JSR Corporation has been supplying an extensive range of products such as synthetic rubbers for car tyres, thermoplastic elastomers with the characteristics of both elastomers and plastics, and latex for paper coating. As part of its mid-term business plan “JSR20i9,” which started in April 2017, JSR Corporation is strengthening competitiveness for the future. It focuses on earnings drivers and profit expansion in SSBR, semiconductor materials and the Life Sciences Business.
The CASE mobility will influence the entire eco-system of the tyre industry. Requirements of tyres for the CASE mobility will be different from today, and raw material suppliers are now pushing themselves meet future demand. The tyres for the new mobility are expected to have high strength, wear resistance, with reduction of emissions. To meet these needs, the company used its proprietary synthesis technology to develop the new SBR with significantly improved mechanical strength compared to conventional SBR. The new hydrogenated SSBR combines JSR’s unique polymerisation and hydrogenation technologies to control the number of unsaturated bonds in the material. “Through this process, it is possible to optimise the interactions among polymer molecules and minimise the stress produced in crosslinking. As a result, this new SBR has, not only approximately two times the mechanical strength of conventional SBR, but also exceeds the strength of natural rubber. Tyres using this new SBR as the tread compound rubber demonstrate more than 50 per cent better wear resistance along with low fuel consumption and grip performance compared to conventional SBR-equipped tyres,” said the company.
“In the CASE, EV vehicle is heavier, that could also lead to higher abrasion that causes rubber microparticles pollution. This is the reason we are focusing on abrasion resistance in our polymer,’’ said Arai. Constant exposure to sunlight could reason for degradation of tyres, but the new hydrogenated SSBR prevents it, and also reduce the microplastic said Arai.
Being in production of synthetic rubber over 60 years, JSR Corporation has been a significant supplier of synthetic rubber solutions to global tyre companies. Since JSR Corporation focuses on materials solutions, it has achieved a great deal of success with various tyres. JSR’s core technology is continuously improving polymerisation with its solid foundation of polymerisation technology, and the company’s polymer design already meets a wide variety of customer needs.
The company believes in speedy development and mass production. JSR works closely with its Tire Materials Technology Development Center at its Yokkaichi Plant to develop polymers, processes and establish mass-production technologies. It applies digital techniques for research and development and mass production technologies and utilises AI and big data to tackle improvements in speed and efficiency and achieve stable quality and mass production. With technologically tailored solutions proposals, tyre manufacturers reduce tyre development time.
In the design and development analysis technologies, JSR uses its high-level analysis technologies to design and develop optimised materials tailored to each type of rubber compound.
Demand for low resistance tyres is growing by 10% every year, and JSR intends to cater to the demand with its functionalised SSBR solutions. According to Keisuke Miyoshi, managing director, JSR Elastomer Europe GmbH said, “The company provides the functionalised Solution SSBR that provides cutting edge technology and low rolling resistance. We plan to cater to the growing demand for low rolling resistance tyres across the globe. To cater to the growing demand for low rolling resistance tyres, the company has increased its production capacities of SSBR with plants in Japan, Thailand and Hungary.”
The total capacity of SSBR is around 220KT.
Being a supplier of a wide range of synthetic rubber solutions, JSR is into the production of a wide range of SSBR, from 1st generation to 5th generation. “Depending on the customer’s demand, we can supply different generation polymers,” said Miyoshi.
With its presence around the globe, JSR focuses on making products needed for the local requirement. The company runs a continuous product development programme based on its close communication with its customers globally. “Japanese automakers are known for making fuel-efficient vehicles, and the same performance is also expected from tyre companies. While European automakers the required strong tyres, we leverage our technical expertise to make products suitable for the respective markets,” said Miyoshi.
JSR produces SSBR at three production sites, in Japan, Thailand and Hungary, which gives the company a unique logistical flexibility to support the global tyre industry. “We are the only synthetic rubber company which is spread globally in terms of synthetic rubber production and that gives us an edge over all our competitors. Customers may not find any difference in quality. Our strategic presence helps us to be more efficient in supplying products and service,” said Miyoshi
With six sales and technical offices in all major markets, the company promptly responds to tyre manufacturer requests timely
- Covestro
- Flame-Retardant Encapsulation Foam
- Flame-Retardant Foam
- Polyurethane Foam
- Baysafe BEF
- Electric Vehicles Traction Battery Safety Requirements
- EV Battery
Covestro Enhances EV Battery Safety With New Flame-Retardant Encapsulation Foam
- By TT News
- July 17, 2025
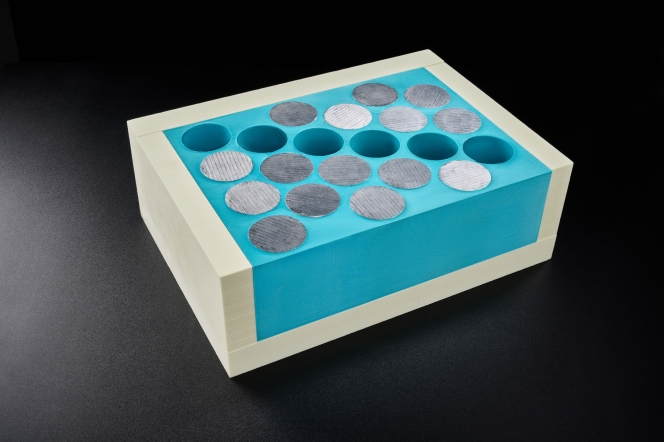
Covestro has introduced its next-generation Baysafe BEF flame-retardant polyurethane foam, a breakthrough in EV battery safety. Designed to prevent thermal runaway propagation between cells, this lightweight foam meets stringent global safety demands, particularly in China, where the new GB 38031-2025 standard will require fireproof batteries from 2026.
As the world’s largest EV market, China’s regulations are expected to influence global standards, making Covestro’s innovation critical for automakers. The foam’s superior flame resistance enhances safety in EVs, e-bikes and portable energy storage, addressing a key consumer concern. By combining cutting-edge flame-retardant technology with lightweight performance, the Baysafe BEF series helps drive the transition to sustainable transportation and energy storage worldwide.
With EV adoption accelerating, Covestro’s material solutions support manufacturers in meeting stricter safety requirements while enabling international expansion. Beyond encapsulation, the company offers polyurethane-based battery covers and shock-absorbing components, strengthening its position in the fast-growing new energy sector.
Akhil Singhania, Global Head of PU Specialties in Covestro’s Tailored Urethanes Business Entity, said, “This innovation represents a significant step towards enabling sustainable mobility through enhanced safety. By launching our advanced flame-retardant technology, Covestro reaffirms its commitment to innovation and strengthens our product portfolio to meet the evolving needs of the EV industry.”
Zeon Develops Hydrophilic SBR For Winter Tyres
- By TT News
- July 16, 2025
Zeon Corporation has announced the development of Nipol BR1300, a novel hydrophilic styrene butadiene rubber (SBR) for winter tyres. Synthesised with a polybutadiene rubber base, the material delivers unprecedented hydrophilicity for tyre applications. Commercial production began in May 2025 at Zeon’s Tokuyama plant in Yamaguchi Prefecture.
As part of its strategic portfolio optimization, Zeon plans to phase out low-profitability products like ESBR-1 and NBR latex by 2026. However, it will continue manufacturing high-margin products, including ESBR-2, nitrile butadiene rubber and solution SBR. This shift underscores Zeon’s focus on advanced, value-driven rubber solutions.
- Covestro India
- CSIR-National Chemical Laboratory
- Circular Economy
- Polyurethane Waste
- Polyurethane Recycling
Covestro India Partners With CSIR-NCL To Pioneer Polyurethane Upcycling Solutions
- By TT News
- July 16, 2025
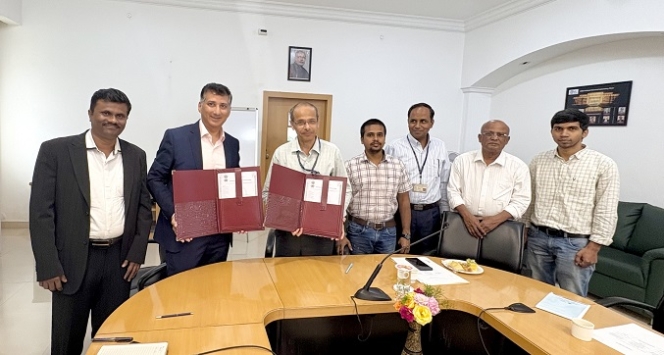
Covestro India has entered into a strategic collaboration with CSIR-National Chemical Laboratory (NCL) through an innovative CSR initiative focused on developing sustainable upcycling technologies for polyurethane waste. This partnership aims to overcome existing recycling limitations by transforming discarded polyurethane materials into valuable chemical feedstocks, potentially revolutionising the material's circular economy.
This collaboration underscores both organisations' commitment to environmental innovation, leveraging NCL's advanced research infrastructure and Covestro's market leadership to address critical gaps in plastic circularity. Current polyurethane recycling methods, predominantly mechanical with some emerging chemical processes, face substantial challenges including material degradation, high energy consumption and hazardous byproduct generation. The project seeks to develop commercially viable chemical recycling solutions that maintain material integrity while minimising environmental impact.
Polyurethanes, widely used in furniture, automotive parts and insulation, present unique recycling difficulties due to their complex molecular structure. Most end up in landfills after use, creating significant sustainability challenges. By combining Covestro's industrial expertise with NCL's seven decades of chemical research excellence, the partnership aims to create breakthrough upcycling technologies.
Avinash Bagdi, Director & Head of Sales & MD Solutions India & Projects – Tailored Urethanes, said, "This partnership strengthens our commitment to finding innovative solutions for polyurethane waste and directly supports Covestro's vision of becoming fully circular. By developing effective methods to upcycle polyurethanes, we're taking concrete steps towards creating a more sustainable future in line with our corporate vision of driving the transition to a circular economy."
Dr Ashish Lele, Director of NCL, said, "CSIR-National Chemical Laboratory is excited to partner with Covestro (India) in this groundbreaking initiative to develop novel chemical upcycling methods for polyurethane waste. The conventional and electrochemical strategies we're developing address the critical limitations of current recycling technologies and align perfectly with our shared vision of a circular economy. This collaboration represents a significant step towards sustainable plastic management in India and globally, with potential to transform polyurethane waste into valuable chemical resources."
Zeon Starts Construction Of Bench-Scale Facility For Sustainable Butadiene Production
- By TT News
- July 11, 2025
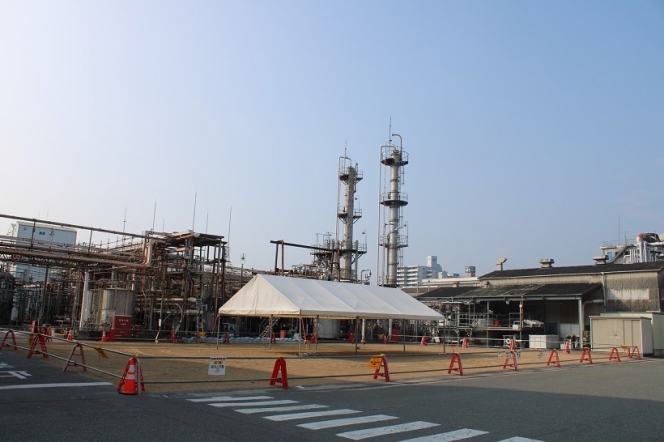
Zeon Corporation has begun building a pilot facility at its Tokuyama Plant in Shunan City, Yamaguchi Prefecture, to test a new method for efficiently producing butadiene from plant-derived ethanol. The demonstration plant, expected to start operations in 2026, will supply butadiene for manufacturing trial batches of polybutadiene rubber, bringing the company closer to commercialising this sustainable production process.
This project is a key part of a joint initiative between Zeon and The Yokohama Rubber Co., Ltd. to develop eco-friendly methods for producing butadiene and isoprene from renewable sources, with full-scale adoption targeted for the 2030s. Under the collaboration, Zeon will produce butadiene rubber at the new facility, while Yokohama Rubber will use the material to create experimental tyres and conduct performance testing. The data collected will help refine the technology ahead of larger-scale trials. The companies aim to finalise the production process by 2030 using an expanded pilot plant, with plans for industrial-scale commercialisation by 2034.
A ceremonial groundbreaking event took place on 10 July 2025, with 33 attendees, including local government officials from Yamaguchi Prefecture and Shunan City, construction partners and Zeon executives such as Chairman Kimiaki Tanaka and Tokuyama Plant Manager Akira Honma. The gathering included traditional safety prayers for the construction phase, marking the official start of this sustainability-focused industrial project.
Comments (0)
ADD COMMENT