Lowering Costs And Changing Testing Parameters With Advanced Systems
- By Sharad Matade
- April 17, 2025
The tyre industry is navigating a complex landscape of rising material costs, geopolitical uncertainties and fierce competition. In response, manufacturers are turning to automation, Industry 4.0 and AI-driven solutions to enhance efficiency and reduce operational expenses. Advanced testing and measurement systems are pivotal in this transition, offering cost-effective quality control, streamlined production and improved consistency. However, integrating these innovations poses challenges, including adapting to evolving tyre designs and meeting stricter OEM requirements. This article explores how technological advancements in tyre testing are reshaping the industry, ensuring performance precision and economic viability in an increasingly competitive market.
Increasing raw material prices, geopolitical crises, rising freight costs and stronger competition have led tyre companies to find ways to lower operational costs. Technological breakthroughs like automation, Industry 4.0, etc. are a boon in disguise in this hour of need. While automation is not a new concept, its usage gradually increases within the tyre industry, riding on the back of other advancements.
Micro-Poise Measurement Systems Division Vice President & Chief Technology Officer Dr Shaun M Immel believes that the ever-increasing need for automation and data connectivity to support Industry 4.0 is driving tyre manufacturers to adopt advanced measurement systems that lower inspection costs, enhance consistency and provide critical data for analytics.
“Simultaneously, manufacturers seek improved equipment throughput while maintaining high measurement quality to meet tightening tyre screening requirements. The growing variety of electric vehicle (EV) tyre designs necessitates greater measurement system flexibility to support a larger number of stock-keeping units (SKUs). Additionally, customers increasingly require user-friendly systems that accommodate inexperienced personnel by presenting simple-to-use and highly automated products,” he added while speaking exclusively to Tyre Trends.
The tyre testing industry has significantly transformed over the past five years. Automation cuts measurement and inspection costs while improving consistency and predictability, allowing manufacturers to redeploy labour to higher-value tasks. It also enables precise, data-driven decision-making by replacing subjective human evaluations with quantifiable metrics, ensuring better process control and continuous improvement.
As tyres grow larger and heavier, automation presents new challenges, but advancements in artificial intelligence (AI), faster processing power and GPU technology are making implementation more feasible and cost-effective. These innovations are fuelling a resurgence in automation, enhancing efficiency and providing manufacturers with deeper insights into production quality and performance.
However, he noted that while including sustainable materials within tyre compounds is strong founded within tyre makers, it is not likely to affect testing strongly. “The shift towards sustainable materials in tyre manufacturing is reshaping the industry. While this evolution may impact tyre design materials and manufacturing processes, it will not significantly alter the core processes of final finish testing. Testing equipment focuses on force variation, dynamic balance, X-ray analysis and geometry measurement, and it remains largely unaffected as long as tyre sizes stay within standard categories. However, as manufacturers integrate new compounds and materials, potential changes in tyre behaviour may lead to adjustments in testing methodologies to address emerging manufacturing challenges,” said Dr Immel.
PARADIGM EVOLUTION
The tyre industry is undergoing a strategic shift. Top-tier manufacturers are moving away from mass production to focus on high-performance and premium tyres, consolidating production into specialised plants for passenger, truck and OTR tyres. This shift is driven by increasing competition from Asian manufacturers dominating the mass-market segment. At the same time, some Asian players are pushing into the premium space, intensifying competition at the high end.
This evolving landscape reinforces the demand for precision testing, high measurement quality and faster throughput. “Our longstanding partnerships with tier-one manufacturers position us well in this premium market, particularly in the 18-inch-and-above segment, where measurement accuracy and reliability are critical and where Micro-Poise’s measurement systems excel. As the industry diversifies, we continue to enhance our equipment’s flexibility and feature set to meet the evolving needs of both established premium brands and emerging challengers,” said Dr Immel.
Furthermore, Dr Immel noted that the testing industry is undergoing significant advancements with a strong focus on increasing throughput while meeting increasingly stringent quality requirements. “Tyre manufacturers face tightening OEM screening limits, necessitating greater accuracy and repeatability in measurement systems to ensure precise and proper classification of tyres for various markets. Traditionally, higher throughput and improved measurement repeatability are a trade-off, but the industry is now working to improve both simultaneously, requiring innovative approaches,” he said.
“A notable shift, particularly influenced by EVs, is the growing demand for higher frequency content in geometry and uniformity measurements. As EVs eliminate engine noise, tyres have become the dominant source of road noise, prompting manufacturers to analyse higher-frequency variations that could contribute to unwanted sound. These variations, often linked to tread design and tyre construction, are now being examined more closely for tyre-to-tyre variation to mitigate its impact,” he added.
He also contended that regulatory trends and market dynamics are driving further changes beyond noise control. The rise of EVs has significantly expanded the number of SKUs manufacturers must manage, pushing the need for greater equipment flexibility and quicker changeover.
“With tyre designs evolving rapidly, testing systems must adapt through quick-change tooling and advanced marking capabilities to accommodate frequent model shifts. At the same time, manufacturers continue to push for higher throughput without compromising measurement and inspection performance, reinforcing the need for cutting-edge solutions that balance speed, accuracy and adaptability in an increasingly complex landscape,” he added.
MEASURING PARAMETERS
According to Dr Immel, the time required to measure and assess a single tyre depends on the type of test(s) being conducted. A typical measurement cycle may range between 15 and 30 seconds, depending on the tyre size, the required tyre ‘warmup’ time, and the measurements being performed. The key to high-quality final finish equipment is to ensure high throughput while maintaining the measurement performance necessary for accurate quality assessments.
Explaining the quality measurement process, he said, “Quality measurement in tyre testing hinges on two fundamental aspects, accuracy and repeatability. Accuracy refers to each measurement’s ability to reflect the tyre’s true assessment value and characteristics, a non-trivial task given the inherent variability in production tyre measurement. Manufacturers rely on these values to determine whether a tyre meets quality standards or should be scrapped.”
Repeatability, on the other hand, measures measurement consistency. Sophisticated technology minimises measurement variations of production tyres, ensuring that the system can effectively differentiate between acceptable and defective products. The financial impact of incorrect classifications, whether approving a faulty tyre or rejecting a good one, is substantial, making excellent system measurement performance a critical factor in reducing long-term operational costs.
Answering what tyre screening limits are acceptable to the market, he said, “The acceptable limits are proprietary to each tyre manufacturer. Each manufacturer receives screening limits from original equipment (OE) manufacturers and select replacement market dealers. These OE and replacement screening limits vary across players. Beyond that, tyre companies often impose stricter internal limits to enhance quality, improve customer perception or differentiate products.”
Alluding to whether the industry is more concerned about variation in passenger car tyres than in TBR or OTR tyres, he explained, “The industry is indeed more focused on variations in PCR, but I believe that’s largely due to volume. Passenger car tyres are produced in significantly higher numbers, and since they are consumer-facing products, expectations are much higher. People notice and care about ride quality, so manufacturers focus heavily on minimising tyre-to-tyre variations.”
“However, even in the TBR segment, certain types like steer and drive tyres undergo strict testing and must meet high standards. Steer tyres, in particular, incorporate advanced technology because they directly impact vehicle handling and safety. Trailer tyres, on the other hand, face less scrutiny since they directly affect ride comfort. That said, manufacturers across all segments are under continuous pressure to tighten tolerances. OEMs and fleet operators are always pushing for lower limits, forcing tyre makers to improve,” he added.
The company is advancing tyre grading technology with a data-driven approach that moves beyond traditional tyre metrics. Developing and integrating alternative measurements aims to refine performance assessments, ensuring a closer correlation between lab results and real-world ride quality. This shift could boost product yields while maintaining more stringent standards, enabling a ‘smarter’ assessment of tyre quality.
When asked about the causes of early tyre failure and how geometry plays a role in identifying defects, he explained that issues in ply splicing during manufacturing can lead to structural weaknesses. If the ply material splice is left open, missing ply cords create a bulge defect when the tyre is inflated under high pressure.
This bulge, a critical measurement in quality control, appears radially along the sidewall and is a standard defect monitored by tyre manufacturers. If the bulge exceeds acceptable limits, it can cause the inner liner to become voided, leading to slow air loss and deflation – an irreparable but not necessarily catastrophic failure mode.
Dr Immel also noted that the company has developed several features to enhance flexibility. “We have an automatic rim change feature with adaptable tooling that streamlines adjustments. We’re also exploring innovations to improve changeover efficiency further. One of our key advantages is that when a tyre enters the system – even if it’s a single unit – we can immediately identify it, load the correct parameters and process it without any cycle time penalty. Unlike other machines requiring manual adjustments and extra cycle time, ours can handle small lot sizes and frequent model changes seamlessly,” informed Dr Immel.
When asked whether every tyre produced on the line is measured, Dr Immel explained that almost all OE tyres undergo screening to meet strict screening limits. For the replacement market, tyre manufacturers screen a varying percentage of products, depending on customer requirements and market strategy. While nearly 100 percent of OE tyres is tested, the extent of screening for replacement tyres varies across manufacturers and customers.
PRODUCT CATALOGUE
Micro-Poise Measuring Systems’ ASTEC FX system evaluates critical parameters such as force variation, while Micro-Poise’s TGIS FS system evaluates tyre runout and sidewall appearance. While these factors primarily influence ride comfort rather than direct safety, they play a role in detecting defects that could lead to premature tyre failure. “Some of these defects have been monitored for decades, forming an industry benchmark,” noted Dr Immel.
When discussing the process of force variation measurement, the executive compared a tyre to a system of parallel springs, where each section should ideally have the same spring constant or stiffness around the tyre. However, variations in manufacturing such as splices, component alignments and positioning errors can create inconsistencies, making certain areas stiffer or softer than others, resulting in a variation of the force the tyre induces into a vehicle while driving.
A load wheel presses into the tyres while it rotates to detect these variations, measuring force fluctuations. Higher force readings indicate stiffer areas, while lower ones suggest softer regions. This data is analysed using Fourier analysis, breaking it down into harmonics to help manufacturers ensure that force variation at certain frequencies remains within acceptable limits.
The US-headquartered company’s ITMS FX (Integrated Tire Measurement System) minimises testing cycle times while integrating and maintaining excellent measurement quality across force variation, dynamic balance and geometry measurements. In high-volume manufacturing, any cycle time advantage can significantly impact overall throughput, driving up the overall equipment value for the customer. “It’s always about how fast you can get the process done – get one tyre out, bring the next in and repeat,” Dr Immel explained.
Beyond speed, system reliability is equally important. Fully automated testing systems need to run continuously with minimal stoppages. “If a fault occurs, recovery must be instant,” he added. However, increasing speed without sacrificing measurement quality presents an inherent challenge.
The company’s Tire Geometry Inspection System (TGIS FS) integrates proprietary tyre-optimised 3D sensors to inspect sidewall geometry accurately. The system employs three strategically placed sensors in fixed locations – one each on the top lateral, radial and bottom lateral surfaces – to complete a full geometric scan in a single tyre revolution. The result is a micron-resolution contour of the entire tyre. This data supports defect detection, dimensional measurements and process optimisation. The system is adaptable across Micro-Poise’s force variation (uniformity), dynamic balance machines and various competitive equipment.
The company is reinforcing its position as the ‘automation partner of choice’ for tyre manufacturers, supported by the fact that it has always focused exclusively on final finish solutions. The company is driving towards fully automated ‘Lights Out’ operations, ensuring maximum efficiency and cost-effectiveness across all its products.
Key advancements include revolutionary throughput enhancements that significantly improve final finish processes without adding costs, ease-of-use innovations that simplify complex systems for less experienced operators and increased flexibility through automated changeovers to address the growing number of SKUs in tyre production.
Additionally, it is advancing automated inspection and defect detection by helping its customers shift from manual to autonomous inspection, which encompasses more precise numerical measurements, reduced errors and a reduction in overall inspection costs.
A major breakthrough in this area is the integration of AI and deep learning (DL) into its Coll-Tech Automatic Defect Recognition (ADR) software for tyre X-ray image analysis. Showcased at the 2024 Tire Tech Expo, the latest advancements have dramatically improved defect detection accuracy and responsiveness to customer configuration and customisation requests.
“Previously, algorithmic versions required extended response times for adaptation and modification, but the AI-driven enhancements have eliminated this delay. Multiple manufacturing facilities are now operating their ADR-equipped X-ray systems without human inspectors, allowing personnel to be redeployed elsewhere while significantly reducing inspection expenses. The transition to full autonomous inspection is a learning process that requires adaptation, but the investment yields substantial positive financial returns. Micro-Poise’s ADR system allows our customers to control the pace and number of steps in the journey to full autonomous inspection. To facilitate adoption, we offer image evaluations, follow-up consultations and in-plant demonstrations,” said Dr Immel.
Beyond inspection advancements, Micro-Poise has also improved tyre grinding systems, enhancing both functional system performance and the visual appearance of ground tyres.
Historically, tyre grinding – used for force variation and geometry optimisation – has been instrumental in converting rejected tyres into OE-grade products. However, some manufacturers hesitate to adopt grinding due to concerns about visible grind marks. Micro-Poise has addressed these concerns by refining the grind appearance and adding new functionalities that turn tyre grinding from an art into a precise science. These innovations increase product yield, improve tyre grading and deliver a strong return on investment for manufacturers. With AI-driven defect detection, automation advancements and improved tyre yield solutions, Micro-Poise is setting new standards for efficiency, accuracy and cost savings in the final finish stage of tyre manufacturing.
The company continuously refines its technology, balancing cost efficiency with high performance. “Customers request additional features based on unique measurement methodologies and defect detection requirements,” Dr Immel said.
Customers expect the machines to operate for decades. Mechanically, the company’s systems are built for longevity, but electronics and software evolve much faster. To address obsolescence, the company offers modular control system upgrades bundled with new features, ensuring customers gain added value while modernising their equipment and extending its lifecycle.
In the context of retrofitting, Dr Immel said, “We design machines to accommodate sensor and measurement upgrades, enabling customers to integrate new parameters without replacing entire systems. The balance lies in designing robust mechanical structures while allowing flexibility in electronics and software.”
ADDRESSING CHALLENGES
Developing intuitive, easy-to-use machines is an ongoing challenge. “Simplifying a machine while maintaining its capabilities is often harder than designing a complex system,” Dr Immel noted.
The company has invested in UX/UI enhancements to improve operator efficiency and ease of use.
Furthermore, the tyre industry is currently facing one of its most dynamic and challenging periods, driven by rapid technological advancements, shifting regulations, sustainability initiatives and the rise of EVs.
One of the biggest challenges is aligning new technologies with practical applications that benefit customers while ensuring their confidence in these innovations. AI and automation, for example, are transforming manufacturing processes, but their complexity can be daunting for tyre producers who must navigate ever-changing market demands.
Additionally, external factors such as tariffs, trade wars and regulatory changes add another layer of uncertainty, making it critical to choose the right technologies that will bring long-term value.
Sustainability is another key concern as tyre manufacturers work to reduce environmental impact through raw material innovations, renewable energy adoption and energy-efficient manufacturing processes.
While the company does not directly influence the chemical composition of tyres, it contributes to sustainability by designing testing and measurement equipment that uses less energy and air.
With AI-driven automation, faster cycle times and a strong focus on usability and upgradeability, it continues to push the boundaries of tyre testing technology. As the industry embraces data-driven solutions, the company remains at the forefront of precision measurement and defect detection.
FUTURE FOCUS
The industry is undoubtedly shifting towards fundamental measurement improvements and enhanced features like predictive maintenance, retrofitment and software upgrades.
“While reducing testing time and improving efficiency remain core priorities, there is an increasing demand for smart, automated solutions that can provide deeper insights into machine performance. Predictive maintenance is an exciting development area, but it is still in its early stages. The ultimate vision is to have intelligent software capable of real-time monitoring systems and predicting failures with precision. However, before reaching that stage, the focus is on establishing a solid data foundation and ensuring rapid recovery when issues arise,” averred Dr Immel.
To address these challenges, the industry is exploring soft sensor technology as a potential alternative to expensive hardware-based monitoring systems. These advancements could reduce reliance on physical sensors while still enabling predictive maintenance capabilities. As the industry moves forward, manufacturers must balance cost, efficiency and long-term viability to maximise the benefits of these innovations.
“The integration of AI and DL technologies is poised to continue, though adoption will likely be measured as manufacturers proceed with caution. While some advancements will prove transformative, others may fade over time. AI-driven systems can significantly improve productivity by shortening design and improvement cycles, making processes more efficient. Additionally, AI models can refine their accuracy over time through continuous feedback and training, leading to smarter and more effective applications in manufacturing,” he added.
He also noted that one key concern is the potential burden on customers. Some AI implementations risk shifting performance optimisation responsibilities such as defect evaluation, labelling and training onto end users. While this may be expected in later stages of adoption, it presents a significant challenge in the early phases, making seamless integration into existing workflows critical.
Another significant area of advancement is tyre grinding technology. While some manufacturers hesitate to use grinding due to concerns over visual imperfections, it remains a valuable and financially beneficial process for refining tyres that exceed variation limits.
Recent innovations aim to standardise and automate grinding, transforming it from an art into a precise, science-driven method. These advancements make the process more efficient and user-friendly, ensuring higher-quality output without compromising visual appearance. n
Micro-Poise TGIS FS Geometry Sensor
JK Tyre Targets Double-Digit Growth in FY2026, Targets INR 10 Billion CAPEX
- By Nilesh Wadhwa
- August 08, 2025
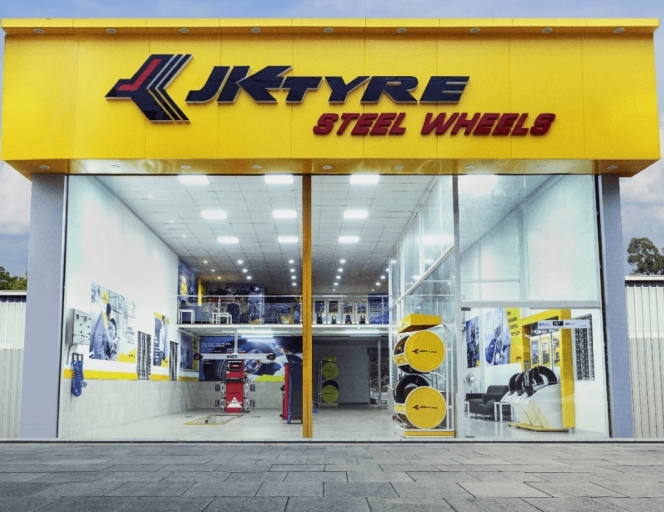
JK Tyre & Industries is aiming for double-digit revenue growth in FY2026, outpacing its forecast for single-digit expansion across the broader tyre industry. Managing Director Anshuman Singhania outlined the company’s ambitions during a post-earnings media call, underscoring confidence in demand recovery and strategic market positioning.
Q1 Performance Overview
For the first quarter of FY2026, JK Tyre reported revenue of INR 38.91 billion, with EBITDA at INR 4.24 billion, translating to a margin of 10 percent. Net profit stood at ₹1.55 billion — up 51 percent compared with the previous quarter, but down 21 percent YoY.
Singhania attributed the annual decline to muted original equipment (OE) demand, particularly in truck and bus radial (TBR) volumes, alongside higher raw material costs compared to the same period last year. He also highlighted an adverse impact from the company’s Tornel business in Mexico, which faced uncertainty due to tariffs on exports from Mexico to the United States, dampening volumes.
Resilience in Domestic and Export Markets
Dr Raghupati Singhania, Chairman and Managing Director, JK Tyre & Industries, said, “The growth momentum in domestic markets remained robust in Q1, with JK Tyre clocking a sales growth of 11 percent YoY, as contributed by a steady demand for our products in both replacement as well as OE segments, underscoring JK Tyre’s continued focus on core growth drivers and strengthening market presence.”
“Despite a challenging and uncertain macro-economic environment, exports of passenger car tyres witnessed a strong traction both on QoQ and YoY basis, signifying pull for our products and enhanced brand perception in the global markets,” said Dr Singhania.
Operational efficiencies and strategic pricing supported performance, even as natural rubber prices remained elevated. Subsidiaries Cavendish (India) and Tornel (Mexico) continued to contribute significantly to the group’s consolidated financials.
Operational efficiencies and strategic pricing supported performance, even as natural rubber prices remained elevated. Subsidiaries Cavendish (India) and Tornel (Mexico) continued to contribute significantly to the group’s consolidated financials.
Regarding trade tensions between India and the US, Anshuman Singhania noted that exports from India to the US account for only around 3 percent of JK Tyre’s revenue and could be redirected to markets such as Mexico, Latin America, Brazil and the UAE if required. With zero tariffs in Mexico, JK Tyre can utilise its production base there to meet demand for both passenger and truck radials. The EU and UK, where JK Tyre holds a strong position in the TBR segment, also remain tariff-free.
Capacity expansion
The company’s INR 14 billion capital expenditure plan is progressing on schedule, covering passenger car radial (PCR), TBR and all-steel truck radial projects. For the year, investment is expected to total INR 9-10 billion, aimed at boosting production capacity by 30-40 percent.
A key driver for future profitability is the shift towards premium products. The share of 16-inch and above passenger car tyres in JK Tyre’s portfolio has grown from 18 percent in FY2020 to 25 percent in FY2025, with a target of 40-45 percent over the next two to three years. This change is being fuelled by rising SUV sales, larger rim sizes in entry-level cars and strong export demand.
The company has also developed a complete range of tyres for electric vehicles, spanning commercial truck radials, bus tyres, passenger radials and two/three-wheeler tyres Major OEMs such as Ashok Leyland’s Switch Mobility and Tata Motors are sourcing these products, including for last-mile connectivity vehicles and newly launched EV buses.
Market Outlook
The replacement market has been a bright spot, with passenger radial volumes up 32 percent year-on-year and truck radial volumes growing in the high single digits. JK Tyre expects demand to strengthen in the second half of FY2026, supported by infrastructure development, a favourable monsoon, potential interest rate cuts, and improved consumer liquidity.
Anshuman Singhania stressed that the worst of raw material price pressures appear to be over, paving the way for margin improvement as the product mix shifts and capacity utilisation rises. With the small car segment’s gradual decline offset by growth in premium categories, JK Tyre remains confident in sustaining momentum.
“Overall, India is poised for growth,” Singhania concluded. “We see positives across the board — from infrastructure push to evolving consumer preferences — and we are well-positioned to capitalise on these trends.”
Yokohama Rubber begins OE tyre supply for BYD’s SEALION 6 DM-i SUV in China
- By TT News
- August 07, 2025
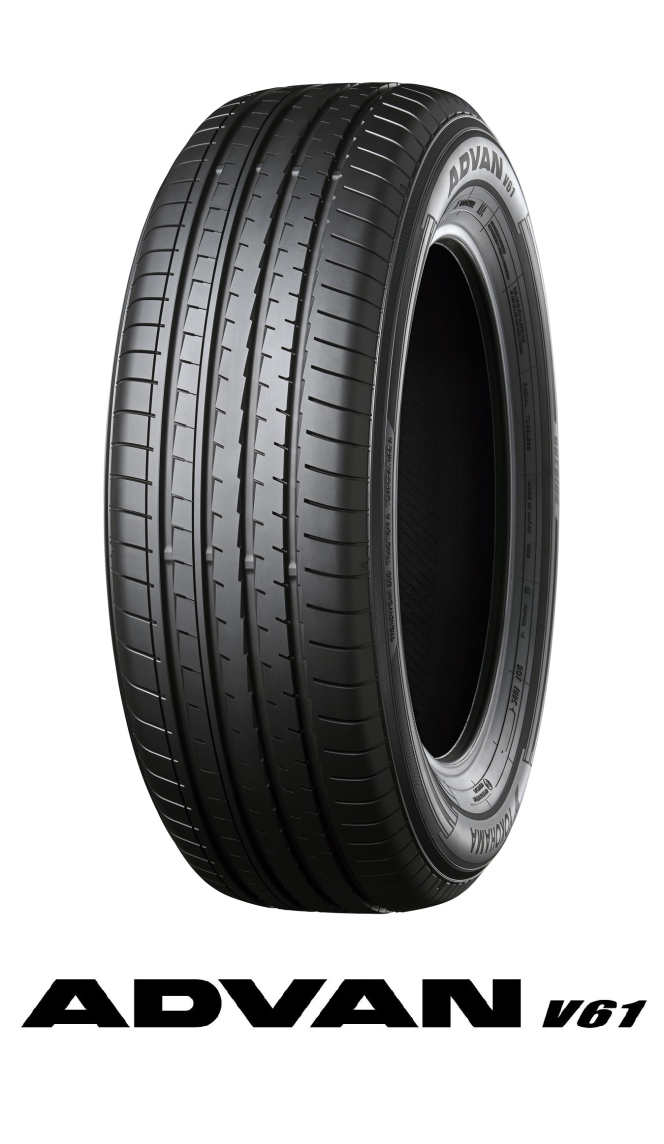
Yokohama Rubber has begun supplying its ADVAN V61 tyres as original equipment for BYD’s new SEALION 6 DM-i SUV, marking the Japanese manufacturer’s first OE partnership with the Chinese carmaker.
The SEALION 6 DM-i, a plug-in hybrid SUV launched by BYD Company Ltd. this July, is being factory-fitted with 235/50R19 103V size ADVAN V61 tyres. The announcement comes as Yokohama seeks to grow its footprint in China’s fast-evolving electric and hybrid vehicle market.
The ADVAN V61 is part of Yokohama’s global flagship ADVAN range and is positioned as a premium SUV tyre. The company said the tyre “offers ADVAN’s hallmark premium-grade driving performance, along with a high-level balance of fuel and energy efficiency, handling stability, and quietness, achieving both comfortable city driving and long-distance touring for heavyweight SUVs.”
The SEALION 6 DM-i combines a 1.5-litre naturally aspirated petrol engine producing up to 74kW with an electric motor generating 160kW. Buyers can choose between 18.3 kWh and 26.6 kWh blade battery options, offering electric driving ranges of 93km and 130km, respectively. All models come equipped with advanced driver assistance systems as standard, and the exterior design draws inspiration from the concept of “ocean aesthetics.”
Sumitomo Rubber’s Tyre Unit Clears Japan Antitrust Probe With Commitment Plan
- By TT News
- August 07, 2025
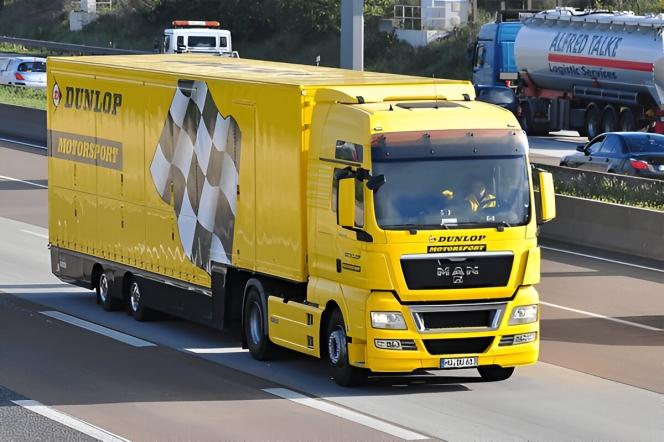
Sumitomo Rubber Industries Ltd said its subsidiary Dunlop Tyre Japan Ltd has completed a Japan Fair Trade Commission investigation into automotive all-season tyre sales after the regulator approved a commitment plan submitted by the unit.
The probe, which examined the subsidiary’s sales practices, concluded without the commission identifying any violation of Japan’s Antimonopoly Act, Sumitomo Rubber said in a statement.
Under Japan’s commitment procedures, companies can submit plans to address potential competition concerns without admitting wrongdoing, allowing them to resolve investigations while avoiding formal sanctions.
"We deeply apologise for the great trouble and anxiety that we have caused to all concerned, including our clients and business partners,” the tyre maker said.
Bekaert Warns Of Weakening Demand As Tariffs And FX Weigh On Outlook
- By TT News
- August 04, 2025
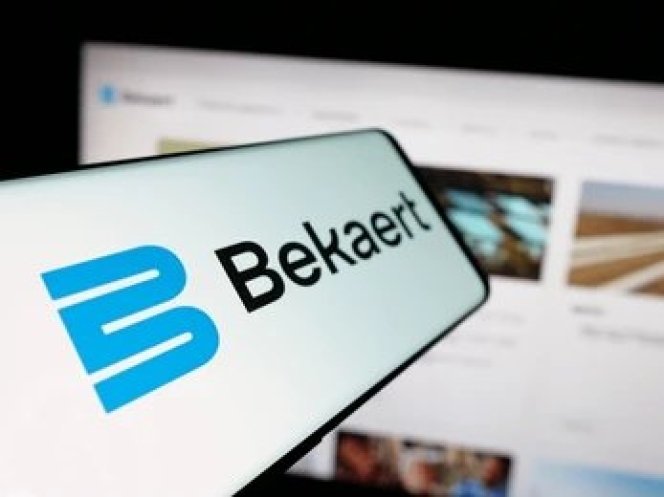
Belgian steel wire maker Bekaert reported resilient first-half 2025 earnings as strong cash generation and cost control offset softer sales, but warned that tariffs and currency pressures are weighing on demand.
The company posted consolidated sales of €1.9 billion, down 5.2 percent year-on-year, with volumes declining 2.6 percent and price/mix effects stripping out a further 2.2 percent. Underlying EBIT slipped 16.2 percent to €171 million, delivering a margin of 8.8 percent compared with 9.9 percent a year earlier.
Free cash flow surged to €123 million from €43 million in the prior-year period, driven by a €135 million reduction in working capital and €21 million in cost savings as the company continued to streamline operations and rein in capex. Net debt fell to €327 million from €399 million despite a continuing €200 million share buyback programme, €74 million of which has been completed.
“We have continued to focus on what we can control best – cash flow and costs - and have significantly reduced overheads and working capital in H1 2025,” chief executive Yves Kerstens said. “Equally, I am very pleased with the hard work of our teams fighting for volumes in the current challenging markets.”
He added: “We are also taking further steps to make our business units more autonomous and agile. Therefore, I am very confident that we will come out of the current business environment stronger and more cost competitive than ever before.”
Bekaert said volumes were particularly strong in its Steel Wire Solutions and Rubber Reinforcement divisions in the United States and China, while European and Latin American demand lagged. Its Brazilian joint ventures delivered €24 million in net profit share, up from €20 million a year ago.
However, the group cautioned that growing trade tensions – including a rise in US steel tariffs from 25 percent to 50 percent – and the weakening of the US dollar and Chinese yuan against the euro were eroding pricing power and softening orders.
“Following a period of resilience in Q2, the tariff uncertainty and weakening economic outlook has started to have an impact on demand,” Bekaert said.
The company now expects slightly lower full-year 2025 sales on a like-for-like basis, with an underlying EBIT margin of between 8.0 percent and 8.5 percent, down from 8.8 percent in the first half.
Comments (0)
ADD COMMENT