Evonik Forms Smart Effects Unit by Merging Silica, Silane Lines
- By TT News
- January 28, 2025
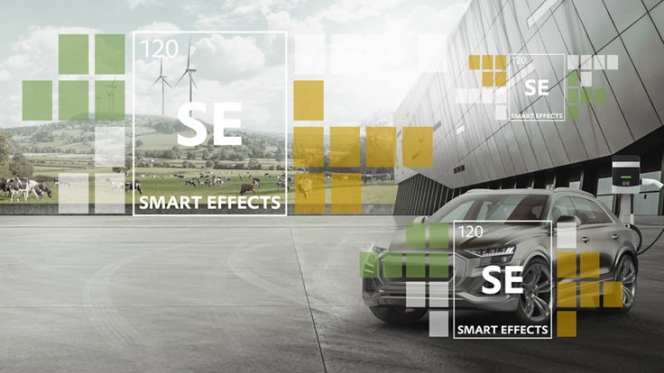
Evonik Industries AG launched Smart Effects, a new 3,500-employee entity combining its silica and silane operations, as the German speciality chemicals maker pushes further into sustainable technologies.
According to a company statement, the unit began operations on 1January, will be part of the company’s Advanced Technologies division and target the automotive, electronics, consumer health, and building materials markets.
“This merger not only enhances our customer relationships but also allows us to advance sustainability in key markets,” said Emmanuel Auer, who heads the Smart Effects business line.
The combined unit will supply materials for electric vehicle batteries and semiconductors while developing new technologies, such as adsorbents for direct air capture of carbon dioxide. Its silica-silane combinations are already used in fuel-efficient “green” tyres.
“The new business line is a strategic step by Evonik to strengthen the financing power of our complementary Silanes, precipitated and fumed Silica technology platforms,” stated Lauren Kjeldsen, President of Smart Materials Division at Evonik. “By combining our expertise in molecular silane chemistry and silica particle design, we can deliver differentiated solutions that add value to our customers with a tailored portfolio approach.”
“With Smart Effects, we aim to go beyond in industry,” Auer concluded. “Our goal is to deliver value for our customers by innovative, complementary technologies based on molecules and particles, driven by circular solutions and sustainable effects in applications.”
Smart Effects will maintain local sales teams and tech centers serving customers in over 100 countries, supported by manufacturing facilities across six continents, the company said. The merger aims to streamline innovation in joint applications and technical processes.
Evonik developed surface-modified silica carriers with amino silanes that can extract CO2 from the atmosphere as part of its sustainability push. The company said the new structure will help accelerate similar innovations targeting environmental challenges.
- Covestro
- Flame-Retardant Encapsulation Foam
- Flame-Retardant Foam
- Polyurethane Foam
- Baysafe BEF
- Electric Vehicles Traction Battery Safety Requirements
- EV Battery
Covestro Enhances EV Battery Safety With New Flame-Retardant Encapsulation Foam
- By TT News
- July 17, 2025
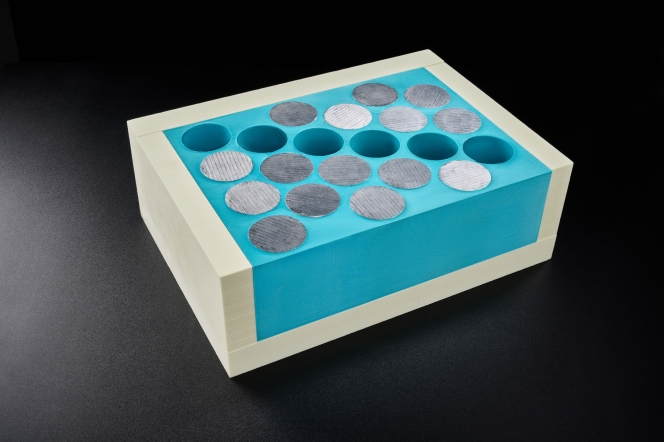
Covestro has introduced its next-generation Baysafe BEF flame-retardant polyurethane foam, a breakthrough in EV battery safety. Designed to prevent thermal runaway propagation between cells, this lightweight foam meets stringent global safety demands, particularly in China, where the new GB 38031-2025 standard will require fireproof batteries from 2026.
As the world’s largest EV market, China’s regulations are expected to influence global standards, making Covestro’s innovation critical for automakers. The foam’s superior flame resistance enhances safety in EVs, e-bikes and portable energy storage, addressing a key consumer concern. By combining cutting-edge flame-retardant technology with lightweight performance, the Baysafe BEF series helps drive the transition to sustainable transportation and energy storage worldwide.
With EV adoption accelerating, Covestro’s material solutions support manufacturers in meeting stricter safety requirements while enabling international expansion. Beyond encapsulation, the company offers polyurethane-based battery covers and shock-absorbing components, strengthening its position in the fast-growing new energy sector.
Akhil Singhania, Global Head of PU Specialties in Covestro’s Tailored Urethanes Business Entity, said, “This innovation represents a significant step towards enabling sustainable mobility through enhanced safety. By launching our advanced flame-retardant technology, Covestro reaffirms its commitment to innovation and strengthens our product portfolio to meet the evolving needs of the EV industry.”
Zeon Develops Hydrophilic SBR For Winter Tyres
- By TT News
- July 16, 2025
Zeon Corporation has announced the development of Nipol BR1300, a novel hydrophilic styrene butadiene rubber (SBR) for winter tyres. Synthesised with a polybutadiene rubber base, the material delivers unprecedented hydrophilicity for tyre applications. Commercial production began in May 2025 at Zeon’s Tokuyama plant in Yamaguchi Prefecture.
As part of its strategic portfolio optimization, Zeon plans to phase out low-profitability products like ESBR-1 and NBR latex by 2026. However, it will continue manufacturing high-margin products, including ESBR-2, nitrile butadiene rubber and solution SBR. This shift underscores Zeon’s focus on advanced, value-driven rubber solutions.
- Covestro India
- CSIR-National Chemical Laboratory
- Circular Economy
- Polyurethane Waste
- Polyurethane Recycling
Covestro India Partners With CSIR-NCL To Pioneer Polyurethane Upcycling Solutions
- By TT News
- July 16, 2025
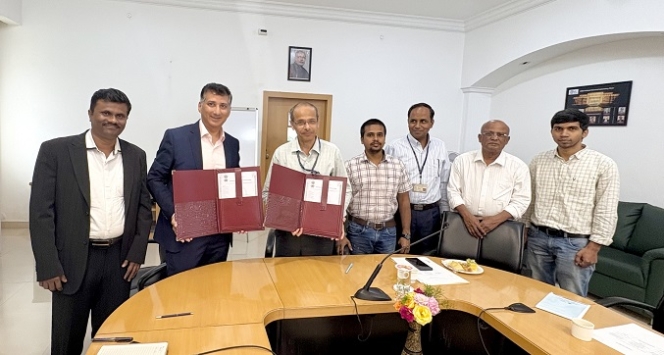
Covestro India has entered into a strategic collaboration with CSIR-National Chemical Laboratory (NCL) through an innovative CSR initiative focused on developing sustainable upcycling technologies for polyurethane waste. This partnership aims to overcome existing recycling limitations by transforming discarded polyurethane materials into valuable chemical feedstocks, potentially revolutionising the material's circular economy.
This collaboration underscores both organisations' commitment to environmental innovation, leveraging NCL's advanced research infrastructure and Covestro's market leadership to address critical gaps in plastic circularity. Current polyurethane recycling methods, predominantly mechanical with some emerging chemical processes, face substantial challenges including material degradation, high energy consumption and hazardous byproduct generation. The project seeks to develop commercially viable chemical recycling solutions that maintain material integrity while minimising environmental impact.
Polyurethanes, widely used in furniture, automotive parts and insulation, present unique recycling difficulties due to their complex molecular structure. Most end up in landfills after use, creating significant sustainability challenges. By combining Covestro's industrial expertise with NCL's seven decades of chemical research excellence, the partnership aims to create breakthrough upcycling technologies.
Avinash Bagdi, Director & Head of Sales & MD Solutions India & Projects – Tailored Urethanes, said, "This partnership strengthens our commitment to finding innovative solutions for polyurethane waste and directly supports Covestro's vision of becoming fully circular. By developing effective methods to upcycle polyurethanes, we're taking concrete steps towards creating a more sustainable future in line with our corporate vision of driving the transition to a circular economy."
Dr Ashish Lele, Director of NCL, said, "CSIR-National Chemical Laboratory is excited to partner with Covestro (India) in this groundbreaking initiative to develop novel chemical upcycling methods for polyurethane waste. The conventional and electrochemical strategies we're developing address the critical limitations of current recycling technologies and align perfectly with our shared vision of a circular economy. This collaboration represents a significant step towards sustainable plastic management in India and globally, with potential to transform polyurethane waste into valuable chemical resources."
Zeon Starts Construction Of Bench-Scale Facility For Sustainable Butadiene Production
- By TT News
- July 11, 2025
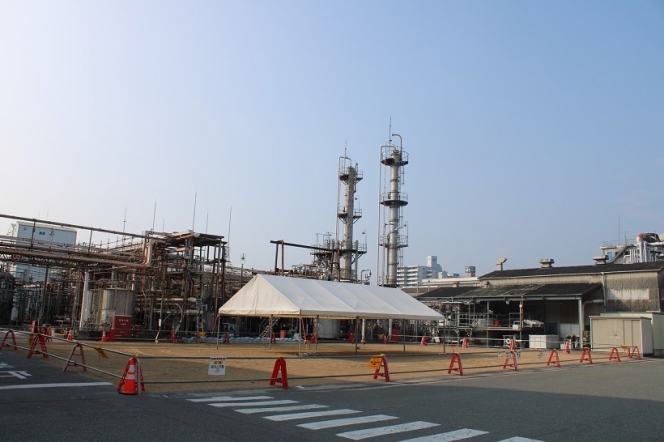
Zeon Corporation has begun building a pilot facility at its Tokuyama Plant in Shunan City, Yamaguchi Prefecture, to test a new method for efficiently producing butadiene from plant-derived ethanol. The demonstration plant, expected to start operations in 2026, will supply butadiene for manufacturing trial batches of polybutadiene rubber, bringing the company closer to commercialising this sustainable production process.
This project is a key part of a joint initiative between Zeon and The Yokohama Rubber Co., Ltd. to develop eco-friendly methods for producing butadiene and isoprene from renewable sources, with full-scale adoption targeted for the 2030s. Under the collaboration, Zeon will produce butadiene rubber at the new facility, while Yokohama Rubber will use the material to create experimental tyres and conduct performance testing. The data collected will help refine the technology ahead of larger-scale trials. The companies aim to finalise the production process by 2030 using an expanded pilot plant, with plans for industrial-scale commercialisation by 2034.
A ceremonial groundbreaking event took place on 10 July 2025, with 33 attendees, including local government officials from Yamaguchi Prefecture and Shunan City, construction partners and Zeon executives such as Chairman Kimiaki Tanaka and Tokuyama Plant Manager Akira Honma. The gathering included traditional safety prayers for the construction phase, marking the official start of this sustainability-focused industrial project.
Comments (0)
ADD COMMENT