Elastomer Tackifiers
- By Dr. Samir Majumdar
- October 19, 2020
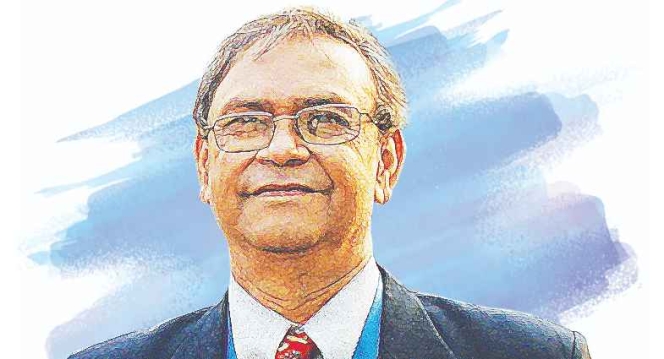
Elastomer tackifiers are those that produce green tack in elastomers. The term “tack” refers to the ability of two uncured rubber materials to resist separation after bringing them into contact for a short time under relatively high pressure. Building tack of rubber components is an important pre-requisite to enable tyre building on the tyre building drum where different rubber layers are put together on the tyre building drum before they are cured. Another important property of tackifier is, it should retain its tack on storage. A good tackifier, therefore, should have the following properties :
- Very high initial and extreme long-term tackiness
- No adverse effect on the rubber compound cure on scorch
- No interference on (a) rubber to metal bonding (b) rubber to fabric bonding
- Physical properties of the cured rubber remain unchanged
- No effect on the performance of aged rubber compound properties
- Improves rubber compound process reliability
- Show extreme good performance in silica / s-SBR based rubber compound.

In general, NR has enough tack because of the presence of a very high quantity of low molecular weight fraction, having its wide molecular weight distribution. Its low molecular weight fraction also generates during its break down in machines. On the contrary, synthetic rubber lack in tack property because of the absence of enough low molecular weight fraction in them, having narrow molecular weight distribute on (Fig.1). Synthetic rubber also resists in the molecular break down upon mastication and therefore, cannot produce low molecular weight fraction. Resins are typically produced with molecular weights (Mw) between 1,000 and 2,000 with maximum Mw around 3000. The molecular weight is important since tackifying resins work at the surface of the rubber compound and must be able to migrate to the surface to be effective. If the molecular weight is too low, the resin will remain soluble in the elastomer and not migrate its way to the surface. If the molecular weight is too high, the elastomer will be insoluble in the elastomer. Rubber industries use both synthetic and natural resins for tack. Following three types are in major use in the industry :
- Aromatic Resins (Phenolic, Cumaron Indane)
- Petroleum based resins
- Plant Resins ( wood rosin resins,Terpene resins)
Only plant resin is a source of natural resins. However, due to product consistency and different compatibility factors, synthetic resins are in major use. Besides tyre and other rubber applications, the major end-uses for resins are in pressure-sensitive adhesives, hot-melt adhesives, road markings, paints, caulks, and sealants. Manufacturers use hydrocarbon resins to produce hot melt adhesives (for infant and feminine) and packaging applications in addition to glue sticks, tapes, labels and other adhesive applications. All resins are sticky and because of their low molecular weight they migrate (diffuse) easily on the rubber product surface and behaves sticky and that causes tack. Tack property is apparently due to two major reasons :
- Spontaneous diffusion of molecules between two uncured rubber layers.
- Strong molecular forces resulting high degree of crystallinity
Highest level of tack in NR could be due to both the reasons, which means, NR has a high degree of crystallinity (stress induced crystallization) and it has also broad (wider) molecular weight distribution (Fig.1), so that, having plenty of lower molecular fraction can diffuse faster between two layers in contact each other. NR is reported to improve upon its tack on mastication because it generates a higher number of lower molecular weight fraction chains upon breaking down on shearing forces in machines. CR (Neoprene Rubber) shows exceptional adhesive property because it shows the highest degree of crystallinity, even much greater than NR, due to its strong intermolecular attractive force.
Honestly, NR may not require any tackifier because it has enough low molecular weight fraction of chain molecules, due to its wider molecular weight distribution (Fig.1), to be migrated on the rubber component surface and can produce enough tack. It loses its tack mostly because it might have been processed at a higher temperature and is already in the premature vulcanization stage. It can also happen due to the fact that although calendaring or extrusions were done at the right temperature stock was made before adequate cooling and thereby allowed scorching in windup liners. It also loses its tack at cold ambient temperature, in the rainy season and also if the filler level is too high or if the viscosity of the stock is substantially higher than required. However, all synthetic rubber or when synthetic rubber (SBR,BR) is blended with NR, may require to add adequate resins for compound processing.
Except C4,C5 petroleum-based resins, all other types of resins are compatible with NR and is added 1-2 phr. Comparatively C9 petroleum-based resin is better in NR. Plant-based resins are found to work better in 100% NR. When NR is compounded with synthetic rubber, the tackifier is a must and the dose could be as high as 2-4 phr depending on the content of synthetic rubber, oil and filler in the compound matrix. All synthetic rubber lag in rubber tack because, in general, synthetic rubber has :
- Narrow molecular weight distribution
- It resisting break down of molecular chains under mechanical shear
- Synthetic rubber is in very pure form
Aromatic Resins (Phenolic, Cumaron Indane) work better in SBR and BR than plant based resins. For hydrocarbon type of elastomers like butyl , halobutyl , EPM and EPDM , petroleum base resin (C4,C5) work better and usually added with 1-2 phr in the formulation, However, with a higher dose of filler, 2-4 phr tackifier could also be added.
Tackifier resins are added to base polymers/elastomers not only to improve tack (ability to stick) but it also helps in better wetting with filler. Increase in tensile strength by adding resins has been witnessed in different types of elastomers, aromatic resins have been witnessed to increase tensile strength of SBR and its blend.
Effect of Environment on Rubber Tack
The tack of a rubber article is greatly affected by environmental conditions such
as temperature, ozone level and humidity. Environment can not influence tack, however, if processed rubber compound is used with in 24 hrs. High temperature and humidity conditions have a detrimental effect on the initial tack and tack retention of an elastomer. Phenolic tackifying resins can help improve tack under these conditions, but they have their limits under extreme conditions. Superior tack retention under the influence of high humidity can be often be achieved with epoxy resin modified alkylphenol-formaldehyde polymers.
Hydrocarbon based tackifying resins are sometimes used as a low-cost alternative to phenolic tackifying resins. However, hydrocarbon resins are not as effective at maintaining tack under adverse environmental conditions, like elevated temperature and high humidity, nor do they have the same tack retention. Hydrocarbon resins however, preferred in butyl and EPDM rubber compound due to their compatibility.
Hydrocarbon resins are not as efficient as phenolic tackifying resins, and higher levels are often required to achieve the same tack. High tackifier resin levels can cause a loss in tensile strength, tear strength and, most importantly, hysteresis. In applications where these properties, especially hysteresis, are important, phenolic tackifying resins are excellent choices and should be used.
HANWA Invests In Thai Tyre Pyrolysis Company
- By TT News
- July 24, 2025
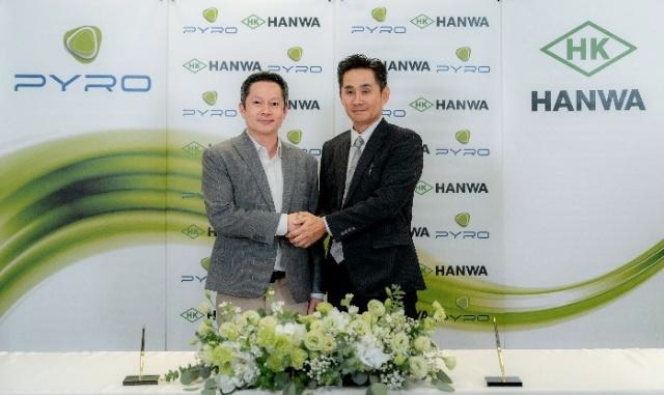
HANWA THAILAND CO., LTD., a subsidiary of Japan’s HANWA CO., LTD., has acquired a partial stake in PYRO ENERGIE CO., LTD., a Thailand-based company specialising in tyre pyrolysis recycling. This strategic move addresses the persistent global issue of end-of-life tyres and manufacturing defects, which often lead to environmental harm through illegal disposal or landfill accumulation. While HANWA Group already supplies tyre chips as an eco-friendly fuel source to Japanese industries, pyrolysis has emerged as a preferred recycling solution in global markets.
The pyrolysis process thermally decomposes waste tyres in an oxygen-deprived environment, yielding reusable materials like pyrolysis oil and carbon residue. These outputs serve as valuable fuel alternatives or raw materials for tyre production and other industrial uses, advancing decarbonisation goals. By partnering with PYRO, HANWA seeks to enhance the commercial viability of pyrolysis-derived products and establish an international supply chain in cooperation with tyre manufacturers. The resulting materials will support the chemical, synthetic rubber and tyre industries, promoting a circular economy.
Both HANWA and HANWA THAILAND hold ‘ISCC PLUS’ and ‘ISCC EU’ certifications, underscoring their commitment to sustainable practices. The group remains dedicated to expanding its portfolio of certified recycled and biomass products, reinforcing its role in building a decarbonised future.
Ecolomondo Secures Quality Approval For rCB Produced At Its Hawkesbury TDP Facility
- By TT News
- July 24, 2025
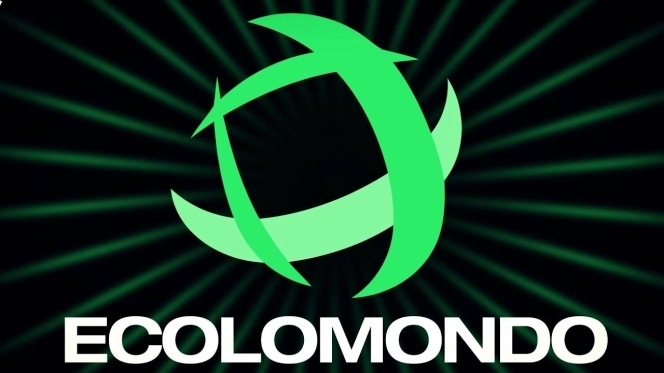
Ecolomondo Corporation, a Canadian leader in sustainable scrap tyre recycling, has achieved a significant milestone as its primary offtake client has officially approved the quality of the recovered carbon black (rCB) produced at its Hawkesbury Thermal Decomposition Process (TDP) facility. This approval follows the successful commissioning of new milling equipment and an rCB processing line, marking a critical step towards full-scale production.
To ensure compliance with stringent quality standards, Ecolomondo conducted extensive in-house testing using advanced laboratory equipment. Key parameters, including humidity, pellet size, pellet hardness, ash content and particle size, were meticulously evaluated. After confirming that all specifications were met, the company shipped rCB samples to offtake clients for independent verification. The clients’ test results aligned closely with Ecolomondo’s own findings, validating the material’s high quality.
In response to this successful validation, the primary offtake client placed an initial order for 23 metric tonnes of rCB, which Ecolomondo is preparing to ship immediately. At full operational capacity, the Hawkesbury facility is projected to recycle between 1.3 million and 1.5 million scrap tyres annually, yielding approximately 4,000 metric tonnes of rCB, 5,000 metric tonnes of pyrolysis oil, 2,000 metric tonnes of steel and 1,200 metric tonnes of process gas. This milestone underscores Ecolomondo’s leadership in sustainable tyre recycling and reinforces the commercial viability of its TDP technology.
Jean- François Labbé, Interim CEO of the Company, said, “The commercial acceptance of our rCB by offtake clients reflects the achievement of many years of technology development and commitment. It is a major achievement for the Company and we are confident that additional orders should come because of the quality of our rCB.”
CARBIOS Signs PET Recycling Deal With Indorama
- By TT News
- July 24, 2025
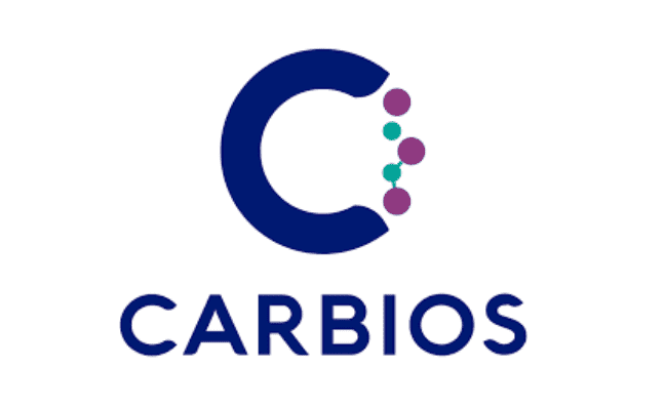
CARBIOS has signed a multi-year commercial agreement with Indorama Ventures, the world’s leading PET producer, to supply biorecycled monomers from its Longlaville plant. Indorama will repolymerise these monomers into r-PET filaments, which Michelin will then integrate into its tyre reinforcements.
Using its proprietary enzymatic recycling technology, CARBIOS will process complex PET waste into high-purity monomers at its new facility. Indorama will handle the conversion of these monomers into technical-grade filaments, enabling Michelin to enhance the sustainability of its tyres. This partnership accelerates the pre-commercialisation phase of CARBIOS’ industrial project, building on recent contracts with two major cosmetics brands for biorecycled PET.
The collaboration highlights the growing demand for circular solutions in manufacturing, with CARBIOS’ innovation playing a pivotal role in transforming waste into high-value materials. This milestone reinforces CARBIOS’ position as a leader in enzymatic recycling and supports Michelin’s commitment to sustainable mobility.
Vincent Kamel, CEO of CARBIOS, said, “This commercial agreement with Indorama Ventures marks a new step in the realisation of our industrial project. It confirms the trust of Indorama Ventures and Michelin in our PET biorecycling technology. Alongside the commercial successes already achieved in cosmetic packaging applications, this agreement illustrates our ability to deliver innovative solutions to the most demanding industries, particularly industrial filaments for tyre applications and, more broadly, textile.”
Fabien Gaboriaud, Director of Circularity and Renewable & Recycled Materials at Michelin Group, said, “This partnership is a tangible expression of our commitment to turning complex waste into high-performance materials. By integrating enzymatically recycled r-PET into our tyres, we are marking a new milestone on our journey toward achieving 100 percent renewable and recycled materials by 2050 — all while staying within planetary boundaries. It is by combining innovation, industrial excellence and close collaboration with trusted partners that we are building a strong and lasting circular model.”
Renato Boaventura, Global Market Head – Mobility at Indorama Ventures, said, “This alliance with both, CARBIOS and Michelin, underlines our commitment to plan ahead and take a leading role in shifting the industry towards circularity.”
- Sinochem Group
- ESG Ratings
- Sinochem International
- Sinochem Equipment
- Shenyang Chemical
- Wind ESG Ratings
ESG Ratings Jump For Sinochem Group’s Listed Companies
- By TT News
- July 19, 2025
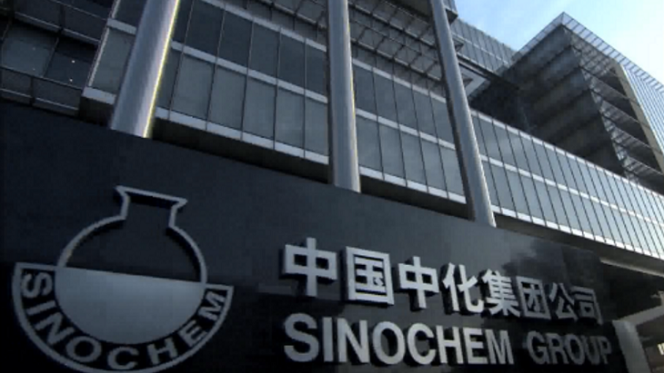
Wind, a leading financial data provider, has released its 2025 ESG (Environmental, Social and Governance) ratings, showcasing notable improvements for several listed companies under Sinochem Group. The ratings reflect these companies' strong commitment to sustainable development and corporate responsibility.
Sinochem International achieved an AA rating in 2025, a significant improvement from its previous rating in 2024. With a comprehensive score of 8.56 out of 10, the company now holds the highest ESG rating in the diversified industrial sector, setting a new record among Sinochem Group’s listed companies. Sinochem Equipment and Shenyang Chemical also demonstrated substantial progress, with both companies upgrading from a BBB rating in 2024 to an A rating in 2025. These improvements underscore the group-wide advancements in sustainability practices.
The upgrades highlight Sinochem Group’s intensified focus on sustainability initiatives, including enhanced environmental compliance, green transition efforts, stronger corporate governance and improved transparency. Additionally, the companies have made strides in social responsibility programmes, such as worker welfare and community engagement.
The ESG rating jumps for Sinochem International, Sinochem Equipment and Shenyang Chemical underscore Sinochem Group’s leadership in sustainable business practices. As China continues to push for carbon neutrality and ESG integration, these companies are well-positioned for long-term growth and resilience.
Comments (0)
ADD COMMENT