- Pirelli
- Science Based Targets initiative
- Greenhouse Gas Emissions
- Paris Agreement
- Net Zero
- SBTi
- Sustainability
- Global Warming
HF READY FOR FUTURE CHALLENGES
- By TT News
- February 22, 2021
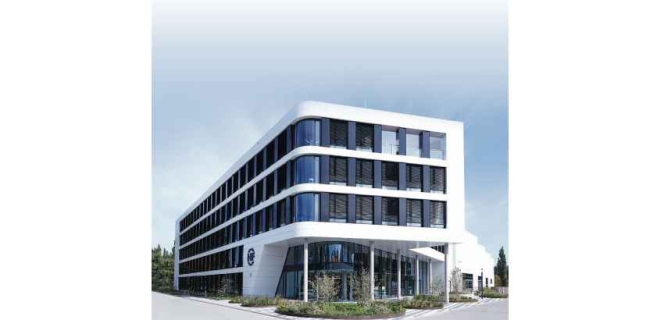
The new headquarters of the Group, which has a history of 165 years of steady growth, serves the business units HF TireTech Group and HF ToolTech Group.
The designing of the new office is tuned to the needs of the Group’s forward march. Direct access from the office facilities to the assembly hall and machine testing area brings all fields of work close together and ensures optimised communication. The established and well proven production unit in Belišće, Croatia remains. Continuous investments in logistics, painting, warehousing and machining under highest economic aspects guarantee state of the art manufacturing.
Back on track
The COVID 19 pandemic and the global lockdown that came with it saw HF being tested hard for its resilience and the capability to help its partners put their production process back on track through its engineering and other services.
“For HF, partnership means to support its valued customers with benefits that will help to keep their production back on track,” says HF TireTech Group Managing Director Dr. Joern Seevers.
HF´s benefits & services for the tyre production are many:
• Technical support for restarting the HF Curing Presses
• Inspection and readjustment of mechanical settings
• Inspection of safety-related components
• Performance check and functional analysis of hydraulic/pneumatic systems
• Software check-up and functionality test
• Close coordination and supply of spare parts
• Individual training for technicians and service people for a smooth and efficient production ramp-up; trainings can take place on customers site or in Hamburg at the Group’s testing press. Virtual support is also available
Dr. Seevers said: “Together with our customers we analyse production processes, optimise, adjust to changed situations, look behind the production and develop new strategies to achieve more flexibility, increase quality, reduce costs and raw material - get into action with a higher level in automation and smart retrofitting and be ready for sustainable tyre production.”
Tandem Mixer technology:
HF takes it to the next level
HF Mixing Group is supplying Tandem Mixers for more than 15 years and has kicked off a revolution in mixing since then. The concept appears to be simple, but all those years of experience have shown that the highest degree of machine engineering has to be combined with extensive process know how to make a Tandem Mixer successful. And a mixing line is only successful if the calculated output and productivity is achieved – combined with a reliability which enables stable production for years.
As matter of fact to develop the process to mix on a Tandem Mixer takes some time and efforts – not to forget the technological know-how of the mixing process itself. HF offers the possibility to accompany this development by offering extensive trials and engineering studies – to shorten the time from ordering a machine up to the point of running in full production.
The goal of a Tandem Mixer is to reduce the specific cost of mixing a compound – on many occasions, HF has proven that overall cost reductions of 15% can be achieved compared to standard lines with a single mixer. This, in between other, is achieved by reducing the mixing steps for a PCR compound from 2,5 to 1,5 steps.
But productivity is not the only driving factor to invest in a Tandem Line – the quality of the compound overall and specifically constant and repeatable mixing of modern compounds is to be ensured. To optimise dispersion, distribution, temperature control and process stability makes a significant difference in today’s production of more complex compound recipes. The intermeshing mixers produced by HF and used in a Tandem Line guarantee to meet these requirements more than any other mixers on the market.
Experiences have shown that no compromise on quality can be made – and HF is supporting this approach with delivering a control system for Tandem Lines which enables their customers to not only run the machine efficiently but also uses online condition monitoring to always reflect on a reliable compound quality which is repeatable.
HF emphasises on result driven production concepts for its customers – further innovations in terms of integrating industry 4.0 solutions to the mixing process are on its way and the focus is clear: Intelligent machines will integrate new digital solutions into the mixing process and will ensure to meet the expectations of the future.
Brownfield projects
The COVID pandemic put a stronger focus on replacing existing machines instead of adding new capacities to a production plant. Also, productivity as well as sustainability aspects are driving many tyre companies to have a closer look to the installed base.
But inspecting a mixing line which has run for more than 15 years (or sometimes even 25 years) brings to light what challenges may come up if this line will be replaced by a new one. Output values need to be increased, a new mixer technology should improve the quality of compounds, modern automation solutions should support the daily production procedures and increase process stability – many more requirements should be met. One of the largest challenges is limited space when looking at an upgrade of machinery.
Not only the pure space but also intralogistics within a mixing line can create headache – from upstream equipment feeding a mixer all the way to downstream machinery processing the batch further – many modern solutions can be used today but looking at the available space installing them is the challenge.
With a clear focus on such brownfield projects, HF has managed several conversions from old to new with unmatched success. A key in such projects is the planning and pre-engineering process. Starting with an inspection of not only the mixer but all surrounding factors in the building – considering also the material flow – and then continuing with a 3D- scan of the existing equipment including pipe and cabling routing the basis for planning can be laid. Supported by this 3D-scan HF engineers plan and design with 3D models the complete mixing mill room.
By keeping the existing machinery as the base layer and inserting new equipment in an over-lay collisions of steel constructions, limitations in space and optimised pipe and cable routing can be identified. Furthermore, an improved process flow chart is the basis of planning material flow, work processes and even manpower to operate the new mixing line. Finally, new controls and automation solutions – on the basis of industry 4.0 – will improve operating and monitoring the equipment.
One of the largest benefits using HF’s Pre-Engineering is shortening the planning and execution time – and last but not least the reduction of financial funds is possible by starting up the new line much quicker compared to the conversion of lines in earlier years.
Safety first
Supporting all major tyre manufacturers with mixing technology HF constantly strives for improving operational procedures in the mixing mill room. When it came apparent that the variety of compounds increased more and more – driven by many more types and technologies in tyres today – the changeover times from one recipe to the other was put in the focus of operational optimisation. Not only flexible automation solutions are required but also quick availability of the mechanical equipment after the last batch of the current recipe was dispatched. In between other HF identified the cleaning of the mixing chamber as a critical action during changeover in two aspects: First it needs to be safe for the maintenance personal to enter the mixing chamber and secondly time can be saved if the access to the chamber can be optimized.
In order to meet both requirements HF’s engineers designed a maintenance box, the so-called mBox©, which is mechanically integrated directly underneath the mixer – combining the mixer with the chute of a dump extruder for example.
In the moment the mixing line is switched to cleaning mode and all movements of parts are blocked a moveable platform – the floor of the maintenance box – is inserted horizontally underneath the mixer. A door of the box can be opened, and maintenance personnel can enter the box safe and secure, standing underneath the mixer with easy access to the mixing chamber.
Besides the safe working environment customers from HF have noticed saving time and having the opportunity of even inspecting the mixing chamber easier and more frequent during a changeover.
Especially in new installations of a mixing line the mBox© can be integrated in the design of the line easily and right from the start – benefitting the safety and operation of the line daily.
HF Screw Presses
The production of screw presses is one of HF`s core competences for decades. The screw press has gained recognition during its affiliation with KRUPP. Thus, the presses operate all over the world and more than 2.500 presses are installed in various industries for example the edible oil industry, biomass technology and rendering. And, most interesting for the tyre industry, the presses accomplish benchmarking results in the dewatering of natural and synthetic caoutchouc. As a more efficient and space saving solution instead of band dryer systems or similar the screw press has its strong eligibility in dewatering process.
HF Curemaster
HF brought the first hydraulic column type curing press to the tyre industry in 1997. Since then, it continued to develop this product to meet the demanding requirements of its customers.
The HF Curemaster was launched two years ago and since then the patented truck tyre curing press has been successfully installed in multiple locations and in efficient operation. The press provides a flexible and compact footprint, making it possible to replace older presses with potentially more presses per existing trench.
The HF Curemaster also focuses on optimising energy efficiency to ensure the lowest total cost of ownership in the curing plant. The HF Curemaster´s hood design incorporates insulation inside the hood to provides the best insulation effect. In addition, the HF Curemaster provides an extremely fast cycle time to minimise the overall amount of heat loss during the open and close sequence of the press.
HF PCR Design
Delivering for a new greenfield plant is relatively straightforward. However, HF understands the important need of the replacement market as well. It is important to be flexible to meet all the varying trench layouts (pit, shelf, pitless, and so on). Equally important is the need to be able to replace existing 42” – 45” old mechanical presses with 48” – 52” modern presses in order to meet the growing demand for larger tyre sizes.
All replacement projects are analysed carefully together with customers. Attention is paid closely to all details related to operation, maintenance access, mould & bladder change requirements as well as all local safety regulations. HF´s long experience with curing presses provides a large variety of modular options to be used for finding the optimised fit for each specific request.
HF Stack Passenger Car Inflator (PCI)
The requirement for post cured tyres continues to grow in the market and HF has designed a simple and compact solution that can be incorporated in all HF presses as well as behind most all existing older presses.
The patented HF Stack PCI design allows for the PCI to be integrated into even the tightest footprints. This solution eliminates any movement or rotations of the PCI body itself and greatly reduces the amount of moving mechanical components and maintenance.
HF Digitalisation
HF recognises the important trend of digitalisation for the tyre manufacturers and has developed reliable, customised software solutions for machine data communication between machine control and customer IT systems. The main steps were to focus on MES, SCADA and Recipe Management interfaces.
HF Smart Curing enables customers to get started quickly and effectively with a future-oriented digitisation solution. The main advantage in this case is that software for machine data acquisition is supplied directly by the supplier and not by IT service providers.
OPC server technology and efficient network solutions are tailored to the machine enable secure data acquisition. This software can provide feedback in regard to condition monitoring, diagnostic function, machine services, energy monitoring and remote service.
The benefit of connecting your equipment with digitalised solutions clearly accelerates a target-oriented development and improves the Total Cost of Ownership of the equipment.
ETRMA Speaks On Automotive Sector Interpretation Guide Of Data Act
- By TT News
- July 01, 2025
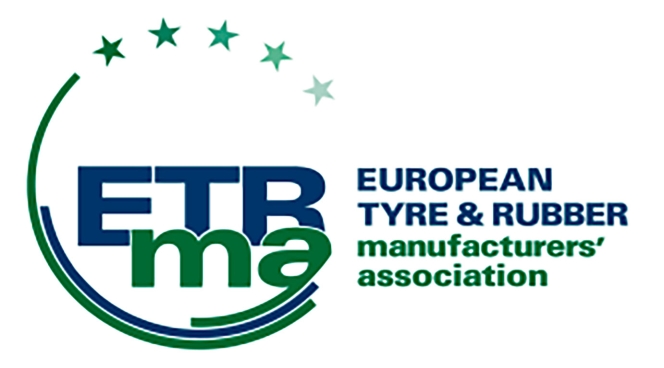
The European Commission’s Industrial Action Plan for the automotive sector included plans to publish Guidance on in-vehicle data alongside the implementation of the Data Act. In response, the European Tyre and Rubber Manufacturers’ Association (ETRMA), alongside other automotive industry groups, has developed an Automotive Sector Interpretation Guide of the Data Act to foster a common understanding ahead of the regulation’s application. This joint effort has helped clarify critical definitions and regulatory interfaces while also incorporating essential tyre-specific considerations – a step ETRMA strongly supports.
Despite this progress, the Data Act’s objectives may fall short without additional measures. Key solutions – such as human-machine interface (HMI) access for user consent and digital ID federation to enable secure, efficient data sharing within a unified European data space – require further exploration under sector-specific regulation. ETRMA remains dedicated to ensuring the Data Act’s implementation promotes fair, non-discriminatory access to in-vehicle data. The association will continue pushing for enforceable rules that guarantee real-time, secure and efficient access to relevant data, safeguarding innovation and competitiveness in the automotive and tyre industries.
Bridgestone India Strengthens Retail Presence with New Select Store In Nashik
- By TT News
- June 30, 2025
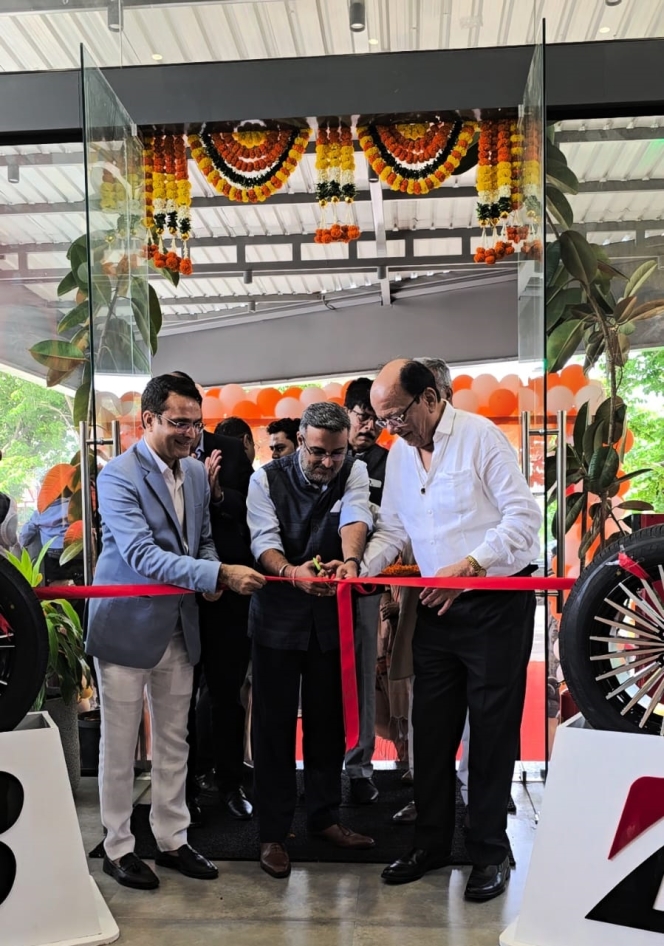
Bridgestone India, a key subsidiary of the global Bridgestone Group and a leader in tyres and mobility solutions, has expanded its premium retail network with the launch of Bridgestone Select Store – M/s Nashik Tyres and Services. The store was inaugurated by Rajarshi Moitra from Bridgestone India, reinforcing the company’s commitment to delivering innovative, customer-centric tyre retail experiences across the country.
Strategically located in Nashik, the store features modern infrastructure and a premium service setup, positioning it as a one-stop destination for tyres and related services in the region. Recognising that tyres are the sole contact point between a vehicle and the road, Bridgestone emphasises safety, performance and driving confidence through its Select stores. These outlets not only help customers choose the right tyres but also enhance their ownership experience with expert guidance and high-quality services.
With over 900 Select stores nationwide, Bridgestone India has established a premium retail network that goes beyond tyre sales to offer a superior, service-driven experience. The expansion of M/s Nashik Tyres and Services further strengthens Bridgestone’s mission to bring world-class tyre solutions closer to customers, reinforcing its pan-India presence with a focus on innovation and customer satisfaction.
Moitra said, “At Bridgestone India, we are committed to redefining the tyre buying experience through our Select stores. As we continue to expand our footprint and enhance manufacturing capabilities our goal is to provide premium products, services and customer experience.”
NEXEN TIRE Sustainability Report Highlights Progress
- By TT News
- June 30, 2025
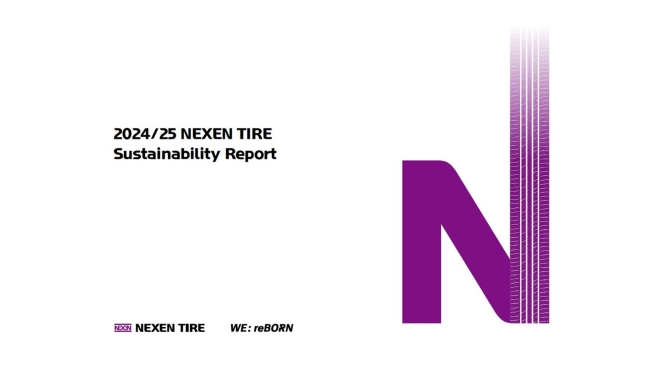
Leading global tyre manufacturer NEXEN TIRE has released its 2024/25 Sustainability Report, demonstrating its commitment to transparent ESG disclosure in line with international standards. This year’s report marks a milestone as it includes consolidated performance data from 10 global subsidiaries, enhancing the company’s enterprise-wide sustainability reporting.
In environmental sustainability, NEXEN TIRE has advanced its carbon management strategy by expanding greenhouse gas (GHG) emissions tracking. The company completed a third-party verified inventory covering Scope 1, 2 and all 15 Scope 3 categories, enabling precise identification of carbon hotspots and targeted reduction initiatives. Additionally, the company is accelerating the development of sustainable materials, evaluating 23 renewable and recycled options across 10 categories. Through proprietary technology, NEXEN TIRE now produces tyres containing up to 70 percent sustainable content. Biodiversity efforts have also intensified, with the company adopting TNFD and LEAP frameworks to assess nature-related risks. An ecological survey around its Changnyeong plant identified protected zones and endangered species habitats within a 50-kilometre radius.
On the social front, NEXEN TIRE celebrated a decade without workplace accidents, a result of proactive safety investments, including facility upgrades, risk assessments and 24-hour disaster monitoring. Enhanced fire prevention systems earned the company the Excellence Award at the 1st Safety Culture Innovation Awards.
In governance, NEXEN TIRE strengthened board diversity by appointing a new female independent director, with independent directors now comprising 62.5 percent of the board. The company also expanded its TISAX certification to eight sites, maintaining zero data breaches for three consecutive years. These efforts underscore NEXEN TIRE’s commitment to sustainable and responsible business practices.
John Bosco (Hyeon Suk) Kim, CEO, NEXEN TIRE, said, “As the industry undergoes rapid transformation driven by electrification, AI and sustainability, NEXEN TIRE is embracing ESG leadership as a core pillar of future competitiveness. Our commitment to responsible innovation and transparency will guide us through the next era of sustainable mobility.”
ZC Rubber to Deploy 3.93 Billion Yuan IPO Proceeds for Subsidiary Expansion
- By TT News
- June 30, 2025
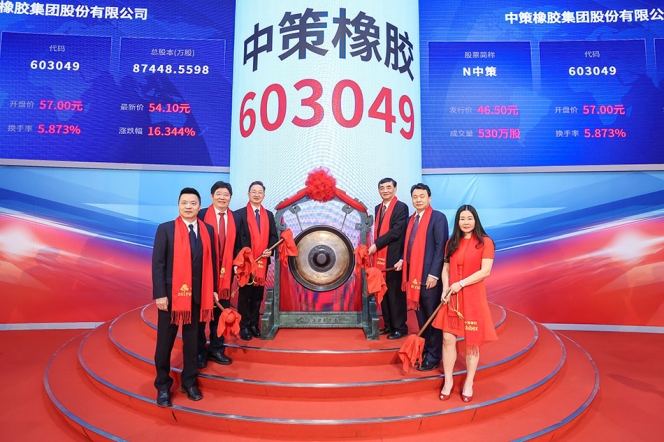
Chinese tyre manufacturer Zhongce Rubber Group Co., Ltd (ZC Rubber) will inject 3.93 billion yuan ($541.3 million) of proceeds from its February initial public offering into wholly owned subsidiaries to fund expansion projects across its production network.
The company’s board approved the deployment of the raised capital through a combination of loans and equity injections to five subsidiaries, according to a regulatory filing. The move represents the full utilisation of net proceeds from ZC Rubber’s IPO, which raised 4.07 billion yuan through the issuance of 87.4 million A-shares at 46.50 yuan each.
Hangzhou Chaoyang Rubber Co Ltd, the group’s largest subsidiary by funding allocation, will receive up to 1.7 billion yuan in loan financing to support its high-performance radial tyre green 5G digital factory project. The facility represents ZC Rubber’s largest single investment among the five planned initiatives.
The company will also provide 850 million yuan to Zhongce Rubber (Tianjin) Co., Ltd. for upgrades in the high-end green tyre industry. At the same time, Zhongce Rubber (Thailand) Co., Ltd. will receive an equivalent amount through a direct capital injection to expand its radial tyre manufacturing capabilities.
Smaller allocations include 352.68 million yuan to Hangzhou Zhongce Qingquan Industrial Co., Ltd. for the production of all-steel radial truck tyres and 180 million yuan to Zhongce Rubber (Jiande) Co., Ltd. for the expansion of its workshop at the JianDe facility.
The funding deployment marks a revision to Zhongce’s original IPO prospectus, which had earmarked 4.85 billion yuan across the five projects. The company has adjusted its plans to align with the actual net proceeds available after deducting underwriting fees and other costs.
Interest rates on subsidiary loans will be benchmarked against comparable bank lending rates, with early repayment options available. The company stated that the funding structure would facilitate project execution while maintaining regulatory compliance through designated account supervision.
Zhongce received approval from China’s securities regulator for its IPO on 26 February, marking the completion of a listing process that positioned the company amongst China’s leading tyre manufacturers seeking to expand production capacity and technological capabilities.
The subsidiary funding initiative received backing from CITIC Securities, the company’s listing sponsor, and external auditors, with both parties indicating no objections to the proposed capital deployment structure.
ZC Rubber's shares have traded on the Shanghai Stock Exchange since its February debut, with the company targeting enhanced production efficiency and market positioning through its post-IPO investment programme.
Comments (0)
ADD COMMENT