionally, Lummus will offer integrated technology packages that combine InnoVent’s pyrolysis system with its own downstream processing solutions, enhancing the value of fuel and chemical products derived from waste tyres.
InnoVent’s technology provides a fully scalable, end-to-end solution for converting discarded tyres into renewable fuels and high-value petrochemicals, covering everything from pre-processing to purification. The company currently operates a commercial-scale facility in Monterrey, Mexico, with an annual processing capacity of up to one million passenger tyres, and has the capability to expand further.
Leon de Bruyn, President and Chief Executive Officer, Lummus Technology, said, “This is another significant step in expanding and strengthening our portfolio for the circular economy. By combining InnoVent’s tyre recycling technology with Lummus’ global licensing and engineering expertise, we will be addressing the global challenge of waste tyres and creating new pathways for sustainable product development.”
Vibhu Sharma, Chief Executive Officer, InnoVent Renewables, said, “Partnering with Lummus has the potential to accelerate the global deployment of our technology and help us address the environmental and public health challenges of one billion end-of-life tyres that are disposed of annually. Together, we can transform waste into valuable resources, reduce carbon emissions and support the transition to a more sustainable future.”
Continental Steps Up Shift To Renewable, Recycled Materials In Tyres
- By TT News
- June 10, 2025
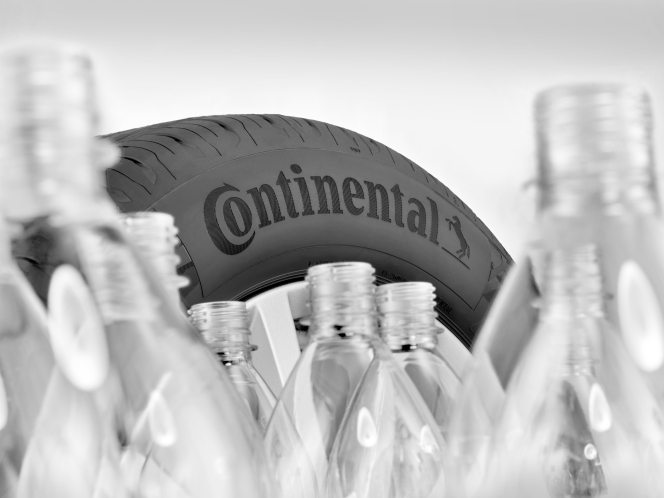
Continental is accelerating its efforts to make tyre production more sustainable, with the German tyre manufacturer expecting the share of renewable and recycled materials in its tyres to rise by up to three percentage points in 2025.
The average share stood at 26 percent in 2024, and Continental said it anticipates a further increase this year due to the expanded use of materials such as synthetic rubber derived from renewable sources, recycled PET polyester, recycled steel, and silica made from rice husk ash — a by-product of rice production.
“We are systematically increasing the share of renewable and recycled materials in our raw material portfolio. In five years, we aim to surpass the 40 percent mark,” said Jorge Almeida, Head of Sustainability at Continental Tires. “To achieve sustainable mobility, we are constantly searching for even more environmentally friendly materials. After extensive testing, we integrate them into production as quickly as possible.”
The company has set a goal of using over 40 percent renewable or recycled materials in its tyres by 2030, without compromising on performance or safety.
A key pillar of this transformation is the adoption of mass balance-certified materials. This approach, certified under ISCC Plus, enables Continental to mix certified and non-certified materials during production while maintaining strict accounting procedures to ensure traceability.
The company has already secured ISCC sustainability certification for its tyre plants in Lousado (Portugal), Hefei (China), Púchov (Slovakia) and Korbach (Germany). Continental is also scaling up its use of recycled steel, silica from rice husk ash, and PET yarns made from recycled plastic bottles via its proprietary ContiRe.Tex process.
Other sustainable innovations include COKOON, an adhesive coating system co-developed with Kordsa that replaces formaldehyde and resorcinol in bonding textile components with rubber. Continental also continues to explore alternative additives derived from renewable sources to improve the tyre vulcanisation process.
“We have developed a comprehensive portfolio of diverse, more sustainable materials and are continuously integrating them into all our products after extensive testing,” Almeida said. “In doing so, we ensure that there is no compromise in safety or performance. With this portfolio, we are getting closer and closer to our ambitious, long-term sustainability goals.”
Comments (0)
ADD COMMENT