- JK Tyre
- Indian Car of the Year (ICOTY)
- Indian Motorcycle of the Year (IMOTY)
- Tae-Jin Park
- Kia India
- Siddhartha Lal
- Eicher Motors
- Santosh Iyer
- Mercedes-Benz India
- Bertrand Dsouza
- Dhruv Behl
Arlanxeo Launches Keltan Ultra-High Mooney 100+ Innovation Platform
- By 0
- June 05, 2020
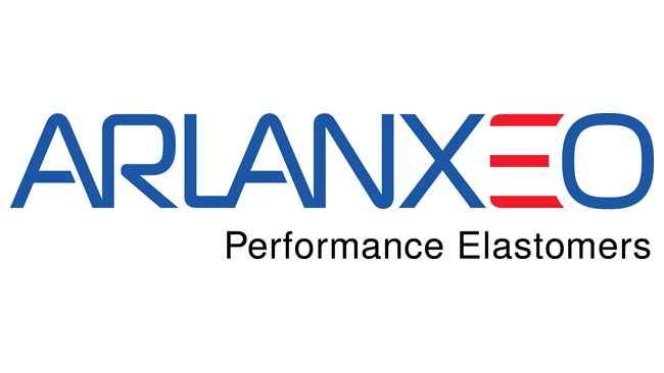
Arlanxeo, a world-leading synthetic rubber company, recently launched its Keltan Ultra-High Mooney 100+ Innovation Platform. Based on the novel Keltan ACE catalyst technology and the excellent finishing process, this platform is primarily focused around the development of new grades with high Mooney viscosity, to optimize physical properties and cost, thus to satisfy the demand for the upgrade of applications across industries, including automotive, construction, and transportation.
Currently, markets are calling for better EPDM products. A major challenge in this has been finding the balance between improved physical properties and reasonable production costs. To satisfy the tight requirements from domestic clients, Keltan Ultra-High Mooney 100+ Innovation Platform has launched three new grades – Keltan 13561C, Keltan 10660C, and Keltan 10950C. Each of these grades has adopted Keltan Controlled Long Chain Branching (CLCB) technology, achieving good mechanical and processing performance. Meanwhile, this platform is about to launch a new Ultra-High Mooney oil-extended grade – Keltan 10675C (50 phr of extender oil).
Keltan 13561C has Mooney viscosity of 130MU at 125℃. Its ultra-high molecular weight enables higher mechanical property that is the same as or even higher than crystalline grades, but without issues of inferior low-temperature performance, high shrinkage, etc. Keltan 10660C reaches 100MU at 125 ℃ and possesses both ultra-high molecular weight and a combination of processing and mechanical properties. With this, Keltan 10660C can be applied to general mixing devices. Both grades are able to bring reduced costs through increasing compound loading without influencing the mechanical property. By virtue of the advantages of ultra-high Mooney, non-crystalline, fast vulcanization, higher elasticity and compound loading, Keltan 13561C and Keltan 10660C can adapt to strict standards of production and application and are widely applied to produce automotive seals and hoses, seals for construction, and rubber products for rail systems.
Sponge grade Keltan 10950C reaches Mooney viscosity of 100MU at 125 ℃. Due to the high Mooney viscosity, the grade also enables a reduced cost with increased compound loading while still maintaining the same mechanical property and compression set. Compared with the previous sponge grades, Keltan 10950C has a larger molecular weight, higher elasticity and non-vulcanized compound strength, and excellent extrusion performance, like outstanding flowability, better collapse resistance, and good profile appearance, offering an alternative for producing high-performance sponge seals. Major applications of the grade include auto sponge profiles, window sponge profiles, and insulation materials for construction.
“Arlanxeo Keltan Ultra-High Mooney 100+ Innovation Platform is committed to fulfilling the customers’ demand for products with higher performance and lower cost. Facing the new challenges and opportunities ushered by the industrial upgrades, we will stay innovative, close to the local market, and customer-centric, and continually innovate to provide excellent products and services”, said Dr. Baojia Cheng, Head of TSAD and R&D, HPE Asia, ARLANXEO.
The three Keltan grades above are all produced by Arlanxeo Changzhou plant and are available in the market.
- Covestro
- Flame-Retardant Encapsulation Foam
- Flame-Retardant Foam
- Polyurethane Foam
- Baysafe BEF
- Electric Vehicles Traction Battery Safety Requirements
- EV Battery
Covestro Enhances EV Battery Safety With New Flame-Retardant Encapsulation Foam
- By TT News
- July 17, 2025
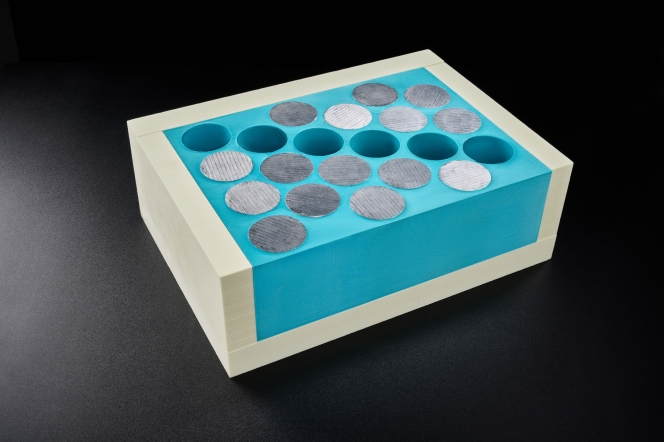
Covestro has introduced its next-generation Baysafe BEF flame-retardant polyurethane foam, a breakthrough in EV battery safety. Designed to prevent thermal runaway propagation between cells, this lightweight foam meets stringent global safety demands, particularly in China, where the new GB 38031-2025 standard will require fireproof batteries from 2026.
As the world’s largest EV market, China’s regulations are expected to influence global standards, making Covestro’s innovation critical for automakers. The foam’s superior flame resistance enhances safety in EVs, e-bikes and portable energy storage, addressing a key consumer concern. By combining cutting-edge flame-retardant technology with lightweight performance, the Baysafe BEF series helps drive the transition to sustainable transportation and energy storage worldwide.
With EV adoption accelerating, Covestro’s material solutions support manufacturers in meeting stricter safety requirements while enabling international expansion. Beyond encapsulation, the company offers polyurethane-based battery covers and shock-absorbing components, strengthening its position in the fast-growing new energy sector.
Akhil Singhania, Global Head of PU Specialties in Covestro’s Tailored Urethanes Business Entity, said, “This innovation represents a significant step towards enabling sustainable mobility through enhanced safety. By launching our advanced flame-retardant technology, Covestro reaffirms its commitment to innovation and strengthens our product portfolio to meet the evolving needs of the EV industry.”
Zeon Develops Hydrophilic SBR For Winter Tyres
- By TT News
- July 16, 2025
Zeon Corporation has announced the development of Nipol BR1300, a novel hydrophilic styrene butadiene rubber (SBR) for winter tyres. Synthesised with a polybutadiene rubber base, the material delivers unprecedented hydrophilicity for tyre applications. Commercial production began in May 2025 at Zeon’s Tokuyama plant in Yamaguchi Prefecture.
As part of its strategic portfolio optimization, Zeon plans to phase out low-profitability products like ESBR-1 and NBR latex by 2026. However, it will continue manufacturing high-margin products, including ESBR-2, nitrile butadiene rubber and solution SBR. This shift underscores Zeon’s focus on advanced, value-driven rubber solutions.
- Covestro India
- CSIR-National Chemical Laboratory
- Circular Economy
- Polyurethane Waste
- Polyurethane Recycling
Covestro India Partners With CSIR-NCL To Pioneer Polyurethane Upcycling Solutions
- By TT News
- July 16, 2025
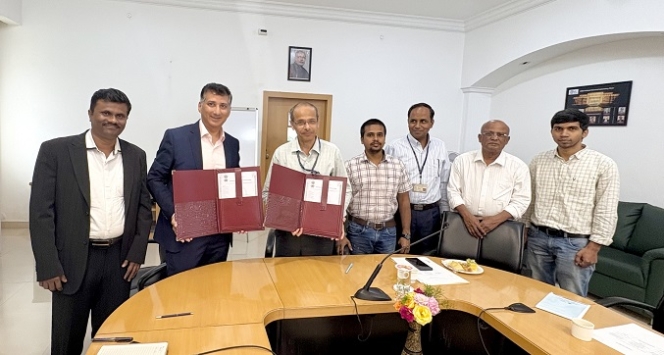
Covestro India has entered into a strategic collaboration with CSIR-National Chemical Laboratory (NCL) through an innovative CSR initiative focused on developing sustainable upcycling technologies for polyurethane waste. This partnership aims to overcome existing recycling limitations by transforming discarded polyurethane materials into valuable chemical feedstocks, potentially revolutionising the material's circular economy.
This collaboration underscores both organisations' commitment to environmental innovation, leveraging NCL's advanced research infrastructure and Covestro's market leadership to address critical gaps in plastic circularity. Current polyurethane recycling methods, predominantly mechanical with some emerging chemical processes, face substantial challenges including material degradation, high energy consumption and hazardous byproduct generation. The project seeks to develop commercially viable chemical recycling solutions that maintain material integrity while minimising environmental impact.
Polyurethanes, widely used in furniture, automotive parts and insulation, present unique recycling difficulties due to their complex molecular structure. Most end up in landfills after use, creating significant sustainability challenges. By combining Covestro's industrial expertise with NCL's seven decades of chemical research excellence, the partnership aims to create breakthrough upcycling technologies.
Avinash Bagdi, Director & Head of Sales & MD Solutions India & Projects – Tailored Urethanes, said, "This partnership strengthens our commitment to finding innovative solutions for polyurethane waste and directly supports Covestro's vision of becoming fully circular. By developing effective methods to upcycle polyurethanes, we're taking concrete steps towards creating a more sustainable future in line with our corporate vision of driving the transition to a circular economy."
Dr Ashish Lele, Director of NCL, said, "CSIR-National Chemical Laboratory is excited to partner with Covestro (India) in this groundbreaking initiative to develop novel chemical upcycling methods for polyurethane waste. The conventional and electrochemical strategies we're developing address the critical limitations of current recycling technologies and align perfectly with our shared vision of a circular economy. This collaboration represents a significant step towards sustainable plastic management in India and globally, with potential to transform polyurethane waste into valuable chemical resources."
Zeon Starts Construction Of Bench-Scale Facility For Sustainable Butadiene Production
- By TT News
- July 11, 2025
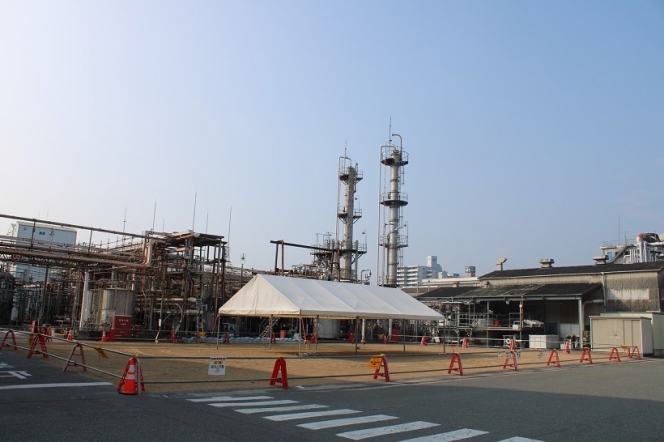
Zeon Corporation has begun building a pilot facility at its Tokuyama Plant in Shunan City, Yamaguchi Prefecture, to test a new method for efficiently producing butadiene from plant-derived ethanol. The demonstration plant, expected to start operations in 2026, will supply butadiene for manufacturing trial batches of polybutadiene rubber, bringing the company closer to commercialising this sustainable production process.
This project is a key part of a joint initiative between Zeon and The Yokohama Rubber Co., Ltd. to develop eco-friendly methods for producing butadiene and isoprene from renewable sources, with full-scale adoption targeted for the 2030s. Under the collaboration, Zeon will produce butadiene rubber at the new facility, while Yokohama Rubber will use the material to create experimental tyres and conduct performance testing. The data collected will help refine the technology ahead of larger-scale trials. The companies aim to finalise the production process by 2030 using an expanded pilot plant, with plans for industrial-scale commercialisation by 2034.
A ceremonial groundbreaking event took place on 10 July 2025, with 33 attendees, including local government officials from Yamaguchi Prefecture and Shunan City, construction partners and Zeon executives such as Chairman Kimiaki Tanaka and Tokuyama Plant Manager Akira Honma. The gathering included traditional safety prayers for the construction phase, marking the official start of this sustainability-focused industrial project.
Comments (0)
ADD COMMENT