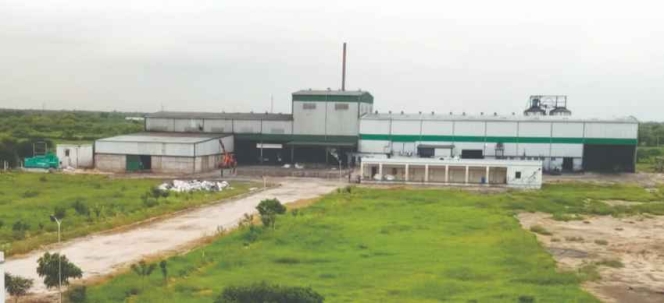
Can you tell us about the background of Radhe Renewable Energy and what was the idea behind the development of the 100 MTPD single reactor continuous pyrolysis plant?
During our travels around India 25 years ago, we used to find farmers burning the agricultural stubble and waste to clear the fields for the next sowing. This used to cause a lot of pollution. With our understanding of hydrocarbons, we decided to create resource out of this waste. We started Radhe Renewable Energy with the idea of creating green fuels from many types of wastes that caused pollution and were a big disposal issue then. Our initial projects were to convert agricultural waste into valuable briquettes which replaced conventional fossil fuels like coal and furnace oil.
Being a hardcore and focused waste-to-energy company, we understood the chemistry of biomass and the future potential of green fuel from biomass. We persisted to find ways to convert rural agricultural waste into wealth with green environment and for sustainable growth of rural India. Our creative and dedicated team moved forward to develop biomass gasification technology to replace fossil liquid fuel in process industries like ceramics, chemical and steel industries with the use of solid biomass briquettes. We were the first company to develop and manufacture industrial scale size biomass and coal gasification technology and replace complete liquid fuel from ceramic industries near Rajkot, India. This reduced the import dependency of coal as fuel. Our team understands the mindset of process industries. We continuously strive to develop technologies that are not only cutting edge but which also create value for the capital invested. We understand that the lifecycle cost is as important as the acquisition cost in India and the other Asian markets. Last but not least, we are completely dedicated to operational safety and sustainable solutions for our clients.
Radhe Renewable Energy has supplied more than 500 biomass and coal gasification technology plants to the various process industries with successful track record in synchronising clients’ processes with gasification. Over this period, our team has gained considerable experience working with big corporates of India (process houses like TATA chemical, H&R Johnson tiles, Somani, Vedanta group, Mahindra, Steel Ispat etc.). We also gained the experience of major process of steel, drying, fertilizer, petrochemical, food, pharma, rubber and mineral industries.
It was in the year 2006 that we started working on a project to convert waste tyres and municipal solid wastes into valuable products. We were the first amongst many who saw the potential of converting this waste into green fuels at that time. We already had lots of experience to convert biomass into char to get charcoal and gas with fast pyrolysis.
What kept you investing in and developing the continuous pyrolysis technology when everyone else was selling thousands of cheaper batch type plants in India?
Equipped with the vast experience that our team had of all process industries, we knew that we wanted to do a revolutionary work in this tyre pyrolysis field too. Hydrocarbon is a big subject. You must handle them properly with full safety, environmental concern, and efficient and stable operation. You cannot think for cheaper batch type technology. We just did not want to do what other small companies were involved in – basically, copying environmentally non-compliant batch type plants from China and selling it in India. The batch type plants were very unsafe to operate, leading to many fires and explosions. The smell and the gases released have affected thousands of people in the last 10 years of their operations across Indian towns and cities.
We chose to take the higher road. We decided to develop and build the best technology plant that India will be proud of. It was an uphill task with huge work and investments involved. It took about three years for a lab scale trial plant to come up. We started scaling up later. It has taken us more than seven years to reach our patented full commercial scale 100 TPD single reactor continuous waste tyre pyrolysis plant.
We can proudly boast that we could perhaps be the only manufacturer to have the largest single reactor 100 TPD continuous plant running successfully for the last nine years. It is sometimes hard to believe that an Indian company can develop and deliver a global technology that can challenge the world in price and performance. The world is amazed with what they see when they understand our technology and offerings. Today, we can offer plants meeting European standards and compliances at about one-fourth of the cost of the European manufacturers. None of them have a 100 TPD show plant operating for as long as we have.
How was the journey in developing indigenous technology for upgrading Recovered Carbon Black (rCB)?
Since the last 25 years, we been working with hydrocarbons, and we know the importance of carbon in daily life. Conventional world is producing carbon black from firing of furnace oil with highly polluting industrial process. At present, the world has few options in making carbon black. These processes consume lots of natural resources and are polluting in nature. Carbon is backbone for many products like rubber, tyre, plastics, Bakelite, minerals, graphite, metal etc. With waste tyre pyrolysis process, we are deriving carbon free without use of any natural resources and without any polluting process. Our continuous pyrolysis process is completely environmentally friendly with almost zero discharge. This process also generates surplus energy for other applications. We understood the importance in upgrading the carbon char generated during the process and worked on it for the more than three years. We were finally able to develop the process to upgrade the rCB to commercial grades successfully. Our rCB is a much sought-after derivative in the Indian market and is being exported across the globe.
How do you evaluate the tyre industry in India? What makes you bet on the carbon black business?
The Indian tyre industry is on a phenomenal growth trajectory and is now very receptive to ideas on sustainability and reuse of recycled materials. We are in active dialogue with many rubber and tyre companies for exploring opportunities to work together with regards to the production and usage of our rCB,
Silica is being aggressively adopted by the tyre industry as a reinforcement material due to tightening of the safety and environmental norms? How will this, according to you, pose a challenge for the rCB industry?
Silica is a useful ingredient of tyre and rubber, which is also found in rCB. As silica is extensively being adopted by the tyre industry, we feel our rCB is absolutely apt for the tyre industry. This will meet both their objectives together – sustainability and reinforcement.
Could you highlight the production capabilities?
Currently, we have 750-800 MT/month rCB production capacity. In the next two years, we will have 300 percent of this capacity in India and about 400 percent of this capacity in the rest of the world. Our brand is Hi-Green carbon black.
Could you talk about the markets the company taps? Are you looking to tap new markets?
We have now opened our doors to companies wanting to set up tyre pyrolysis plants with carbon upgradation systems. The response is overwhelming. We have inquiries coming from all over the world. Initially, people were sceptical if we really had done what we say. They are impressed when they visit our facility. We are now in active dialogue with at least 5-6 companies across Europe and the USA. The future looks very bright.
Do you think there is a need for further collaboration between CB producers and tyre companies?
Yes … definitely, this is a marriage that will last. Tyre companies will be able to complete the circular economy loop. It is a win-win for all.
What are your future plans?
To establish high capacity plants in highly aware European, US, UK and Australian markets and create an ecosystem for high quality tyre-derived oil and rCB. We have started the process to appoint channel partners in Europe and many other strategic markets. We will have our footprints in these markets in the next 24 months.
What are the challenges in the business?
Opportunities and challenges are two sides of the same coin. We always felt that most companies look at the path of least resistance and miss out on the major learning which leads to greatness.
We have built the technology on our own. We have had to invest into the development with our own resources. If we were in Europe or other first world countries, we would have had access to low-cost funding, especially for R&D.
The other challenges in India and other Asian markets are the ever-changing government norms. Quite often, we find that these environmental norms do not have any ground connect. The norms are often formed without proper evaluation of technology merits and guided by local sources. For example, waste tyres are still classified in the hazardous waste category. Strangely, coal and biomass does not classify as hazardous waste. We fail to understand the logic behind such norms. These matters hinder the growth of the right technologies.
Despite all these challenges, we have been able to make our mark in the country.We now look forward to setting our footprints across the globe. (TT)
USTMA Brings Industry Leaders to Capitol Hill to Push for U.S. Manufacturing & Road Safety Policies
- By TT News
- June 25, 2025
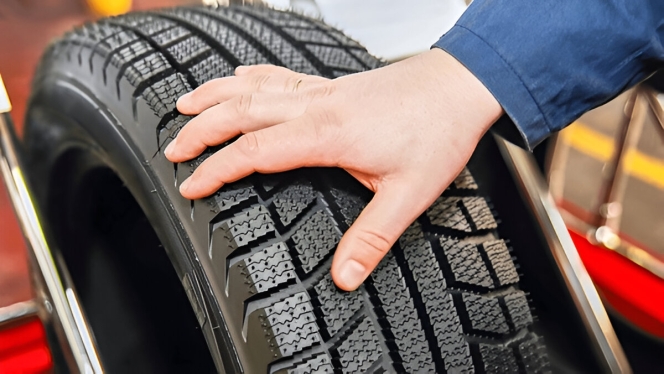
The U.S. Tire Manufacturers Association (USTMA) is convening its annual Tire Manufacturing Ambassadors programme this week, sending industry professionals to Capitol Hill to press lawmakers on policies supporting domestic manufacturing, road safety and sector innovation.
The two-day event, running from 24–25 June, brings together representatives from USTMA’s 11 member companies — including engineers, business managers and marketers — to meet with members of Congress and their staff. The discussions are expected to focus on key legislative priorities such as expanding tyre retreading in the U.S., advancing consumer safety initiatives, and passing a congressional resolution in support of National Tire Safety Week.
“The U.S. tyre manufacturing industry is a vibrant engine of innovation, enabling safe and sustainable mobility for consumers and businesses. Our industry is a cornerstone of the nation’s economy, supporting more than 800,000 jobs and keeping up with evolving consumer expectations on reliability, safety and environmental impact,” said Anne Forristall Luke, USTMA president and CEO.
The ambassadors, who live in the same communities where the industry operates, are set to highlight how national legislation impacts local jobs and infrastructure. USTMA members operate 55 manufacturing facilities across 16 states and contribute to a $170.6 billion annual economic footprint, the association said.
The event follows a letter sent by USTMA to Congressional leaders in February outlining the sector’s legislative agenda. The group is advocating for increased investment in tyre innovation, transparency measures for consumers, and job creation through infrastructure and sustainability-focused policies.
“Our Ambassadors represent the manufacturing workers who power the industry every day, and we are honoured by their advocacy for the tyre manufacturing industry and the communities it supports,” Luke added.
The initiative reflects USTMA’s broader push to align policymakers with the industry’s goals of maintaining global competitiveness while securing long-term growth for U.S. manufacturing.
Nokian Tyres Named Among World’s Most Sustainable Companies by TIME Magazine
- By TT News
- June 25, 2025
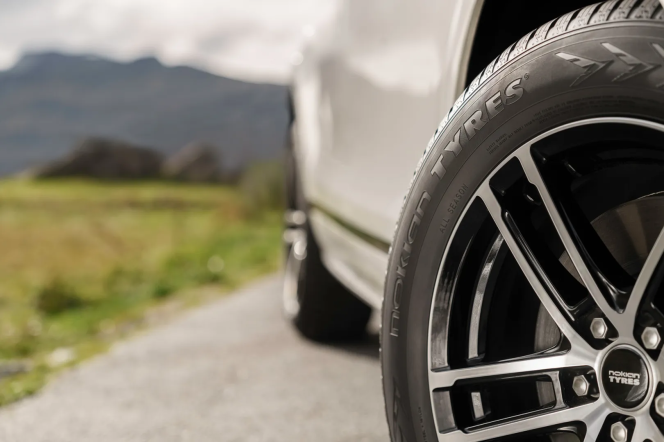
Finnish tyre manufacturer Nokian Tyres has been recognised by TIME Magazine as one of the World’s Most Sustainable Companies 2025, ranking 98th on the prestigious global list of 500 companies demonstrating outstanding environmental and social responsibility.
The second edition of the rankings, compiled by TIME Magazine in collaboration with data firm Statista, evaluated companies based on verified sustainability commitments, including UN Global Compact membership and greenhouse gas emission reduction targets validated by the Science-Based Targets initiative.
Assessment criteria also included performance ratings from respected organisations such as CDP and MSCI, alongside evaluations of sustainable business practices, transparency, and environmental and social stewardship.
Nokian Tyres has positioned itself as a sustainability pioneer within the tyre industry, driving sustainable development both within its operations and throughout its value chain. The company’s environmental leadership dates back three decades, with its Finnish factory becoming the world’s first tyre manufacturing facility to achieve environmental certification in 1995.
“We create tyres that are safe, innovative and sustainable. Nokian Tyres has been a pioneer in sustainability in the tyre industry for over three decades. As early as 1995, our factory in Finland was the first tyre factory in the world to gain an environmental certification. We are proud of our track record and want our sustainability actions to have a meaningful impact. The most recent example of this is our new factory in Romania, the first full-scale zero CO2 emission tyre factory in the world,” said Paolo Pompei, president and chief executive of Nokian Tyres.
The company’s latest sustainability milestone is its new Romanian manufacturing facility, which represents the world’s first full-scale zero CO2 emission tyre factory, demonstrating Nokian Tyres’ continued commitment to environmental innovation in industrial manufacturing.
Sinochem Breaks 500 Billion Yuan Brand Value Milestone, Ranks Seventh in China’s Most Valuable Brands
- By TT News
- June 25, 2025
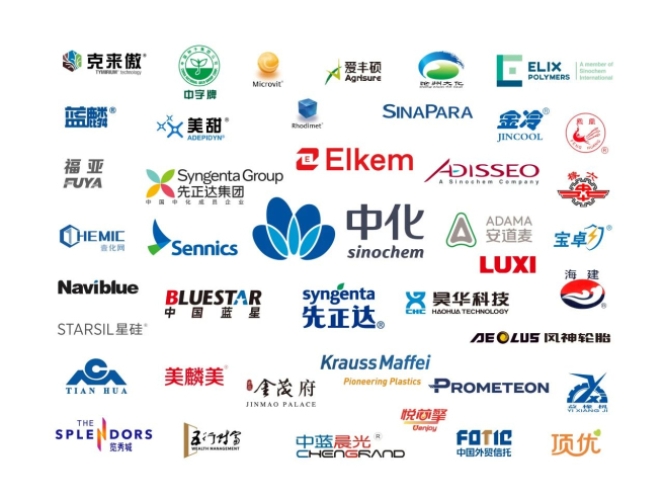
Chinese state-owned enterprise Sinochem has achieved a significant milestone, with its brand value surpassing 500 billion yuan for the first time, according to rankings released at the 22nd World Brand Conference in Beijing.
The World Brand Lab announced that Sinochem ranked seventh on its annual “China’s 500 Most Valuable Brands” list for 2025, with the company’s brand value climbing from 475.906 billion yuan in 2024 to over 500 billion yuan this year.
This marks the 22nd consecutive year that the Sinochem brand has secured a position on the prestigious ranking. The company’s property development arm, Jinmao, also featured prominently, placing 170th with a brand value of 74.186 billion yuan.
The World Brand Lab’s methodology evaluates brand worth through three key metrics: financial performance, brand strength, and consumer behaviour analysis, employing a “present value of earnings method” for valuation. The ranking is widely regarded as one of the most authoritative assessments in Chinese brand research.
Sinochem’s consistent performance has been particularly notable since 2004 when it first entered the top ten of the annual list. Following the establishment of China National Chemical Corporation on 8 May 2021, the enhanced Sinochem brand has maintained its seventh position for four consecutive years, demonstrating sustained growth in brand value and international market recognition.
The company attributed its success to implementing comprehensive brand management strategies aligned with government directives on brand development. Sinochem stated that it will continue to leverage high-quality brand building and valuable brand assets to strengthen its core functions and competitiveness, supporting the company’s long-term development objectives.
The World Brand Conference, now in its 22nd year, serves as a key platform for evaluating China’s corporate brand landscape and tracking the evolution of the country’s most significant commercial entities.
- Continental
- Continental Tires
- Edwin Goudswaard
- Ultra High Performance tyres
- AC Schnitzer
- Brabus
- Porsche Panamera
- Maserati Levante
- Audi RS6 Avant
- Polestar 3
- BMW 5 Series
- BYD Seal
Continental Strengthens Position in Ultra-High-Performance Tyre Market
- By TT News
- June 25, 2025
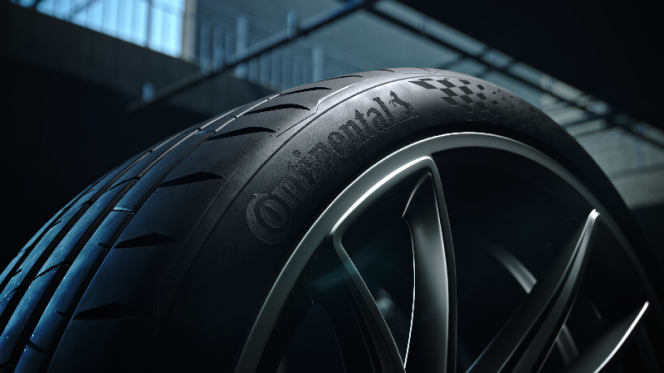
German tyre major Continental is significantly expanding its presence in the global market for ultra-high-performance (UHP) tyres. The company states that the UHP tyres are designed for safe and dynamic driving at high speeds and are available in sizes from 18 inches.
Between 2019 and 2024, the premium tyre manufacturer increased its worldwide sales of UHP tyres in the passenger car and light truck segment by approximately 15 percent. Over the same period, the share of UHP tyre sales across all Continental brands rose from 38 to 52 percent, and to 60 percent for the core Continental brand, up from 46 percent five years ago.
Edwin Goudswaard, Head of R&D, Continental Tires, said, “For us, ultra-high-performance tyres are much more than a technological flagship product – they are a strategic driver of innovation. Their development requires engineering of the highest standard, high-tech materials and precise testing and production processes. At the same time, they demonstrate our solid position in the premium segment and significantly contribute to Continental’s economic strength.”
UHP tyres are claimed to provide excellent grip, precise steering, strong brake performance and high driving stability, primarily used on powerful vehicles such as sports cars, SUVs and luxury saloons. The global demand for UHP tyres is projected to grow by around 9 percent annually until 2029, driven by the increasing popularity of SUVs and the electrification of powertrains. Continental is experiencing particularly high demand for UHP tyres in the Asia-Pacific region, especially in China.
The German brand currently offers UHP tyres across all product segments, including summer, winter and all-season tyres. The flagship product in its UHP portfolio is the SportContact 7. Since its global launch in 2022, the SportContact 7 has won 21 out of 24 independent tyre tests, boasting a success rate of over 87 percent.
The company stated that tyre testers have praised its ‘shortest braking distances under all test conditions’ and ‘very balanced and safe vehicle handling on dry roads and even better performance on wet roads compared with the competition.’ Its precise steering characteristics, reproducible driving responses and excellent grip during sporty driving have also received acclaim.
Continental continues to invest in the development of its UHP products, fostering close collaborations with vehicle manufacturers and tuning specialists like AC Schnitzer and Brabus.
"These partnerships enable us to transfer ideas from the high-performance segment to the mass market,” explained Goudswaard. The High-Performance Technology Centre (HPTC) in Korbach produces high-performance tyres for powerful and technologically sophisticated passenger cars and conducts rigorous testing under realistic extreme conditions.
The SportContact 7 has received original equipment approvals for various models, including the Porsche Panamera, Maserati Levante, Audi RS6 Avant, Polestar 3, BMW 5 Series and BYD Seal. The tyre is available in 120 sizes from 18 to 24 inches and has been developed for both electric and conventional vehicles.
Comments (0)
ADD COMMENT