We Are On A Steep Learning Curve Since The Beginning Of 2020: Rogier van Hoof
- By Sharad Matade
- October 13, 2021
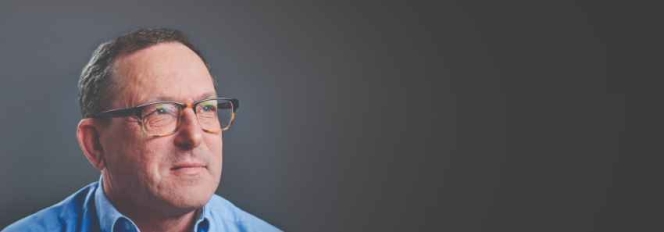
Being a global supplier of tyre oil, Nynas supplies its products to major tyre companies worldwide. However, the Covid-19 pandemic brought unforeseen challenges in transporting goods through all three modes of transportations, and Nynas is no exception! In an interview with Sharad Matade of Tyre Trends, Rogier van Hoof, Head of Secondary Distribution Naphthenics at Nynas, says enhanced communication and exchange of information digitally will help the company handle the new challenges. He also added that the container availability is expected to be normalised in 2022 but road transportation will remain a challenge.
Ever since Covid-19 engulfed the world, the job of Rogier van Hoof, Head of Secondary Distribution Naphthenics at Nynas, has become more challenging. Though tyre production is coming back on track speedily, the challenges at the logistic front are still demanding. Recollecting the initial impact of Covid, van Hoof says, "For Nynas, it all started in early 2020, when the lockdowns in China forced factories to close down manufacturing activities. However, the initial shock was largely seen in truck movements. As part of the measures, drivers had to go into quarantine after a long haul drive. They could pick up a container, but they had to go into quarantine when they were back at the delivery point. So we saw an immediate effect on the truck availability. The cascading impact, I don't think anybody could have predicted. We are on a steep learning curve since the beginning of 2020."
van Hoof and his team swung into action and immediately enhanced the communication with its customers, forwarders and logistic partners to evaluate options to tackle the unprecedented challenges. "I don't think anyone was prepared for what had happened afterwards. Before Covid, people used to take logistics for granted that you order something and it's there when you want it. But with the Covid situation, people have realised to approach things differently, not only on the factory levels but also on the logistics sides on a day to day basis. There are still many limitations we have to deal with," says van Hoof.
According to van Hoof, in the last one and a half years, the just-in-time concept is out of the window and long-term planning has become the priority. "In the past, we knew there was a vessel going every week, and we had substantial free times in getting the containers in, getting them loaded and bringing them to the quay. Even if we would miss a vessel, we always could ship it next week, so the delay was manageable – but that has gone completely out of the window today. It is clear that if you miss a vessel, the next vessel with space will be there maybe in a month. This means everyone needs to plan much further ahead," says van Hoof.
Most countries are now recovering from the Covid impact; however, many major export destinations are still grappling with severe restrictions. Many main ports are congested and containers are either stacking up at cargo ports or in inland depots. This imbalance results in waiting time for space on vessels, according to reports, between three to eight weeks. The logistics supply chain is struggling to get back in balance resulting in extreme price spikes and unpredictable delays. "This is a situation which is unprecedented; we have never seen it before," adds van Hoof.
van Hoof says loyalty and predictability are helping the company sail through the rough time. "We have been working with our logistic partners for a long time and, therefore, they know that what we promise them, we deliver. Predictability towards the stakeholders like transporters, shipping lines, forwarders has become key. In desperation, many companies are making overbooking of containers but failing to utilise the booking fully. In our relationship with our forwarders and the shipping lines, we have been able to show loyalty and keep our promise. If we tell the shipping line that we will ship 50 containers this week, we will make sure that these 50 containers are there. Our loyalty is rewarded by the fact that they will treat us as a preferential client. Price is no longer the highest priority, and this is something people need to realise. There's always somebody who is prepared to pay more,” explains van Hoof.
van Hoof feels the container availability situation will be normalised by 2022, but the driver availability issue will remain a more significant issue.
Currently, the company has 23 depots worldwide, of which Antwerp, Houston and Singapore are central storage facilities and blending stations. Last year, the company transported around 700,000 tonnes of oil by sea. There were also 30,000 deliveries by road tanker, 10.000 container transports and 250,000 drums delivered to customers worldwide.
However, opening more depots to tackle the logistic challenges is not viable, thinks van Hoof. Around 2018-19, shipping costs for containers were at the lowest level ever; companies always preferred shipping over setting up depots. "Now our shipping costs have not only increased substantially, but the reliability of the shipping has gone down to the lowest ever. I think that less than 60 percent of the vessels arrive at the bars on time. So we are continuously looking at what is now the best solution. But you also have to consider that opening a depot in a country is not a temporary thing. It is something you do for the long run," explains van Hoof.
van Hoof also sees a possibility of working with its clients to manage container utilisation. "There are customers who are logistically shipping more than we do. So can we use the strength of both companies to find a solution? For instance, let's say we ship 100 containers to India and our customer ships 200 containers from India, so we are seeing if we can help each other, can we use their containers? We see more and more openness among the stakeholders in tackling logistic challenges," says van Hoof.
Nynas is currently implementing a transport management system within the company, which will allow it to digitalise the information. The transport management system allows exchanging data between stakeholders, including Nynas' depots, transporters, forwarders, inspectors and customs agents. "Today, everybody's under stress, and people need real information in real time," adds van Hoof.
The company plans to go into the second phase to integrate all that information with other stakeholders.
The Nynas executive advises the youngsters in the transporting job to be agile and eager to learn to tackle unusual situations. "You need to deal with much information and make sense of that information and use it correctly. So if you are somebody who gets up in the morning and goes to work, and has no idea what will happen during the day, then you're a suitable candidate for the job. For me, I make a little list of two or three things to do every day, and at the end of the day, I'm always happy that I've done two or three jobs, because, during the day, there are so many other things that need attention or immediate attention," concludes van Hoof. (TT)
Pirelli Launches New Scorpion All Season SF3 Tyre For SUVs
- By TT News
- July 01, 2025
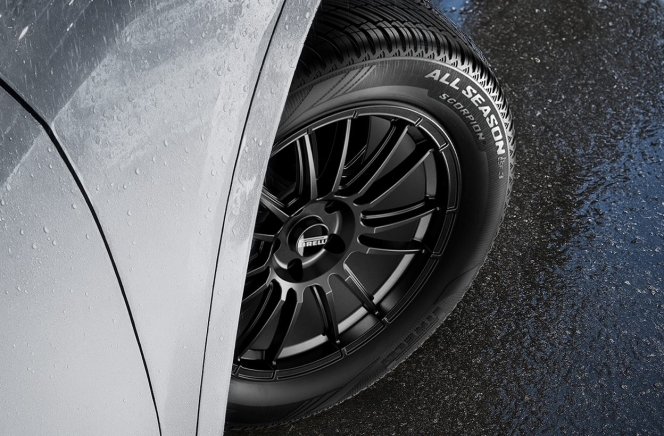
Pirelli has introduced the Scorpion All Season SF3, a new all-season tyre specifically engineered for SUVs, building upon the award-winning technology of the Cinturato All Season SF3 while tailoring performance to the demands of larger, heavier vehicles.
Designed for safety and versatility across diverse weather conditions, the tyre has already earned top ratings in independent Dekra tests, excelling in cumulative braking performance. It carries an ‘A’ rating for wet grip on the European tyre label and meets the 3PMSF standard for certified snow traction. Additionally, the Scorpion All Season SF3 prioritises driving comfort, with a ‘B’ rating for external noise and class A/B efficiency in rolling resistance, ensuring long-lasting performance and lower emissions. The compound is engineered for stiffness and high-temperature stability, while new polymer blends and natural-origin resins enhance cold-weather grip without sacrificing wet traction. Pirelli leveraged AI-driven Virtual Compounder technology to refine the material composition, alongside 3D modelling to synchronise tread and compound design for optimal performance.
To enhance SUV handling, Pirelli incorporated reinforced tread blocks with a progressive entry geometry, which gradually increases the contact patch with the road. This design minimises pressure peaks, reducing vibrations and noise while improving stability and grip – particularly beneficial for heavier vehicles. The tread also features an adaptive structure with 3D sipes that evolve from straight lines to a zigzag pattern as the tyre wears, maintaining snow traction even with reduced tread depth. These sipes dynamically adjust under pressure, shifting between a winter-optimised and summer-friendly profile for balanced year-round performance.
The Scorpion All Season SF3 expands Pirelli’s all-season lineup, catering to the rising demand for versatile tyres. Available in 17- to 21-inch sizes, select models include Elect technology for compatibility with electric and plug-in hybrid vehicles, as well as the Pirelli Noise Cancelling System (PNCS) to reduce road noise.
Bridgestone Logistics Transfers 66.6% Shares To SBS Holdings
- By TT News
- July 01, 2025
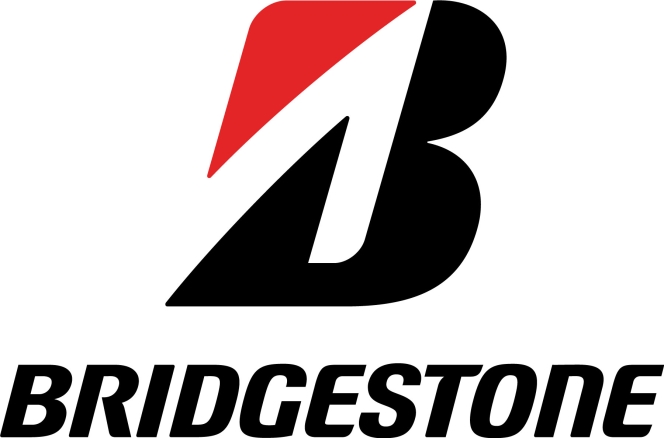
Bridgestone Corporation has agreed to transfer 66.6 percent shares of its wholly owned subsidiary, Bridgestone Logistics Co., LTD, to SBS Holdings, Inc. This move aligns with Bridgestone’s strategy to strengthen its global business by adapting to dynamic market conditions and building a foundation for sustainable growth. In Japan, the company is restructuring operations to enhance productivity and innovation across its value chain, from tire development to logistics and sales. The share transfer is part of these broader efforts to optimise business performance.
The Japanese logistics sector is experiencing major shifts due to carbon neutrality goals, sustainable supply chain demands and labour shortages. SBS Holdings, a key player in the industry, sees these challenges as growth opportunities and is implementing forward-looking strategies. By integrating Bridgestone Logistics into its operations, SBS Holdings aims to bolster the subsidiary’s business and management capabilities, positioning it for future expansion.
Bridgestone Logistics has been advancing sustainable logistics through digital solutions, including next-generation delivery systems, collaborative logistics to improve efficiency and modal shifts toward eco-friendly transport. These initiatives will support SBS Holdings’ mission to ensure safe, secure and sustainable logistics operations. Additionally, SBS Holdings’ adoption of electric vehicles, logistics technology and IT-driven systems will further enhance efficiency. The collaboration will unlock synergies by leveraging SBS Holdings’ expertise, network and resources, enabling Bridgestone Logistics to explore new business opportunities beyond the Bridgestone Group and create greater social and customer value. Moreover, by aligning with SBS Holdings’ workforce development strategies, Bridgestone Logistics will foster talent growth and organisational innovation.
ETRMA Speaks On Automotive Sector Interpretation Guide Of Data Act
- By TT News
- July 01, 2025
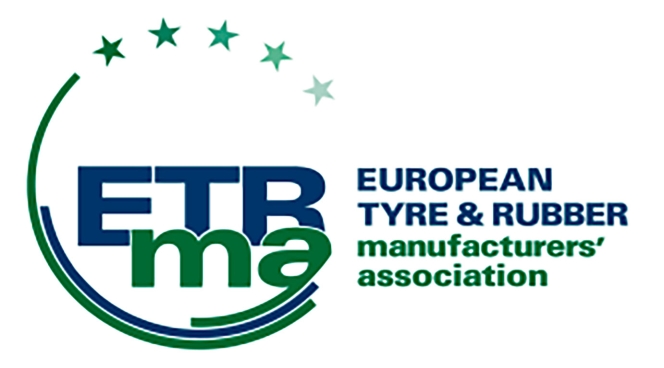
The European Commission’s Industrial Action Plan for the automotive sector included plans to publish Guidance on in-vehicle data alongside the implementation of the Data Act. In response, the European Tyre and Rubber Manufacturers’ Association (ETRMA), alongside other automotive industry groups, has developed an Automotive Sector Interpretation Guide of the Data Act to foster a common understanding ahead of the regulation’s application. This joint effort has helped clarify critical definitions and regulatory interfaces while also incorporating essential tyre-specific considerations – a step ETRMA strongly supports.
Despite this progress, the Data Act’s objectives may fall short without additional measures. Key solutions – such as human-machine interface (HMI) access for user consent and digital ID federation to enable secure, efficient data sharing within a unified European data space – require further exploration under sector-specific regulation. ETRMA remains dedicated to ensuring the Data Act’s implementation promotes fair, non-discriminatory access to in-vehicle data. The association will continue pushing for enforceable rules that guarantee real-time, secure and efficient access to relevant data, safeguarding innovation and competitiveness in the automotive and tyre industries.
Bridgestone India Strengthens Retail Presence with New Select Store In Nashik
- By TT News
- June 30, 2025
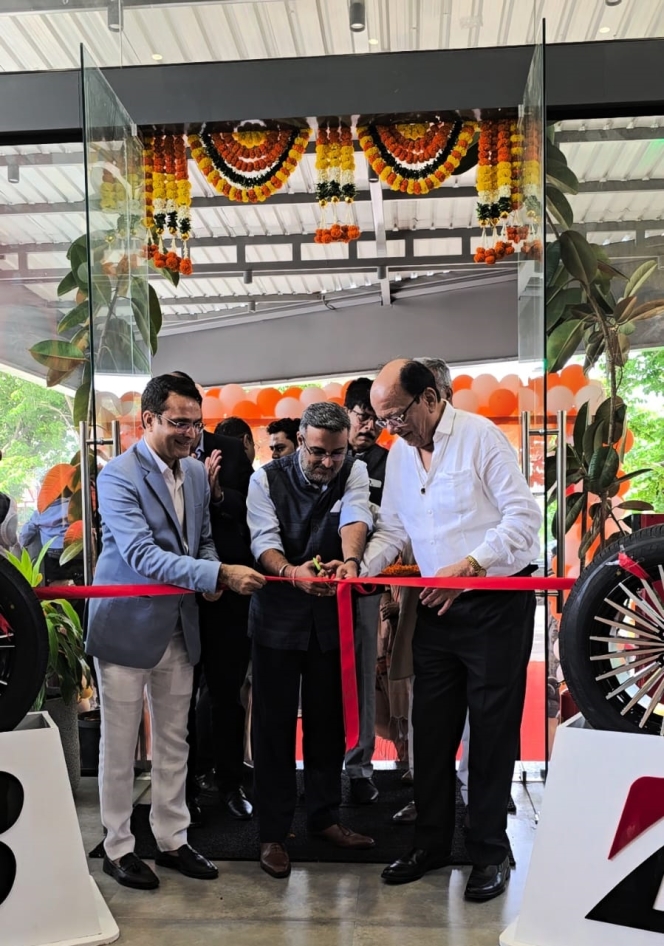
Bridgestone India, a key subsidiary of the global Bridgestone Group and a leader in tyres and mobility solutions, has expanded its premium retail network with the launch of Bridgestone Select Store – M/s Nashik Tyres and Services. The store was inaugurated by Rajarshi Moitra from Bridgestone India, reinforcing the company’s commitment to delivering innovative, customer-centric tyre retail experiences across the country.
Strategically located in Nashik, the store features modern infrastructure and a premium service setup, positioning it as a one-stop destination for tyres and related services in the region. Recognising that tyres are the sole contact point between a vehicle and the road, Bridgestone emphasises safety, performance and driving confidence through its Select stores. These outlets not only help customers choose the right tyres but also enhance their ownership experience with expert guidance and high-quality services.
With over 900 Select stores nationwide, Bridgestone India has established a premium retail network that goes beyond tyre sales to offer a superior, service-driven experience. The expansion of M/s Nashik Tyres and Services further strengthens Bridgestone’s mission to bring world-class tyre solutions closer to customers, reinforcing its pan-India presence with a focus on innovation and customer satisfaction.
Moitra said, “At Bridgestone India, we are committed to redefining the tyre buying experience through our Select stores. As we continue to expand our footprint and enhance manufacturing capabilities our goal is to provide premium products, services and customer experience.”
Comments (0)
ADD COMMENT