- Yokohama Rubber Co
- Yokohama Tech
- RFID
- Yokohama Rubber
- conveyor
Yokohama’s Remote Monitoring Tech For Conveyor Belts Detects Abnormalities In Real Time
- by TT News
- December 18, 2024
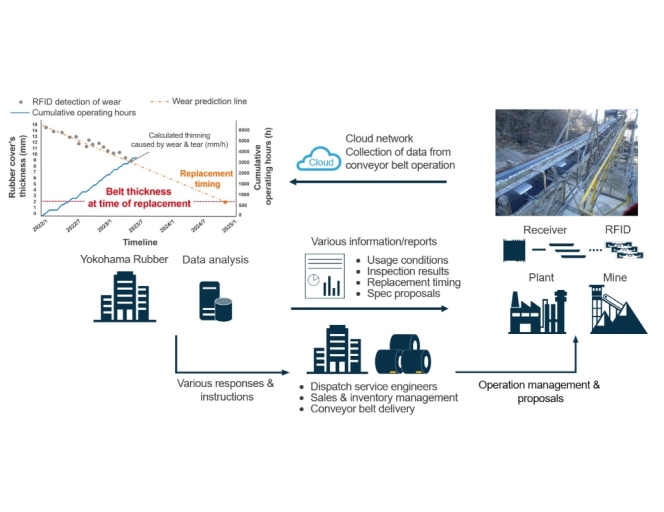
Yokohama Rubber Co, one of the leading tyre manufacturers globally, has developed a sensing technology that remotely monitors conveyor belts operations and detects abnormalities in real-time.
Planned to be commissioned by end-2027 as a comprehensive solution soon, the proprietary sensing technology captures data to detect issues and allows operators to optimise the management of conveyor belt operations.
The Japanese tyre major conducted extensive field trials successfully between February 2022 and December 2024.
How does it work?
The system combines a proprietary Radio Frequency Identification (RFID) tag with Yokohama Rubber conveyor belts, which detects minute changes in the belt’s wear, damage, temperature and other conditions that it claims cannot be detected by normal inspections.
The data is transmitted directly to Yokohama’s data centre where it is monitored in real time.
Yokohama shared that the comprehensive solutions will allow users to check the data, which will allow early identification of abnormalities to prevent damage and fire risks. The Japanese major has applied for 13 patents related to this sensing technology and its operating system.
In addition to reducing unwanted risks, the system also improves efficiency, slashes maintenance cost and help reduce dependency on manual labour.
- Rodolfo Comerio
- Calendering lines
- rubber
Rodolfo Comerio Develops Innovative Calendering Lines To Improve Energy Efficiency
- by TT News
- December 16, 2024
Italy-headquartered Rodolfo Comerio, a leading supplier of advanced systems for calendering lines, has come out with a new innovative solution, which it believes will further make plants more sustainable.
The company’s new calendering lines provides rigorous control, which enables thickness uniformity. Its production versatility processes a wide range of technical materials with different chemical and physical properties. This reduces production times and maximises productivity all the while cutting down on wastage.
Rodolfo Comerio stated that energy efficiency in buildings starts with roof insulation, which is also an effective way to cut down on thermal dispersion and enhance indoor comfort.
The company claims that materials manufactured with its calendering lines are higher efficient, have better durability even in extreme weather conditions and are much more sustainable.
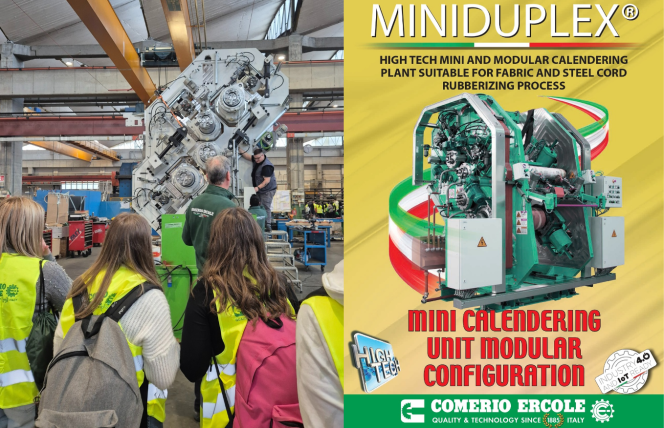
Comerio Ercole, the Italian machinery manufacturer, is poised to enhance industrial performance with its advanced calendering solutions, which enable greater flexibility, precision and efficiency in production processes.
The company’s innovative Shuttle CE windup unit is designed for fully automated roller changes without halting operations, offering substantial cost savings and improved productivity.
The Shuttle CE unit features two identical stands on a shifting platform. While one stand operates under the cross-cutter unit, the other remains offline for roller replacement. This dual-stand configuration, combined with offline loading and unloading via dedicated cranes or integrated systems, eliminates manual intervention and enhances process optimisation.
Further demonstrating its technological leadership, Comerio Ercole recently commissioned a cutting-edge MINIDUPLEX rubber sheeting calendering plant. The plant’s HYDROPLUS configuration achieves ultra-thin rubberised sheets as fine as 0.075 mm, marking a significant breakthrough in precision calendering. The company continues to invest in R&D to refine its solutions and maintain competitive leadership.
- Sumitomo Rubber Industries
- Rockwell Automation
- James Glasson
- Kenji Saito
Sumitomo Rubber Industries to Deploy Rockwell Automation MES Platform
- by TT News
- December 11, 2024
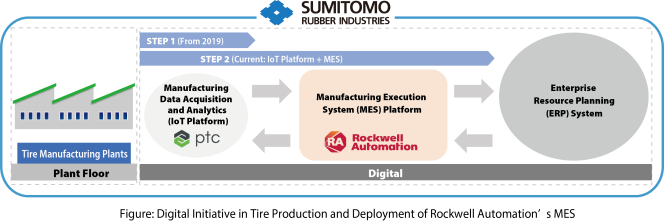
Sumitomo Rubber Industries has decided to deploy Rockwell Automation's manufacturing execution system (MES) platform at its largest domestic factory in Shirakawa City, Fukushima Prefecture, Japan.
The factory will begin operations using the new platform in the second half of 2025.
This move comes as part of the company’s efforts to promote the use of digital technology in tyre production, aiming to enhance and streamline factory operations globally.
Kenji Saito, Executive Officer, General Manager of Manufacturing HQ, Tyre Business HQ Sumitomo Rubber Industries, said, “We believe that leveraging Rockwell Automation’s expertise and flexibility, and our strong partnership with PTC to the maximum will enable us to standardise manufacturing management and enhance operational efficiency globally, driving our growth. To implement DX management as set out in our management vision, we intend to deploy the MES system beginning with the domestic factory and other manufacturing sites thereafter. We will continue to collaborate with Rockwell Automation, a global leader in manufacturing, and embrace new challenges with a forward-looking approach, making full use of AI.”
James Glasson, Vice President, Global Industry Auto, Tire and Advanced Mobility, Rockwell Automation, said, “This initiative will enhance operating efficiency, minimise manufacturing risks, reduce implementation costs and significantly accelerate speed to market.”
In recent years, the manufacturing industry has faced numerous challenges, including rapid changes in the business environment and labour shortages due to Japan’s declining working-age population. To address these challenges, Sumitomo Rubber Industries has been working with PTC since 2019 to adopt PTC’s IoT platform and develop applications to integrate data across production lines and manufacturing sites.
This system has been rolled out at nine of the company’s 11 tyre manufacturing sites, including all four factories in Japan.
The deployment of the Rockwell Automation MES platform will accelerate data organisation and enable the accumulation and sharing of valuable data such as quality and production forecasts across the company. By linking the collected and managed data with the enterprise resource planning (ERP) system, corporate management can gain a comprehensive view of manufacturing operations worldwide.
The Shirakawa Factory will begin operating the MES platform in the second half of 2025. After verifying its effectiveness by the end of 2026, Sumitomo Rubber Industries aims to standardise and roll out the platform to its factories in Japan and overseas.
- Michelin
- Brembo
- Serge Lafon
- Daniele Schillaci
Brembo and Michelin Partner to Develop Next-Generation Braking Systems
- by TT News
- December 11, 2024
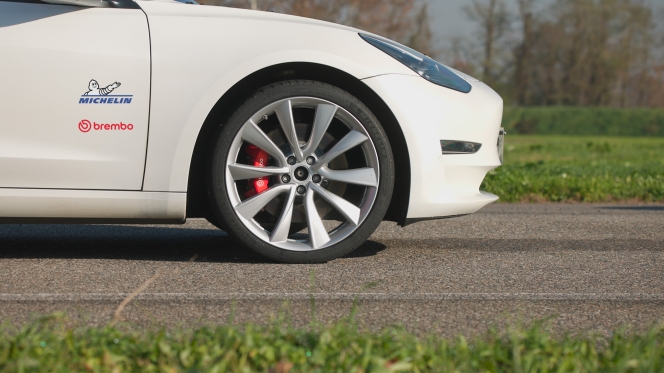
Brembo, a global leader in braking systems, and Michelin, a leading tyre manufacturer, have signed a global agreement to collaborate on the development of advanced braking technologies.
The partnership leverages Brembo’s expertise in braking systems, vehicle modelling, and artificial intelligence and Michelin’s leadership in tyre modelling and algorithm development.
The innovation relies on the continuous exchange of real-time data between Michelin’s connected solutions software, which provides tyre grip data, and Brembo’s innovative SENSIFY braking system. This data enables engineers to fine-tune the braking system with exceptional precision, enhancing SENSIFY’s performance.
Michelin’s tyre-connected solutions utilise the company’s expertise in tyre physics modelling and simulation. Through live vehicle data analysis, Michelin has developed software that provides real-time information on tyre wear (Michelin SmartWear), load (Michelin SmartLoad) and grip (Michelin SmartGrip). This software is compatible with all tyre brands.
Serge Lafon, President of the Business Line Automotive Original Equipment at Michelin, commented: “We are thrilled to join forces with a brand like Brembo, a leader in its field. Our shared passion for innovation and excellence allows us to take a new step forward in enhancing user safety. Allowing customers to keep their tires in use as long as possible with total peace of mind is a core objective of Michelin, thus protecting their purchasing power and the environment. Today, Michelin is a “data-driven company” where simulation and software development are essential tools in the real-time monitoring of tyres. Together, Michelin and Brembo are building a unique solution for the vehicles of the future, developed today by the car makers.”
“At Brembo, we believe in the power of technology and artificial intelligence,” said Daniele Schillaci, CEO of Brembo. “In fact, we are increasingly becoming a company combining software capabilities with our expertise in the corner of the vehicle, mastering callipers, discs and friction materials with unique know-how. SENSIFY represents the new standard in braking that will target a zero-accident vision. This partnership with Michelin illustrates the power of collaboration and innovation in the automotive industry.”
Brembo’s SENSIFY sets a new benchmark for braking systems, designed for integration into any modern vehicle. It combines Brembo’s braking components with a digital brain that utilises AI, algorithms, and sensors to independently control each wheel.
Initial virtual and on-track tests have demonstrated promising results. In the first phase, Michelin’s tyre models and algorithms were integrated with Brembo’s intelligent braking models in a virtual environment. In the second phase, physical tests were conducted at Michelin’s Research Center, confirming the simulation results.
Tests demonstrated braking distance reductions of up to four metres (13 feet) during Anti-lock Braking System (ABS) events, with the same tyres in various conditions. The braking system also exhibited quicker response times, minimised traction loss, improved lateral stability and eliminated wheel locking, contributing to a smoother and more comfortable driving experience.
Comments (0)
ADD COMMENT