Cleaner Pyrolysis
- By Sharad Matade
- July 04, 2025
Paul Lloyd: “Farrel Pomini’s core business lies in supplying processing equipment for the plastics and petrochemical industries."
Pyrolysis has long been associated with pollution and inefficiency, particularly in developing markets where outdated methods dominate. However, technological advancements and a stronger push for circularity are transforming this perception. HF Group, through its subsidiary Farrel Pomini and WF Recycle-Tech, is at the forefront of this shift, introducing a continuous pyrolysis system that promises cleaner and more efficient tyre recycling. Unlike traditional batch processing, its technology ensures consistent output, better resource recovery and reduced emissions.
Pyrolysis has always been considered to be a dirty business. However, with the changes in technology and the increasing hunt for circularity across the tyre industry, businesses are attempting to redefine the age-old tyre recycling process and remove the malice associated with it.
Farrel Pomini is one such entity with the HF Group that is attempting to make pyrolysis cleaner. WF Recycle-Tech, established in 2013, started commercial operations in 2022 with selling its first pyrolysis unit in 2024, slated to be operational in 2026.
Speaking to Tyre Trends, President Paul Lloyd said, “Farrel Pomini’s core business lies in supplying processing equipment for the plastics and petrochemical industries. While its continuous mixer can be used for rubber applications, it is primarily designed for plastic masterbatches and compounds. The company operates across multiple divisions with its plastics compounding equipment focusing on niche applications for highly filled and temperature-sensitive materials. Although the plastics market is significantly larger than the rubber sector, Farrel Pomini targets specialised segments within it. Expanding its footprint in sustainability, the company has developed recycling systems for both plastics and rubber. The end-of-life tyre recycling solution was developed in collaboration with its group company, WF Recycle-Tech.”
Tyre pyrolysis has long been regarded as a polluting industry, particularly in developing countries where unregulated plants often operate at night to evade environmental scrutiny. In markets like India, many such facilities shut down due to non-compliance, reinforcing the industry’s reputation as a ‘dirty business’.
Lloyd further explained, “In Europe, the focus is shifting towards sustainability, driving innovation in pyrolysis technology. Traditional methods relied on large kilns, where tyres were burned with external heat over extended periods. The process was inefficient, labour-intensive and environmentally damaging, requiring extensive manual cleanup.
HF Group has taken a different approach, developing a continuous pyrolysis system that eliminates these challenges.”
Instead of batch processing, the system ensures a constant flow of material, allowing for the controlled capture of gases, liquids and solid outputs. The process begins with pre-grinding tyres into metal-free rubber crumb (6–20 mm), which is then fed into the machine via a hopper. Operating at a capacity of 1,500 kilogrammes per hour, the system requires only continuous material input while automatically managing output streams including recovered oil and gas.
Apropos to the pain points that the company wanted to address, he noted, “Over the past decade of developing this solution, several key learnings and priorities emerged. First and foremost, the goal was to create an efficient pyrolysis system that could consistently process tyre waste at an industrial scale. Second, the decision to develop a continuous rather than batch-based system was fundamental as continuous pyrolysis offers greater consistency, scalability and efficiency. Third, integrating a continuous mixer in the pre-processing stage became a major focus as it significantly improved the homogeneity and quality of the output materials. Finally, optimising the recovered output, particularly recovered carbon black, became the primary objective. Initially, the project was focused on tyre-derived oil (TDO), but as the market evolved, the emphasis shifted to producing the highest-quality rCB, aligning with upcoming ASTM standards and stringent industry requirements.”
By integrating advanced processing controls, the solution ensures cleaner, more efficient pyrolysis, positioning itself at the forefront of sustainable and cleaner tyre recycling.
THE OUTPUT
HF Group’s expertise in mixing technology creates a natural synergy between its traditional business and its expansion into tyre recycling. While the company is known for its tyre curing and rubber mixing solutions, it also has a plastics mixing division; this same mixing technology plays a crucial role in its pyrolysis process.
The recycling system starts with tyre crumb, which is fed into a high-shear Farrel Continuous Mixer originally designed for plastics processing. The mechanical shear heating raises the temperature of the material to 330 degrees Celsius. This ensures uniform heating before the material enters the pyrolysis chamber, where temperatures increase to between 520 degrees Celsius and 580 degrees Celsius. The continuous system eliminates inefficiencies seen in traditional batch pyrolysis, where prolonged heating cycles lead to higher energy consumption and inconsistent output.
Material recovery is a key advantage of the system. For every tonne of tyre crumb processed, approximately 50 percent is converted into pyrolysis oil, yielding 550–570 litres. Around 40 percent becomes recovered carbon black (rCB), a critical raw material that can replace virgin carbon black in industrial applications. The remaining 10 percent is gas, which can be used to power the system, further improving energy efficiency.
Beyond throughput, the system’s design significantly reduces overall energy demand. Mechanical shear heating minimises reliance on external thermal energy, while the continuous process prevents heat loss and optimises fuel efficiency.
Additionally, rCB from the pyrolysis process requires 60–70 percent less energy to refine, further enhancing sustainability.
“Pyrolysis fundamentally relies on heat and time in the absence of oxygen. Under these conditions, tyres thermally degrade, breaking down into vapour, which is condensed into oil and a solid residue, which is now widely used as recovered carbon black (rCB). This output can be further refined for industrial applications, creating a circular economy within the rubber industry,” explained Lloyd.
CHALLENGING INTEGRATION
The primary challenge for tyre manufacturers in adopting rCB is achieving performance characteristics comparable to virgin carbon black. Similarly, tyre pyrolysis oil must meet stringent quality standards to serve as a feedstock for high-value applications beyond just fuel. The company’s continuous pyrolysis system addresses these concerns by enhancing the quality and usability of both outputs.
“In the case of tyre pyrolysis oil, if used as a fuel, the calorific value may vary slightly, but it remains a viable option. However, its greater potential lies in serving as a feedstock for sustainable carbon black or even virgin carbon black production. The consistency of the oil’s composition determines its suitability for high-end applications, making process control a critical factor,” noted Lloyd.
He added, “For rCB, higher quality directly translates into increased usability across different applications. While rCB will never completely replicate virgin carbon black, superior grades enable a higher substitution rate. In some cases, a high-quality rCB can replace up to 30 percent of virgin carbon black, whereas lower-quality alternatives may only allow a 15 percent substitution. This increased usability not only enhances sustainability but also raises the material’s commercial value.”
HF Group’s rCB, produced through its WF Recycle-Tech process, has been extensively tested across multiple industries. It has demonstrated strong performance in plastics masterbatch applications, technical rubber goods and even tyre manufacturing. One major tyre producer has already validated its suitability for substitution in new tyres, underscoring its industry acceptance.
A key differentiator of the process lies in its patented two-stage pyrolysis system. While continuous pyrolysis itself is well established, HF Group’s innovation stems from its integration of a high-shear Farrel Continuous Mixer in the first stage.
This approach ensures uniform heating, eliminates direct heat exposure and optimises the pyrolysis reaction in the second stage. The result is a more efficient process that yields higher-quality recovered carbon black and cleaner tyre pyrolysis oil.
PERSEVERING THROUGH LIMITATIONS
The primary limitations of the system, Lloyd noted, revolve around scalability, operational efficiency and material consistency. The current processing capacity of 1,500 kilogrammes per hour is relatively low. Scaling up production rates while maintaining efficiency and reliability is an ongoing challenge. The key challenge is ensuring long-term operational stability and optimising run times.
Another significant factor is feedstock variability, particularly in markets like India, where used tyres from different sources such as passenger cars, trucks and buses are often mixed without segregation. The ideal scenario would involve processing a uniform type of tyre with a consistent rubber composition, but in reality, recycling operations must work with what is available.
“There are two main approaches to addressing this viz-a-viz meticulous sorting, which ensures consistency but is time-consuming and costly, or strategic blending, which creates a stable output by balancing material variations. The current system has been designed to handle diverse feedstocks without sorting, using a consistent blend of tyres to produce a predictable output,” said Lloyd.
In the long term, technological advancements such as artificial intelligence or tracking mechanisms for tyres could enhance sorting processes, making recycling operations more efficient. However, for now, the focus remains on refining the system to handle real-world feedstock conditions while delivering high-quality outputs. The continuous processing system also provides flexibility to adjust parameters and optimise results, making it a robust solution even in environments where feedstock quality is unpredictable.
MARKET TALK
The return on investment for pyrolysis systems is quite favourable, but it carries risks, especially in the early stages. A well-managed system operating efficiently for 6,000–7,000 hours per year, with a stable feedstock supply and consistent product quality, can generate strong financial returns, explained the executive.
However, challenges arise if there are interruptions in material supply, equipment downtime or fluctuations in product quality. These factors introduce uncertainty, which can make securing financing more difficult. That said, the market for TDO and rCB is growing, providing ample opportunities for revenue. Companies that can differentiate its output and meet quality standards can command premium prices, further improving ROI.
The market focus for HF Group’s advanced pyrolysis solutions primarily includes recyclers looking to add more value to their processes, material users such as tyre manufacturers and technical rubber companies seeking sustainable raw materials and new businesses emerging in response to industry needs.
“In the US and Europe, there is a growing entrepreneurial push to bridge the gap between traditional recycling and the sustainability requirements of the tyre industry. However, in markets like India and other parts of Asia, the challenge lies in shifting perceptions. Many existing pyrolysis operations use older-generation systems. The transition to modern, cleaner and more efficient systems requires education, proof of performance and financial support. Despite these challenges, India remains a strong market for HF, as the industry values high-quality technology and is willing to invest in the best solutions once the benefits are clearly demonstrated,” informed Lloyd.
Over the next five years, the company’s primary goal is to establish a proven track record with the first full-scale pyrolysis system, demonstrating its performance, reliability and efficiency. Once this is achieved, the focus will shift to helping potential customers secure financing by reducing perceived risks, making it easier for them to invest in the technology.
Alluding to the next phase of development, Lloyd informed, “The next phase of development focuses on three main areas. The first priority is industrialising the system to ensure it operates efficiently, consistently and reliably over long production cycles. This transition from pilot-scale to full-scale manufacturing is where HF Group’s expertise in engineering advanced processing equipment comes into play. Secondly, efforts are underway to further refine the pyrolysis reaction to enhance output quality and efficiency. Lastly, ongoing research and development is focused on post-processing improvements, particularly the removal of ash from recovered carbon black to increase its usability in high-performance applications.” n
HANWA Invests In Thai Tyre Pyrolysis Company
- By TT News
- July 24, 2025
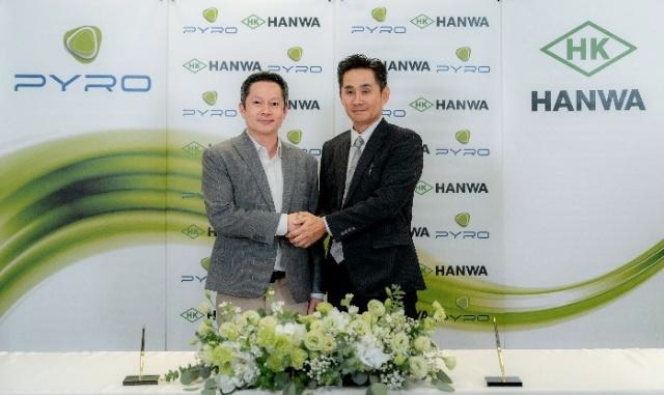
HANWA THAILAND CO., LTD., a subsidiary of Japan’s HANWA CO., LTD., has acquired a partial stake in PYRO ENERGIE CO., LTD., a Thailand-based company specialising in tyre pyrolysis recycling. This strategic move addresses the persistent global issue of end-of-life tyres and manufacturing defects, which often lead to environmental harm through illegal disposal or landfill accumulation. While HANWA Group already supplies tyre chips as an eco-friendly fuel source to Japanese industries, pyrolysis has emerged as a preferred recycling solution in global markets.
The pyrolysis process thermally decomposes waste tyres in an oxygen-deprived environment, yielding reusable materials like pyrolysis oil and carbon residue. These outputs serve as valuable fuel alternatives or raw materials for tyre production and other industrial uses, advancing decarbonisation goals. By partnering with PYRO, HANWA seeks to enhance the commercial viability of pyrolysis-derived products and establish an international supply chain in cooperation with tyre manufacturers. The resulting materials will support the chemical, synthetic rubber and tyre industries, promoting a circular economy.
Both HANWA and HANWA THAILAND hold ‘ISCC PLUS’ and ‘ISCC EU’ certifications, underscoring their commitment to sustainable practices. The group remains dedicated to expanding its portfolio of certified recycled and biomass products, reinforcing its role in building a decarbonised future.
Ecolomondo Secures Quality Approval For rCB Produced At Its Hawkesbury TDP Facility
- By TT News
- July 24, 2025
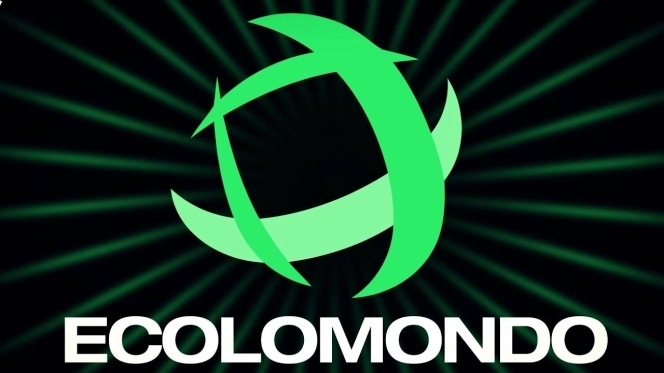
Ecolomondo Corporation, a Canadian leader in sustainable scrap tyre recycling, has achieved a significant milestone as its primary offtake client has officially approved the quality of the recovered carbon black (rCB) produced at its Hawkesbury Thermal Decomposition Process (TDP) facility. This approval follows the successful commissioning of new milling equipment and an rCB processing line, marking a critical step towards full-scale production.
To ensure compliance with stringent quality standards, Ecolomondo conducted extensive in-house testing using advanced laboratory equipment. Key parameters, including humidity, pellet size, pellet hardness, ash content and particle size, were meticulously evaluated. After confirming that all specifications were met, the company shipped rCB samples to offtake clients for independent verification. The clients’ test results aligned closely with Ecolomondo’s own findings, validating the material’s high quality.
In response to this successful validation, the primary offtake client placed an initial order for 23 metric tonnes of rCB, which Ecolomondo is preparing to ship immediately. At full operational capacity, the Hawkesbury facility is projected to recycle between 1.3 million and 1.5 million scrap tyres annually, yielding approximately 4,000 metric tonnes of rCB, 5,000 metric tonnes of pyrolysis oil, 2,000 metric tonnes of steel and 1,200 metric tonnes of process gas. This milestone underscores Ecolomondo’s leadership in sustainable tyre recycling and reinforces the commercial viability of its TDP technology.
Jean- François Labbé, Interim CEO of the Company, said, “The commercial acceptance of our rCB by offtake clients reflects the achievement of many years of technology development and commitment. It is a major achievement for the Company and we are confident that additional orders should come because of the quality of our rCB.”
CARBIOS Signs PET Recycling Deal With Indorama
- By TT News
- July 24, 2025
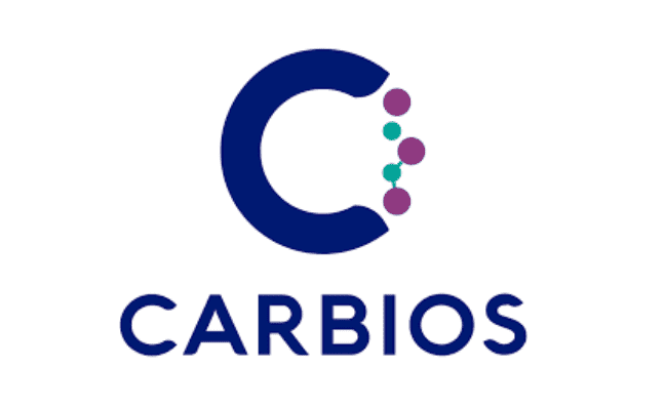
CARBIOS has signed a multi-year commercial agreement with Indorama Ventures, the world’s leading PET producer, to supply biorecycled monomers from its Longlaville plant. Indorama will repolymerise these monomers into r-PET filaments, which Michelin will then integrate into its tyre reinforcements.
Using its proprietary enzymatic recycling technology, CARBIOS will process complex PET waste into high-purity monomers at its new facility. Indorama will handle the conversion of these monomers into technical-grade filaments, enabling Michelin to enhance the sustainability of its tyres. This partnership accelerates the pre-commercialisation phase of CARBIOS’ industrial project, building on recent contracts with two major cosmetics brands for biorecycled PET.
The collaboration highlights the growing demand for circular solutions in manufacturing, with CARBIOS’ innovation playing a pivotal role in transforming waste into high-value materials. This milestone reinforces CARBIOS’ position as a leader in enzymatic recycling and supports Michelin’s commitment to sustainable mobility.
Vincent Kamel, CEO of CARBIOS, said, “This commercial agreement with Indorama Ventures marks a new step in the realisation of our industrial project. It confirms the trust of Indorama Ventures and Michelin in our PET biorecycling technology. Alongside the commercial successes already achieved in cosmetic packaging applications, this agreement illustrates our ability to deliver innovative solutions to the most demanding industries, particularly industrial filaments for tyre applications and, more broadly, textile.”
Fabien Gaboriaud, Director of Circularity and Renewable & Recycled Materials at Michelin Group, said, “This partnership is a tangible expression of our commitment to turning complex waste into high-performance materials. By integrating enzymatically recycled r-PET into our tyres, we are marking a new milestone on our journey toward achieving 100 percent renewable and recycled materials by 2050 — all while staying within planetary boundaries. It is by combining innovation, industrial excellence and close collaboration with trusted partners that we are building a strong and lasting circular model.”
Renato Boaventura, Global Market Head – Mobility at Indorama Ventures, said, “This alliance with both, CARBIOS and Michelin, underlines our commitment to plan ahead and take a leading role in shifting the industry towards circularity.”
- Sinochem Group
- ESG Ratings
- Sinochem International
- Sinochem Equipment
- Shenyang Chemical
- Wind ESG Ratings
ESG Ratings Jump For Sinochem Group’s Listed Companies
- By TT News
- July 19, 2025
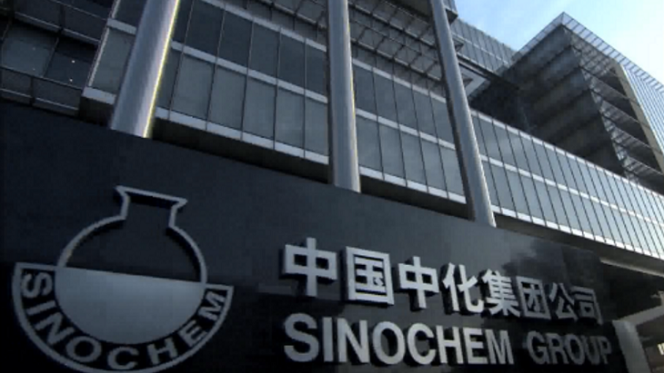
Wind, a leading financial data provider, has released its 2025 ESG (Environmental, Social and Governance) ratings, showcasing notable improvements for several listed companies under Sinochem Group. The ratings reflect these companies' strong commitment to sustainable development and corporate responsibility.
Sinochem International achieved an AA rating in 2025, a significant improvement from its previous rating in 2024. With a comprehensive score of 8.56 out of 10, the company now holds the highest ESG rating in the diversified industrial sector, setting a new record among Sinochem Group’s listed companies. Sinochem Equipment and Shenyang Chemical also demonstrated substantial progress, with both companies upgrading from a BBB rating in 2024 to an A rating in 2025. These improvements underscore the group-wide advancements in sustainability practices.
The upgrades highlight Sinochem Group’s intensified focus on sustainability initiatives, including enhanced environmental compliance, green transition efforts, stronger corporate governance and improved transparency. Additionally, the companies have made strides in social responsibility programmes, such as worker welfare and community engagement.
The ESG rating jumps for Sinochem International, Sinochem Equipment and Shenyang Chemical underscore Sinochem Group’s leadership in sustainable business practices. As China continues to push for carbon neutrality and ESG integration, these companies are well-positioned for long-term growth and resilience.
Comments (0)
ADD COMMENT