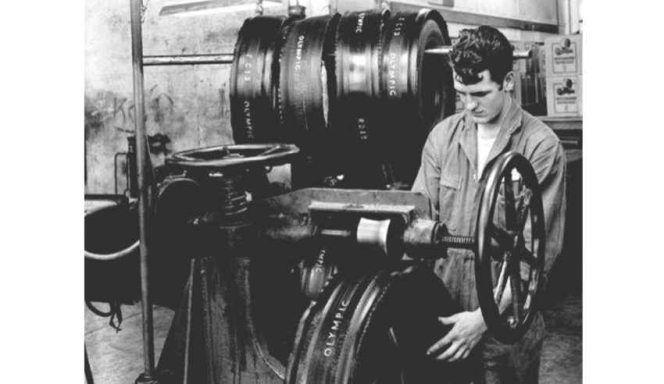
Nothing is stable. Technology is continuously evaluated. Materials science, electronics and software are the main three engines that reverse reactions or open new horizons.
Tyres are always known as black and round. However, the tyre engineers are aware of the weight achieved, the construction and the types of materials used in the tyres. What was the ancestor of the tyre, where is it going now?
The tyres were rated very quickly after vulcanisation 150 years ago. The first use of synthetic rubber and synthetic fibers, as well as the first radial tyre, go back around 70 years. Programming the control of the tyre building and curing machines with sensors and timer was a cornerstone. The new chemicals and advanced materials which suit well for process control, more homogeneous mixing, material integration and long-lasting rubber products.
Today's tyres last to the end of their useful life, which is primarily measured by the Remaining Tread Depth (RTD) which is greater than a limit value set by local legal approval. Twenty years ago, many defective tyres were found in scrapyards that were almost like new, but today the tyre will last almost lifetime.
Today, Mechanical rubber derivatives production machine parts are made to tighter tolerances. The integrity of the main body material is higher than in previous years. Alloys or composites are widely used compared to recent years. More controlled and homogeneous surface finishing is applied. Modern tyre production machines are equipped with robotics, full sensors and automation, stepper motors and greater controllability which are examples of the harmonization of creativity and innovation in the industry.
More than all that, today manufacturing machines are more purpose oriented, lighter, sensitive and modular.
The other very preliminary point of view is to analyse the needs of the main processes and what should be the strategy when you have an idea to buy new machines?
Every system needs new machines to install for a reason. It is used either to increase capacity or to renew a range of products, just to modernise or update technology. What should be the strategy when you have an idea to buy new machines? Either you are looking for a machine that matches your technology or you are taking the risk of a technology upgrade. The same category but a more efficient, more productive, safer and more controllable machine may be preferred or a completely new technology may be chosen.
If a very new technology is chosen, the time it takes to adapt can result in large production losses. It may take longer to adapt, etc. However, if you don't take such a risk, how will you manage the technology update in later years?
The other very preliminary point of view is to analyse the needs of the main processes. For example, if you are a tyre manufacturer, customers will only know your brand name. You are responsible for the end product. Third parties do not know where to start preparing tyres or what process to use to make them.
For example, you can have a textile calendar or you can get calendered textile and steel layers on the outside. When using a supplier, you don't need a factory calender machine. This also applies to the compounds used in the manufacture of the components. Today, a large volume of masterbatch is used in the rubber products industry. Organizing a good supply chain for manufacturing rubber compounds eliminates the need for mixers, a few mils, large silos, or process oil tanks.
A review of all processes and machine setup is necessary at regular intervals in order to remain competitive. Fewer production machines can increase productivity and controllability and intensify management. Less personal use, less energy and maintenance costs can be achieved. However, alternative suppliers need to be developed and diversified.
In the past, some particularly large tyre manufacturers had tyre cord treatment units in tyre factories. Some of them have steel wire production facilities for their own supply. Today we are witnessing a complete change of mind. The focus on the main process areas is mainly taken into account, which has completely changed the perspective in business. Today, most tyre manufacturers contract out the processing of 2nd class compounds. So, there is no refinery mill machines in tyre factories. The heating of the rubber in the preparation zones of the main components is carried out by cold feed extruders. Large capacity extruders are used under the drop door in mixing rooms. As a result, there are very few milling machine and milling operators in the tyre factory. Factory structures are smaller, parts production and machine maintenance are outsourced.
Full robot transfer units already exist, No man-tyre building and curing are achievable now. Profile extruders are already disabled, calendering might be totally needless by body ply webbing on tyre building drums.
Being open and innovative in the tyre and rubber industry is important. Support for technological innovation and productivity, as well as the vision to find more efficient devices, is required. New control systems with computers and automation are inevitable. Indeed, the company's employees must have a vision to choose the last and the best for the future. The most important thing is to find profitable solutions for the entire company.
As you follow the progress of the machine, keep in mind that new materials are coming. Any fashionable material will one day be a burden on the staff. Major hardware changes require new processes or machines. The ultimate case is the cancellation of part of the process, which means the cancellation of the production machines. Such a case can be irresistible at any time.
The increasingly demanding structure of the automotive industry and regulations will demand ever lighter, more environmentally friendly and more rolling-resistant tyres, which repeatedly calls for ambitious innovations. Innovative materials are inevitable to exceed expectations. Just as new materials come out of the R&D thicket box and enter the daily production inventory, the production area and machinery should be reorganised.
Full robot transfer units already exist in many phases instead of being transported. There are automatic scan and uniformity checks. No man tyre building and curing operations are achievable now. Profile extruders are already being phased out in some tyre factories. Body ply webbing could be more of a standard technology in tyre building. Calendering may be totally needless in tyre plants.
As far as automation and controllability technologies assess, there is still room for refinement or cancellation of production processes and machines in tyre factories.
Today, Mechanical rubber products production machine’ parts are made to tighter tolerances. The integrity of the main body material is higher than in previous years. (TT)
Rubber Board Announces 2025 Subsidy Scheme
- By TT News
- August 22, 2025
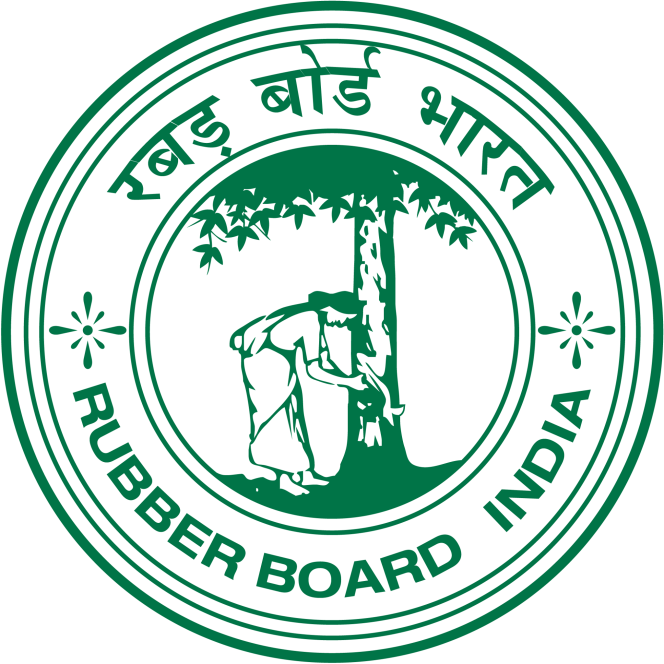
In a move to promote rubber cultivation, the Rubber Board of India has announced a new financial aid scheme for 2025. Growers in non-traditional regions are now eligible to apply for subsidies supporting both new planting and re-planting initiatives. The application process is exclusively online through the ‘service plus’ portal on the Board’s official website, with a submission deadline of 31 October 2025.
To complete their application, growers must provide digital copies of essential documents. These include land ownership certificates, a rough sketch of the planted area, a copy of their Aadhaar-linked bank passbook and proof of purchasing planting materials from recognised nurseries. Successful applicants will receive financial assistance of INR 50,000 per hectare. For additional information, growers are advised to consult the Rubber Board’s website or contact their nearest regional office, field station, or the Board’s call centre.
Global Tire Recycling Market to Hit USD 8.9 Bln by 2029 on Sustainability Push – MarketsandMarkets
- By TT News
- August 22, 2025
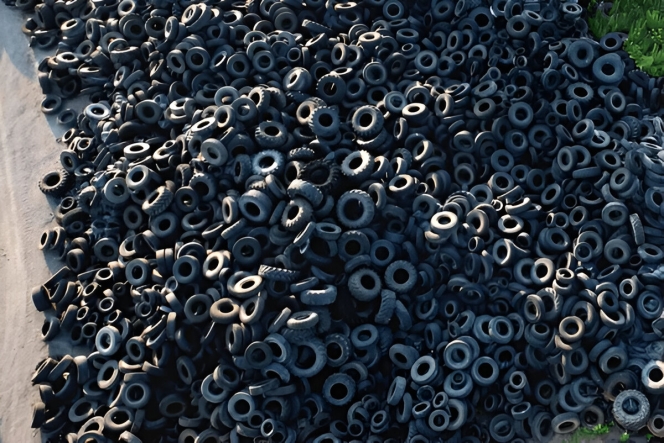
The global tyre recycling market is forecast to grow to USD 8.92 billion by 2029 from USD 7.44 billion in 2024, driven by mounting volumes of end-of-life tyres (ELTs), tighter environmental regulations and rising demand for sustainable materials, according to research firm MarketsandMarkets.
The market is projected to expand at a compound annual growth rate (CAGR) of 3.7 percent over the period, the report said.
According to the World Business Council for Sustainable Development, one passenger tyre per person is discarded annually in the developed world, contributing to about 1 billion ELTs globally each year. A 2022 study in ScienceDirect estimated some 4 billion ELTs are already stockpiled worldwide, a figure expected to reach 5 billion by 2030.
“The mass piling of 1 billion ELTs per year to be expected to reach 5 billion by 2030 calls for an ever-increasing process of recycling tyes in a more sustainable means of waste management,” the report noted.
MarketsandMarkets said demand is being spurred by both environmental concerns and industry adoption of new recycling technologies aimed at reducing landfill volumes while maximising material reuse.
Rubber is set to remain the most dominant recycled by-product, with applications in crumb rubber, rubberised asphalt, playground surfaces and sports fields. Mechanical shredding, described as the most cost-effective and scalable method, will continue to lead recycling processes due to its wide applicability in construction, energy and automotive sectors.
Construction is expected to be the largest end-use industry, as recycled materials such as crumb rubber are increasingly used in road building and green infrastructure projects.
Asia-Pacific is projected to remain the biggest consumer of recycled tye products during the forecast period.
Key players in the sector include Liberty Tye Recycling (US), GENAN HOLDING A/S (Denmark), ResourceCo (Australia), GRP Ltd (India), Lehigh Technologies (US), Entech Inc (US), Emanuel Tye (US), BDS Tye Recycling (US), Contec (Poland) and CRM (US).
Global TPMS Market to Edge Up to 71.4 Mln Units by 2030 – Research and Markets
- By TT News
- August 22, 2025
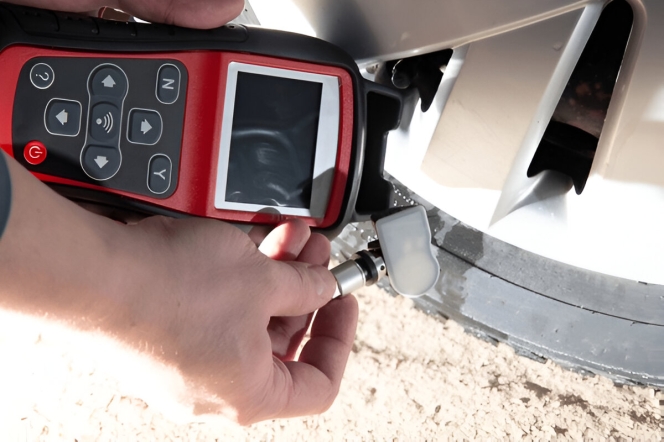
The global market for Tyre Pressure Monitoring Systems (TPMS) is projected to grow modestly over the next five years, with volumes rising from an estimated 68.9 million units in 2025 to 71.4 million units by 2030, according to a report published.
The “Sector Innovation Report: Tyres and Wheels Q2 2025”, released by Research and Markets, forecasts a compound annual growth rate (CAGR) of 0.7 percent for the TPMS market.
The study synthesises data from multiple sources and provides an overview of the tyres and wheels sector, highlighting recent developments, patent activity, job trends and regional growth prospects.
The report identifies opportunities for auto manufacturers and suppliers to refine sales and marketing strategies, noting growing demand for detailed, region-specific data.
Key sections include an analysis of patent filings by region and country, sector forecasts across five geographies – Asia-Pacific, Europe, the Middle East and Africa, North America and South America – as well as profiles of leading component suppliers.
The report also tracks job listings and advertising activity in the sector, broken down by geography, occupational category and level of seniority.
Companies covered in the report include Bridgestone, Continental, Goodyear, Michelin and Hankook.
Wisconsin Truck Driver Wins 41st Goodyear Highway Hero Award
- By TT News
- August 22, 2025
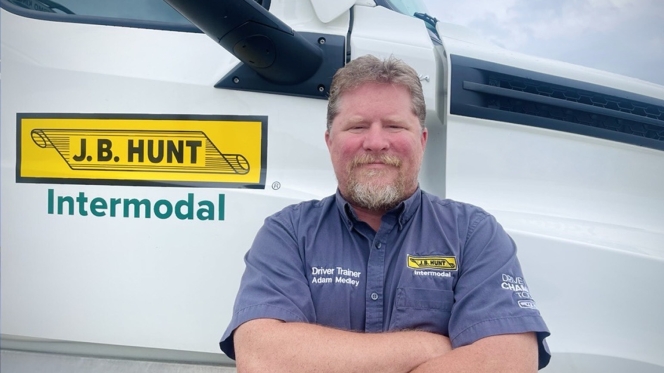
Truck driver Adam Medley of Omro, Wisconsin, has been named the winner of the 41st Goodyear Highway Hero Award. The professional driver for J.B. Hunt Transport, Inc. was recognised for a courageous act performed on 28 July 2024 while driving on County Rd A in Green Lake, WI.
While navigating a familiar route, Medley initially steered to avoid what he assumed was road debris. As he drew closer, he realised a person was lying directly in the roadway. Medley promptly and safely pulled over, rushed to assist the individual and moved them to safety before contacting the police.
Established in 1983, the Goodyear Highway Hero Award honours commercial drivers in the U.S. and Canada who perform extraordinary acts of courage. Winners are selected by an independent panel of industry judges from nominations submitted each year. As this year’s honouree, Medley will receive a cash prize and a commemorative ride on the Goodyear blimp.
Goodyear presents the award to acknowledge the vital role of the commercial trucking industry. The program’s stories of heroism inspire the company to continuously enhance its commercial tire products and support services, like its Fleet HQ network, to ensure drivers have reliable assistance on the road.
Nick Hobbs, Chief Operating Officer at J.B. Hunt, said, "In a moment where every second counted, Adam put the safety and well-being of others first. His actions exemplified integrity and selflessness, and we are excited that Goodyear has recognised him with this year's Highway Hero Award."
Joe Burke, Vice President, Goodyear North America Commercial, said, "Adam's story continues to remind us that professional truck drivers are the unsung heroes of our roads. His quick and professional response to this unexpected situation demonstrates the integrity, dedication and compassion that define what's the best of our industry."
Comments (0)
ADD COMMENT