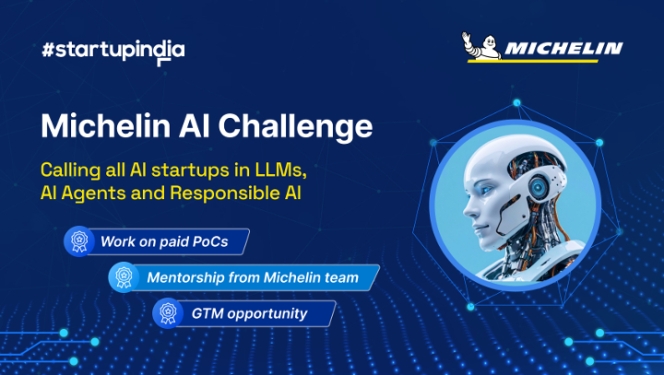
Michelin, one of the global leaders in tyre technology, announced a collaboration with the Department for Promotion of Industry and Internal Trade (DPIIT) to launch India’s first AI Startup Challenge. The initiative aims to propel innovation and entrepreneurship in the country’s manufacturing sector.
The challenge was unveiled in the presence of senior DPIIT officials, including Joint Secretary Sanjiv and Director Sumeet Kumar Jarangal. Dr Ambica Rajagopal, Group Chief Data and AI Officer, and Shantanu Deshpande, Managing Director of Michelin India, represented Michelin. A recorded address by DPIIT Secretary Rajesh Kumar Singh emphasised the programme’s significance.
Rajesh Kumar Singh, Secretary of DPIIT, said, “Michelin and Startup India, through the AI Challenge, invite Indian startups to co-build technical solutions using large language models for business use cases. The Michelin AI Startup Challenge offers opportunities to develop solutions in manufacturing, supply chain, operating software, and infrastructure, leveraging AI and robotics to enhance manufacturing processes, improve product quality, boost safety, and reduce defects. This initiative aims to create sustainable products and expose Indian talent to global contexts and clients. I encourage all DPIIT-recognised startups to apply for the programme and wish them the best.”
Sanjiv, Joint Secretary, DPIIT, highlighted the importance of public-private partnerships and the key role that manufacturing companies like Michelin play in bringing the right resources to help elevate the country’s entrepreneurial ecosystem. He also focused on the department’s commitment to empowering startups to scale their innovations and make a lasting impact on a global scale.
Sumeet Kumar Jarangal, Director, DPIIT, spoke about the importance of AI and the government’s focus on advanced manufacturing and automation. He congratulated the Michelin team for developing a programme completely synergistic with the nation’s vision.
The 12-week challenge, hosted on the Startup India portal, invites applications from leading Indian AI startups. Selected participants will receive mentorship and the opportunity to compete at a demo day in Delhi this September. The top eight finalists will pitch their solutions to a panel of judges from Startup India and Michelin India.
The top three startups will be awarded paid pilot projects with Michelin, valued at up to INR 5,00,000 each. Additionally, they will be eligible for long-term global contracts and incubation support from Michelin leadership. The challenge focuses on fostering AI-powered solutions in manufacturing, supply chain management, operational software, and infrastructure development.
Dr Ambica Rajagopal, Michelin Group Chief Data and AI Officer at Michelin India said, “There has never been a more exciting time for startups in the AI world, and we are delighted to contribute significantly to advancing India’s technology sector. It is a proud moment for us to strengthen our commitment to the AI industry in collaboration with the government’s visionary Startup India initiative.”
Commenting on this initiative, Shantanu Deshpande, Managing Director, Michelin India, stated, “At Michelin, we are committed to a greener future where sustainability and innovation are at the forefront of our efforts. We eagerly anticipate the participation of Indian startups in the AI challenge as we co-build global solutions together.”
The initiative will unfold in stages, beginning with outreach and application collection in July. Shortlisted startups will undergo mentorship until September, culminating in a final pitch event.
This 12-week AI Startup Challenge aims to find and support innovative startups in manufacturing. Top winners will receive mentorship, pilot projects, and incubation opportunities. This collaboration aims to bridge the gap between industries and startups, empowering them with AI to become global leaders.
Yokohama Rubber Recognised As Supplier Engagement Leader In CDP's 2024 Assessment
- By TT News
- August 01, 2025
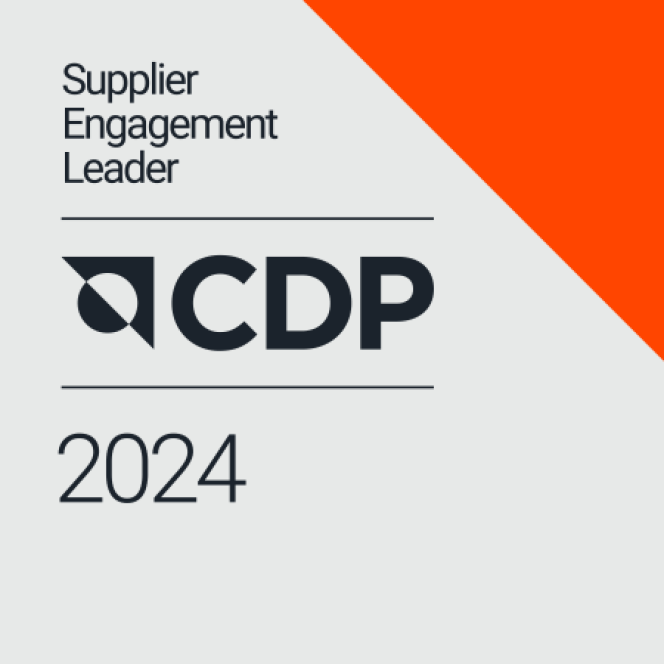
Yokohama Rubber Co., Ltd. has been recognised as a Supplier Engagement Leader in CDP's 2024 assessment, achieving the highest rating for its efforts in collaborating with suppliers to address climate change.
CDP, a global environmental nonprofit, evaluates companies based on governance, targets, Scope 3 emissions, risk management and supplier engagement. This marks Yokohama Rubber’s third consecutive year and sixth overall time receiving top honours in CDP’s climate change evaluation.
Committed to achieving net-zero CO₂ emissions from its operations by 2050, the company has actively worked to reduce its environmental impact across the supply chain. Since 2013, it has disclosed Scope 3 emissions and implemented the Yokohama Green Procurement Guidelines to encourage sustainable material sourcing. Through annual CSR briefings, Yokohama Rubber engages suppliers in its carbon neutrality initiatives, fostering cooperation to lower emissions throughout the supply chain.
Hankook Tire Publishes 2024-25 ESG Report
- By TT News
- August 01, 2025
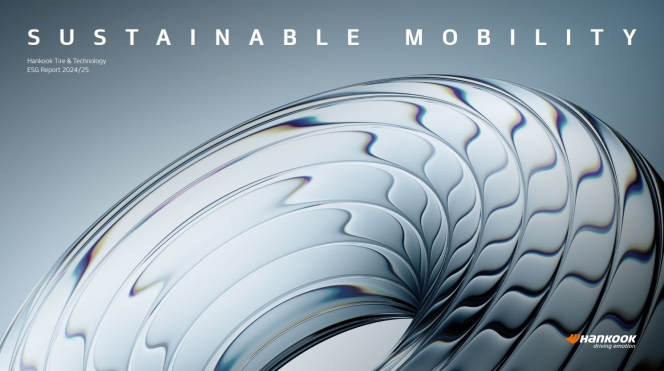
Hankook Tire has published its 16th annual ESG Report for 2024/25, detailing its sustainability achievements and future strategies aligned with its global ESG vision focused on Eco Value Chain, Sustainable Products and Responsible Engagement. The report adopts a comprehensive framework that evaluates social, environmental and financial impacts in line with the European Sustainability Reporting Standards (ESRS), emphasising enhanced biodiversity disclosures compliant with international guidelines like the TNFD.
Key focus areas include eight major management priorities such as climate action, resource efficiency, human rights and innovation. Hankook Tire is also strengthening its response to global ESG regulations, including the EU Deforestation Regulation (EUDR), through a dedicated committee overseeing natural rubber supply chain management.
To support sustainable growth, the company has an ESG Committee under its Board of Directors, operational since 2021. It is also driving circular economy initiatives, such as commercialising Korea’s first tyre using chemically recycled PET fibre and mass-producing EV tyres with 77 percent ISCC PLUS-certified sustainable materials.
Beyond environmental efforts, Hankook Tire engages in social initiatives, including biodiversity conservation, employee development and community partnerships. Its long-term commitment to sustainability dates back to 2009, with milestones like the 2018 sustainable rubber policy and the 2023 board performance evaluations to enhance governance transparency.
ZC Rubber Indonesia Launches First ATV Tyre
- By TT News
- August 01, 2025
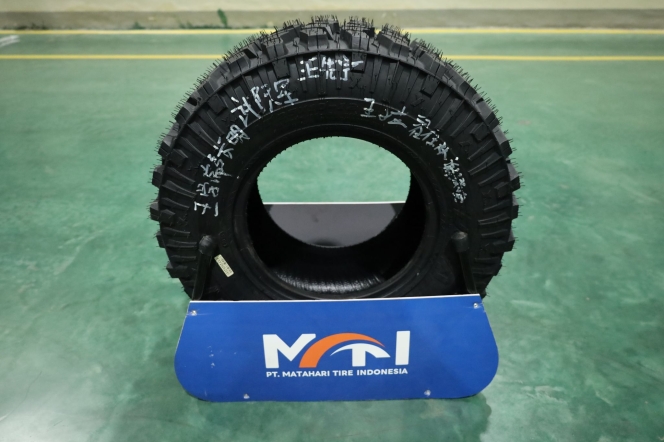
ZC Rubber has successfully commenced production of its first all-terrain vehicle (ATV) tyre at its Indonesian subsidiary, PT. Matahari Tire Indonesia (MTI), marking a strategic expansion into specialised mobility segments.
MTI’s state-of-the-art factory, covering 500,000 square metres, is strategically located in a region rich in natural rubber resources. Equipped with advanced digital technology and staffed by a highly skilled workforce, the facility is poised to meet the growing demand for high-quality tyres in both local and international markets, including the United States.
ZC Rubber’s investment in Indonesia provides access to vital raw materials and strengthens its global supply chain. The facility is poised to serve both local needs and support ZC Rubber’s international market expansion, reinforcing the company’s commitment to innovation, quality, and sustainable development.
Nexen Tire Posts Record Q2 Revenue Of $577 Million On Strong European, US Demand
- By TT News
- August 01, 2025
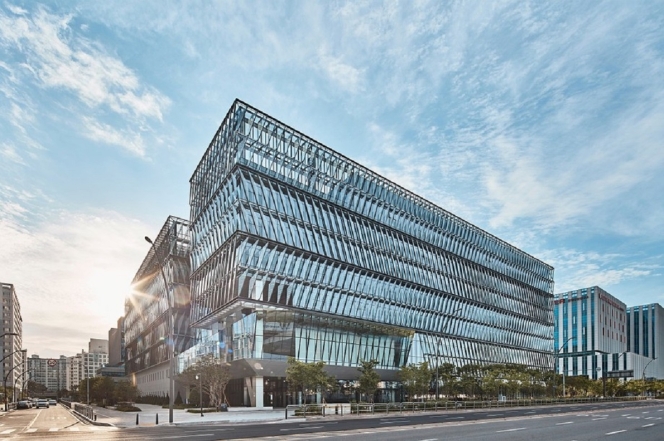
South Korean tyre maker achieves second consecutive quarterly revenue record despite raw material pressures
South Korean tyre manufacturer NEXEN TIRE reported record quarterly revenue for the second consecutive period on Thursday, posting consolidated sales of 804.7 billion won in the second quarter as increased European production capacity and recovering US demand offset global automotive sector uncertainties.
The company’s operating profit reached 42.6 billion won in the three months to June, remaining stable from the previous quarter despite ongoing pressure from elevated raw material costs that began in late 2024.
The strong performance was primarily attributed to enhanced production following the completion of Phase 2 expansion at NEXEN TIRE’s Czech Republic facility, combined with targeted regional sales strategies that secured key supply volumes across both original equipment and replacement market segments.
US sales strengthened further in the second quarter, building momentum from the first-quarter recovery after experiencing a temporary decline in the latter half of 2024. Expanded retail distribution partnerships supported the improvement, the company said.
In the Asia-Pacific region, Australia and Japan delivered record sales volumes, driven by continued investment in distribution network development.
Ocean freight costs provided some margin relief, though the company continued to face headwinds from raw material price increases that began in late 2024. However, NEXEN TIRE expects improved profitability in the second half as key input costs have been trending downward since early 2025.
During the first six months of 2025, the tyre maker began supplying original equipment tyres for 11 vehicle models, including the Hyundai NEXO, Kia EV4 and TASMAN, whilst deepening partnerships with global automakers, including premium brands.
The company said it would implement gradual price adjustments in the US market in response to recent tariff policy changes, focusing on expanding high-margin products and strategically reallocating global supply volumes to mitigate profitability risks.
“Despite persistent macroeconomic challenges, NEXEN TIRE achieved record-breaking sales for two consecutive quarters by maintaining balanced growth across both OE and RE segments,” said Chief Executive John Bosco (Hyeon Suk) Kim. “We will continue to reinforce our global competitiveness through strategic partnerships and region-specific initiatives.”
NEXEN TIRE has been building brand awareness through localised marketing efforts across North America, Europe, the Middle East, and the Asia-Pacific regions whilst expanding its retail presence through strategic distributor partnerships.
Comments (0)
ADD COMMENT