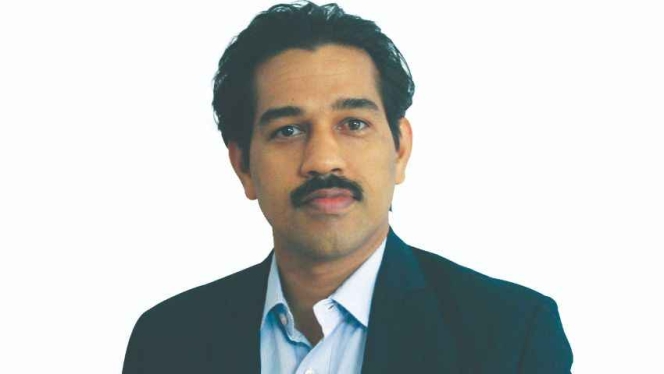
When we discuss about a motorcycle's performance, we generally speak about its engine power, torque, top speed, how fast it can accelerate, vehicle sound etc. Nevertheless, all these are meaningless if a driver cannot control the machine and/or is not comfortable while riding. There comes the importance of tyres. Tyres are the most crucial parts of a vehicle suspension system. Tyres are the only component in a motorcycle that constantly stays in contact with the road. The part of tread which is in contact with road surface is called ‘contact patch’ & Is about half the size of a post card. The overall suspension system (including tyres) ensures the right contact between the tires and the road surface at every stage of driving, thereby ensuring stability and good handling of the vehicle.
As tyres are the only contact with the road, they are responsible for multiple functions, such as –
Transfer the engine power to the road- meeting the demands of acceleration and braking
Provides right hold (grip) on different surfaces like dry, wet, snow, loose soils etc.
Helps the rider to steer the vehicle by responding to the handle movements
Carry the weight of the vehicle & rider
Ensuring the comfort of the rider by absorbing and dampening shock
Apart from the above aspects, tyres play a vital role in vehicle aesthetics, safety, fuel efficiency etc. These and several other challenges make Motorcycle tyre design a very interesting and responsible subject.
Apart from being a crucial part of a vehicle suspension system, tyres are the only contact between vehicle & road. Motorcycle vehicle dynamics and control characteristics are highly influenced by the tyre design. It is therefore highly imperative for a vehicle chase/suspension designer & tyre designer to work together in tandem. This will ensure that the part designs will complement each other and deliver the characteristic target performance of a motorcycle. A robust interaction mechanism between the R&Ds of OEM [Original Equipment Manufactures] and tyre manufactures is a growing necessity to cater to the ever‐increasing demands of performance entrusted upon the tyre of today. In case of tyres getting designed exclusively for aftermarket, a tyre designer work closely with the vehicle dynamics team to ensure that the retrofit design delivers desired target performance of the vehicle
Some of the major steps involved in motorcycle tyre design are
Product planning & Tyre “Size” finalization: During this stage a vehicle designer & tyre designer jointly review the vehicle performance requirements and decides the parameters specific to tyre performance. This includes:
Defying the application /terrine: Depending on application, 2 wheelers maybe broadly classified as Sport, Cruiser, Choppers, Touring, scooter, Step through, Sport touring, Enduro etc. Different OEM’s follow different terminologies, but a for a tyre designer to understand the final use by the user is of utmost importance. Demands from a tyre varies with each vehicle category, for example, for a cruiser the tyre is designed to be robust so as to hold up the weight of such heavy bikes and deliver long tyre life, whereas for a Sport touring /super sport bike, tyres are designed to deliver quick and precise handling with superior grip. These tires are lighter and made by using softer compounds for Superior grip.
Selection of Bias /Bias belted / Radial: At this juncture, I am not going to delve deeper into a detailed comparison of these constructions – however, it is important to acknowledge that both these construction types have their respective advantages and disadvantages. Each of these constructions has few specific applications where one performs better than the other. The selection of construction type mainly depends on vehicle category (application), vehicle Speed, load on the tyre, stability requirements, handling requirements, etc. for example Bias tyres are used in medium speed but heavy weight vehicles owing to their sturdy sidewalls, whereas Radial tyres are the ideal choice for high speed , vehicles because of their superior dimensional stability.
Selection of Tube type Vs Tubeless: Functionally both types of tyres have a proven track record for almost all applications. Hence this choice mainly depends on vehicle Rim design, which is decided by the overall aesthetic demand & application of the motorcycle.For high speed application, tubeless is always preferred
Finalizing the Tyre size / Tyre Geometry: In general, we may call it as tyre “size” – which includes tyre width, tyre diameter, rim diameter etc. Tyre geometry affects the vehicle dynamics like caster, trail, vehicle Center of gravity [CoG], etc. It also influences the area of contact between vehicle and road surface under different riding conditions & load-carrying capacity of the tyres. Furthermore, tyre size significantly influences vehicle aesthetic as well. Tyre “size” and vehicle rim size are always interconnected. Decision on one influence the decision on the other. Usually motorcycles have different front and rear tyre sizes depending on vehicle geometry & load distribution. Tyre “sizes” are decided considering all these parameters & the designers ensures that it follows the standards’ guidelines applicable in target countries.
Tyre tread profile design:
Contrary to the passenger car tyre designs which have almost flat tread surface, motorcycle tires have a U-shaped profile and a contact patch that changes size and shape during cornering. There is a major difference in the way lateral force is built up in passenger car and two wheelers. In case of passenger car, mechanism of lateral force builds up is due to slip angle whereas in two-wheeler it is mainly because of the camber or the leaning of the vehicle. Hence you see a flat tread area for passenger car tyre and U-shaped profile for Motorcycle tyre
This U-shaped profile is an important design factor having a direct influence on vehicle performances such as drivability (handling) durability, ride comfort, noise and wear resistance etc.
These tread contours are designed as the arc of one radius, or a combination of arcs with two or more radii. These profiles ensure the required contact patch availability at different lean angles & are controlled by the lean characteristic of the vehicles. It is very critical to balance the performance of front tyre & rear tyre of s motorcycle for precise handling of the vehicle. The contour designs play an important role in front /Rear tyre balance.
Tyre tread pattern design:
Patterns are molded in the tread area of tyre by repeated arrangement of ‘Groves’ or ‘Blocks’ & are generally referred to as “tread pattern”.
Significance of tread pattern:
Tread pattern plays a vital role in tyre performance such as:
Optimizing the traction on the riding surface
Eliminating aquaplaning
Optimizing the” Wear” of tread area·
Ensuring the continuity of tyre performance at different wear Stages [ wear %] of tyre.
Rolling resistance of the tyre
Noise generation
roviding a measurable clue to the owner on time for removal /suitability for continuous usage. etc.
Tread patterns not only helps in achieving the target performance, but also impart unique look to tyres and enhance aesthetics
Tyre patterns are broadly classified into 4 Major headings
- Rib patterns
- Directional
- Block [ Knobby]
- Slick tyres [Pattern less]
Selection of which group of patterns is mainly controlled by the terrain of application, e.g. Directional patterns are preferred in paved roads and knobby pattern ae mainly used on off-road applications. Pattern less tyres are normally used in racing track applications to provide maximum traction. Vehicles are designed to work in a combination of different terrains – similarly, tread patterns also have subgroups– which are optimized to operate in different combination of terrains. E.g. Semi knobby patterns for on – off allocations, High land – minimum grove patterns for Supersport highway applications etc.
Designer alter the direction of the grove, depth of the grove, number of groves, the ratio between Grove area & non grove area [ Land- sea ratio] , shape of the grove, the width of the grove etc. to optimize the performance of tread pattern. These patterns are designed to perform under different dynamic conditions. Nowadays designers seek the help of computer-aided simulations to predict the performance under different loading /riding conditions to optimize the pattern design.
Tyre as an Aesthetic component
The visual appeal of tyre is significant contributor in the overall aesthetics of a motorcycle. Hence in addition to performing all the functional requirements discussed so far, tyres ought to look good too.
The tread pattern should complement the overall styling language of a motorcycle. This attracts the attention of OEM’s vehicle styling studios towards tyre tread designs as well. In fact, most of the new tyre designs are done first at styling studio and then technically optimized by the tyre engineer to guarantee the functionality.
Material design
Tyre is a composite material made of different rubber compounds and reinforcing materials. Right compound and reinforcing material selection are crucial to achieve the target performance of tyre.
- Reinforcing materials:
Reinforcing materials provides the required strength and stiffness for tyre body [carcass]. This includes “tyre cords” used in tyre body ply & “bead wires” used in bead construction of tyres. Most used tyre cord materials are Nylon 6, Nylon 6-6, Polyester, Aramid, Rayon, Steel, etc.
These materials differ in their chemical composition, tensile strength, elongation properties, impact strength, temperature resistance, rubber adhesion, etc. Tyre engineer must choose the right tyre cords depending on the performance demands of the tyre like load carrying capacity, durability, impact resistance, drivability, speed of operations etc. Cost & availability also are few decisive parameters during selection of reinforcing materials.
Tyre Cord denier, cord style, EPI (Ends Per Inch), angle of cords and number of plies affect the strength of a tyre and are chosen based on engineering, and design criteria.
structural durability of a tyre is Primarily determined by the reinforcing material
- Rubber compound design
Each part of the tyre must dispense different functions and are thus designed with different rubber compounds like tread compound, sidewall compound, carcass compound, bead wire coat compound, etc. Though all these compounds have their own importance, but tread compound selection is the most critical, as it has a direct impact on tyre traction, handling, wear performance, durability, rolling resistance, etc.
-
- Trends of tread compound design:
Even though smaller number of components are used in a motorcycle tyre, than as compared with passenger car tyres, but performance challenges involved in compounding are far more complex considering less area of tyre in contact with road. 3 major performance requirements in motorcycle tread compound are (1) Grip (2) Rolling resistance [fuel efficiency] and (3) Tyre life which is generally referred as the magic triangle in tyre rubber compounding. This is due to the contradictory response of these 3 performance characteristics to rubber compounding approach. For example, improvement in Grip normally comes with an increase in rolling resistance with conventional compounding as both are related to energy loss. It is always a challenge for tyre compounder to improve all three performance requirements together and this calls for the incorporation of advanced polymers and fillers.
Performance priorities for tread compound changes based on operating terrain, type of vehicle, etc. e.g. Street two-wheeler tread compound designs primarily focus on high grip and high-speed capabilities, whereas an on-off application tyre require higher cut and chunk resistance tread compound.
Demand for lower rolling resistance tyre is showing a steady increase Year-on-Year. Major divers for this growing demand are Electric vehicle introduction & increased focus on vehicle fuel efficiency, in few segments. Tread compounds are expected to deliver lower rolling resistance, without compromising the Grip – typical “magic triangle” puzzle for any tyre compounding engineer. Tyre industry can address this challenge by usage of new generation materials like SSBR, functionalized SSBR, high molecular
Design for manufacturing
For success of any product – Design & manufacturing sync is a must. While designing, to accommodate all functional requirements, a designer cannot ignore the significance of manufacturing process. Hence every tyre design is optimized to satisfy both functional & manufacturability needs. This if not done properly may result in suboptimal performance of the product,
Product Performance Testing
It’s important to review and verify the product performance before releasing it into the market. There are a set of Indoor & Outdoor tests for performance review. A few of them are listed below,
Indoor tests: High-speed drum test, Endurance test, Rolling resistance test, Force and moment testing, Stiffness test, Footprint etc.
Outdoor tests: Ride and Handling testing (track, off-road, public road etc.], Braking test [wet, dry], tyre wear test etc.
Blend of Engineering & Art
Being an integral part of vehicle suspension system & only contact point with road, a tyre plays significant role in motorcycle performance [safety, drivability etc.]. In addition to these performance parameters, tyres have significant influence on the overall styling of the vehicle. It complements the primary theme of the vehicle. A right blend of engineering and art is essential for a successful tyre design. One cannot substitute the other. Amongst different steps of tyre design like, dimension finalization, tread design & martial design etc. the most critical step is tread design (profile, pattern & compound)
Few areas designers are focusing today to meet the near/middle future demands are
- Lowering the rolling resistance – without compromising grip
- Shortening the time to market.
- virtual simulation of tyre performance
References
- ‘’The pneumonic tyre’’, National Highway Traffic Safety Administration, Feb 2006
- T. French, Tyre Technology, Hilger, New York, 1989.
- Mechanics of Pneumatic Tires, S. K Clark, ed., University of Michigan, US Department of Transportation, National Highway Traffic Safety Administration, Washington, DC, 20590, 1891.
4. Handbook of vehicle-road interaction: vehicle dynamics, suspension design, and road damage / edited by David Cebon. p. cm. - (Advances in engineering), ISBN 9026515545
5. “Tyre and Vehicle Dynamics” , Hans B. Pacejka, Professor Emeritus Delft University of Technology, Consultant TNO Automotive Helmond
The author is General Manager - Product Development,2&3-Wheeler tyres, CEAT Tyres
NIRA Dynamics Partners BANF Smart Tire System For Advanced Vehicle Safety And Predictive Maintenance
- By TT News
- June 16, 2025
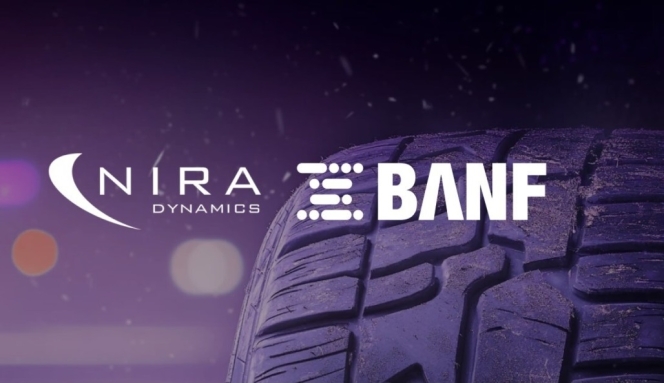
Swedish automotive software leader NIRA Dynamics AB and BANF Smart Tire System of South Korea have announced a new partnership aimed at significantly enhancing vehicle safety and predictive maintenance for commercial vehicles. The collaboration will see BANF integrate its high-frequency tyre sensors into NIRA's established software ecosystem.
This strategic alliance aims to disrupt Tyre Pressure Monitoring Systems (TPMS), providing commercial fleets and automakers with unprecedented real-time insights into tyre health and road safety. NIRA Dynamics, founded in 2001, is a global automotive software powerhouse with its technologies deployed in over 120 million vehicles worldwide, including an indirect TPMS (iTPMS) that has surpassed 110 million units sold.
Under the agreement, NIRA will incorporate BANF's triaxial tyre sensors into its Road Surface Information (RSI) and Wheel Safety Insights (WSI) platforms. These platforms already utilise existing vehicle sensor data and proprietary algorithms for functions like tyre grip estimation, tread wear analysis and loose wheel detection.
BANF's key innovation lies in its Smart Profiler system, which wirelessly powers internal tyre sensors directly from the vehicle battery, overcoming the challenge of continuous power and real-time data transmission from rotating tyres. This integration will significantly enhance NIRA's capabilities, particularly for monitoring commercial vehicle loads and dual-tyre setups, by providing sensor data at high sampling rates of 1kHz and 4kHz.
Otto Johansson, Head of Innovation at NIRA Dynamics, said, "This collaboration accelerates our vision of creating a comprehensive vehicle intelligence network. While our software solutions already process data from millions of vehicles, adding specialised hardware enables new use cases in predictive maintenance and ADAS applications."
NIRA's evolution from software-only tyre pressure monitoring to multi-layered safety systems is evident in its flagship Tyre Pressure Indicator (TPI) technology, which has eliminated the need for physical sensors in many applications, significantly reducing electronic waste. The company has also collaborated with automotive giants like Volkswagen Group on innovations such as Road Surface Alerts.
The partnership also addresses critical safety needs in commercial vehicles. NIRA's Loose Wheel Indicator (LWI), already deployed in Audi vehicles, will now be extended to heavy-duty vehicles through the BANF collaboration, aiming to mitigate the thousands of annual wheel detachment incidents reported.
For fleet operators, the integrated system promises substantial operational benefits. NIRA's Winter Road Insights product, which helps optimise road maintenance, combined with BANF's wear prediction algorithms, is expected to lead to reduced tyre replacement costs and improved fuel efficiency.
Ron Yoogun Lee, Head of Business Development, BANF, said, “Our goal is to enhance cost-effectiveness, save lives and preserve the environment by digitising tyres, which are the last analog domain in the mobility industry.”
Looking ahead, NIRA's technology roadmap includes developing ‘grip maps’ for SAE Level 2-3 autonomous vehicles and leveraging data from millions of vehicles to create AI models for predictive infrastructure maintenance, further solidifying its position at the forefront of automotive innovation.
Anyline Launches TireBuddy App to Streamline Tyre Inspections
- By TT News
- June 13, 2025
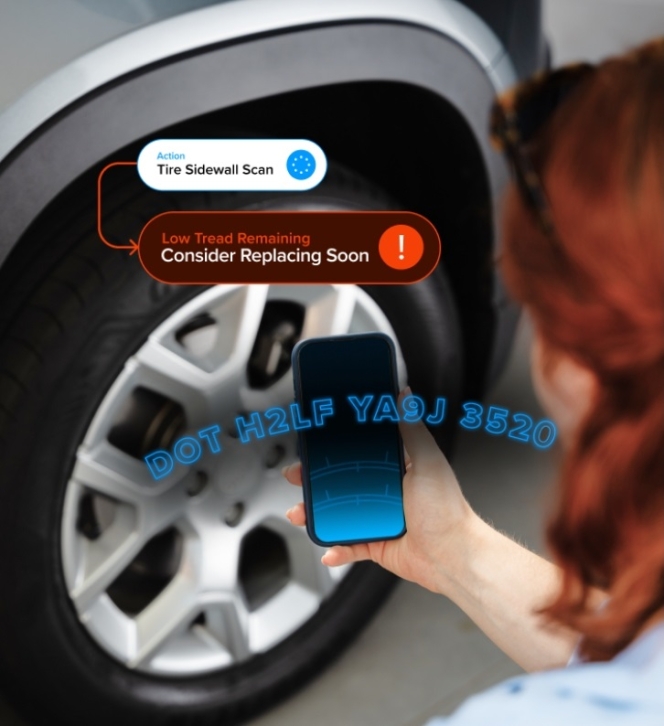
AI-powered mobile data capture company Anyline has launched TireBuddy, a smartphone-based app designed to modernise tyre inspections in automotive service bays. The app replaces traditional, manual inspection methods with a standardised digital workflow that delivers consistent, data-backed results and clear customer reports.
TireBuddy offers technicians tools to detect tread depth issues, tyre age, alignment concerns and sidewall damage using AI-powered analysis and visual reporting – without the need for additional hardware. Reports can be instantly shared in digital or printed formats, helping to reduce manual entry errors and increase customer trust.
The launch comes ahead of National Tire Safety Week (30 June 30 – 4 July), positioning the app as a timely solution for shops preparing for the summer travel season.
Lukas Kinigadner, Co-Chief Executive Officer, Anyline, said, “TireBuddy is not only about faster inspections — it’s about more trustworthy ones. We’re helping garages and service centres replace subjective tyre checks with data-backed insights and visual reporting that both technicians and customers can rely on.”
Frederic Baroin, Global Head of Automotive Business at Anyline, said, “TireBuddy empowers technicians with real-time, reliable data that strengthens recommendations and builds customer confidence. We designed it to deliver clarity, not complexity, in every inspection.”
By enhancing inspection accuracy and transparency, Anyline said TireBuddy can also drive higher service approvals and boost shop revenue.
CEAT Acquires India’s First Scania Heavy-Duty Truck to Boost Tyre Testing
- By TT News
- June 03, 2025
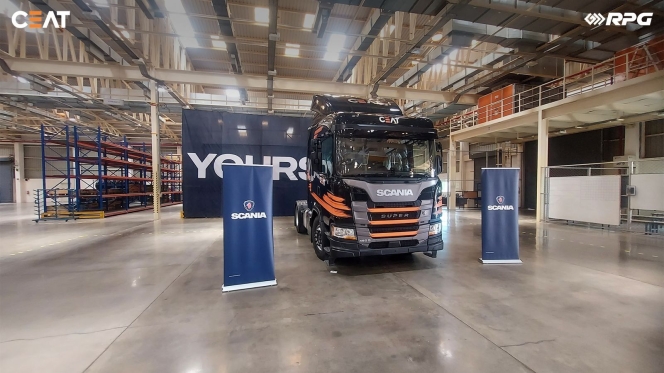
Indian tyre maker CEAT said it has purchased the country’s first Scania 460 G prime mover truck to strengthen its research and development operations as the company pushes to expand in overseas markets.
The Mumbai-based manufacturer described the acquisition as part of efforts to upgrade its commercial vehicle tyre testing capabilities to international standards, particularly for certification in Europe and the United States.
The Scania G460 produces 460 horsepower from its 12.7-litre engine and can handle a gross vehicle weight of 150,000 kilograms (330,693 pounds). The truck features Scania’s Super engine technology, which the Swedish manufacturer says improves fuel efficiency while cutting emissions.
CEAT officials stated that the new testing platform will help accelerate product development and reduce costs while meeting stricter global standards.
“This high-performance vehicle is not just a prime mover — it’s a strategic investment in our Commercial Vehicle Tyre Testing Infrastructure, aimed at elevating our research & development capabilities to meet global standards,” the company said in a statement.
The investment comes as Indian tyre companies grapple with volatile raw material prices while trying to capitalize on strong domestic demand from India’s growing automotive sector. Industry analysts say that manufacturers are under pressure to improve efficiency and expand internationally in order to maintain profitability.
CEAT joins other major Indian tyre makers in ramping up research capabilities as they compete for market share both domestically and abroad.
The company said the new truck will support vehicle dynamics testing and help reduce the time needed to bring new commercial tyre products to market.
Goodyear Drives into Software Defined Vehicle Market with SDVerse Partnership
- By TT News
- May 29, 2025
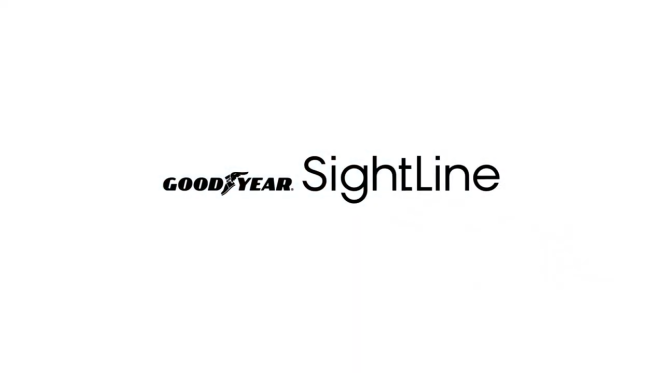
SDVerse, a leading B2B marketplace for vehicle software, has announced that global tyre major Goodyear will now promote its SightLine suite of tyre intelligence software offerings on the SDVerse platform.
This collaboration marks a significant move for Goodyear into the burgeoning software-defined vehicle (SDV) space, offering tyre-centric software solutions designed to boost vehicle performance, safety and efficiency.
Goodyear's intelligent mobility solutions, including real-time tyre health diagnostics, road surface sensing and predictive maintenance insights, are engineered to allow OEMs and Tier-1 suppliers to integrate tyre intelligence directly into a vehicle's core systems.
SDVerse will be the inaugural online marketplace to feature Goodyear's expansion from traditional hardware into the digital realm of mobility. This strategic shift by Goodyear reflects the industry's increasing focus on data-driven, connected platforms where every vehicle component contributes to a safer and more efficient driving experience.
Werner Happenhofer, Vice-President of Global Tire Intelligence & Solutions at Goodyear, said, "Our tyre intelligence technologies are at the core of our commitment to innovation. Integrating these technologies into a vehicle's control systems represents a significant step forward in enhancing vehicle safety, performance and efficiency. Partnering with SDVerse gives us the opportunity to collaborate with other members and OEMs as we meet the evolving demands of the industry."
For SDVerse, Goodyear's entry further solidifies its mission to revolutionise automotive software sourcing by connecting buyers and sellers, accelerating innovation and enabling software-defined mobility at scale.
Prashant Gulati, CEO, SDVerse, said, "We’re thrilled to welcome Goodyear to SDVerse. Goodyear’s move into software is not only bold but incredibly timely. Their presence on our platform underscores the breadth of what software-defined vehicles can become – where even tyres evolve into intelligent systems contributing real-time data and decision-making capabilities across the vehicle ecosystem."
Comments (0)
ADD COMMENT