New And Worn Phase Tests Make Tyres Safer And Long Lasting
- By Ertugrul Bahan
- December 25, 2024
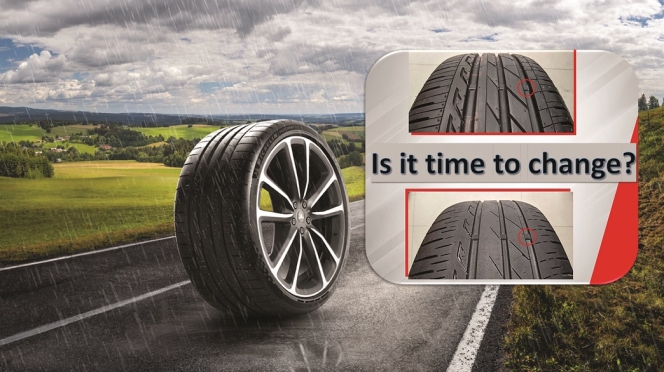
What does ‘Tyre Labelling’ guarantee? It shows schematically the classification of tyres in terms of fuel consumption, noise and wet performance. The tyre manufacturer is obliged to demonstrate the values indicated on the label in tests carried out in accordance with the test method described in EU regulations. This essentially means that the performance parameters of the tyres in question are at least exactly at this level or above the positive side of the limit scale, but only when the tyres are new, i.e. at the beginning of tyre installation. It is technically expected that the stated performance values will not change until the end of the first 10,000 kilometres or until wear of approximately 1.5 mm occurs.
Who knows what the actual grading of tyres will be after the second 10,000 kilometres or at 3 mm down wear stage? No one can correctly estimate what the wet noise and traction will be after most of the mini-kerf or notches are eliminated or reduced, but only when the tyre is tested it can be monitored. Or if the tyre's grooves are completely ‘V’ type, and after a period of time the tyre's traction forces change significantly, then rolling resistance and wet braking behaviour will become significantly different.
The performance level of worn tyres might be therefore quite uncertain and must be taken into account on a legal basis. The wet performance of worn tyres will be a check point for ‘wet grip class’ grading on EU Tyre label after 1st July of 2024, which is in line with the demand of tyre industry parties asking more sustainability. Thanks to the introduction of a new EU regulation R117-04, tyres sold in EU distribution channels meet the same minimum wet braking performance requirements not only when new but also when worn down to the legal minimum tread depth of 1.6 mm.
EU is the most sensitive and advanced market to sustainability in the world. It is driven at any time by the increasingly aspiring regulatory agenda and there is always a constant development in this respect. Requirements of consumers or the automotive industry are more demanding by a more conscious society. Tyres’ life cycle contributing to a more sustainable future proactively identifies and addresses the potential human health and environmental impacts associated with the industry. Therefore, safer and more environmentally sound mobility options are always geared towards resource conservation and fuel economy amongst the focus points of innovations.
Thanks to the introduction of a new EU regulation R117-04, tyres sold in EU distribution channels meet the same minimum wet braking performance requirements not only when new but also when worn down to the legal minimum tread depth of 1.6 mm. They must therefore be tested both as new and as worn tyres before receiving the 'wet grade’ on the label. This means that EU drivers can now buy safer tyres that meet the legal minimum standards for wet braking performance, even when worn down to the legal minimum tread depth.
As a weak point of R117-04 regulation, it only covers wet braking of new and worn-out tyres. It does not cover ‘noise’ and ‘rolling resistance’ items given on labelling or more simply endurance performance level of especially cheap tyres in the market with a 1.6 mm tread depth assuming they will not change!
Informal wet braking tests conducted by ETRTO show that the wear rate of group ‘C1’ tyres can decrease by up to 50 percent, while the loss rate of group ‘C2’ and ‘C3’ tyres remain in 10 percent. The new regulation R117-04 therefore does not apply to group ‘C2’ and ‘C3’ tyres, as they normally have a greater tread depth and it is assumed that the level of wet braking does not change during the wear phase. However, since group ‘C1’ tyres have a smaller tread depth, it is assumed that their contact patch is more subject to negative changes, so that the wet braking performance also changes more after use.
As a weak point of R117-04 regulation, it only covers wet braking of new and worn-out tyres. It does not cover ‘noise’ and ‘rolling resistance’ items given on labelling or more simply endurance performance level of especially cheap tyres in the market with a 1.6 mm tread depth assuming they will not change!
The new R117-04 regulation may mainly be considered as sustainability issue rather than total safety. It promotes tyre usage until defined min tread depth creating a room to consumers to trust the tyres above minimum tread depth level. However, it should still be positively considered a step forward to the worn tyres’ safety regulation. It accepts that wet braking level of worn tyres are more critical and important safety issue and should be regulated. By the way, consumers may use their tyres in longer stage, giving a contribution to a greener world.
The transparency provided by the new regulation, which came into force on 2024 July, is even more essential, as some performances deteriorate over time, especially in terms of safety. R117-04 in this term guarantees enhanced safety, better respect for the environment and the protection of motorists’ purchasing power.
Common consumer behaviour shows that 50 percent of car tyres are demounted before reaching a residual depth of 3 mm and replaced with a new set of tyres.
Michelin has studied the safety margin of used tyres since 2018 and has stressed the importance of tyres to be used until 1.6 mm remaining tread depth. The best way was to test worn tyres because it can easily reflect the real risks a driver can face on the road. During the study, the results were surprisingly varied. It was shown that some worn tyres performed better than new tyres when braking on wet roads. This was exactly what Michelin has been saying for a long time. The performance of different tyre brands also varies considerably.
Common consumer behaviour shows that 50 percent of car tyres are demounted before reaching a residual depth of 3 mm and replaced with a new set. In global scale, this makes around 400 million tyres are prematurely scraped every year. A quarter of this amount, or almost 100 million tyres, would save at least 6 million tonnes of CO2 instead of reproducing it. The implementation of this regulation will certainly have an impact on the demand for new tyres in Europe.
R117-04 presently focus mainly on only tread depth attribute, while aspects such as ageing or rubber structural integrity degradation remain outside the scope of this amendment.
In addition, in the hope that higher performance requirements will not result in higher costs for consumers, the changes are designed to encourage consumers to continue using sustainable tyres instead. Once drivers are confident in their tyres, they will drive to a tread depth of 1.6 mm, potentially saving EUR 6 billion a year by not complying with proposals to reduce tread depth to less than 3 mm.
R117-04 presently focuses mainly on tread depth attribute, while aspects such as ageing or rubber structural integrity degradation remain outside the scope of this amendment. We also mentioned some additional weak points above. However, imposing these standards, will increase the driver’s awareness for worn tyres performance limits and let them to make more informed decisions when purchasing tyres.
On the other hand, understanding the ‘NEW AND WORN PHASE TESTS CONCEPT’ will become the standard mentality of the customer, who will be able to assess the attitude towards the initial performance of the tyres, which may change over time, but should not! The new challenge will be to weed out products that are not gripping in the wet when worn and have not met these expectations for years..!
JK Tyre Targets Double-Digit Growth in FY2026, Targets INR 10 Billion CAPEX
- By Nilesh Wadhwa
- August 08, 2025
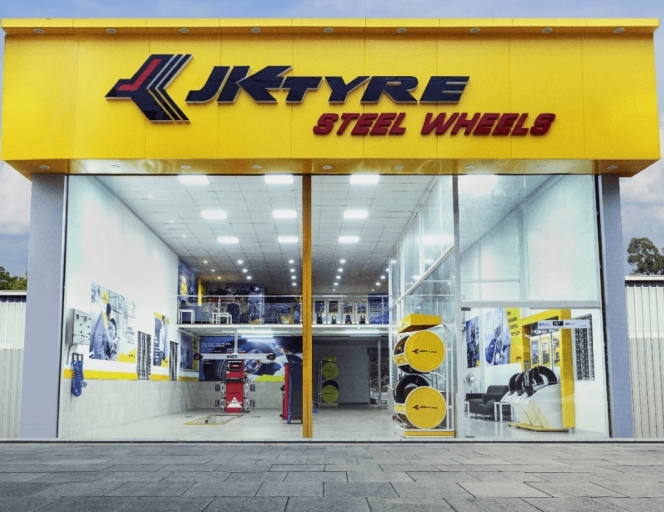
JK Tyre & Industries is aiming for double-digit revenue growth in FY2026, outpacing its forecast for single-digit expansion across the broader tyre industry. Managing Director Anshuman Singhania outlined the company’s ambitions during a post-earnings media call, underscoring confidence in demand recovery and strategic market positioning.
Q1 Performance Overview
For the first quarter of FY2026, JK Tyre reported revenue of INR 38.91 billion, with EBITDA at INR 4.24 billion, translating to a margin of 10 percent. Net profit stood at ₹1.55 billion — up 51 percent compared with the previous quarter, but down 21 percent YoY.
Singhania attributed the annual decline to muted original equipment (OE) demand, particularly in truck and bus radial (TBR) volumes, alongside higher raw material costs compared to the same period last year. He also highlighted an adverse impact from the company’s Tornel business in Mexico, which faced uncertainty due to tariffs on exports from Mexico to the United States, dampening volumes.
Resilience in Domestic and Export Markets
Dr Raghupati Singhania, Chairman and Managing Director, JK Tyre & Industries, said, “The growth momentum in domestic markets remained robust in Q1, with JK Tyre clocking a sales growth of 11 percent YoY, as contributed by a steady demand for our products in both replacement as well as OE segments, underscoring JK Tyre’s continued focus on core growth drivers and strengthening market presence.”
“Despite a challenging and uncertain macro-economic environment, exports of passenger car tyres witnessed a strong traction both on QoQ and YoY basis, signifying pull for our products and enhanced brand perception in the global markets,” said Dr Singhania.
Operational efficiencies and strategic pricing supported performance, even as natural rubber prices remained elevated. Subsidiaries Cavendish (India) and Tornel (Mexico) continued to contribute significantly to the group’s consolidated financials.
Operational efficiencies and strategic pricing supported performance, even as natural rubber prices remained elevated. Subsidiaries Cavendish (India) and Tornel (Mexico) continued to contribute significantly to the group’s consolidated financials.
Regarding trade tensions between India and the US, Anshuman Singhania noted that exports from India to the US account for only around 3 percent of JK Tyre’s revenue and could be redirected to markets such as Mexico, Latin America, Brazil and the UAE if required. With zero tariffs in Mexico, JK Tyre can utilise its production base there to meet demand for both passenger and truck radials. The EU and UK, where JK Tyre holds a strong position in the TBR segment, also remain tariff-free.
Capacity expansion
The company’s INR 14 billion capital expenditure plan is progressing on schedule, covering passenger car radial (PCR), TBR and all-steel truck radial projects. For the year, investment is expected to total INR 9-10 billion, aimed at boosting production capacity by 30-40 percent.
A key driver for future profitability is the shift towards premium products. The share of 16-inch and above passenger car tyres in JK Tyre’s portfolio has grown from 18 percent in FY2020 to 25 percent in FY2025, with a target of 40-45 percent over the next two to three years. This change is being fuelled by rising SUV sales, larger rim sizes in entry-level cars and strong export demand.
The company has also developed a complete range of tyres for electric vehicles, spanning commercial truck radials, bus tyres, passenger radials and two/three-wheeler tyres Major OEMs such as Ashok Leyland’s Switch Mobility and Tata Motors are sourcing these products, including for last-mile connectivity vehicles and newly launched EV buses.
Market Outlook
The replacement market has been a bright spot, with passenger radial volumes up 32 percent year-on-year and truck radial volumes growing in the high single digits. JK Tyre expects demand to strengthen in the second half of FY2026, supported by infrastructure development, a favourable monsoon, potential interest rate cuts, and improved consumer liquidity.
Anshuman Singhania stressed that the worst of raw material price pressures appear to be over, paving the way for margin improvement as the product mix shifts and capacity utilisation rises. With the small car segment’s gradual decline offset by growth in premium categories, JK Tyre remains confident in sustaining momentum.
“Overall, India is poised for growth,” Singhania concluded. “We see positives across the board — from infrastructure push to evolving consumer preferences — and we are well-positioned to capitalise on these trends.”
Yokohama Rubber begins OE tyre supply for BYD’s SEALION 6 DM-i SUV in China
- By TT News
- August 07, 2025
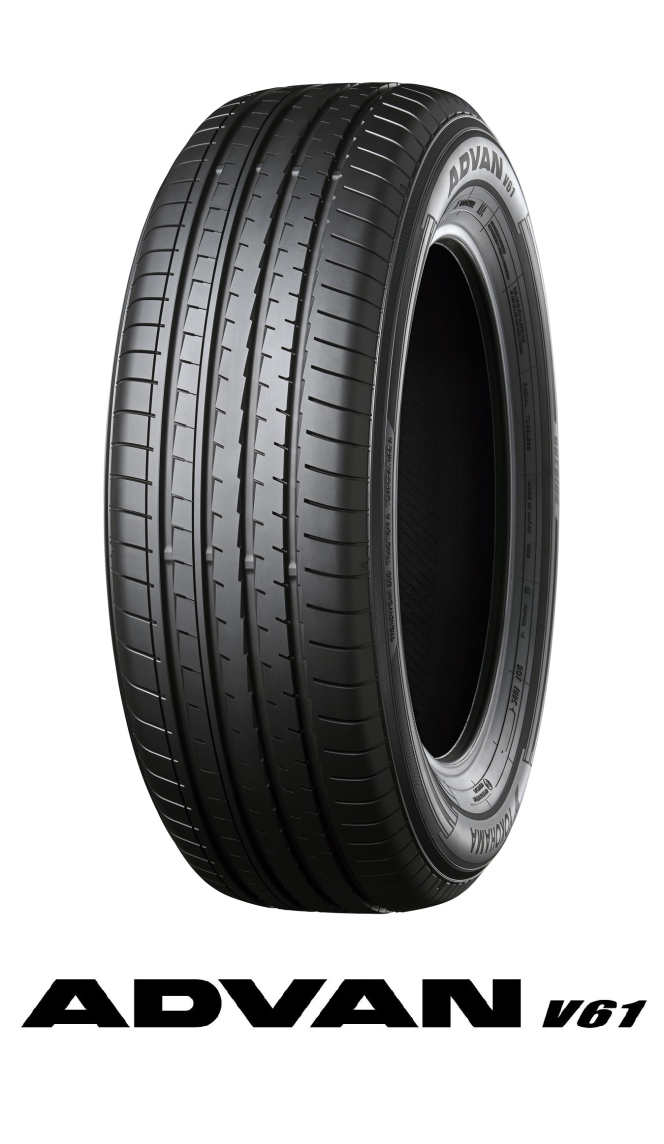
Yokohama Rubber has begun supplying its ADVAN V61 tyres as original equipment for BYD’s new SEALION 6 DM-i SUV, marking the Japanese manufacturer’s first OE partnership with the Chinese carmaker.
The SEALION 6 DM-i, a plug-in hybrid SUV launched by BYD Company Ltd. this July, is being factory-fitted with 235/50R19 103V size ADVAN V61 tyres. The announcement comes as Yokohama seeks to grow its footprint in China’s fast-evolving electric and hybrid vehicle market.
The ADVAN V61 is part of Yokohama’s global flagship ADVAN range and is positioned as a premium SUV tyre. The company said the tyre “offers ADVAN’s hallmark premium-grade driving performance, along with a high-level balance of fuel and energy efficiency, handling stability, and quietness, achieving both comfortable city driving and long-distance touring for heavyweight SUVs.”
The SEALION 6 DM-i combines a 1.5-litre naturally aspirated petrol engine producing up to 74kW with an electric motor generating 160kW. Buyers can choose between 18.3 kWh and 26.6 kWh blade battery options, offering electric driving ranges of 93km and 130km, respectively. All models come equipped with advanced driver assistance systems as standard, and the exterior design draws inspiration from the concept of “ocean aesthetics.”
Sumitomo Rubber’s Tyre Unit Clears Japan Antitrust Probe With Commitment Plan
- By TT News
- August 07, 2025
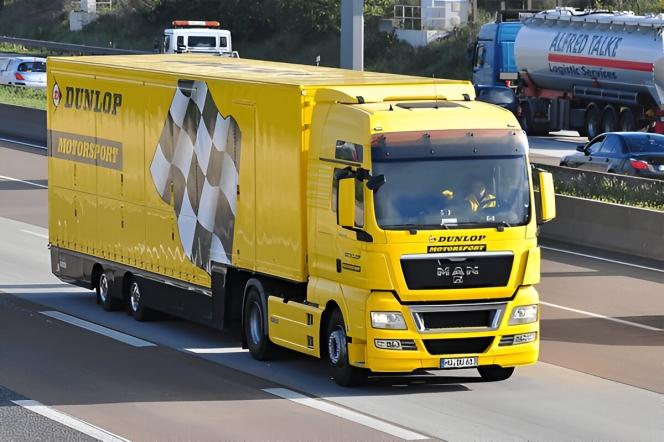
Sumitomo Rubber Industries Ltd said its subsidiary Dunlop Tyre Japan Ltd has completed a Japan Fair Trade Commission investigation into automotive all-season tyre sales after the regulator approved a commitment plan submitted by the unit.
The probe, which examined the subsidiary’s sales practices, concluded without the commission identifying any violation of Japan’s Antimonopoly Act, Sumitomo Rubber said in a statement.
Under Japan’s commitment procedures, companies can submit plans to address potential competition concerns without admitting wrongdoing, allowing them to resolve investigations while avoiding formal sanctions.
"We deeply apologise for the great trouble and anxiety that we have caused to all concerned, including our clients and business partners,” the tyre maker said.
Bekaert Warns Of Weakening Demand As Tariffs And FX Weigh On Outlook
- By TT News
- August 04, 2025
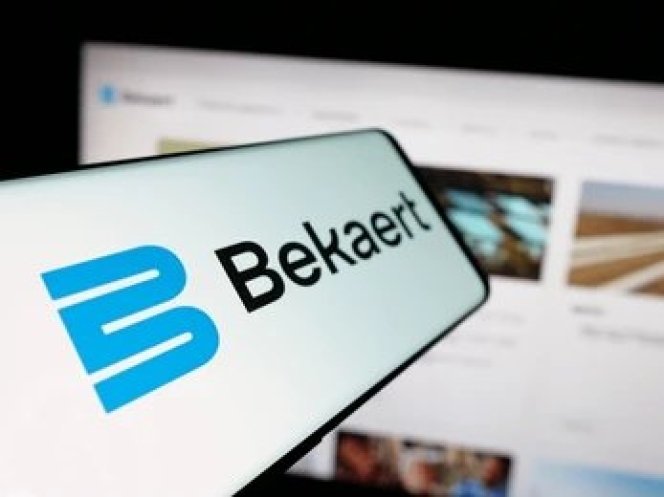
Belgian steel wire maker Bekaert reported resilient first-half 2025 earnings as strong cash generation and cost control offset softer sales, but warned that tariffs and currency pressures are weighing on demand.
The company posted consolidated sales of €1.9 billion, down 5.2 percent year-on-year, with volumes declining 2.6 percent and price/mix effects stripping out a further 2.2 percent. Underlying EBIT slipped 16.2 percent to €171 million, delivering a margin of 8.8 percent compared with 9.9 percent a year earlier.
Free cash flow surged to €123 million from €43 million in the prior-year period, driven by a €135 million reduction in working capital and €21 million in cost savings as the company continued to streamline operations and rein in capex. Net debt fell to €327 million from €399 million despite a continuing €200 million share buyback programme, €74 million of which has been completed.
“We have continued to focus on what we can control best – cash flow and costs - and have significantly reduced overheads and working capital in H1 2025,” chief executive Yves Kerstens said. “Equally, I am very pleased with the hard work of our teams fighting for volumes in the current challenging markets.”
He added: “We are also taking further steps to make our business units more autonomous and agile. Therefore, I am very confident that we will come out of the current business environment stronger and more cost competitive than ever before.”
Bekaert said volumes were particularly strong in its Steel Wire Solutions and Rubber Reinforcement divisions in the United States and China, while European and Latin American demand lagged. Its Brazilian joint ventures delivered €24 million in net profit share, up from €20 million a year ago.
However, the group cautioned that growing trade tensions – including a rise in US steel tariffs from 25 percent to 50 percent – and the weakening of the US dollar and Chinese yuan against the euro were eroding pricing power and softening orders.
“Following a period of resilience in Q2, the tariff uncertainty and weakening economic outlook has started to have an impact on demand,” Bekaert said.
The company now expects slightly lower full-year 2025 sales on a like-for-like basis, with an underlying EBIT margin of between 8.0 percent and 8.5 percent, down from 8.8 percent in the first half.
Comments (0)
ADD COMMENT