Pyrum Secures Silver EcoVadis Sustainability Rating
- By TT News
- July 08, 2025
Pyrum Innovations AG has once again earned the prestigious EcoVadis silver medal for its sustainability efforts, achieving a score of 70 points – a 9-point increase from its previous rating. This places Pyrum among the top eight percent of companies evaluated in the ‘recovery of recyclable materials’ sector.
The EcoVadis assessment rigorously evaluates corporate sustainability across four key areas: environment, labour and human rights, ethics and sustainable procurement. Pyrum demonstrated notable progress in sustainable procurement, driven by enhancements to its quality and environmental management systems, now incorporating sustainability criteria, along with the implementation of new group-wide compliance policies. The recertification remains valid until June 2026.
Moving forward, Pyrum plans to intensify its focus on sustainability reporting, particularly in expanding CO₂ accounting and strengthening employee compliance awareness as part of its responsible corporate governance strategy. The company aims to refine existing processes while integrating ESG (environmental, social, governance) priorities to further advance its sustainability commitments.
Pascal Klein, CEO, Pyrum Innovations AG, said, “We are delighted to have once again been awarded the silver medal by EcoVadis and to have improved our rating. It confirms that we are on the right track. We are particularly proud that our new environmental and compliance guidelines are already having a positive impact. It also shows that our continuous efforts are not only bearing fruit within the company but are also being praised and recognised by our partners.”
CARBIOS Strikes Multi-Year Deal With Indorama Ventures For Tyre Textile Recycling
- By TT News
- August 07, 2025
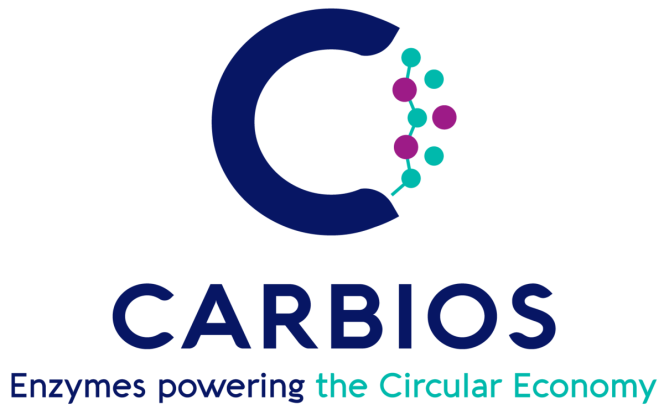
French biotech firm expands into industrial fabrics market through enzymatic PET recycling technology
French biotechnology company CARBIOS has signed a multi-year commercial agreement with Thailand's Indorama Ventures to supply recycled materials for tyre manufacturing, marking the firm's expansion into the industrial fabrics sector.
Under the deal, CARBIOS will provide biorecycled monomers from its planned Longlaville industrial plant to Indorama Ventures, the world's largest polyester producer. The Thai company will transform these materials into recycled polyethylene terephthalate (r-PET) filaments for use in tyre reinforcement by French tyre manufacturer Michelin.
The partnership represents CARBIOS's entry into a new market segment beyond its existing focus on cosmetic packaging applications. The company uses proprietary enzymatic recycling technology to break down complex PET waste into high-quality recycled materials.
"This commercial agreement with Indorama Ventures marks a new step in the realisation of our industrial project," said Vincent Kamel, chief executive of CARBIOS. "It confirms the trust of Indorama Ventures and Michelin in our PET biorecycling technology."
The deal comes weeks after CARBIOS signed its first sales contracts for biorecycled PET with two unnamed global cosmetics companies, as the firm builds momentum ahead of the commercial launch of its Longlaville facility.
Michelin, which has committed to using 100 percent renewable and recycled materials by 2050, said the partnership advances its circular economy objectives.
"This partnership is a tangible expression of our commitment to turning complex waste into high-performance materials," said Fabien Gaboriaud, director of circularity and renewable & recycled materials at Michelin Group. "By integrating enzymatically recycled r-PET into our tyres, we are marking a new milestone on our journey toward achieving 100 percent renewable and recycled materials by 2050."
Indorama Ventures, which generated $15.4 billion in revenue last year, said the alliance underscores its commitment to circular economy principles. The company employs approximately 25,000 people across manufacturing operations in Europe, Africa, the Americas, and Asia Pacific.
"This alliance with both, CARBIOS and Michelin, underlines our commitment to plan ahead and take a leading role in shifting the industry towards circularity," said Renato Boaventura, global market head mobility at Indorama Ventures.
CARBIOS, founded in 2011, has developed enzyme-based biological processes to break down plastics as part of efforts to prevent plastic pollution and accelerate the transition to a circular economy. The company operates an industrial demonstration plant for biorecycling that has been operational since 2021.
Construction of what the company describes as the world's first biorecycling plant is expected to resume in the second half of 2025, subject to securing additional funding.
Cabot Launches LITX 95F Conductive Carbon For Energy Storage Systems
- By TT News
- August 06, 2025
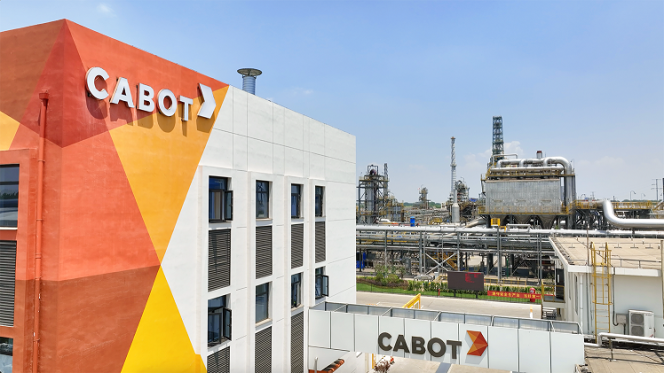
Cabot Corporation has launched LITX 95F, a high-performance conductive carbon additive designed for lithium-ion batteries in energy storage systems (ESS). Optimised for residential, commercial and industrial ESS applications, this advanced material enhances conductivity, extends cycle life and improves processability – critical for systems requiring durability under frequent charging and discharging.
With the global ESS market expanding due to renewable energy adoption and demand for grid stability, battery manufacturers need cost-effective, high-performance solutions. LITX 95F meets these needs by boosting energy density and cycle life while maintaining stability. Pouch cell tests with thick electrodes confirm its superior capacity retention, offering manufacturers greater flexibility in ESS design.
The material’s high-structure morphology strengthens conductivity and stability over repeated cycles. Additionally, its compatibility with thick cathode designs helps lower material costs without sacrificing performance. This innovation supports the growing ESS sector by enabling more efficient, reliable and scalable battery solutions.
Jeff Zhu, Executive Vice President and President, Carbon & Silica Technologies, Battery Materials and Asia Pacific Region, said, “As the global energy landscape continues to evolve, the ESS market requires advanced materials that deliver both performance and efficiency. Our new LITX 95F product is a direct response to the needs of the market and our battery customers – leveraging our deep industry expertise with proven performance to help scale ESS applications faster and more efficiently. This launch reflects our commitment to enabling a more sustainable future by delivering innovative solutions for battery technologies that support the energy transition at a global scale.”
- Association of Natural Rubber Producing Countries
- ANRPC
- Monthly NR Statistical Report
- Natural Rubber
ANRPC Publishes Monthly NR Statistical Report For June 2025
- By TT News
- August 06, 2025
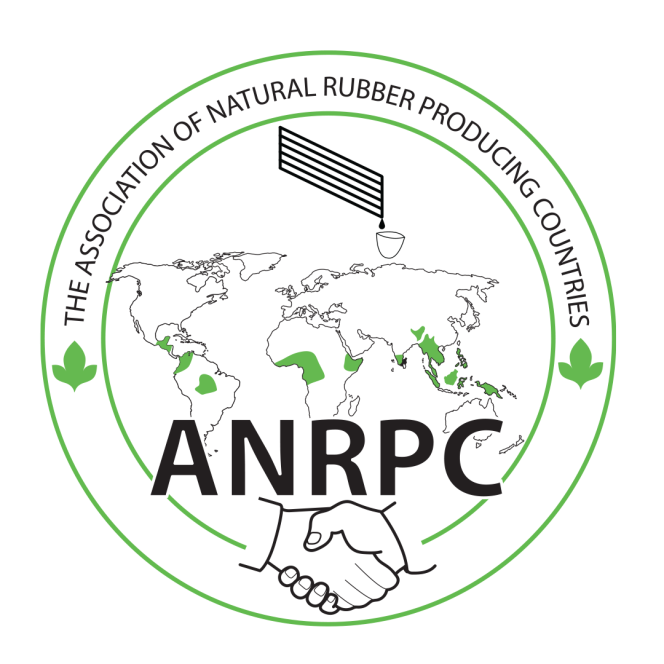
The Association of Natural Rubber Producing Countries (ANRPC) has released its Monthly NR Statistical Report for June 2025, providing an overview of key developments in the global natural rubber sector. The latest data indicates a sustained downward price trend, primarily driven by improving supply conditions in major producing nations, elevated stockpiles at key ports and ongoing trade policy uncertainties.
Market analysts attribute the bearish sentiment to a combination of factors, including increased output from leading rubber-producing countries and subdued industrial demand, particularly from tyre manufacturers. These conditions have contributed to mounting pressure on prices, with limited signs of immediate recovery. The ANRPC notes that while production levels remain stable, cautious demand projections persist due to broader macroeconomic concerns, including potential trade disruptions and slowing global economic growth.
Projections for 2025 suggest a modest 0.5 percent increase in worldwide natural rubber production compared to the previous year. Meanwhile, consumption is anticipated to grow by 1.3 percent, reflecting a slight but uneven recovery across key markets. However, analysts warn that external factors, such as shifting US tariff policies and weaker-than-expected industrial activity, could further dampen demand growth in the coming months.
Cabot To Acquire Bridgestone’s Mexico Carbon Manufacturing Facility
- By TT News
- August 05, 2025
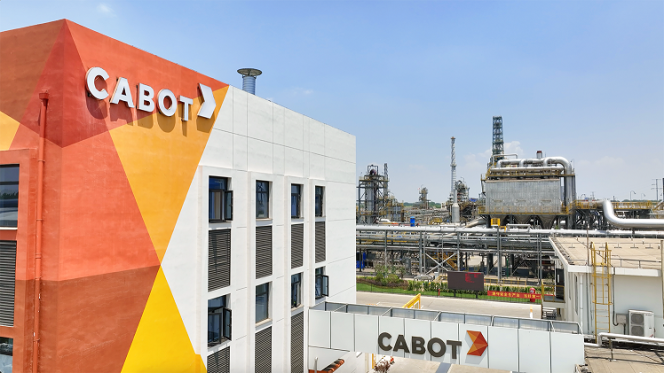
Cabot Corporation has signed a definitive agreement to purchase Mexico Carbon Manufacturing S.A. de C.V. (MXCB) from Bridgestone Corporation for USD 70 million on a debt-free, cash-free basis, pending standard closing adjustments. The deal, which requires regulatory approval in Mexico, is anticipated to finalise within three to six months.
The MXCB facility, established in 2005, produces reinforcing carbons and is strategically located near Cabot’s existing Altamira plant, operational since 1990. This acquisition reinforces Cabot’s partnership with Bridgestone, ensuring long-term supply of reinforcing carbon products while expanding Cabot’s production capacity and global footprint. The facility’s versatility allows for the manufacture of additional reinforcing carbon products, enabling Cabot to meet diverse customer demands and pursue future growth opportunities.
By integrating MXCB, Cabot strengthens its position as a leading global supplier of carbon black, reaffirming its commitment to delivering high-quality, reliable materials to key markets. Bridgestone’s decision to sell MXCB to Cabot reflects confidence in Cabot’s expertise and consistent performance as a trusted industry partner. This move aligns with Cabot’s long-term growth strategy and enhances its ability to serve customers worldwide.
Sean Keohane, President and CEO, Cabot Corporation, said, “We are excited to expand our global reinforcing carbons network and deepen our collaboration with Bridgestone. This acquisition aligns with our strategy to grow in core markets and reinforces our commitment to operational excellence, innovation and customer value. Our long-standing experience in the region and cultural alignment with the local team supports a smooth integration and long-term success. Importantly, this acquisition also further strengthens our position as a global leader in reinforcing carbons, enabling us to deliver innovative solutions and dependable supply to customers.”
Comments (0)
ADD COMMENT