PHYSICS BEHIND RUBBER TRIBOLOGY
- By 0
- May 04, 2020
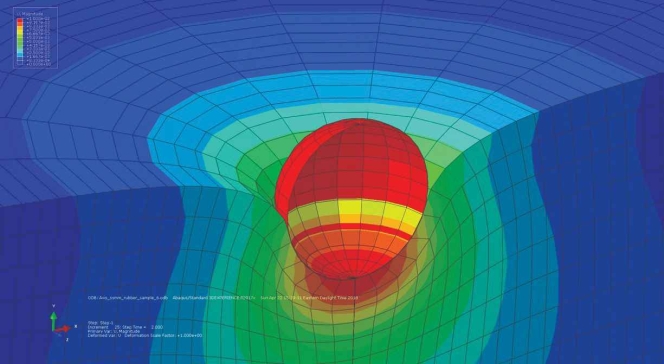
By Sunish Vadakkeveetil, Mehran Shams Kondori, and Saied Taheri
Center for Tire Research (CenTiRe), Virginia Tech
Rubber, mainly because of its viscous nature, is a widely used material for most contact applications such as, seals, tyres, footwear, wiper blades, bushings etc. The material possesses the property of both a liquid (viscous) and a solid (elastic). Hence, rubber frictional losses at the contact interface is classified into three mechanisms as shown in Figure 1. Hysteresis (μ_hys ) – Energy dissipated due to internal damping of rubber caused by undulation in the surface. Adhesion (μ_adh ) – Due to intermolecular or Vander Waals attraction at the contact interface. It vanishes in the presence of contaminants or lubricants on the surface. Viscous (μ_visc ) – Due to hydrodynamic resistance caused by the fluid in the contact interface. It mainly occurs under the presence of lubricant or fluid in between the contact interface.



Friction as a concept has evolved, as shown in Figure 2 from a simple empirical relation, developed by Amonton’s (1699) and Columb (1785) to more complex representations by considering these different mechanisms of friction. Initial experimental observations by Bowden and Tabor [1] observed the microscopic behaviour of the contact and obtained that the real area of contact is only a part of the nominal contact area. Grosch & Schallamach [2] performed experimental observation to determine the influential factors and obtain a relation between temperature and velocity-dependent friction to frequency-dependent viscoelastic behaviour. Savkoor[3] considers the frictional losses due to adhesive mechanism at the contact interface using a rudimentary theory where the interaction is considered as a series of processes from the growth of contact area in the initial stage to initiation and propagation of crack in the final stage.
Heinrich [4] developed an analytical representation to estimate the hysteretic component of friction by considering the energy losses at the contact interface to the internal damping of rubber from the undulations of the surface. The energy loss thus obtained is related to the frictional shear stress by the energy relation given by Eq. (2).
ΔE=∫d^3 x dt u ̇ . σ (1)
σ_f=ΔE/(A_0 v t) (2)
Persson and Klüppel [5] extended the theory to consider the effect of the surface roughness by assuming the surface to behave as a fractal nature and obtaining the total energy loss being the sum over the different length scales. Klüppel considers the GW theory to consider the contact mechanics where Persson developed a stochastic based contact mechanics theory assuming the rubber deformations to follow the surface asperities, the results are as shown in Figure 3. To consider the actual deformation profile of rubber, an affine transformation approach [6] is considered to obtain the actual deformation of rubber contact. The results are as shown in Figure 4.


In addition to analytical methods, computational approaches are also considered to estimate deformation behaviour of a rubber block on a rough substrate (Figure 5). The numerical model [7] is validated using indentation experiment and compared against a single asperity model as shown in Figure 6. This is later being extended to obtain friction and wear characteristics of rubber at the contact interface by considering the deformations at the contact interface and obtaining the frictional force [5], [8].



Figure 6: FE Model Of Single Asperity Model & Comparison Of Results With Experimental & Analytical Approach
Wear is mainly due to the frictional shear stress generated at the contact interface leads to energy dissipation at the rubber – substrate contact interface that is either transformed into heat or responsible for crack initiation and propagation eventually leading to material removal. The major contribution of the wear occurs either due to the interaction of smooth asperity and rubber surface (adhesive wear), Figure 7 (a) instantaneous tearing of rubber by sharp asperities (abrasive wear), Figure 7 (b) or due to repeated cyclic contact stress (fatigue wear, Figure 7 (c)).
Due to the importance and complexity of the wear problem, it has been a vital topic of interest studied by many researchers [2]. Numerical techniques and empirical approaches have seen their light in the midst of the expensive and cumbersome experimental observations [9], [10]. Archard’s law states that “the volume rate of wear (W) is proportional to the work done by the frictional forces” as given by Eq. (3), where τ_f is the frictional shear stress and v is sliding velocity.
W∝τ_f v (3)




In the case of road surfaces, the removal of rubber particles can be considered as a process of nucleation and propagation of crack like defects until it is detached to form a wear particle, as shown in Figure 8. Based on this mechanism of crack propagation, a physics-based theory assuming the crack propagates (Figure 9 & Figure 10) from already present defects or voids on the rubber surface was considered and then later compared with experimental methods performed using Dynamic Friction Tester (Figure 11) [6], [11], [12]. Future studies are being performed using analytical and computational approached to estimate the wear characteristics of a rubber material considering damage mechanics [8] and crack propagation theory considering the effect of surface roughness. An experimental technique is also being developed based on the Leonardo Da Vinci concept to experimental test the friction and wear characteristics of a rubber block under pure sliding.
References:
[1] D. Bowden, F. P., & Tabor, The friction and lubrication of solids. Oxford university press., 2001.
[2] A. Gent and J. Walter, The Pneumatic Tire, no. February. 2006.
[3] A. R. Savkoor, “Dry adhesive friction of elastomers: a study of the fundamental mechanical aspects,” 1987.
[4] H. Gert, “Hysteresis friction of sliding rubber on rough and fractal surfaces,” Pochvozn. i Agrokhimiya, vol. 25, no. 5, pp. 62–68, 1990.
[5] S. Vadakkeveetil, “Analytical Modeling for Sliding Friction of Rubber-Road Contact,” Virginia Tech, 2017.
[6] A. Emami and S. Taheri, “Investigation on Physics-based Multi-scale Modeling of Contact, Friction, and Wear in Viscoelastic Materials with Application in Rubber Compounds,” Virginia Tech, 2018.
[7] S. Vadakkeveetil, A. Nouri, and S. Taheri, “Comparison of Analytical Model for Contact Mechanics Parameters with Numerical Analysis and Experimental Results,” Tire Sci. Technol., p. tire.19.180198, May 2019.
[8] S. Vadakkeveetil and S. Taheri, “MULTI – LENGTH SCALE MODELING OF RUBBER TRIBOLOGY FOR TIRE APPLICATIONS,” Virginia Tech, 2019.
[9] K. R. Smith, R. H. Kennedy, and S. B. Knisley, “Prediction of Tire Profile Wear by Steady-state FEM,” Tire Sci. Technol., vol. 36, no. 4, pp. 290–303, 2008.
[10] B. W. and R. N. D. Stalnaker, J. Turner, D.Parekh, “Indoor Simulation of Tire Wear: Some Case Studies,” Tire Sci. Technol., vol. 24, no. 2, pp. 94–118, 1996.
[11] A. Emami, S. Khaleghian, C. Su, and S. Taheri, “Comparison of multiscale analytical model of friction and wear of viscoelastic materials with experiments,” in ASME International Mechanical Engineering Congress and Exposition, Proceedings (IMECE), 2017, vol. 9.
[12] M. Motamedi, C. Su, M. Craft, S. Taheri, and C. Sandu, “Development of a Laboratory Based Dynamic Friction Tester,” in ISTVS 7th Americas Regional Conference, 2013.
- Association of Natural Rubber Producing Countries
- ANRPC
- Monthly NR Statistical Report
- Natural Rubber
ANRPC Publishes Monthly NR Statistical Report For July 2025
- By TT News
- September 05, 2025
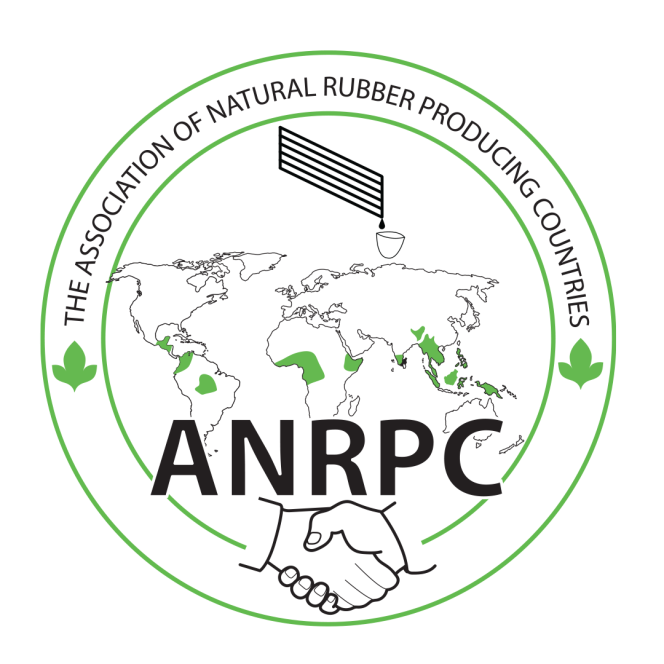
The Association of Natural Rubber Producing Countries (ANRPC) has released its Monthly NR Statistical Report for July 2025, providing an overview of key developments in the global natural rubber sector.
According to the report, natural rubber prices exhibited significant volatility in July. This instability was driven by a combination of adverse weather conditions impacting production, ongoing geopolitical tensions and international trade tariffs. After an initial phase of ample supply and muted demand, market sentiment shifted as concerns over potential supply disruptions prompted a notable increase in purchasing activity.
The report further projects a modest global production increase of 0.5 percent for 2025, while demand is anticipated to grow by a slightly higher 1.3 percent. However, this growth is expected against a challenging backdrop of a potential global economic slowdown. Complex US tariff policies and their widespread ripple effects are primary factors contributing to what may become one of the most subdued years for economic expansion since the pandemic.
Continental Pioneers Industrial-Scale Rubber Recycling With Advanced Pyrolysis
- By TT News
- September 03, 2025
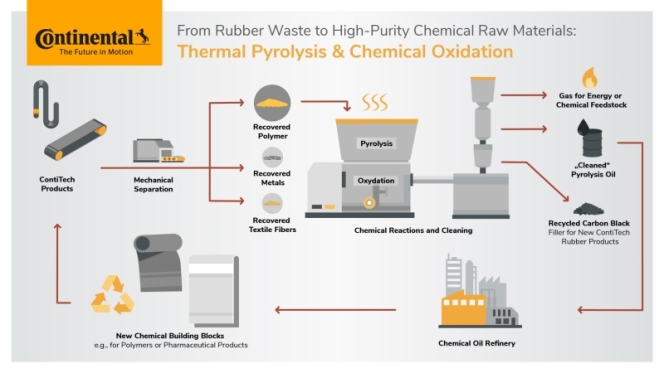
Continental is establishing a groundbreaking industrial process for recycling complex rubber waste through a strategic acquisition of key patents and the launch of a new pilot facility. This initiative, led by its ContiTech division, leverages advanced pyrolysis technology to transform end-of-life rubber products into valuable raw materials, creating a sustainable alternative to fossil resources.
The core of this innovation is a thermal decomposition process where waste rubber is heated in a low-oxygen environment. This breaks the material down into its core chemical constituents, one of which is a high-quality oil with properties mirroring traditional crude oil. This output is particularly significant as it can be directly used in the manufacture of new plastics and rubber goods, effectively closing the material loop.
A major historical obstacle for the industry has been the difficulty of recycling vulcanised rubber, whose altered chemical structure resists conventional separation methods. Pyrolysis successfully circumvents this challenge, cleanly decomposing the material to recover not only oil but also carbon black and other energy sources. The widespread adoption of pyrolysis has been hindered until now by the complexity of purifying its outputs to meet industrial standards. Continental’s new facility, originally developed by British start-up LowSulphurFuels, directly addresses this hurdle with a specialised purification process, making large-scale rubber recycling both technically feasible and economically attractive.
This advancement is especially critical for complex rubber products like composite hoses and specialised seals, which were previously nearly impossible to recycle efficiently. By converting this challenging waste stream into a high-grade resource, Continental is driving progress towards a circular economy. This move also reinforces the company's position as a leader in sustainable innovation, complementing its extensive patent portfolio and ongoing projects focused on material recovery and developing eco-friendly solutions for the automotive and industrial sectors.
Dr Michael Hofmann, Chief Technology Officer, ContiTech, said, “With this technology, we’re closing a crucial gap in the circular materials economy: we’re able to recover high-quality raw materials from rubber waste, which we can then feed back into the chemical material cycle to create new products without relying on crude oil. We’re thus demonstrating how innovation can become the driving force behind sustainable industrial processes – and how a previously untapped raw material cycle can be made economically viable.”
Zeon Board Approves Higher Budget For Cyclo Olefin Polymer Facility
- By TT News
- September 03, 2025
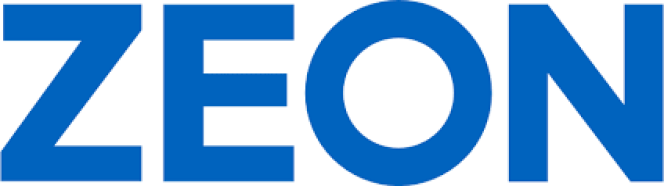
Following a resolution by its Board of Directors on 29 August 2025, Zeon Corporation has formally revised the total investment for its upcoming cyclo olefin polymer (COP) production plant. The new total investment is now projected to be approximately JPY 78.0 billion (approximately USD 525.70 million), a significant increase from the initial estimate of approximately YEN 70.0 billion (approximately USD 471.77 million) announced in June 2024.
This upward revision is attributed to anticipated increases across key construction areas, including rising costs for labour, raw materials and equipment. The updated financial framework incorporates both confirmed and projected cost escalations to ensure accurate budgeting. Zeon Corporation intends to fund the entire investment through a combination of internally generated capital and loans from financial institutions.
The new facility remains on schedule for completion in the first half of fiscal year 2028. Due to this timeline, the substantial investment is not expected to materially affect the company's consolidated financial results for the fiscal year ending 31 March 2026. The project is a central pillar of the company’s medium-term business strategy, identified as a major future growth driver.
The decision to proceed with the plant underscores the strong market outlook for Zeon’s cyclo olefin polymers. These advanced materials are prized for their superior optical clarity, extremely low water absorption and high purity. While already established in applications like optical films and lenses, demand is growing rapidly from the medical and semiconductor industries. By expanding its production capacity, Zeon aims to capitalise on this robust and expanding demand, thereby strengthening its market position and enhancing its corporate value over the medium to long term.
Kraton And International Paper Finalise Agreements For Operational Continuity In Savannah
- By TT News
- September 02, 2025
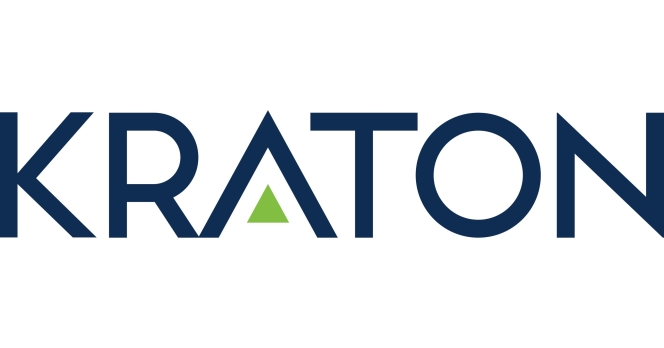
In a move to ensure operational continuity, Kraton Corporation has finalised service agreements with International Paper for its Savannah, Georgia facility. As a leading global producer of specialty polymers and biobased pine chemical products, Kraton will continue to receive essential site services from International Paper, a leader in sustainable packaging. This arrangement guarantees an uninterrupted production and supply of critical pine chemicals for the global market.
The agreements solidify both companies' shared commitment to reinforcing the pine chemicals value chain and providing reliable service to their customers. For Kraton, this partnership provides stability as it makes strategic infrastructure investments at the Savannah plant. These planned upgrades are designed to facilitate the site's long-term independent operations, supporting Kraton’s broader focus on business resilience and future growth. This initiative reinforces Kraton's position as a global leader in delivering high-performance, sustainable, bio-based solutions.
Minco van Breevoort, President, Kraton Pine Chemicals, said, “Securing this agreement reinforces our unwavering commitment to our customers and the pine chemicals industry. It’s business as usual. Our teams are fully aligned to ensure reliable operations, and this agreement provides continuity of supply to pine chemical markets as we invest in our long-term capabilities.”
Chris Roeder, Vice President and General Manager, Pine Chemicals and Low Carbon Solutions, International Paper, said, “We are pleased to renew and extend our partnership with Kraton. This arrangement confirms our long-standing relationship with Kraton and our commitment to being a reliable, long-term partner to Kraton and participant in the pine chemicals markets for years to come.”
Comments (0)
ADD COMMENT