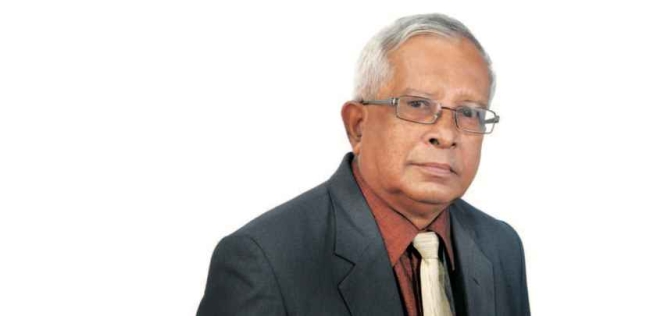
HRD seeks to constantly maintain maximum efficiency and effectiveness by examining employee functions in their jobs. To increase the performance of a company, HRD focuses on elements such as staff satisfaction, compensation, and incentives to keep up morale in order to achieve the highest possible performance from the employees HRD covers the role of recruitment, job analysis, performance appraisals, and skill inventorying to gain a competitive advantage. The extracted data during HR Planning are required to keep track of the human capital functioning within the company. While the task of compiling accurate data may be difficult, advances in technology play a major role in today’s HR function to help automate the work and make it easier.
In the digital era, current human resource planning is leaning toward a more machine-based system. The benefits of cutting-edge technology can help HR planners greatly increase the efficiency and their ability to forecast future needs and wants. The future of HR lies in data analytics that compiles all the information on employees, including their upbringing, experience, performance, and skill sets and monitors them via a computerised interface. Human resource planning is creating strategies around machine run data. The resulting benefit makes artificial intelligence (AI) an important asset that would decrease the time spent on recruitment and increasing its effectiveness while also providing applicants with a fair assessment.
It is with a great sense of admiration mixed up with a dash of amazement, that I scan the current HRD scenario to witness the giant strides made in this field. Yet amongst the glamour and glitter orchestrated by many organisations, which apparently looks like the tip of the iceberg, perhaps it could be my imagination at this late stage of life, I notice a sense of undue stress and dissatisfaction among the staff at all levels in most companies I happen to visit during my consultancies. It makes me to wonder whether we are better off nowadays and motivates me to recollect the scenarios that existed half a century ago during my formative years
As the well quoted words of Mark Antony in Julius Caesar of Shakespeare:
Friends, Romans, countrymen, lend me your ears;
I come to bury Caesar, not to praise him,
My aim is not to glorify the so-called good old days, but to glimpse at some of the best practices used which were appropriate in those bygone days, and some which in my opinion can still be practically valid.
When I faced the first interview at the Bata Shoe Company of Ceylon Ltd in 1969, the very first question I was asked by the Personnel Manager was why I have stipulated a low salary. You should never underestimate yourself. I was reminded. By that time, I had a little over one years’ experience in one of the footwear companies and I was studying part-time for LIRI ( UK ). We joined as trainees under the Management Development Personnel (MDP), and the very first document we were given was a printed leaflet about learning principles (which I still have filed). It started with the famous ancient Chinese quote:
Give a Man a Fish, and You Feed Him for a Day. Teach a Man to Fish, and You Feed Him for a Lifetime.
The type of training was truly hands-on. Whichever functional area we were selected, be it Production, Technical, Purchasing, Marketing, HR or Engineering, we were assigned to the sales outlets and showrooms for one week to familiarize with customer requirements and to learn the shoe sizes by practice. It was a very practical way of understanding customer perception on which there are a multitude of techniques available these days. In the technical and production area which I preferred, our training programme included actual learning and practice of milling, the internal mixer, and other rubber processing machinery, including moulding , and later, working alongside the operators ( sitting next to Nellie) , in the footwear conveyors. The injection molding techniques were not available in the Sri Lanka factory by that time. This reminds me of the Genba (real place) concept, of the Japanese which I happen to familiarize, much later in life. The “Baptism by Fire” became a guiding light in shaping my career in the rubber industry. We were also given a small ring bound hardcover pocket notebook, where we were compelled to list down the daily tasks, mark the ones accomplished and carry forward the balance to the next day. Every operational division used a “Workshop Balance Sheet '' which gave a record of hourly production against target, and the reasons for any shortfall had to be corrected promptly. It was also required to show the material and machine availability for the following day’s production requirement and get the signature of the responsible persons. This was a simple yet effective way of assigning responsibility and accountability. Internal Memos were delivered by hand and the signature of the recipient was taken on the original, and in retrospect, I think that this was a more reliable mode than the emails when considering accountability.
It was an era where there no ICT, and other paraphernalia, computers, electronic calculators, smartphones and APPs that a young person has at his disposal The fastest mode of communication was the Telex, and photocopier (Xerox) and the Facsimile, were yet to see the dawn of the day. We were given a large record book similar to a modern wedding photographic album, which was called the Wellington Book, (named after the Duke of Wellington, of the Battle of Waterloo fame), to record all our learning experiences, which the Personnel Manager discussed with us during the weekly counselling sessions. At a time when the now famous ISO 9001 Procedures and SOPs were not heard of, the organization used standard procedures, and other working documents and formats, including standard formula cards, in its worldwide network of about 110 factories.
We were encouraged to learn from direct observations which include cleanliness and housekeeping also, reminiscent of the power of observations of Sherlock Holmes, which generally ended up with the comment “elementary my dear Watson”. Although the systemized data analysis and virtual access were m not available, my opinion is that the power of observation and hands-on experience enhances the brain functioning, which even some of the modern research has shown to be diminishing with the automation and Artificial Intelligence.
The importance of Tacit (implicit) knowledge or knowing how was given a prominent position during those days, while Explicit knowledge (knowing what), codified and digitalized, plays a more important role nowadays. A parallel from the field of medical examination seems suitable to cite at this juncture. Competent Ayurvedic physicians are capable of diagnosing many physical illnesses, acutely by feeling the pulse of the patient (which even some Western practitioners used to do in our young days), while modern specialists are heavily dependent on tests and techniques and numbers, and yet the general status of physical wellbeing of the people is no better.
Another important aspect of HRD during those days was providing opportunities for representing the company in regional conferences, where we had to present and discuss the technical and other productivity improvements with our counterparts. The only equipment available were the slide projectors and the Flip Charts, which made it a challenging task. It was also an opportunity to interact with people of different nationalities and cultures, which the current tele -conferences and the most recent webinars cannot fulfil adequately. Evaluation of such training was initially done by way of a presentation to the Senior Management and a component of the annual increments was determined by the productive activities one completed after the training, apparently was “no free lunch”.
Some of the leading rubber and chemical raw material suppliers of the yesteryears, Bayer, Monsanto, Rheine Chemie, Polysar,ICI and Vanderbilt , to name few played a leading role in improving the knowledge base of the personnel engaged in the industry. Their Handbooks, and Technical Notes were invaluable treasures. The three-week residential Customer Technical Training Programme of Bayer India was in the Annual HR Agendas during those daysI had the fortune of participating in this programme in 1978, and it was very efficiently handled by Ms R.R Pandit ( diseased ) , SN Chakravarthi.
During my subsequent career progress with companies in Nairobi, Kenya and Sri Lanka, I have made an endeavor to use some of these proven methods to develop the technical and production staff in the companies I have worked. One of the effective methods that can be cited is the compulsory training in Banbury Mixing given to trainees from the universities in Sri Lanka during their In-Plant Training and it gives me a great satisfaction to see that most of them have done very well in their careers and are holding high positions in the industry. Working in an environment with carbon black is a useful learning method, which will be helpful in our professional as well as personal lives.
Not all human resources managers are created equal. In fact, they come from a variety of backgrounds on their way to higher-level HR positions. Still, despite these different paths, many still share basic HR manager responsibilities. The most vital aspect is the importance of the personal touch and the “people centeredness” with respect to the interphases, which the modern techniques seem to be fast obliterating
The vital message I would wish to the industry is the dire importance of the 3Bs, namely, going back to the base at whatever technology level we are engaged, reinforce the base and sustain the base.
ETRMA Speaks On Automotive Sector Interpretation Guide Of Data Act
- By TT News
- July 01, 2025
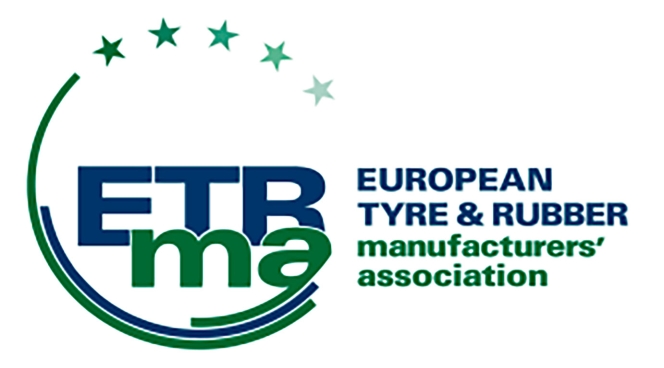
The European Commission’s Industrial Action Plan for the automotive sector included plans to publish Guidance on in-vehicle data alongside the implementation of the Data Act. In response, the European Tyre and Rubber Manufacturers’ Association (ETRMA), alongside other automotive industry groups, has developed an Automotive Sector Interpretation Guide of the Data Act to foster a common understanding ahead of the regulation’s application. This joint effort has helped clarify critical definitions and regulatory interfaces while also incorporating essential tyre-specific considerations – a step ETRMA strongly supports.
Despite this progress, the Data Act’s objectives may fall short without additional measures. Key solutions – such as human-machine interface (HMI) access for user consent and digital ID federation to enable secure, efficient data sharing within a unified European data space – require further exploration under sector-specific regulation. ETRMA remains dedicated to ensuring the Data Act’s implementation promotes fair, non-discriminatory access to in-vehicle data. The association will continue pushing for enforceable rules that guarantee real-time, secure and efficient access to relevant data, safeguarding innovation and competitiveness in the automotive and tyre industries.
Bridgestone India Strengthens Retail Presence with New Select Store In Nashik
- By TT News
- June 30, 2025
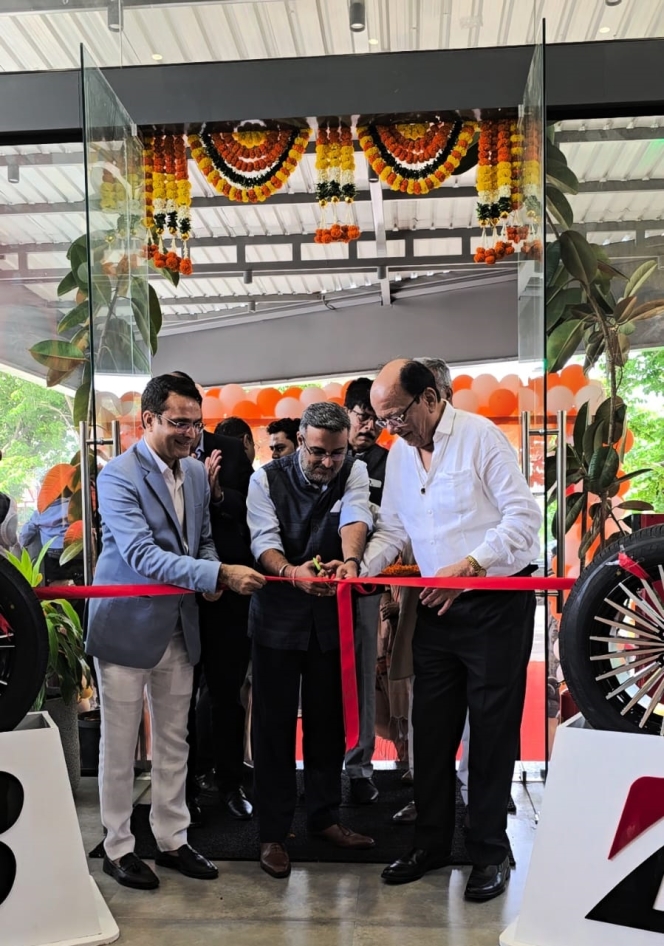
Bridgestone India, a key subsidiary of the global Bridgestone Group and a leader in tyres and mobility solutions, has expanded its premium retail network with the launch of Bridgestone Select Store – M/s Nashik Tyres and Services. The store was inaugurated by Rajarshi Moitra from Bridgestone India, reinforcing the company’s commitment to delivering innovative, customer-centric tyre retail experiences across the country.
Strategically located in Nashik, the store features modern infrastructure and a premium service setup, positioning it as a one-stop destination for tyres and related services in the region. Recognising that tyres are the sole contact point between a vehicle and the road, Bridgestone emphasises safety, performance and driving confidence through its Select stores. These outlets not only help customers choose the right tyres but also enhance their ownership experience with expert guidance and high-quality services.
With over 900 Select stores nationwide, Bridgestone India has established a premium retail network that goes beyond tyre sales to offer a superior, service-driven experience. The expansion of M/s Nashik Tyres and Services further strengthens Bridgestone’s mission to bring world-class tyre solutions closer to customers, reinforcing its pan-India presence with a focus on innovation and customer satisfaction.
Moitra said, “At Bridgestone India, we are committed to redefining the tyre buying experience through our Select stores. As we continue to expand our footprint and enhance manufacturing capabilities our goal is to provide premium products, services and customer experience.”
NEXEN TIRE Sustainability Report Highlights Progress
- By TT News
- June 30, 2025
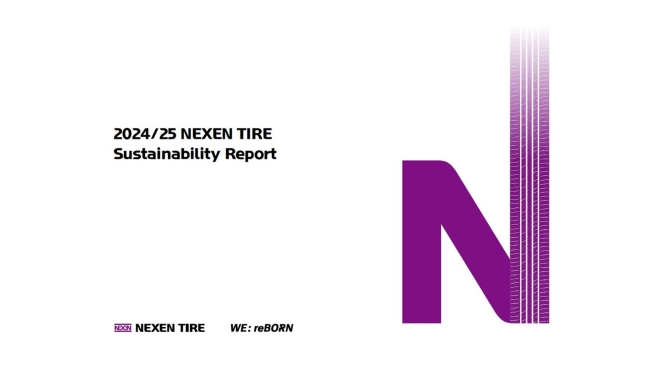
Leading global tyre manufacturer NEXEN TIRE has released its 2024/25 Sustainability Report, demonstrating its commitment to transparent ESG disclosure in line with international standards. This year’s report marks a milestone as it includes consolidated performance data from 10 global subsidiaries, enhancing the company’s enterprise-wide sustainability reporting.
In environmental sustainability, NEXEN TIRE has advanced its carbon management strategy by expanding greenhouse gas (GHG) emissions tracking. The company completed a third-party verified inventory covering Scope 1, 2 and all 15 Scope 3 categories, enabling precise identification of carbon hotspots and targeted reduction initiatives. Additionally, the company is accelerating the development of sustainable materials, evaluating 23 renewable and recycled options across 10 categories. Through proprietary technology, NEXEN TIRE now produces tyres containing up to 70 percent sustainable content. Biodiversity efforts have also intensified, with the company adopting TNFD and LEAP frameworks to assess nature-related risks. An ecological survey around its Changnyeong plant identified protected zones and endangered species habitats within a 50-kilometre radius.
On the social front, NEXEN TIRE celebrated a decade without workplace accidents, a result of proactive safety investments, including facility upgrades, risk assessments and 24-hour disaster monitoring. Enhanced fire prevention systems earned the company the Excellence Award at the 1st Safety Culture Innovation Awards.
In governance, NEXEN TIRE strengthened board diversity by appointing a new female independent director, with independent directors now comprising 62.5 percent of the board. The company also expanded its TISAX certification to eight sites, maintaining zero data breaches for three consecutive years. These efforts underscore NEXEN TIRE’s commitment to sustainable and responsible business practices.
John Bosco (Hyeon Suk) Kim, CEO, NEXEN TIRE, said, “As the industry undergoes rapid transformation driven by electrification, AI and sustainability, NEXEN TIRE is embracing ESG leadership as a core pillar of future competitiveness. Our commitment to responsible innovation and transparency will guide us through the next era of sustainable mobility.”
ZC Rubber to Deploy 3.93 Billion Yuan IPO Proceeds for Subsidiary Expansion
- By TT News
- June 30, 2025
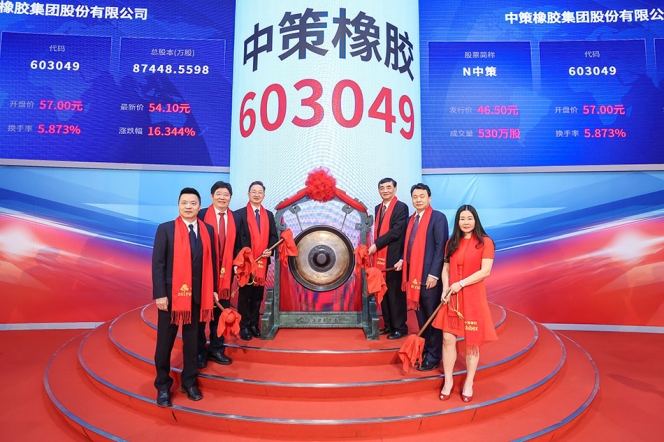
Chinese tyre manufacturer Zhongce Rubber Group Co., Ltd (ZC Rubber) will inject 3.93 billion yuan ($541.3 million) of proceeds from its February initial public offering into wholly owned subsidiaries to fund expansion projects across its production network.
The company’s board approved the deployment of the raised capital through a combination of loans and equity injections to five subsidiaries, according to a regulatory filing. The move represents the full utilisation of net proceeds from ZC Rubber’s IPO, which raised 4.07 billion yuan through the issuance of 87.4 million A-shares at 46.50 yuan each.
Hangzhou Chaoyang Rubber Co Ltd, the group’s largest subsidiary by funding allocation, will receive up to 1.7 billion yuan in loan financing to support its high-performance radial tyre green 5G digital factory project. The facility represents ZC Rubber’s largest single investment among the five planned initiatives.
The company will also provide 850 million yuan to Zhongce Rubber (Tianjin) Co., Ltd. for upgrades in the high-end green tyre industry. At the same time, Zhongce Rubber (Thailand) Co., Ltd. will receive an equivalent amount through a direct capital injection to expand its radial tyre manufacturing capabilities.
Smaller allocations include 352.68 million yuan to Hangzhou Zhongce Qingquan Industrial Co., Ltd. for the production of all-steel radial truck tyres and 180 million yuan to Zhongce Rubber (Jiande) Co., Ltd. for the expansion of its workshop at the JianDe facility.
The funding deployment marks a revision to Zhongce’s original IPO prospectus, which had earmarked 4.85 billion yuan across the five projects. The company has adjusted its plans to align with the actual net proceeds available after deducting underwriting fees and other costs.
Interest rates on subsidiary loans will be benchmarked against comparable bank lending rates, with early repayment options available. The company stated that the funding structure would facilitate project execution while maintaining regulatory compliance through designated account supervision.
Zhongce received approval from China’s securities regulator for its IPO on 26 February, marking the completion of a listing process that positioned the company amongst China’s leading tyre manufacturers seeking to expand production capacity and technological capabilities.
The subsidiary funding initiative received backing from CITIC Securities, the company’s listing sponsor, and external auditors, with both parties indicating no objections to the proposed capital deployment structure.
ZC Rubber's shares have traded on the Shanghai Stock Exchange since its February debut, with the company targeting enhanced production efficiency and market positioning through its post-IPO investment programme.
Comments (0)
ADD COMMENT