Reducing Carbon Footprint through Rubber Cultivation
- By 0
- April 22, 2020
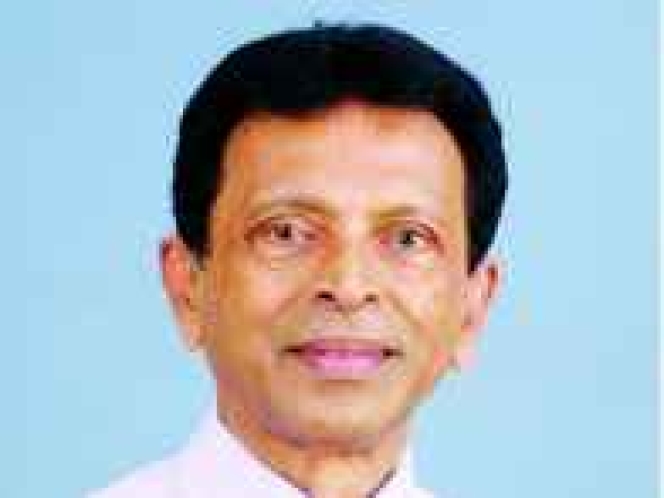
By Dr Sunil E Fernando
The natural rubber tree converts a greenhouse gas to a hydrocarbon. It is also capable of delivering it in commercially viable quantities almost on a daily basis, unlike any other. In addition, it retains some carbohydrates produced over a 30-year period, as medium density hardwood. This natural process of the biosynthesis of two products not only sustains the farmer, but also reduces the impact on global warming to some extent due to carbon dioxide extraction. Thus, preserving existing rubber plantations and cultivating more, especially in marginal lands, will help to mitigate an imbalance created due to the production of excessive quantities of a greenhouse gas
Benefits of Growing Rubber: Hevea brasiliensis or the rubber tree began its epic journey in 1875, when Sir Henry Wickham brought 70,000 seeds from Rio Tapajos in the upper Amazon to Kew gardens in London. Of these, 1911 seedlings were planted in Gampaha botanical gardens, Sri Lanka, initiating an agricultural revolution in South East Asia and an industrial revolution globally. Apart from giving 14 million tons of Natural Rubber (NR) consumed annually worldwide, the tree has other attributes listed below.
Extracting 24.9 kilograms of Carbon dioxide (CO2) Greenhouse gas (GHG) to produce one Kilogram of latex
Yielding 2.1 cubic meters/tree of wood from GHG as biomass, every 30-year cycle
Produce easily biodegradable litter, compared to monocultures like Teak
Require less chemical fertilisers, water and pesticides
Retains biodiversity as a tropical plant and co-exists with other species allowing for intercropping
The uniqueness of the rubber tree is its ability to fix CO2 almost instantaneously into a hydrocarbon on a daily basis, with water and energy from sunlight while nature took millions of years converting biomass to a hydrocarbon, Petroleum. The tree is a natural solar panel trapping energy from the Sun, propagating a chemical reaction giving a hydrocarbon, while releasing Oxygen to the atmosphere and accumulating a timber resource. Tapped from year 5, the tree removes a GHG every other day, unlike any other plant species, for 11 months of the year for 25 years.
Why Excess CO2 is bad
CO2 present in the atmosphere is a double-edged sword. "CO2-Earth" reports, its concentration increased from 330 ppm in 1975 to 408.55 in September 2019, and further to 410.27 in November 2019. CO2 absorbs Infrared radiation (heat radiation) from the Sun through molecular vibrations, and emit this energy unlike gases like Nitrogen and Oxygen. Ozone, Methane and Nitrous Oxide are other GHG's, which absorb energy from the sun and similarly emit heat, warming the atmosphere.
However, GHG's maintains atmospheric temperatures without converting Earth into an ice ball. Nevertheless, high concentration of GHG in atmosphere, emit more heat to sustain global warming due to an imbalance created by excessive human activity like burning fuel, rearing of cattle/sheep, giving-off excessive CO2 and Methane, respectively. Two confirmed methods to lower ill effects of GHG are, produce less and increase plant cover.
CO2 is the raw materials for all forms of Carbohydrates, Proteins and Fats produced by plants providing for growth and energy in life forms. What is alarming is the excess CO2 produced, accumulating in the atmosphere, and in Oceans. Dissolved CO2 in seawater, raises temperature and forms Carbonic acid, increasing Ocean acidification. Ocean acidification reduces the ability of sea creatures to fix Calcium as Calcium Carbonate, another form of Carbon sink.
Carbon Dioxide Accumulation Antoine Lavoisier said, in a chemical reaction matter is neither created nor destroyed. Producing GHG through human intervention, new matter is not created but it leads to an unsustainable imbalance of matter in the environment. This is what causes the problem.

Figure 1. Figure 1. Representation of the CO2 Cycle (https://serc.carleton.edu/eslabs/carbon/2a.html)
CO2 is a GHG not only produced by burning fuels and biomass. Humans exhale One Kilogram of it daily. Increase in population does not increase CO2, as exhaled balances out by inhaling. But when human population went up from 1 billion 200 years ago to 7 billion now, increase in human activity led to an imbalance in the atmosphere and the Oceans due to release of CO2 and Methane. Biomass generation too is dwindling due to the population pressure. Thus, this imbalance of accumulating matter capable of absorbing heat is the main reason for global warming.
Biosynthesis of Natural Rubber About 2000 plant species produce NR, but Hevea brasiliensis produce commercially exploitable dispersion in water as latex. The biological reason for NR production is not clear, but it may prevent pathogenic microorganisms entering the tree. Latex is found in horizontally arranged interconnected cells called laticifer, in the bark of the tree, High yielding plantations with about 400 trees per hectare have reported a production of 2500 Kg/NR /Year. The theoretical yield potential is estimated at, 7,000 to 10,000 kg/Ha/Year. A tree giving 15 to 30g of rubber per day, tapping on alternative days yields 2.2-4.5 Kg of NR per year. According to Apollo Vredestein R and D, on average 1.9 Kg of NR goes into a tire and a tree produces enough rubber to make 2 tires per year or 50 in lifetime.
Plants take in CO2 for survival. Some converts part into an edible form, as carbohydrate and fats while the rest is converted to forms like cellulose. These may end up as wood, becoming a Carbon sink for a length of time. In rubber trees, the process extends converting part of CO2 to a rubber hydrocarbon containing Carbon and Hydrogen, more akin to Petroleum. This wonder tree makes a hydrocarbon in few minutes, while nature took millions of years to convert biomass derived from CO2 to Petroleum.

and Non-MVA Pathways (Chiang. C. C. K, 2013, PhD Thesis,
the Graduate Faculty of the University of Akron).
The biosynthetic pathway for NR in Hevea begins with the monomer precursor, Isopentenyl pyrophosphate (IPP). IPP is an adduct of Pyrophosphoric acid and Isoprene monomer. However, IPP is not an uncommon material, limited to Hevea, but is formed from carbohydrates, in other plants, algae, bacteria, in mammals and humans. The formation of IPP is said to occur by following two pathways; Mevalonate (MVA) or non-mevalonate (non-MVA), deoxy-xylulose pathway. In rubber trees, breakdown products from carbohydrates like Pyruvates and Glyceraldehydes are transformed into IPP, in Cytosol in Cytoplasm/Plastids in plant cells, in several stages in the presence of many enzymes like mevalonate kinase (MVK) and mevalonate diphosphate decarboxylase (MVD). Figure 2.
Figure 2 Representation of the Formation of IPP through MVA and Non-MVA Pathways (Chiang. C. C. K, 2013, PhD Thesis, the Graduate Faculty of the University of Akron).
On isomerisation with enzyme, Isomerase IPP is converted to Dimethyl allyl pyrophosphate (DMPP). IPP and DMPP are building blocks for diverse groups of bio-molecules like Cholesterol, Vitamin K, Coenzyme Q10 (CoQ10) and Cis-polyisoprene (NR). Figure 3
Figure 3 Pathway to NR Biosynthesis

In rubber producing Russian dandelion (Taraxacum koksaghyz Rodin), enzyme transformation of sugars enrich NR formation. In the summer months, dandelions produce excess sugars and store it as Inulin. The possibility of metabolic engineering assisted enzyme degradation of Inulin to enhance production of IPP and then to NR has been explored for dandelion. Meanwhile Researchers have succeeded in decoding the Genome sequence in Hevea. This can lead to high yielding rubber clones, by locating genes responsible for biosynthesis of rubber.
Latex with 30% NR and 5% non-rubbers is produced in special cells called laticifers located horizontally and a lateral cut of the bark exposes most number, giving latex. Since the laticifer density is genotype dependant determining latex yield, it can give the direction for biologists as a selection marker for high yielding clones. In older rubber trees chemicals inducing Ethylene formation in the bark-tissue or generated it in situ like 2-Chloroethylphosphonic acid, are used as yield stimulants. Such developments, together with appropriate nutrition infusion, can increase NR yields, making rubber cultivation attractive to farmers.
Chloroethylphosphonic acid
Hevea brasiliensis is a dual-purpose tree, making Carbon sinks from CO2 in two ways, as a hydrocarbon and as wood, extracted in a 30-year cycle. Plants like wheat and rice also fix CO2 to give edible Carbohydrates, often twice a year. Nevertheless, human/animal consumption of edible carbohydrates quickly gives CO2 back to the environment. Thus with respect to environmental benefits, producing NR by growing rubber trees is a more favourable option. Fortunately, rubber cultivation has increased from 9.9 in 1975 to 14.0 million hectares in 2018 giving these benefits worldwide.
Preserving and enhancing rubber cultivation
The rubber farmer does a silent service by extracting latex and thus removing substantial quantity of GHG on a daily basis. As NR based products stay longer in service, Carbon in it remains intact for a longer period without burdening the environment. Each tree has the uncanny ability to function as a tap, working 150 days a year to clean up the environment unlike other plant-based options. It leaves a raw material as timber derived from GHG, extracted in every 30-year cycle giving 50 Kg of wood/tree. The global potential for wood at a replanting rate of 3% of acreage annually is, approx 7.30 Mn Tons/ year.
The environmental benefits can be maximised if the farmer taps the tree every other day for 11 months of the year if their livelihood is secularly safeguarded. Going into alternatives for from existing land is counterproductive to the environment. The negative process will occur only if the farmer finds the daily sustenance by growing rubber becomes a hard task. To encourage the farmer, requires a collective and a concerted effort from:
Buyers giving stable/reasonable price
Biologists developing fast growing, high yielding, drought and disease resistant trees
Cultivation experts developing new and less-laborious extraction techniques and attractive intercropping practices
Technologists adding value to existing NR products and developing new products
• Chemists by modification to give new elastomeric materials from NR as raw materials for other processes
• Environmentalists by increasing international awareness of the benefits of growing rubber
With respect to increased appreciation of the capability of modified NR forms, an enterprising tire manufacturer uses Epoxidised NR/Silica combination in automobile tire treads, to give higher wet grip and low rolling resistance tires. Such greener tires used in hybrid and electric cars, made these vehicles more environmental friendly. Olefinic elastomers like NR, contains reactive double bonds with potential to be modified as raw materials in many applications. Table 1, Figures 4 and 5. Such developments will give impetus to the sustainability and growth of an industry, benefitting the rubber farmer while fixing more GHG as well.

(Polgar. L.M, ‘Chemical modification of hydrocarbon elastomers, Progress in Polymer Science, 2016)

showing New Products Potential
(Polgar. L.M, ‘Chemical modification of hydrocarbon elastomers, Progress in Polymer Science, 2016)
ENDS
References:
1. Bhowmik. I (2006), Tripura Rubber Mission Technical Bulletin 2. https://www.co2.earth/
3. Rao. P. S, et.al (1998), Agricultural and Forest Meteorology 3, 90
4. Chiang. C. C. K (2013), Natural rubber biosynthesis, PhD Thesis, The Graduate Faculty of The University of Akron, USA 5. Decoding the rubber tree genome, https://www.sciencedaily.com/releases/2016/06/160624100225.htm
Dr Sunil E Fernando is Former Executive Director, DPL Group, Sri Lanka, Managing Director Dipped Products (Thailand) Limited, Former Director, DPL Plantations and Kelani Valley Plantations Limited, Sri Lanka, and a Consultant - Latex Products
- Covestro
- Flame-Retardant Encapsulation Foam
- Flame-Retardant Foam
- Polyurethane Foam
- Baysafe BEF
- Electric Vehicles Traction Battery Safety Requirements
- EV Battery
Covestro Enhances EV Battery Safety With New Flame-Retardant Encapsulation Foam
- By TT News
- July 17, 2025
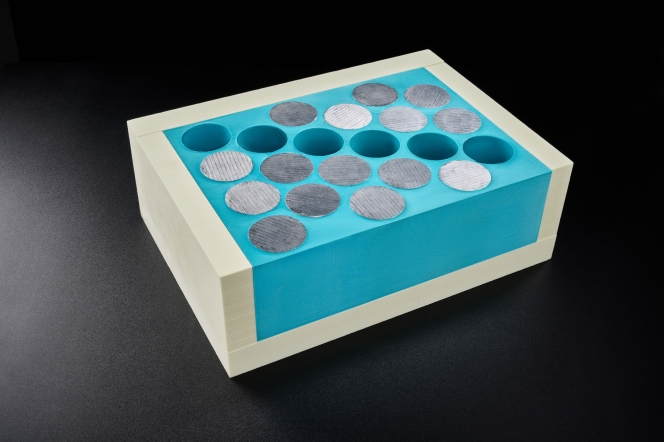
Covestro has introduced its next-generation Baysafe BEF flame-retardant polyurethane foam, a breakthrough in EV battery safety. Designed to prevent thermal runaway propagation between cells, this lightweight foam meets stringent global safety demands, particularly in China, where the new GB 38031-2025 standard will require fireproof batteries from 2026.
As the world’s largest EV market, China’s regulations are expected to influence global standards, making Covestro’s innovation critical for automakers. The foam’s superior flame resistance enhances safety in EVs, e-bikes and portable energy storage, addressing a key consumer concern. By combining cutting-edge flame-retardant technology with lightweight performance, the Baysafe BEF series helps drive the transition to sustainable transportation and energy storage worldwide.
With EV adoption accelerating, Covestro’s material solutions support manufacturers in meeting stricter safety requirements while enabling international expansion. Beyond encapsulation, the company offers polyurethane-based battery covers and shock-absorbing components, strengthening its position in the fast-growing new energy sector.
Akhil Singhania, Global Head of PU Specialties in Covestro’s Tailored Urethanes Business Entity, said, “This innovation represents a significant step towards enabling sustainable mobility through enhanced safety. By launching our advanced flame-retardant technology, Covestro reaffirms its commitment to innovation and strengthens our product portfolio to meet the evolving needs of the EV industry.”
Zeon Develops Hydrophilic SBR For Winter Tyres
- By TT News
- July 16, 2025
Zeon Corporation has announced the development of Nipol BR1300, a novel hydrophilic styrene butadiene rubber (SBR) for winter tyres. Synthesised with a polybutadiene rubber base, the material delivers unprecedented hydrophilicity for tyre applications. Commercial production began in May 2025 at Zeon’s Tokuyama plant in Yamaguchi Prefecture.
As part of its strategic portfolio optimization, Zeon plans to phase out low-profitability products like ESBR-1 and NBR latex by 2026. However, it will continue manufacturing high-margin products, including ESBR-2, nitrile butadiene rubber and solution SBR. This shift underscores Zeon’s focus on advanced, value-driven rubber solutions.
- Covestro India
- CSIR-National Chemical Laboratory
- Circular Economy
- Polyurethane Waste
- Polyurethane Recycling
Covestro India Partners With CSIR-NCL To Pioneer Polyurethane Upcycling Solutions
- By TT News
- July 16, 2025
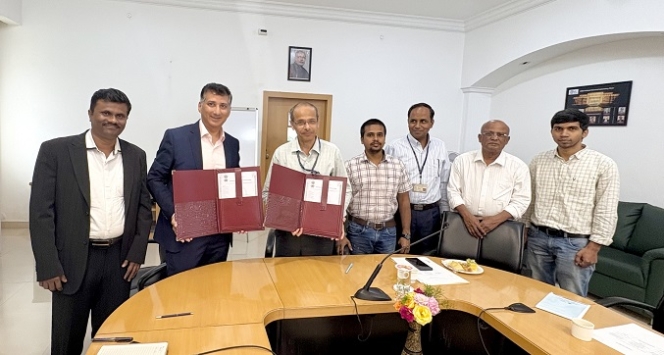
Covestro India has entered into a strategic collaboration with CSIR-National Chemical Laboratory (NCL) through an innovative CSR initiative focused on developing sustainable upcycling technologies for polyurethane waste. This partnership aims to overcome existing recycling limitations by transforming discarded polyurethane materials into valuable chemical feedstocks, potentially revolutionising the material's circular economy.
This collaboration underscores both organisations' commitment to environmental innovation, leveraging NCL's advanced research infrastructure and Covestro's market leadership to address critical gaps in plastic circularity. Current polyurethane recycling methods, predominantly mechanical with some emerging chemical processes, face substantial challenges including material degradation, high energy consumption and hazardous byproduct generation. The project seeks to develop commercially viable chemical recycling solutions that maintain material integrity while minimising environmental impact.
Polyurethanes, widely used in furniture, automotive parts and insulation, present unique recycling difficulties due to their complex molecular structure. Most end up in landfills after use, creating significant sustainability challenges. By combining Covestro's industrial expertise with NCL's seven decades of chemical research excellence, the partnership aims to create breakthrough upcycling technologies.
Avinash Bagdi, Director & Head of Sales & MD Solutions India & Projects – Tailored Urethanes, said, "This partnership strengthens our commitment to finding innovative solutions for polyurethane waste and directly supports Covestro's vision of becoming fully circular. By developing effective methods to upcycle polyurethanes, we're taking concrete steps towards creating a more sustainable future in line with our corporate vision of driving the transition to a circular economy."
Dr Ashish Lele, Director of NCL, said, "CSIR-National Chemical Laboratory is excited to partner with Covestro (India) in this groundbreaking initiative to develop novel chemical upcycling methods for polyurethane waste. The conventional and electrochemical strategies we're developing address the critical limitations of current recycling technologies and align perfectly with our shared vision of a circular economy. This collaboration represents a significant step towards sustainable plastic management in India and globally, with potential to transform polyurethane waste into valuable chemical resources."
Zeon Starts Construction Of Bench-Scale Facility For Sustainable Butadiene Production
- By TT News
- July 11, 2025
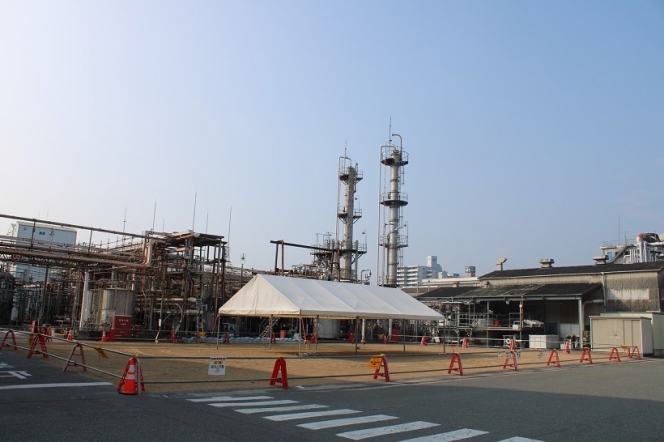
Zeon Corporation has begun building a pilot facility at its Tokuyama Plant in Shunan City, Yamaguchi Prefecture, to test a new method for efficiently producing butadiene from plant-derived ethanol. The demonstration plant, expected to start operations in 2026, will supply butadiene for manufacturing trial batches of polybutadiene rubber, bringing the company closer to commercialising this sustainable production process.
This project is a key part of a joint initiative between Zeon and The Yokohama Rubber Co., Ltd. to develop eco-friendly methods for producing butadiene and isoprene from renewable sources, with full-scale adoption targeted for the 2030s. Under the collaboration, Zeon will produce butadiene rubber at the new facility, while Yokohama Rubber will use the material to create experimental tyres and conduct performance testing. The data collected will help refine the technology ahead of larger-scale trials. The companies aim to finalise the production process by 2030 using an expanded pilot plant, with plans for industrial-scale commercialisation by 2034.
A ceremonial groundbreaking event took place on 10 July 2025, with 33 attendees, including local government officials from Yamaguchi Prefecture and Shunan City, construction partners and Zeon executives such as Chairman Kimiaki Tanaka and Tokuyama Plant Manager Akira Honma. The gathering included traditional safety prayers for the construction phase, marking the official start of this sustainability-focused industrial project.
Comments (0)
ADD COMMENT