Orion SA Names Natalia Scherbakoff, Chief Technology Officer
- By TT News
- October 18, 2024
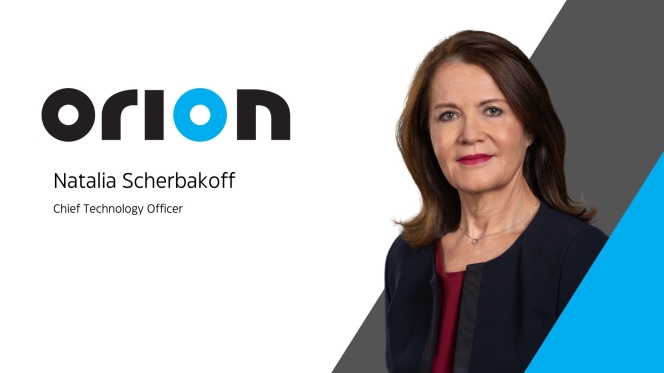
Orion, a global speciality chemicals manufacturer, appointed Natalia Scherbakoff as chief technology officer, effective immediately.
Scherbakoff succeeds David Deters, who led Orion’s innovation efforts for nearly a decade. Deters will remain with the company through year-end to ensure a smooth transition.
Based at Orion’s main innovation hub in Cologne, Germany, Scherbakoff will oversee the company’s technical centres in China, South Korea and the U.S. She will focus on further developing Orion’s innovation capabilities, including leveraging its new Battery Innovation Centre in Cologne.
Additionally, Scherbakoff will lead a €12.8 million project, partially funded by the German government and European Union, to develop and demonstrate a climate-neutral process for producing carbon black from alternative carbon sources. This technology aims to improve Orion’s yield and production efficiency using circular feedstocks.
“Natalia has broad global experience, a track record of moving ideas through the development process to successful product launches, and commercial savvy. She combines strong people skills with a passion for driving innovation and achieving tangible outcomes,” Orion CEO Corning Painter said. “She is arriving at an exciting time here at Orion, and I am looking forward to her building on the success we have had under David’s leadership in batteries, circular products, coatings, and other customer applications.”
Scherbakoff joins Orion from Trinseo, a speciality materials company, where she served as vice president of technology and innovation. She oversaw global research, development, and technology innovation in that role, focusing on sustainability and circular solutions. Additionally, she supported key growth initiatives and mergers and acquisitions while serving on Trinseo’s Corporate Environmental, Social and Governance Council.
Scherbakoff brings a wealth of experience across diverse industries. Prior to Trinseo, she held leadership positions at Plastic Omnium (now OPmobility), a French automotive supplier; Owens Corning, a building materials manufacturer; and Clayens NP, a speciality materials producer, where she currently serves as a non-executive board member. She is also a member of the Forbes Technology Council.
JK Tyre Targets Double-Digit Growth in FY2026, Targets INR 10 Billion CAPEX
- By Nilesh Wadhwa
- August 08, 2025
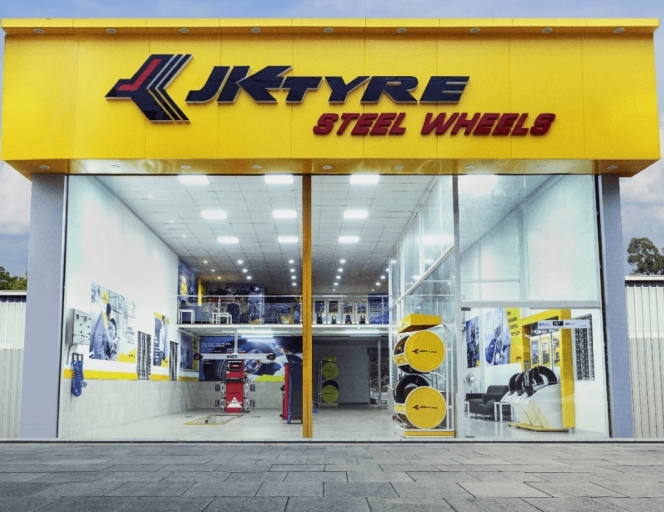
JK Tyre & Industries is aiming for double-digit revenue growth in FY2026, outpacing its forecast for single-digit expansion across the broader tyre industry. Managing Director Anshuman Singhania outlined the company’s ambitions during a post-earnings media call, underscoring confidence in demand recovery and strategic market positioning.
Q1 Performance Overview
For the first quarter of FY2026, JK Tyre reported revenue of INR 38.91 billion, with EBITDA at INR 4.24 billion, translating to a margin of 10 percent. Net profit stood at ₹1.55 billion — up 51 percent compared with the previous quarter, but down 21 percent YoY.
Singhania attributed the annual decline to muted original equipment (OE) demand, particularly in truck and bus radial (TBR) volumes, alongside higher raw material costs compared to the same period last year. He also highlighted an adverse impact from the company’s Tornel business in Mexico, which faced uncertainty due to tariffs on exports from Mexico to the United States, dampening volumes.
Resilience in Domestic and Export Markets
Dr Raghupati Singhania, Chairman and Managing Director, JK Tyre & Industries, said, “The growth momentum in domestic markets remained robust in Q1, with JK Tyre clocking a sales growth of 11 percent YoY, as contributed by a steady demand for our products in both replacement as well as OE segments, underscoring JK Tyre’s continued focus on core growth drivers and strengthening market presence.”
“Despite a challenging and uncertain macro-economic environment, exports of passenger car tyres witnessed a strong traction both on QoQ and YoY basis, signifying pull for our products and enhanced brand perception in the global markets,” said Dr Singhania.
Operational efficiencies and strategic pricing supported performance, even as natural rubber prices remained elevated. Subsidiaries Cavendish (India) and Tornel (Mexico) continued to contribute significantly to the group’s consolidated financials.
Operational efficiencies and strategic pricing supported performance, even as natural rubber prices remained elevated. Subsidiaries Cavendish (India) and Tornel (Mexico) continued to contribute significantly to the group’s consolidated financials.
Regarding trade tensions between India and the US, Anshuman Singhania noted that exports from India to the US account for only around 3 percent of JK Tyre’s revenue and could be redirected to markets such as Mexico, Latin America, Brazil and the UAE if required. With zero tariffs in Mexico, JK Tyre can utilise its production base there to meet demand for both passenger and truck radials. The EU and UK, where JK Tyre holds a strong position in the TBR segment, also remain tariff-free.
Capacity expansion
The company’s INR 14 billion capital expenditure plan is progressing on schedule, covering passenger car radial (PCR), TBR and all-steel truck radial projects. For the year, investment is expected to total INR 9-10 billion, aimed at boosting production capacity by 30-40 percent.
A key driver for future profitability is the shift towards premium products. The share of 16-inch and above passenger car tyres in JK Tyre’s portfolio has grown from 18 percent in FY2020 to 25 percent in FY2025, with a target of 40-45 percent over the next two to three years. This change is being fuelled by rising SUV sales, larger rim sizes in entry-level cars and strong export demand.
The company has also developed a complete range of tyres for electric vehicles, spanning commercial truck radials, bus tyres, passenger radials and two/three-wheeler tyres Major OEMs such as Ashok Leyland’s Switch Mobility and Tata Motors are sourcing these products, including for last-mile connectivity vehicles and newly launched EV buses.
Market Outlook
The replacement market has been a bright spot, with passenger radial volumes up 32 percent year-on-year and truck radial volumes growing in the high single digits. JK Tyre expects demand to strengthen in the second half of FY2026, supported by infrastructure development, a favourable monsoon, potential interest rate cuts, and improved consumer liquidity.
Anshuman Singhania stressed that the worst of raw material price pressures appear to be over, paving the way for margin improvement as the product mix shifts and capacity utilisation rises. With the small car segment’s gradual decline offset by growth in premium categories, JK Tyre remains confident in sustaining momentum.
“Overall, India is poised for growth,” Singhania concluded. “We see positives across the board — from infrastructure push to evolving consumer preferences — and we are well-positioned to capitalise on these trends.”
Yokohama Rubber begins OE tyre supply for BYD’s SEALION 6 DM-i SUV in China
- By TT News
- August 07, 2025
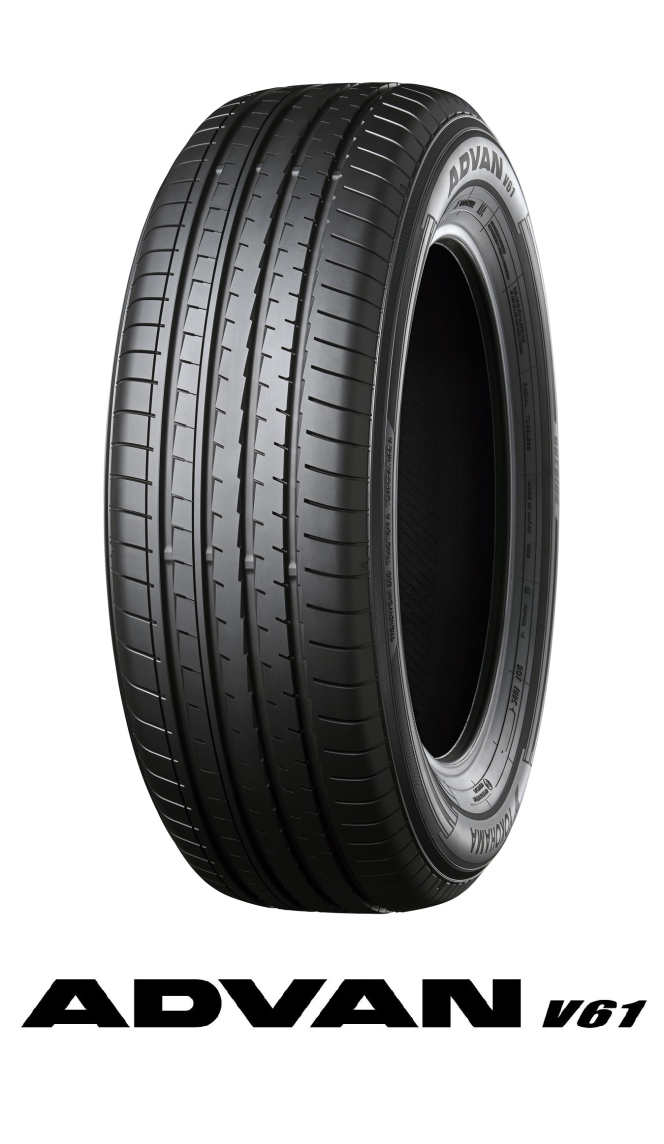
Yokohama Rubber has begun supplying its ADVAN V61 tyres as original equipment for BYD’s new SEALION 6 DM-i SUV, marking the Japanese manufacturer’s first OE partnership with the Chinese carmaker.
The SEALION 6 DM-i, a plug-in hybrid SUV launched by BYD Company Ltd. this July, is being factory-fitted with 235/50R19 103V size ADVAN V61 tyres. The announcement comes as Yokohama seeks to grow its footprint in China’s fast-evolving electric and hybrid vehicle market.
The ADVAN V61 is part of Yokohama’s global flagship ADVAN range and is positioned as a premium SUV tyre. The company said the tyre “offers ADVAN’s hallmark premium-grade driving performance, along with a high-level balance of fuel and energy efficiency, handling stability, and quietness, achieving both comfortable city driving and long-distance touring for heavyweight SUVs.”
The SEALION 6 DM-i combines a 1.5-litre naturally aspirated petrol engine producing up to 74kW with an electric motor generating 160kW. Buyers can choose between 18.3 kWh and 26.6 kWh blade battery options, offering electric driving ranges of 93km and 130km, respectively. All models come equipped with advanced driver assistance systems as standard, and the exterior design draws inspiration from the concept of “ocean aesthetics.”
Sumitomo Rubber’s Tyre Unit Clears Japan Antitrust Probe With Commitment Plan
- By TT News
- August 07, 2025
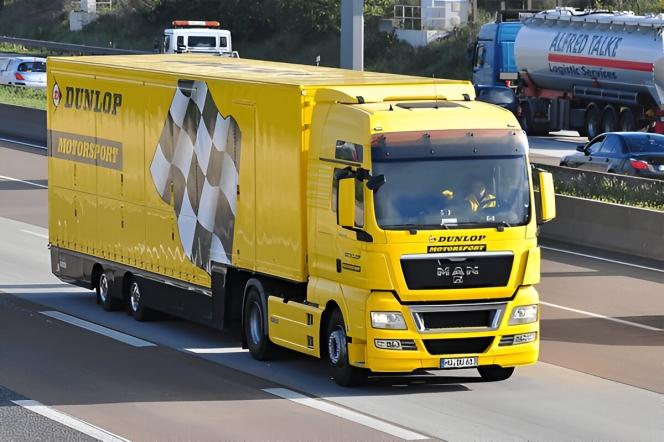
Sumitomo Rubber Industries Ltd said its subsidiary Dunlop Tyre Japan Ltd has completed a Japan Fair Trade Commission investigation into automotive all-season tyre sales after the regulator approved a commitment plan submitted by the unit.
The probe, which examined the subsidiary’s sales practices, concluded without the commission identifying any violation of Japan’s Antimonopoly Act, Sumitomo Rubber said in a statement.
Under Japan’s commitment procedures, companies can submit plans to address potential competition concerns without admitting wrongdoing, allowing them to resolve investigations while avoiding formal sanctions.
"We deeply apologise for the great trouble and anxiety that we have caused to all concerned, including our clients and business partners,” the tyre maker said.
Bekaert Warns Of Weakening Demand As Tariffs And FX Weigh On Outlook
- By TT News
- August 04, 2025
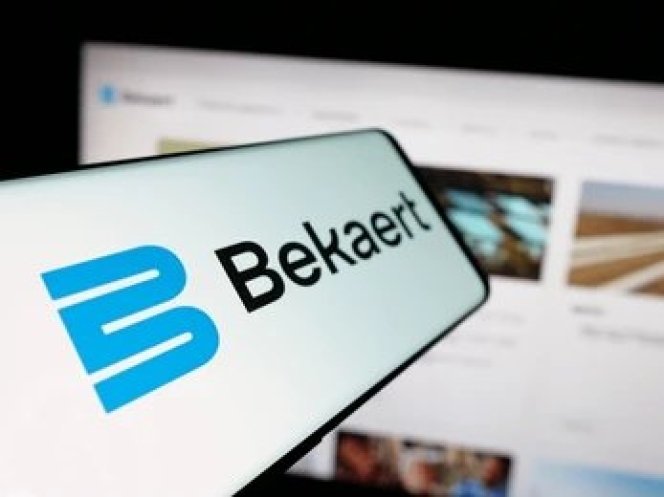
Belgian steel wire maker Bekaert reported resilient first-half 2025 earnings as strong cash generation and cost control offset softer sales, but warned that tariffs and currency pressures are weighing on demand.
The company posted consolidated sales of €1.9 billion, down 5.2 percent year-on-year, with volumes declining 2.6 percent and price/mix effects stripping out a further 2.2 percent. Underlying EBIT slipped 16.2 percent to €171 million, delivering a margin of 8.8 percent compared with 9.9 percent a year earlier.
Free cash flow surged to €123 million from €43 million in the prior-year period, driven by a €135 million reduction in working capital and €21 million in cost savings as the company continued to streamline operations and rein in capex. Net debt fell to €327 million from €399 million despite a continuing €200 million share buyback programme, €74 million of which has been completed.
“We have continued to focus on what we can control best – cash flow and costs - and have significantly reduced overheads and working capital in H1 2025,” chief executive Yves Kerstens said. “Equally, I am very pleased with the hard work of our teams fighting for volumes in the current challenging markets.”
He added: “We are also taking further steps to make our business units more autonomous and agile. Therefore, I am very confident that we will come out of the current business environment stronger and more cost competitive than ever before.”
Bekaert said volumes were particularly strong in its Steel Wire Solutions and Rubber Reinforcement divisions in the United States and China, while European and Latin American demand lagged. Its Brazilian joint ventures delivered €24 million in net profit share, up from €20 million a year ago.
However, the group cautioned that growing trade tensions – including a rise in US steel tariffs from 25 percent to 50 percent – and the weakening of the US dollar and Chinese yuan against the euro were eroding pricing power and softening orders.
“Following a period of resilience in Q2, the tariff uncertainty and weakening economic outlook has started to have an impact on demand,” Bekaert said.
The company now expects slightly lower full-year 2025 sales on a like-for-like basis, with an underlying EBIT margin of between 8.0 percent and 8.5 percent, down from 8.8 percent in the first half.
Comments (0)
ADD COMMENT