JK Organisation Commences ‘Mission Critical’, A Vaccination Effort
- By TT News
- April 29, 2021
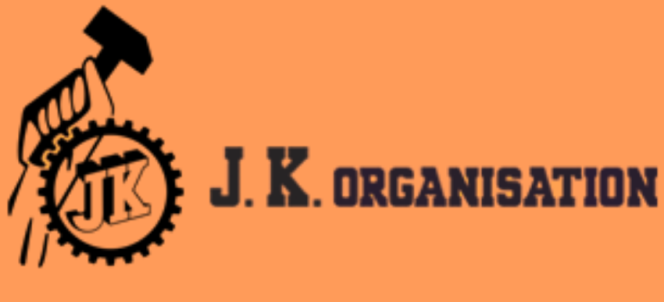
JK Organisation has commenced ‘Mission Critical’, a CSR drive, to ensure rapid vaccination of its stakeholders across the organisation.
The group has already vaccinated over 12,000 personnel so far. With all Indian adults being eligible to receive the Covid-19 vaccine starting May 1, JK aims to vaccinate over 40,000+ individuals soon.
Additionally, to extend support for immediate on-ground response to a large section of the society and its employees, JK Organisation has set up a Covid-19 helpdesk at the Pushpawati Singhania Research Institute (PSRI Hospital), New Delhi, and created isolation wards near its plants for migrant labour and other communities. The Covid Core Group, comprising of the top management personnel, has also been created to review the Covid 19 relief measures every week.
Bharat Hari Singhania, President, JK Organisation, said, “The safety and wellbeing of our people, our customers, business partners, and the communities in which we operate, are of paramount importance and our utmost priority. Everything else, comes later”. (TT)
Continental Americas Announces Leadership Transition In Replacement Tires Business
- By TT News
- June 08, 2025
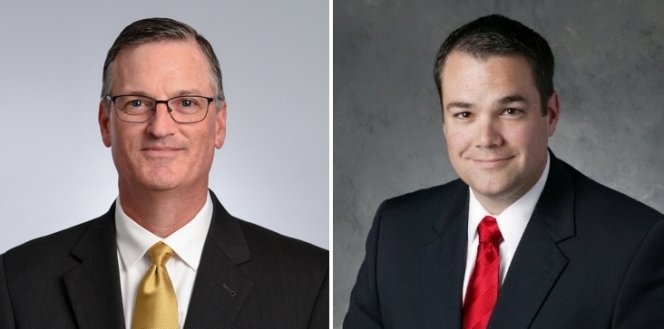
Continental Tire the Americas, LLC has announced an upcoming leadership transition in its U.S. Passenger and Light Truck (PLT) replacement tyre division. Bill Caldwell, Senior Vice President of Sales and Marketing, will retire in June 2025 after more than 20 years with the company. Chris Charity, the current Vice President of Sales, will assume Caldwell’s role effective 1 July 2025.
Caldwell has been at the helm of the U.S. PLT replacement business since 2009, following his leadership of Continental’s Original Equipment (OE) Key Account Management team. During his tenure, he played a pivotal role in expanding the market presence of both the Continental and General Tire brands, driving strategic growth and strengthening dealer partnerships.
Charity, a 20-year veteran of Continental, joined the company in 2002 as a quality engineer before transitioning into sales leadership. His deep industry knowledge, customer-focused approach and proven track record in sales strategy make him the ideal successor to continue the division’s upward trajectory.
Tansu Işık, Head of Continental’s Business Area Replacement Tires the Americas, said, “Bill has made a lasting contribution to Continental’s success in the Americas. His leadership, integrity and commitment to excellence have helped shape the business and culture. On behalf of the entire organization, I want to thank Bill for his outstanding service and wish him a fulfilling and well-deserved retirement.” On Charity’s appointment, he said, “Chris brings the right mix of experience, vision and dedication to lead our U.S. PLT Replacement business into the future. I’m confident he will continue to build on our strong foundation and drive further success.”
Caldwell said, “I’m incredibly proud of what we’ve accomplished together over the years. It’s been an honour to work with such a dedicated team, and I’m confident that Chris will continue to lead with the same passion and commitment that has defined our success.”
Charity said, “I’m grateful for the opportunity to step into this role and build on the strong foundation Bill has laid. I look forward to working with our teams and partners to continue delivering value and innovation to our customers.”
Nokian Tyres CFO Niko Haavisto to depart as Finnish tyre maker begins succession search
- By TT News
- May 30, 2025
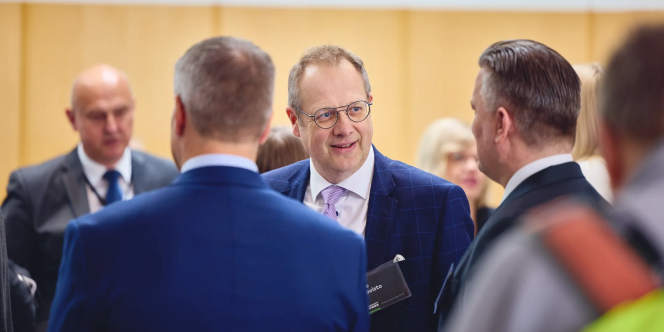
Finnish tyre manufacturer Nokian Tyres Plc said its chief financial officer Niko Haavisto would leave the company, with the firm moving quickly to appoint an interim replacement whilst searching for a permanent successor.
The Helsinki-listed company announced that Jari Huuhtanen, currently vice president of group business control, would step into the CFO role on an interim basis from June 1st as the recruitment process gets underway.
Nokian Tyres, known for its winter and all-season tyres, provided no details regarding Haavisto's reasons for departure or his future plans.
The announcement comes during a challenging period for the global tyre industry, which has faced supply chain disruptions and fluctuating raw material costs.
"I want to thank Niko for his contributions to the company. Niko has been a valuable member in the Nokian Tyres team, and we wish him all the best in his future endeavours," said Paolo Pompei, president and chief executive of Nokian Tyres.
The company has not disclosed a timeline for appointing Haavisto's permanent replacement.
Michelin Opens New Service Store In Bengaluru As Premium Car Market Grows
- By TT News
- May 28, 2025
French tyre manufacturer partners with Cherry Tyre Park for 3,000 sq ft facility in Indiranagar
Michelin has opened a new service store in Bengaluru, expanding its retail footprint in India's technology capital as demand for premium automotive services rises alongside growing luxury car ownership.
The 3,000 square foot Michelin Tyres & Services Store, located in the upmarket Indiranagar district, has been established through a partnership with Cherry Tyre Park, India's largest tyre retail network. The facility offers precision tyre fitting, wheel balancing and alignment services.
Michelin's expansion comes as Bengaluru experiences increased demand for high-performance mobility solutions, driven by a growing market for premium and luxury vehicles in the city, which serves as India's information technology hub.
"Bengaluru has always been a key market for us with our consumers valuing quality, innovation, and performance. The launch of this new Michelin Tyres & Services store in partnership with Cherry Tyre Park strengthens our commitment to bringing world-class services and a premium experience for our customers in this dynamic and fast-growing market," said Shantanu Deshpande, Managing Director of Michelin India.
The store was inaugurated by Siddharth Mehta, Marketing Director at Michelin India, alongside representatives from Cherry Tyre Park.
Cherry Tyre Park has maintained a partnership with Michelin for over 12 years. The collaboration reflects Michelin's strategy to leverage established retail networks whilst expanding its presence in India's southern region.
The French company, which positions itself as a technology leader in the tyre industry, has been tailoring its premium offerings to meet the requirements of luxury and high-performance vehicles as India's automotive market evolves.
Michelin's latest store opening underscores the company's broader commitment to enhancing retail infrastructure and customer service capabilities across key Indian markets, particularly in regions with significant premium vehicle penetration.
Comerio Ercole Marks 140 Years with Major R&D Expansion
- By TT News
- May 26, 2025
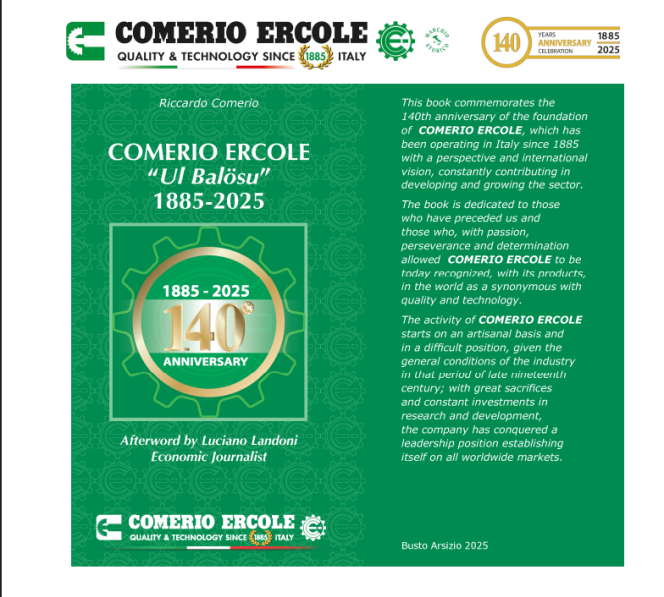
Italian industrial machinery manufacturer Comerio Ercole SpA is celebrating its 140th anniversary this year whilst unveiling significant investments in research and development capabilities as the family-owned company seeks to strengthen its position in global polymer processing markets.
The Busto Arsizio-based firm, which exports 94 percent of its production worldwide and employs 250 people across its group operations, has published a commemorative 272-page book documenting its industrial journey from 1885 to 2025. The company was founded by Ercole Comerio, known affectionately as “Ul Balösu”, who launched the enterprise the same year he married Teresa Marcora.
Comerio Ercole will showcase two major technological developments at its main production facility on 6th June, opening its doors to institutional partners and industry stakeholders. The company is launching a new universal Industry 5.0 manufacturing centre alongside an expanded R&D technology centre featuring advanced experimental equipment.
“Our corporate DNA is based on deep respect for tradition and constant forward-looking drive within an evolutionary process that never stops,” said Riccardo Comerio. “Every day we face challenging and stimulating situations that push us to keep improving.”
The R&D expansion includes two new experimental machines - one for mixing and one for calendaring - equipped with cutting-edge longitudinal stretching units for thin sheets. The facility’s main laboratory operates as a “mini-factory” with a four-roll calendering line that can be reconfigured to three or five rolls depending on process requirements.
The enhanced laboratory features a dual-feeding system accommodating direct extrusion and feeding from mills and internal mixers. A second laboratory houses a calendering line designed for the embossing processes of films and nonwovens, offering up to 100 different patterns for material enhancement.
These investments are designed to bolster the company’s capacity to support customers in developing new polymer and elastomer processing techniques. Comerio Ercole’s R&D team provides project support through patent validation, underlining the firm’s focus on technology and service delivery.
Economic journalist Luciano Landoni, who authored the commemorative book's afterword, highlighted the company’s entrepreneurial example. “The entrepreneurial example of Comerio Ercole is highly motivating, especially for young people, who now more than ever need concrete signals based on competence, passion and vision," he said.
The company operates under the corporate structure of Comerio Ercole SpA a Socio Unico, with a share capital of €2.2 million, and is coordinated by Comerio 1885 Holding Srl SB. Its machinery serves customers in the polymer and rubber processing industries globally, and the firm maintains its headquarters at Via Castellanza 100 in Busto Arsizio, northern Italy.
Comments (0)
ADD COMMENT