The Rough Trek: The Journey of ISO 9001 and Quality Management
- By PP Perera
- May 05, 2021
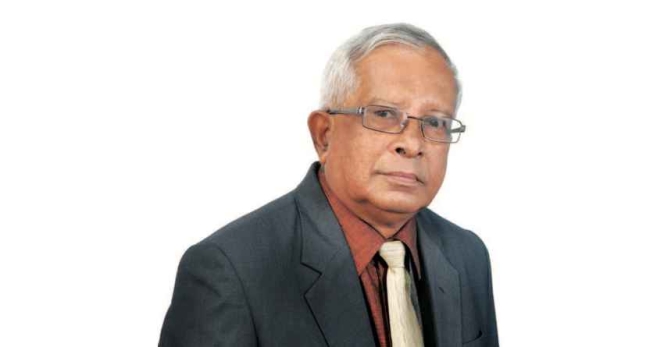
As far as Quality Management System (QMS) certification is concerned, my first exposure was to ISO 9000: 1994, about seven years after the first ISO 9000 standard emerged from the former BS 5750. The 20 + auditable QMS requirements has resulted in a bewildering and voluminous mass of documentations. It was virtually a system of documents, contrary to a documented system. According to the standard, the company was expected to establish, implement and maintain a documented procedure for all the auditable requirements of the standard. It was a period when the standard was spreading like bush fire, creating a gold mine for Consultants who thrived on the ignorance of the client companies. Preparation and maintenance of the documentation alone, engaged considerable managerial time, and hence the tendency to consider ISO 9000 based QMs as an area separate from the Quality Assurance and other operational functions which has still continued to the present day. This created some dichotomy between the ISO Department and the other functional sections resulting in conflicts. On doing the QMS audits, as an independent auditor for many companies, I have the experience of being confronted with a cart-load of files and documents. This was of course before, the soft copy methodology firmly got established. Many of the External Auditors, spent considerable time, in checking Document and Records, in scrutinizing document reference and revision numbers of even the less significant documents and formats, rather than concentration on the more important requirements. In this respect, I have a great respect for one of the very senior officers of the Sri Lanka Standards Institution, whose approach was to study the operational relationships and their effectiveness.
The transition in to ISO 9001:2000 saw some very significant and far-reaching changes, which the industries, took about one to two years to fully realize. It was a challenge for the auditors and the Certification bodies as well. A careful scrutiny of the eight principles of quality management, will show that they are nothing else but common business sense. The eight principles are:
- Customer focus
- Leadership
- Involvement of people
- Process approach
- Systems approach to management
- Continual improvement
- Factual approach to decision making
- Mutually beneficial supplier relations.
A casual glance at the principles, will reveal that it is about common sense of good managerial practices., irrespective of whether one goes for certification or not. However, it was an uphill task to grapple these concepts and integrate them holistically in to the quality management systems. Process approach in very simple terms means how to relate the inputs to outputs through the value adding conversions and how to control the activities, realize the desired results. It is directly related to the traditional definition of productivity, namely the ratio of out puts to inputs. What was difficult to comprehend was the fact that, the other seven quality management principles also provide inputs for the process approach. As an example, the auditors found it a grey area when it comes to evaluating leadership, in the context of the process approach. Regarding the establishment of the Quality Policy, which in turn is a requirement under leadership, I have seen many quality polices with attractive wordings which more often serve as show pieces. Very few companies have used the quality policy to provide direction for the setting up of quality objectives. One of the meaningful but concise quality policies I have seen is “We do everything, correctly, right first time at all times’’.
While the 2008 version of the ISO 9001 standard consisted of some notional changes only, the 2015 version signified a complete change of the concept of quality stressing the importance of quality in business strategy, by considering the impacts of external and internal factors and the expectations of internal and external parties on quality and including risk management as an important aspect of quality. Although the prime focus on ISO is product or service quality, companies cannot ignore the impact on quality, which covers product quality (Q), Price (P), and Delivery (D). The recent impacts of Covid-19 pandemic on the above aspect of quality, was amply seen throughout the world. The above requirements under the Organization Context, is a move in the right direction, in integrating quality in to all aspects of the business. However, most companies and even auditors, consider this in isolation as another requirement of the ISO 9001, which need minimum compliance. Similar comments can have made on the Identification of the risks and opportunities of the operational processes.
Product and service quality is used by most companies as means of maximizing the profit. The Nobel Prize Winner in Economics, Milton Friedman in 1970, stated that the sole responsibility of a business is to “use its resources to increase its profits. As a result of the rapid growth in consumerism, both locally and globally, business firms operate in a challenging and continually changing business environment. The rapid change is supported by rapidly expanding technology, and particularly of information technology. Dynamic organizations are making serious efforts to keep abreast of developments, in the changing business environment, while many traditional and conservative organizations are failing. Change has become inevitable.”
While we cannot find any fault with this approach, one cannot overlook the Social and Environmental bottom lines, which together with the Economic bottom-line, constitute the Triple Bottom of Sustainable development. The role of quality management on the social and environmental bottom lines, is a concept that has great potential in the modern-day concept. The reduction of scarp and rejects, especially in the tyre industry, will improve the environmental performance, while reducing the health and fire risks, often caused by irresponsible dumping.
Internal and external communications under the requirement 7.0, Support of the ISO 9001 and 14001:2015 standards are another area where adequate attention has been given. Despite the great advances in ICT, we can trace miscommunications as the root cause of most of the Non- conformance report raised during the QMS audits.
John Ruskin, the English author, (1819 -1900 ) once said, “ Quality is never an accident. It is always the result of intelligence effort.” I have seen this famous quote adorning the walls in some offices of CEOs and Senior Managers. However, the perennially repeating non-conformances related to quality in a large number of companies, make me to wonder whether the management and the mangers, “walk the talk.” Companies have in their procession, a handy tool, in the disguise of ISO 9001:2015, to enable them to establish the standard procedures, (SOPs), operate them and control, but many consider it as something to worry about only during the external audits of the certification bodies.
In this respect, it is worthy of mentioning that, in my country Sri Lanka, there is a famous Buddhist Cultural Pageant, in August every year, that attracts locals as well large numbers of tourists from across the globe. For the past 400+ years, this event follows the SOPs, without any, awareness of the ISO 9000, emphasizing that there is no magic or mystery about ISO, but the prevalence of good common sense. (TT)
- ATMA
- Automotive Tyre Manufacturers’ Association
- TyreSafe
- Indian Tyre Technical Advisory Committee
- ITTAC
- Tyre Safety
TyreSafe Honours India's ATMA With First-Ever International Award
- By TT News
- August 25, 2025
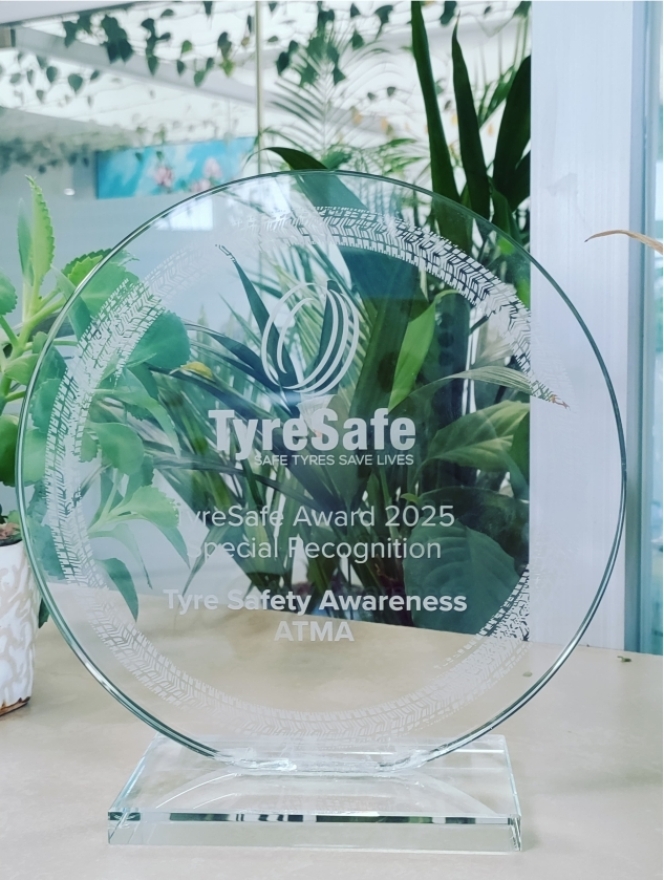
The Automotive Tyre Manufacturers’ Association (ATMA) has received a historic Special Recognition Award from UK-based tyre safety charity, TyreSafe. This marks the first time the organisation has presented an international award, highlighting the global resonance of ATMA’s extensive efforts in promoting tyre safety across India.
TyreSafe’s award specifically commended ATMA for its profound dedication and highly innovative approach. The association’s multifaceted initiatives have successfully educated over 20,000 participants and conducted inspections on more than 30,000 tyres. A cornerstone of this effort has been the Ideathons programme, which engages youth to develop creative concepts and inspire future road safety advocates, aligning perfectly with TyreSafe’s global vision for safer roads.
This recognition follows years of expansive activity by ATMA and its technical arm, the Indian Tyre Technical Advisory Committee (ITTAC). Their nationwide outreach has included over 200 safety activations, such as roadside clinics, inspection zones at petrol pumps and workshops for schools and universities. They have forged significant institutional partnerships, providing comprehensive training for over 1,000 tanker drivers in collaboration with Indian Oil Corporation and working with various state transport departments.
Campaigns on major expressways have involved inspecting thousands of vehicles and distributing safety materials, while continuous education is provided through webinars, social media and publications. Supported by its member companies, including Apollo, Bridgestone, CEAT, JK Tyre and MRF, ATMA remains dedicated to scaling this crucial outreach. The association continues to urge all stakeholders – from vehicle users to policymakers – to join this vital movement, reinforcing that tyres are not just components but essential life-safety systems.
Arun Mammen, Chairman, ATMA, said, “We are immensely proud that TyreSafe has recognised ATMA’s work in tyre safety. This award underscores our commitment to elevating public awareness and encouraging responsible tyre maintenance through engagement with motorists and institutional partnerships. Our journey continues with the shared vision of making roads safer across India.”
Sudershan Gusain, Head – Tyre Safety Awareness, ATMA/ITTAC, said, “This recognition by TyreSafe validates our extensive grassroots efforts: from petrol pump tyre clinics and university workshops to Ideathons and expressway campaigns. Educating over 20,000 people and inspecting 30,000 tyres is just the beginning. We will keep amplifying our message: proper tyre maintenance is crucial not just for vehicle performance but for saving lives.”
Linglong Germany Moves To Hannover Office
- By TT News
- August 25, 2025
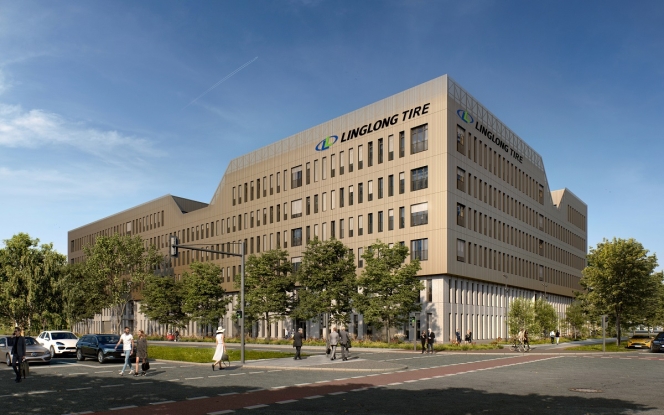
Linglong Germany GmbH has officially moved to a new office in Hannover. Located at Hollerithallee 22, the modern 500 sqm space is designed to integrate sustainable principles and collaborative work environments. It will serve as a central hub for 35 employees spanning research and development, logistics, human resources, after-sales, marketing and sales.
The site includes a state-of-the-art 300 sqm workshop, capable of storing 600 tyres and equipped with advanced technology for tyre data analysis and test vehicle preparation. Furthermore, this new headquarters will serve as the central command centre for coordinating testing activities at the company's permanent tracks in Spain (IDIADA) and in Ivalo in Finland (UTAC). This strategic expansion underscores Linglong's firm commitment to its growth and long-term presence in the European market.
Ceat SecuraDrive Circl Limited Edition Sustainable Tyres Launched In India
- By TT News
- August 25, 2025
Ceat, the flagship company of the RPG Group, has launched limited edition SecuraDrive Circl, which it claims is India’s first road ready passenger car tyre with up to 90 percent sustainable (bio-based) materials.
The SecuraDrive Circl tyres are said to push the boundaries of sustainability and technology while strengthening the company’s premium positioning. The launch builds on Ceat’s recent introduction spanning CALM technology, ZR-rated tyres and Run-Flat tyres.
Targeted at urban consumers aged 25-45 in Tier 1 cities, particularly from affluent households who view sustainability as both a responsibility and a lifestyle statement, the SecuraDrive Circl combines eco-consciousness, safety and top-tier performance in a single product.
The tyres are developed at Ceat’s state-of-the-art global R&D centre in Halol and is available in two variants – featuring 50 percent and 90 percent sustainable material content. With the latter, Circl becomes the most sustainable passenger car tyre ever road-tested and commercially launched.
The product introduces three global, patented firsts that the company said redefines sustainable tyre technology:
- Unified Biopolymer Inner Liner – a simplified material architecture that reduces manufacturing emissions and sets a benchmark in sustainable design.
- Glycerol-Based Accelerator – a bio-based alternative to petroleum-derived chemicals, ensuring eco-friendliness down to the smallest component.
- Anti-Static Silica Conductive Solution – a novel formulation that eliminates the use of carbon black while preserving electrical conductivity and passenger safety.
Beyond the product, Ceat is pursuing a comprehensive sustainability agenda – from sourcing greener raw materials to introducing circular practices for recycling end-of-life tyres. The SecuraDrive Circl marks a pivotal step in this journey, reinforcing the company’s commitment to shaping a cleaner future for mobility.
The tyres will be available at Ceat’s premium retail outlets and authorised dealerships across key markets from September 2025, priced at INR 12,999 for the 90 percent sustainable variant and INR 8,999 for the 50 percent variant.
Arnab Banerjee, MD & CEO, Ceat, said, “SecuraDrive Circl is a breakthrough that demonstrates how India can set new benchmarks in sustainable mobility. By achieving 90% sustainable content in a fully road ready tyre, Ceat is redefining performance and eco innovation, while reinforcing our journey to become a premium, future ready brand. Sustainability is no longer a choice but a responsibility. This launch reaffirms our vision of leading the transition to greener mobility.”
Lakshmi Narayanan B, Chief Marketing Officer, Ceat, said, “Consumers today are increasingly conscious about the choices they make, especially when it comes to sustainability. With SecuraDrive Circl, we are giving them a product that aligns with their values without asking them to compromise on performance, safety, or style. Circl represents the perfect blend of innovation and eco consciousness, and with this launch, Ceat is proud to set a new benchmark for sustainable mobility in India.”
CEAT Anchors Global OHT Strategy With $171 Million Sri Lanka Investment
- By TT News
- August 25, 2025
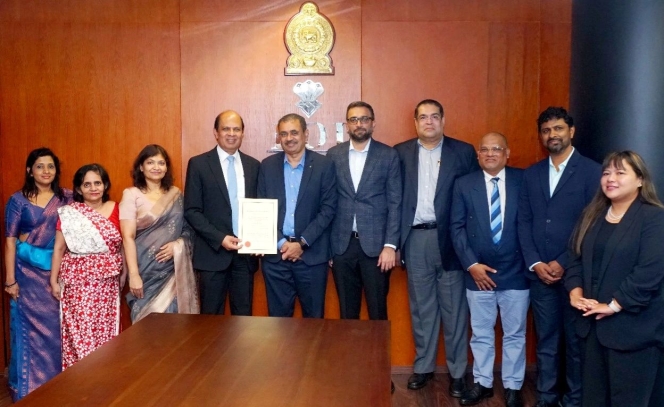
Sri Lanka has secured a pivotal USD 171 million investment from CEAT OHT Lanka, marking a major advancement for its manufacturing and export sector. This substantial commitment, formalised through an agreement with the Board of Investment of Sri Lanka, stands as one of the most significant recent Indian investments in the country and is set to position Sri Lanka as a premier global hub for off-highway tyre (OHT) production.
A cornerstone of the agreement is a tripartite commitment to workforce stability. A memorandum of understanding between CEAT OHT Lanka, Michelin Lanka and the Inter-Company Employees Union guarantees job security for all 1,483 existing employees. This ensures the full retention of their seniority, salaries and benefits, explicitly ruling out any retrenchments and providing seamless continuity throughout the operational transition.
The project follows CEAT's strategic acquisition of Michelin's Construction Compact Line Business, which includes key manufacturing plants in Midigama and Kotugoda. This move grants CEAT complete global ownership of the Camso brand, cementing its role as a leading international player in this high-value industrial segment.
Arjuna Herath, Chairman, BOI, said, “We welcome CEAT’s significant investment into Sri Lanka, which is among the largest investments from India in recent times. This approval underlines our confidence in CEAT’s vision and will further elevate Sri Lanka’s position as a global manufacturing and export hub.”
Amit Tolani, Chief Executive, CEAT Specialty, said, “BOI’s approval for CEAT OHT Lanka marks a new chapter in our partnership with Sri Lanka. With CEAT’s vision of expanding our global off-highway tyre business, we have great plans for this country. This investment will bring exciting new opportunities for Sri Lanka while playing a central role in our future growth.”
Kumar Subbiah, Chief Financial Officer, CEAT Ltd, said, “Our immediate priority is ensuring a seamless transition while safeguarding jobs and strengthening our operations in Sri Lanka. This investment reaffirms CEAT’s long-term commitment to our employees and to building Sri Lanka as a world-class hub for OHT manufacturing and exports.”
Comments (0)
ADD COMMENT