Sumitomo Rubber Industries to Deploy Rockwell Automation MES Platform
- By TT News
- December 11, 2024
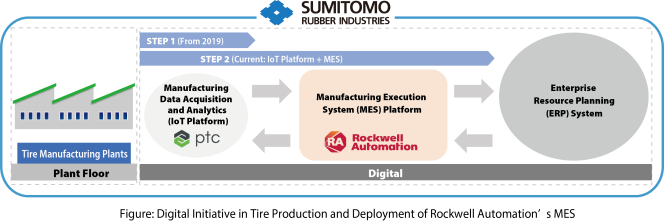
Sumitomo Rubber Industries has decided to deploy Rockwell Automation's manufacturing execution system (MES) platform at its largest domestic factory in Shirakawa City, Fukushima Prefecture, Japan.
The factory will begin operations using the new platform in the second half of 2025.
This move comes as part of the company’s efforts to promote the use of digital technology in tyre production, aiming to enhance and streamline factory operations globally.
Kenji Saito, Executive Officer, General Manager of Manufacturing HQ, Tyre Business HQ Sumitomo Rubber Industries, said, “We believe that leveraging Rockwell Automation’s expertise and flexibility, and our strong partnership with PTC to the maximum will enable us to standardise manufacturing management and enhance operational efficiency globally, driving our growth. To implement DX management as set out in our management vision, we intend to deploy the MES system beginning with the domestic factory and other manufacturing sites thereafter. We will continue to collaborate with Rockwell Automation, a global leader in manufacturing, and embrace new challenges with a forward-looking approach, making full use of AI.”
James Glasson, Vice President, Global Industry Auto, Tire and Advanced Mobility, Rockwell Automation, said, “This initiative will enhance operating efficiency, minimise manufacturing risks, reduce implementation costs and significantly accelerate speed to market.”
In recent years, the manufacturing industry has faced numerous challenges, including rapid changes in the business environment and labour shortages due to Japan’s declining working-age population. To address these challenges, Sumitomo Rubber Industries has been working with PTC since 2019 to adopt PTC’s IoT platform and develop applications to integrate data across production lines and manufacturing sites.
This system has been rolled out at nine of the company’s 11 tyre manufacturing sites, including all four factories in Japan.
The deployment of the Rockwell Automation MES platform will accelerate data organisation and enable the accumulation and sharing of valuable data such as quality and production forecasts across the company. By linking the collected and managed data with the enterprise resource planning (ERP) system, corporate management can gain a comprehensive view of manufacturing operations worldwide.
The Shirakawa Factory will begin operating the MES platform in the second half of 2025. After verifying its effectiveness by the end of 2026, Sumitomo Rubber Industries aims to standardise and roll out the platform to its factories in Japan and overseas.
BendPak Launches Ranger RB30T Hybrid Wheel Balancer For Truck And Bus Wheels
- By TT News
- August 07, 2025
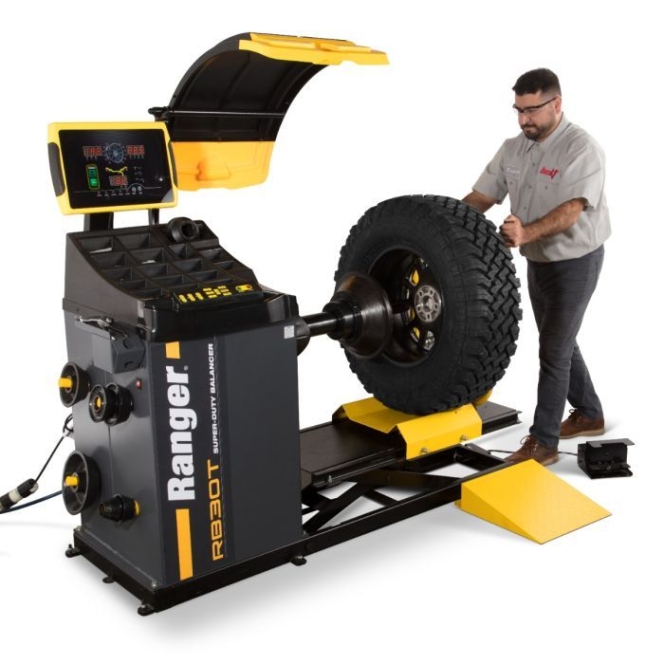
Designed to tackle the largest truck and bus wheels while maintaining precision for passenger vehicles, the RB30T Hybrid Wheel Balancer from Ranger (a BendPak division) delivers power and versatility. Switching between heavy-duty and light-duty applications is effortless, requiring just a button press. Its integrated pneumatic wheel lift enhances safety and ergonomics by minimising manual handling and reducing injury risks.
Capable of balancing wheels for buses, semi-trucks, OTR vehicles, light trucks and cars, the RB30T ensures fast, accurate results without recalibration. Its re-engineered platform supports wheels up to 330 lbs (approx. 150 kg), 49.25 inches in diameter and 20 inches wide, with rapid cycle times – seven seconds for car wheels and around 20 seconds for full truck assemblies. At its core, the Ranger Drive-Check system uses advanced 64-bit processing and quartz piezoelectric sensors to detect even the slightest imbalances across multiple axes. This smart technology simulates real-world driving conditions, identifying vibrations before they become road issues and automatically recommending optimal corrections.
Built for durability, the RB30T features a ribbed nylon-fibre drive belt, counter-weighted flywheel system and a three-phase motor with solid-state phase conversion for smooth, high-torque operation under heavy loads. The balancer comes ready to use with a commercial mounting kit, including cones and adapters, while its spacious top tray and side shelves keep wheel weights and tools organised for efficient workflow.
Available as a standalone unit or with the Ranger Select package – which includes professional installation and training – the RB30T is a robust solution for shops handling diverse wheel balancing needs.
Sean Price, Director of Product Development, said, “The new RB30T wheel balancer can do it all. Its versatility makes the RB30T a great choice not just for heavy-duty fleets and repair garages but also for high-volume tyre shops and mixed fleets.”
Bridgestone Launches First Aircraft Tyre Tracking System With Cebu Pacific
- By TT News
- August 04, 2025

Bridgestone has officially rolled out its proprietary aircraft tyre management system “easytrack” in collaboration with Cebu Pacific Air, marking the first deployment of the solution by a commercial airline.
The system, launched in April 2025, uses QR codes and a smartphone app to track aircraft tyres across the supply chain—replacing Cebu Pacific’s manual, paper-based process.
“As Cebu Pacific continues to expand its operations, it's essential that we invest in smart solutions that enhance efficiency and reduce manual workload,” said Shevantha Weerasekera, Vice President, Engineering & Fleet Management at Cebu Pacific. “Partnering with Bridgestone to implement the ‘easytrack’ system has enabled us to significantly improve our tyre management processes significantly, ensuring greater accuracy, safety, and productivity across our operations.”
Bridgestone said the system has halved labour time for inventory management and achieved full tyre tracking accuracy after verification trials at Cebu Pacific’s warehouses, MROs, and maintenance bases.
“As a value co-creation partner, we have proposed solutions tailored to on-site operations based on learnings and insights gained from Cebu Pacific Air’s frontline operations,” said Arata Tomita, Director, Global Aviation Tire Solutions Business Division at Bridgestone. “We are very pleased that the official implementation of ‘easytrack’ has contributed to the improvement of operational accuracy, safety, and productivity.”
Bridgestone said the move aligns with its “Bridgestone E8 Commitment,” with a focus on enhancing efficiency and ecology by supporting sustainable tyre practices and operational productivity.
Japan’s ispace, Bridgestone Sign Agreement To Develop Tyres For Lunar Rovers By 2029
- By TT News
- August 04, 2025
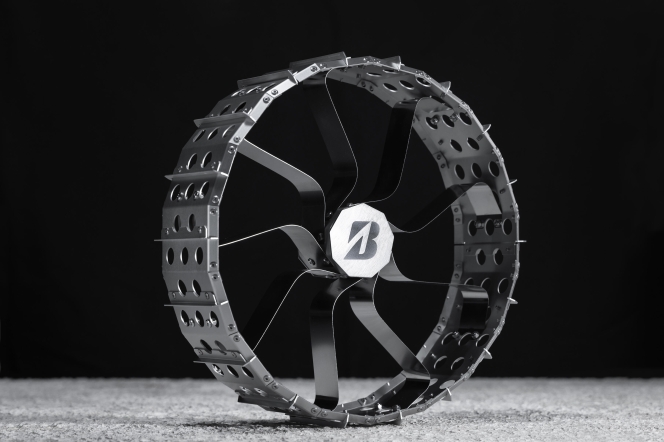
Japanese start-up ispace inc. and tyre maker Bridgestone have agreed to jointly develop tyres for small and midsize lunar rovers, targeting Moon use by 2029.
The partnership equips Bridgestone’s elastic wheel technology—designed to adapt to harsh lunar terrain—on ispace's rover prototypes. The companies will conduct Earth-based performance tests before Moon deployment.
“Bridgestone’s lunar rover tyre has a structure of thin metal spokes, enabling flexible deformation while maintaining durability,” said Masaki Ota, Director of OE Business Strategy & Planning/New Mobility Business Division at Bridgestone. “This design delivers superior ability to traverse and shock absorption, allowing the rover to traverse the lunar surface and overcome obstacles such as lunar rocks.”
Bridgestone started developing lunar rover tyres in 2019 and unveiled concept models in April 2025 with lower weight to suit smaller rover platforms.
ispace, known for micro-sized lunar rovers, sees the partnership as key to its long-term lunar economy mission.
“ispace's goal of establishing a new economy on the Moon requires the participation of players from a wide range of industries,” said Takeshi Hakamada, Founder & CEO of ispace. “Bridgestone… is now developing lunar rover tyres for the extreme environments found on the Moon. These tyres will undoubtedly contribute to future human advancement on the Moon.”
The companies said they are also exploring collaboration opportunities through the Space Strategy Fund at Japan’s national space agency, JAXA.
Magna Tyres Introduces AI-Powered Chatbot As Part Of Customer Service Initiative
- By TT News
- July 08, 2025
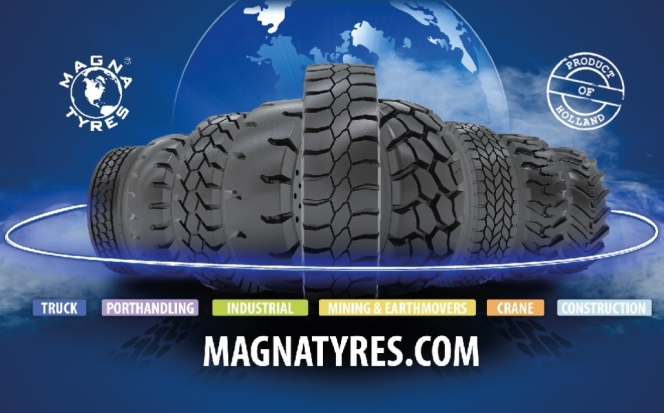
Magna Tyres, a leading premium off-the-road (OTR), industrial and truck tyre solutions company, has launched a new AI-powered (Artificial Intelligence) chatbot on its official website.
The chatbot will provide instant assistance to its customers 24x7 in any language around the world.
Robert Gruijters, Head of Marketing, Magna Tyres, said, “Customer service is at the core of our brand promise. With a Net Promoter Score (NPS) of 67, we already outperform many in our industry and this launch reinforces our commitment to becoming a truly best-in-class brand by being always available, accessible and responsive.”
This move is part of the company’s efforts to not only meet but exceed customer expectations by providing an instantaneous response ranging from product queries to general support.
Comments (0)
ADD COMMENT