Govt Push Paves Way For OTR Recycling In Australia
- By Gaurav Nandi
- February 28, 2025
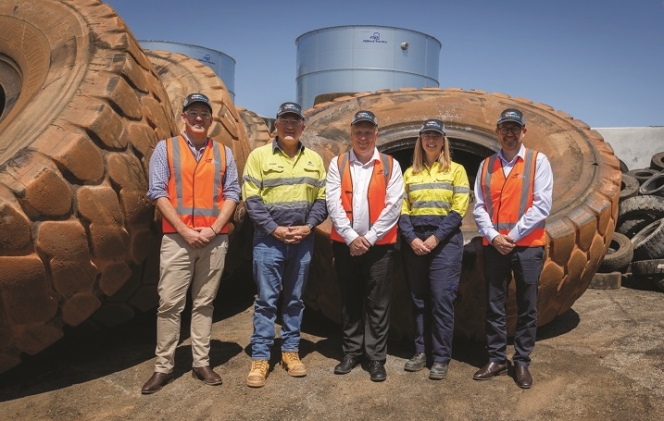
The Australian Government’s push for end-of-life tyre recycling, particularly through the use of crumb rubber in road construction, has been gaining momentum. With Western Australia and Queensland continuing to grow rapidly but key markets like Victoria falling away, challenges remain in expanding the use of crumb rubber, especially in New South Wales and South Australia. However, partnerships like that between Tyrecycle and Alcoa Australia are helping pave the way for the recycling of OTR tyres, creating new opportunities.
The Australian Government’s endeavour for recycling end-of-life (ELT) tyres has been lauded by industry experts in many mature markets. Since December 2021, Australia has prohibited the export of whole baled tyres, except for specific casings and retreads. The Australian Government emphasises a circular economy approach, which includes incentives for local manufacturing by procuring tyre-derived materials such as crumb rubber for asphalt and other civil applications. The Western Australian Government has used over 3,000 tonnes of crumb rubber for road projects in a single year.
However, challenges remain with the recycling of off-the-road (OTR) tyres, often disposed of at mining sites. Nonetheless, the proactive nature of the government, especially in Western Australia, has paved the way for OTR tyre recycling, with recyclers forming partnerships with mining companies to ensure a steady stream of supply.
One such collaboration is between Tyrecycle, the recycling arm of ResourceCo, and Alcoa Australia. Tyrecycle’s state-of-the-art recycling facility in East Rockingham, 40 kilometres south of Perth, has already welcomed its first load of used OTR tyres from Alcoa, which is a bauxite mining company.
Speaking to Tyre Trends on the current state of waste OTR tyres, Tyrecycle Chief Executive Officer Jim Fairweather stated, “Currently, an estimated 130,000 tonnes of OTR tyres are discarded annually; 50,000 tonnes in The Pilbara alone. Tyrecycle is processing about 15,000 tonnes per year and aims to expand its footprint into key mining regions like the Hunter Valley, Bowen Basin and Pilbara. These areas are pivotal to Australia’s coal and iron ore mining industries, presenting significant opportunities for waste management and resource recovery.”
He added, “Mining operators often choose the cost-effective route of burying waste tyres on-site, which hinders recycling efforts. While some companies recognise the importance of responsible waste management, regulatory enforcement is needed to make recycling a standard practice. Proactive companies in the mining sector are stepping up, recognising the reputational and environmental risks associated with poor waste management. However, broader adoption is hampered by minimal regulatory mandates.”
COLLABORATIVE MEASURES
The collaboration between Tyrecycle and Alcoa was driven by a mutual commitment to sustainable practices and innovation in waste management. For the recycler, it represented a strategic move to expand its capacity to process OTR tyres and, in the future, conveyor belts, which are significant waste streams in the mining sector. This partnership evolved over five years of discussions, trials and project planning.
Equipped with a larger primary shredder capable of processing substantial pieces of OTR tyres, the plant in East Rockingham enabled the recycler to manage Alcoa’s tyre waste effectively. Prior trials at the recycler’s New South Wales facility ensured the material could be processed successfully, laying the groundwork for this full-scale collaboration.
“Alcoa provides full OTR tyres, which are pre-processed using excavators to reduce size. These pieces are then fed into our fully automated plant, where they undergo a comprehensive process to produce crumb rubber as fine as 700 microns. The crumb rubber is repurposed into road construction material within Western Australia, creating a closed-loop system. The project aligns with the Western Australian Government’s push for the integration of rubber crumb in road infrastructure, ensuring sustainable outcomes,” said Fairweather.
He mentioned that the company has initiated partnerships with major mining operators, securing long-term offtake agreements to convert OTR tyres into value-added products for resale. While agreements are being finalised with several top-tier miners, the company aims to secure additional multi-year contracts, further cementing its position in the growing circular economy of Australia’s resource sector.
PRODUCTION
The company operates nine facilities culminating in a current processing volume of 180,000 tonnes annually with 30 percent spare capacity, allowing for up to 250,000 tonnes per year. Crumb rubber production stands at approximately 25,000 tonnes annually.
While mining tyres constitute a smaller portion of the company’s operations, the bulk of recycling comes from collecting approximately 20 million tyres annually from retail outlets across Australia, including regions such as Far North Queensland, Tasmania, Perth and the Pilbara. These include PCR, TBR, four-wheel-drive tyres, forklift tyres and even bicycle tyres. Roughly 80,000 tyres are collected daily.
Alcoa’s waste OTR tyres are entirely processed into crumb rubber for the Western Australian market. Beyond this, crumb rubber from other ELTs is sold into sectors such as the steel industry, adhesives manufacturing, playground surfacing, walking trails and civil applications. While these sectors are important, they don’t match the volumes required for road construction in Australia.
Additionally, tyre derived fuel (TDF) is manufactured in various sizes to cater to different customer needs. For example, 1.5-inch steel-free chips are used in power boilers, while 2-inch, 3-inch, 4-inch and 6-inch chips are utilised in cement kilns, both locally and for export to countries like Japan.
Offshore customers further process these materials into products like micronised rubber powder. The company also supplies feedstock to large tyre recycling businesses in India and Korea.
Commenting on whether Alcoa takes any of the tyre-derived product under the agreement, Fairweather informed, “Alcoa currently does not take any products, but there are opportunities in development, particularly in the smelting sector, where materials could be used as reductants.”
CONSUMPTION
While crumb rubber production serves local markets exclusively, TDF and steel exports continue to play a vital role in the company’s global strategy with a focus on improving quality and expanding domestic utilisation.
“The crumb rubber produced is fully consumed within Australia, reflecting a strong domestic demand for applications such as road construction. While 5,000 tonnes of TDF is consumed domestically in New South Wales, the vast majority – over 100,000 tonnes – is exported. That said, domestic consumption of TDF is poised to increase significantly with plans to redirect approximately 100,000 tonnes for use within Australia as part of ongoing pipeline development projects,” said the executive.
“Additionally, steel extracted from the tyres is traded globally as scrap. With the installation of steel-cleaning systems across all facilities, we now export steel with a much lower rubber contamination rate, reduced from 20 percent to 1-2 percent. This enhancement improves the value of the scrap and allows for more competitive pricing at the collection stage,” he added.
Commenting on the use of crumb rubber for roads, he said, “Road construction remains the largest consumer of crumb rubber in Australia, outpacing other uses. The Western Australian Government’s mandate to use crumb rubber in roads has been evolving over the past three years. Three years ago, there was virtually no sale of crumb rubber for road construction in Western Australia. However, today, Western Australia has become the second-largest market for crumb rubber used in roads across the country, despite having only 10–15 percent of Australia’s population.”
“The Main Roads Western Australia agency played a pivotal role by mandating crumb rubber in road specifications, significantly increasing demand. Additionally, the Western Australian Government supported this initiative by funding the creation of tyre processing infrastructure. This dual approach that includes stimulating private sector investment while ensuring procurement for recycled materials has been key to making these investments viable,” he added.
QUALITY CONTROL
Fairweather quipped that being one of the largest recyclers in the land has its perks when it comes to quality controls. With an expansive collection network that draws in tyres that are not only manufactured at home but imported from different regions ensures understanding of different chemical compositions.
As for ensuring the quality of crumb rubber, especially for road construction, he said, “We implement rigorous quality control procedures from testing the crumb rubber three times a day across all facilities to ensure that it is consistent and free of impurities. We take specific measures to ensure even sample collection and use advanced software to track and grade the rubber’s size distribution. Chemical tests are also performed periodically to maintain the integrity of the crumb rubber. Given the varied origins of the tyres, the company’s large scale allows it to homogenise these variations, ensuring a high-quality product.”
He added that quality is paramount because contaminants like metal can damage equipment used in road construction and asphalt applications. The company maintains a metal contamination level of less than 0.01 percent, which is crucial for the reliability and functionality of the crumb rubber in its applications.
Regarding the recycling of mining tyres compared to passenger and TBR tyres, he noted that there is a significant difference in the process. “Mining tyres are much larger and require different handling equipment and primary processing. These tyres need to be pre-processed to remove the bead before being reduced to a manageable size. In contrast, passenger and TBR tyres undergo a more standard shredding process, which then leads to various mechanical resizing depending on the final product,” said the executive.
The TDF also goes through a rigorous quality control process.
MARKET FORCES
The largest market for crumb rubber in Australia has historically been Victoria, where it has been widely used in road construction. However, in recent times, Victoria’s market has faced challenges, largely due to budgetary pressures that have led to delays or cancellations of road projects. Despite this, it has remained the leader in crumb rubber consumption for roads.
Western Australia and Queensland are closely matched, coming in second for crumb rubber usage. On the other hand, New South Wales (NSW) and South Australia are behind in their adoption of crumb rubber in road construction, with NSW, particularly Sydney, significantly lagging. This presents an opportunity for growth in those regions, as they could start to increase their usage to match the other mainland states.
Tasmania, due to its smaller population and limited road construction, uses less crumb rubber, but this is proportional to the region’s size and needs.
“The collaboration with Alcoa and the potential for them to purchase products in the future is still under discussion. Both parties are open to exploring further development of this partnership. Alcoa has proven to be a strong partner, and there are good opportunities for continued collaboration, especially in creating a circular process that benefits both Alcoa and the broader market,” averred Fairweather.
The growth strategy for the company focuses on expanding its production capabilities and increasing the value-added nature of its products. This includes ongoing investment in plant infrastructure and a focus on increasing market share, particularly in tyre collection volumes.
The company sees significant potential in the OTR sector, which is currently untapped, and plans to continue developing new products and processes to offer higher-value products rather than just TDF.
TDF, however, remains an essential part of the business. It plays a crucial role in tyre recycling by reducing landfill waste and offering a more environmentally friendly alternative to fossil fuels.
Trials on imported tyres were also successfully completed with full-scale processing set to begin imminently. Tyrecycle also plans to establish processing facilities in Central Queensland and Western New South Wales, reducing logistical barriers and enhancing service capabilities.
JK Tyre Targets Double-Digit Growth in FY2026, Targets INR 10 Billion CAPEX
- By Nilesh Wadhwa
- August 08, 2025
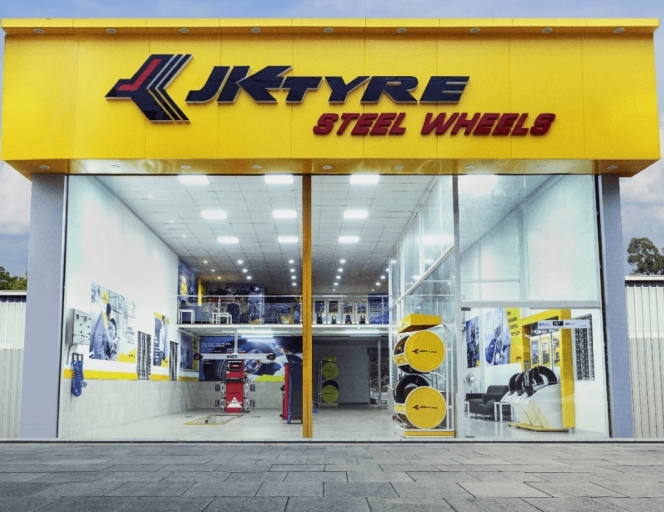
JK Tyre & Industries is aiming for double-digit revenue growth in FY2026, outpacing its forecast for single-digit expansion across the broader tyre industry. Managing Director Anshuman Singhania outlined the company’s ambitions during a post-earnings media call, underscoring confidence in demand recovery and strategic market positioning.
Q1 Performance Overview
For the first quarter of FY2026, JK Tyre reported revenue of INR 38.91 billion, with EBITDA at INR 4.24 billion, translating to a margin of 10 percent. Net profit stood at ₹1.55 billion — up 51 percent compared with the previous quarter, but down 21 percent YoY.
Singhania attributed the annual decline to muted original equipment (OE) demand, particularly in truck and bus radial (TBR) volumes, alongside higher raw material costs compared to the same period last year. He also highlighted an adverse impact from the company’s Tornel business in Mexico, which faced uncertainty due to tariffs on exports from Mexico to the United States, dampening volumes.
Resilience in Domestic and Export Markets
Dr Raghupati Singhania, Chairman and Managing Director, JK Tyre & Industries, said, “The growth momentum in domestic markets remained robust in Q1, with JK Tyre clocking a sales growth of 11 percent YoY, as contributed by a steady demand for our products in both replacement as well as OE segments, underscoring JK Tyre’s continued focus on core growth drivers and strengthening market presence.”
“Despite a challenging and uncertain macro-economic environment, exports of passenger car tyres witnessed a strong traction both on QoQ and YoY basis, signifying pull for our products and enhanced brand perception in the global markets,” said Dr Singhania.
Operational efficiencies and strategic pricing supported performance, even as natural rubber prices remained elevated. Subsidiaries Cavendish (India) and Tornel (Mexico) continued to contribute significantly to the group’s consolidated financials.
Operational efficiencies and strategic pricing supported performance, even as natural rubber prices remained elevated. Subsidiaries Cavendish (India) and Tornel (Mexico) continued to contribute significantly to the group’s consolidated financials.
Regarding trade tensions between India and the US, Anshuman Singhania noted that exports from India to the US account for only around 3 percent of JK Tyre’s revenue and could be redirected to markets such as Mexico, Latin America, Brazil and the UAE if required. With zero tariffs in Mexico, JK Tyre can utilise its production base there to meet demand for both passenger and truck radials. The EU and UK, where JK Tyre holds a strong position in the TBR segment, also remain tariff-free.
Capacity expansion
The company’s INR 14 billion capital expenditure plan is progressing on schedule, covering passenger car radial (PCR), TBR and all-steel truck radial projects. For the year, investment is expected to total INR 9-10 billion, aimed at boosting production capacity by 30-40 percent.
A key driver for future profitability is the shift towards premium products. The share of 16-inch and above passenger car tyres in JK Tyre’s portfolio has grown from 18 percent in FY2020 to 25 percent in FY2025, with a target of 40-45 percent over the next two to three years. This change is being fuelled by rising SUV sales, larger rim sizes in entry-level cars and strong export demand.
The company has also developed a complete range of tyres for electric vehicles, spanning commercial truck radials, bus tyres, passenger radials and two/three-wheeler tyres Major OEMs such as Ashok Leyland’s Switch Mobility and Tata Motors are sourcing these products, including for last-mile connectivity vehicles and newly launched EV buses.
Market Outlook
The replacement market has been a bright spot, with passenger radial volumes up 32 percent year-on-year and truck radial volumes growing in the high single digits. JK Tyre expects demand to strengthen in the second half of FY2026, supported by infrastructure development, a favourable monsoon, potential interest rate cuts, and improved consumer liquidity.
Anshuman Singhania stressed that the worst of raw material price pressures appear to be over, paving the way for margin improvement as the product mix shifts and capacity utilisation rises. With the small car segment’s gradual decline offset by growth in premium categories, JK Tyre remains confident in sustaining momentum.
“Overall, India is poised for growth,” Singhania concluded. “We see positives across the board — from infrastructure push to evolving consumer preferences — and we are well-positioned to capitalise on these trends.”
Yokohama Rubber begins OE tyre supply for BYD’s SEALION 6 DM-i SUV in China
- By TT News
- August 07, 2025
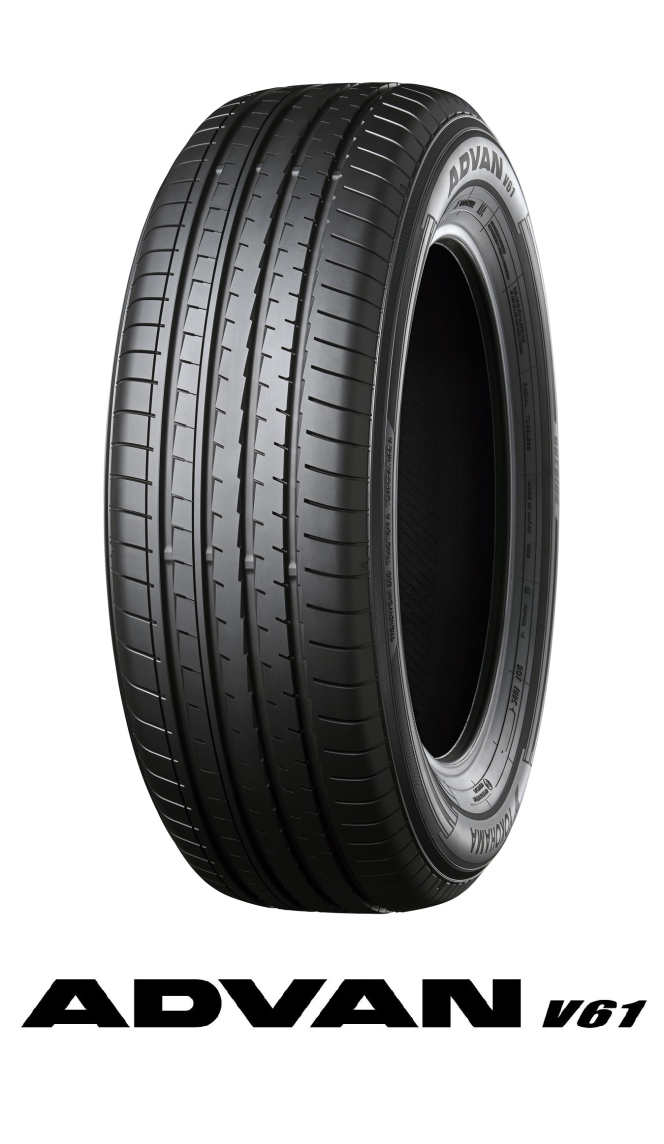
Yokohama Rubber has begun supplying its ADVAN V61 tyres as original equipment for BYD’s new SEALION 6 DM-i SUV, marking the Japanese manufacturer’s first OE partnership with the Chinese carmaker.
The SEALION 6 DM-i, a plug-in hybrid SUV launched by BYD Company Ltd. this July, is being factory-fitted with 235/50R19 103V size ADVAN V61 tyres. The announcement comes as Yokohama seeks to grow its footprint in China’s fast-evolving electric and hybrid vehicle market.
The ADVAN V61 is part of Yokohama’s global flagship ADVAN range and is positioned as a premium SUV tyre. The company said the tyre “offers ADVAN’s hallmark premium-grade driving performance, along with a high-level balance of fuel and energy efficiency, handling stability, and quietness, achieving both comfortable city driving and long-distance touring for heavyweight SUVs.”
The SEALION 6 DM-i combines a 1.5-litre naturally aspirated petrol engine producing up to 74kW with an electric motor generating 160kW. Buyers can choose between 18.3 kWh and 26.6 kWh blade battery options, offering electric driving ranges of 93km and 130km, respectively. All models come equipped with advanced driver assistance systems as standard, and the exterior design draws inspiration from the concept of “ocean aesthetics.”
Sumitomo Rubber’s Tyre Unit Clears Japan Antitrust Probe With Commitment Plan
- By TT News
- August 07, 2025
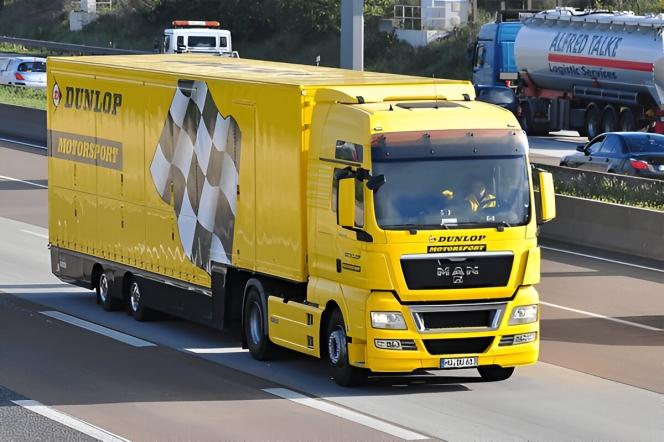
Sumitomo Rubber Industries Ltd said its subsidiary Dunlop Tyre Japan Ltd has completed a Japan Fair Trade Commission investigation into automotive all-season tyre sales after the regulator approved a commitment plan submitted by the unit.
The probe, which examined the subsidiary’s sales practices, concluded without the commission identifying any violation of Japan’s Antimonopoly Act, Sumitomo Rubber said in a statement.
Under Japan’s commitment procedures, companies can submit plans to address potential competition concerns without admitting wrongdoing, allowing them to resolve investigations while avoiding formal sanctions.
"We deeply apologise for the great trouble and anxiety that we have caused to all concerned, including our clients and business partners,” the tyre maker said.
Bekaert Warns Of Weakening Demand As Tariffs And FX Weigh On Outlook
- By TT News
- August 04, 2025
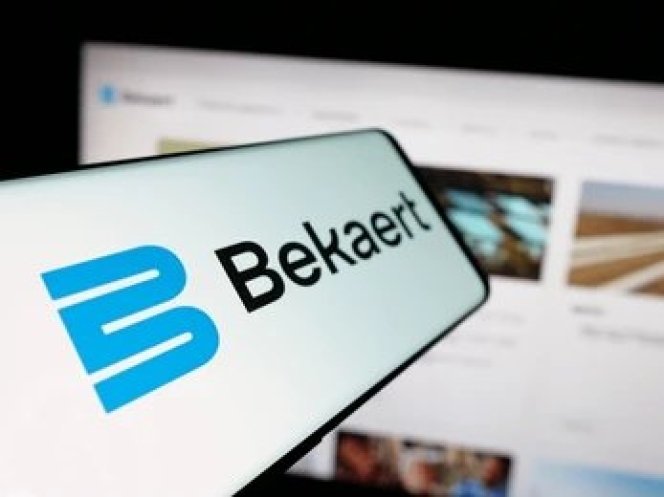
Belgian steel wire maker Bekaert reported resilient first-half 2025 earnings as strong cash generation and cost control offset softer sales, but warned that tariffs and currency pressures are weighing on demand.
The company posted consolidated sales of €1.9 billion, down 5.2 percent year-on-year, with volumes declining 2.6 percent and price/mix effects stripping out a further 2.2 percent. Underlying EBIT slipped 16.2 percent to €171 million, delivering a margin of 8.8 percent compared with 9.9 percent a year earlier.
Free cash flow surged to €123 million from €43 million in the prior-year period, driven by a €135 million reduction in working capital and €21 million in cost savings as the company continued to streamline operations and rein in capex. Net debt fell to €327 million from €399 million despite a continuing €200 million share buyback programme, €74 million of which has been completed.
“We have continued to focus on what we can control best – cash flow and costs - and have significantly reduced overheads and working capital in H1 2025,” chief executive Yves Kerstens said. “Equally, I am very pleased with the hard work of our teams fighting for volumes in the current challenging markets.”
He added: “We are also taking further steps to make our business units more autonomous and agile. Therefore, I am very confident that we will come out of the current business environment stronger and more cost competitive than ever before.”
Bekaert said volumes were particularly strong in its Steel Wire Solutions and Rubber Reinforcement divisions in the United States and China, while European and Latin American demand lagged. Its Brazilian joint ventures delivered €24 million in net profit share, up from €20 million a year ago.
However, the group cautioned that growing trade tensions – including a rise in US steel tariffs from 25 percent to 50 percent – and the weakening of the US dollar and Chinese yuan against the euro were eroding pricing power and softening orders.
“Following a period of resilience in Q2, the tariff uncertainty and weakening economic outlook has started to have an impact on demand,” Bekaert said.
The company now expects slightly lower full-year 2025 sales on a like-for-like basis, with an underlying EBIT margin of between 8.0 percent and 8.5 percent, down from 8.8 percent in the first half.
Comments (0)
ADD COMMENT