Improving Tyres With Growing Opportunities
- By Sharad Matade & Gaurav Nandi
- January 16, 2025
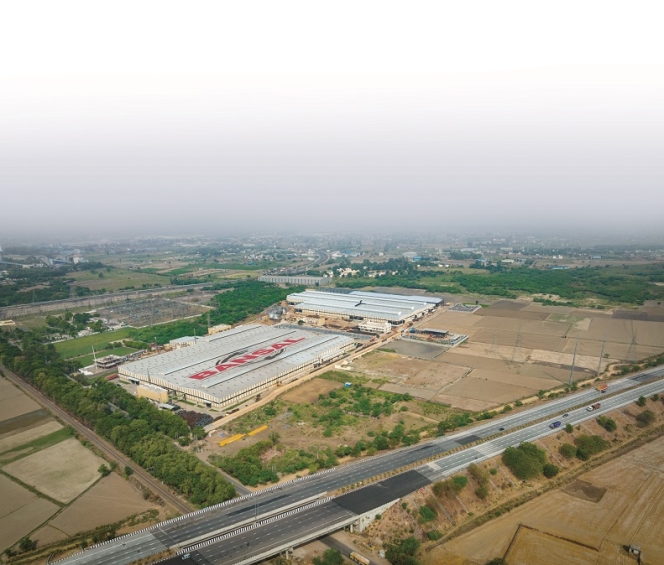
Bansal Wire Industries, India’s largest stainless steel wire manufacturing company, is charting a dynamic course in the Indian tyre market with innovative solutions aimed at enhancing performance and sustainability. Leveraging its expertise in the automotive sector, the company is introducing advanced steel cords and bead wire products designed to improve tyre efficiency, rolling resistance and fuel economy.
Bansal Wire Industries is optimistic on capitalising on the growth of the Indian tyre market as tyre makers endeavour to offer more efficient rubber wheels. The Delhi-based conglomerate is planning to introduce products within its tyre-industry portfolio that will improve performance. The company already caters to the automobile industry with products spanning outer and inner spring, circlips and washer categories.
Speaking to Tyre Trends on upcoming products, Managing Director Pranav Bansal iterated, “Our modern manufacturing setup enhances product performance; this is particularly in line with current industry trends as we move towards producing super tension and super tensile plus steel cord products. These innovations are expected to improve rolling resistance and reduce tyre weight, both of which contribute to better fuel efficiency and performance. We are actively embracing complete digitalisation and bringing more automation into our processes, helping us increase efficiency and ensure product consistency.”
He added, “We pride ourselves in being the only Indian company manufacturing steel cord for the PCR and TBR sectors with offerings in normal tensile, high tensile and super tensile (ST). Additionally, we have expanded our bead wire manufacturing capabilities with facilities in both South and North India and we continue to explore innovations to serve the evolving needs of the tyre industry.”
Alluding to the reason behind expanding into the tyre industry, he noted, “Our expansion into the tyre industry is driven by the increasing demands of durable, high-quality materials and products, as supported by industry research reports done by Invest India, among others. By diversifying our product portfolio, we aim to meet this demand for efficient materials. By focusing on high-quality steel cords and bead wires, we help improve tyre performance, which in turn enhances vehicle stability, handling and safety, especially under challenging road conditions.”
“The Indian tyre industry has witnessed a significant growth over the past few years, which is driven by an exponential increase in production, domestic sales, exports and overall revenue. An integral growth factor in this is the increase in the ownership of vehicles, which further aids the tyre industry. Additionally, the surge in demand for tyres for trucks and buses, fuelled by expanding mobility and industrialisation, has given a boost to the sector,” he added.
The company caters to over 5,000 customers, offering more than 4,000 different wire products across industries such as automotive, infrastructure and consumer durables. While its primary market is India, the manufacturer also exports products to over 50 countries. The US and Europe are among its largest markets, where it continues to see significant demand for products.
Industry talk
Bansal mentioned that the increasing demand in the automotive industry, domestically, presents tremendous opportunities for the company. “Our high-performing products allow us to constantly evolve. However, challenges like fluctuating raw material prices as well as the changing regulatory requirements could impact. Expansion internationally, specifically in regions like the US and Europe, provides significant opportunities, but geo-political risks and trade regulations could challenge the operations on a global level,” he noted.
Alluding to the strategies implemented by the company to meet the growing demands, he iterated, “In the automotive and tyre industry, collaboration with stakeholders is key to driving innovation and meeting the growing demand for high-quality wire products. We focus on building strong partnerships with manufacturers, suppliers and research institutions to align our solutions with industry needs. Regular engagement through industry forums, trade shows and feedback mechanisms allow us to understand evolving requirements and deliver solutions that enhance performance, safety and sustainability. By participating in joint development projects, sharing technical expertise and staying updated on emerging trends, we ensure our products remain at the forefront of technological advancements.”
Quality and sustainability
The company has manufacturing facilities for bead wire in both South and North India. The production capacity at its South India facility is 50 kilotonnes per year, and at the North India facility, it is 30 kilotonnes per year. Additionally, it has a pilot manufacturing site for steel cords in North India, which currently has a production capacity of 20 kilotonnes per year. The company plans to gradually scale up this capacity to meet the growing demand of the tyre industry.
Commenting on quality measures implemented to derive industry-grade materials, he explained, “We are committed to ensuring the highest product quality and will soon be the only company in India with dedicated in-house research and development wing for both steel cord and bead wire. Our research and development facility spans 12,000 square feet and is equipped with state-of-the-art equipment to drive innovation. To achieve 'First Time Right' production, we have conducted extensive gap analyses of our processes and implemented all necessary improvements. Additionally, our manufacturing facilities are equipped with cutting-edge machinery, all integrated with a complete digital interface to capture real-time data, ensuring the highest standards in production and quality.”
The company also puts focus in the principles of circularity with several initiatives. “Sustainability is a core focus area for us and we are addressing it in several ways. Our use of renewable energy has reached 70 percent in some of our plants and we are dedicatedly moving towards water positivity in many of our facilities. We are exploring the use of green steel in both our steel cord and bead wire products. To further reduce our environmental impact, we are investing in energy-efficient machinery and continuously seeking ways to minimise emissions across our operations,” said Bansal.
Future course
According to Bansal, the company is anticipating several key trends that will influence its business, including a strong focus on product innovation to enhance performance and quality. “We are committed to show resilience to maintain operational stability in dynamic markets. We work dedicatedly to improve the customer experience through feedback and satisfaction while also fostering diversity and inclusion within our workplace culture. Sustainability and corporate social responsibility remain priorities, alongside embracing technological advances to optimise our operations and product offerings for the future. These trends will guide our growth and ensure we stay ahead in a competitive market,” explained Bansal.
Besides, the company is also focused on significant growth opportunities through the establishment of new facilities and capacity expansions. “Our new manufacturing site in North India for both steel cord and bead wire has a current steel cord capacity of 20 kilotonnes per year with plans to scale it to 200 kilotonnes per year over the next five years. In bead wire, we now have two new state-of-the-art manufacturing facilities in South and North India with a combined production capacity of 80 kilotonnes per year, ensuring that we are well positioned to meet the increasing demand from our customers in the coming years,” concluded Bansal.
Hana RFID Appoints Jason Chang As New Asia Sales Director
- By TT News
- August 21, 2025
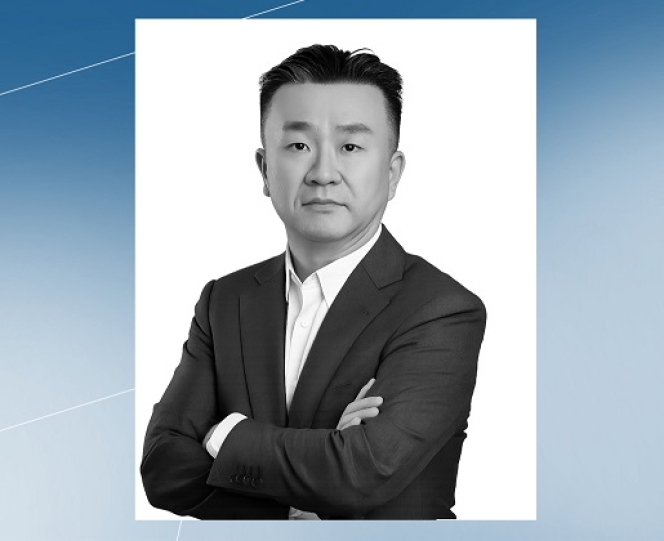
Hana Technologies, Inc. (Hana RFID) has strengthened its leadership in the Asian market with the appointment of industry veteran Jason Chang as Sales Director for Asia. Based in Shanghai, he will be responsible for managing key customer relationships and driving strategic growth throughout the region.
Chang brings a wealth of relevant experience to the role, with over 15 years in the RFID sector following a successful career in IT. His proven track record includes significant tenures at leading firms like Xerafy, Stora Enso and Beontag. His accomplishments range from pioneering the development of innovative flexible anti-metal tags to launching groundbreaking RFID-based retail solutions that gained widespread adoption in China and Europe. He has also demonstrated a strong capacity for growth, most recently achieving remarkable business expansion in the APAC market.
This appointment is a strategic milestone for Hana RFID, underscoring its commitment to supporting global customers with high-performance technology and expert, on-the-ground leadership. This move highlights Hana RFID's focused strategy on deepening its regional support and providing partners with sophisticated RAIN RFID inlay and embeddable tag solutions, backed by local expertise.
Mike Hetric, Senior Vice President – Sales & Marketing, Hana RFID, said, “The appointment of Jason Chang is a significant step forward in improving local availability and supporting our key partners in Asia. Jason’s track record in driving innovation, his deep market knowledge and his commitment to customer success will be invaluable as we expand our footprint in this dynamic region.”
Chang said, “I’m excited to be part of the Hana RFID team, which is recognised in the market as both a key player and a trusted partner for an ever-growing network of label converters, service bureaus and system integrators. I look forward to working alongside our partners in Asia to deliver innovative solutions and exceptional service.”
Ralson Tire North America Expands Leadership Team
- By TT News
- August 21, 2025
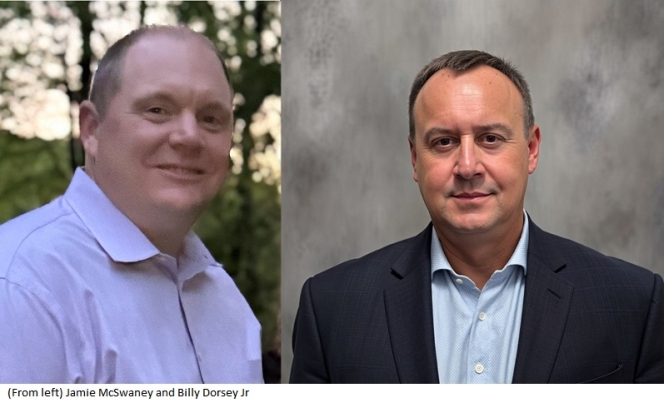
Ralson Tire North America (RTNA) has expanded its leadership team with the appointment of two seasoned tyre industry professionals.
As per the new development, Billy Dorsey Jr has been appointed as Vice President of Sales – South and Jamie McSwaney has been appointed as Vice President of Sales – North. Both the new appointments bring a combined 45 years of tyre industry experience to the company.
Brian Sheehey, President, RTNA, said, “These additions signal our unwavering commitment to accelerating Ralson’s growth in the US and Canada. We’re building a leadership team that knows how to compete, win and deliver results. Their deep industry relationships and ability to execute will be instrumental as we continue to grow our footprint in the North American trucking industry.”
Nordic Market Will Fare Well For Premium Tyres: Citira
- By Gaurav Nandi
- August 21, 2025
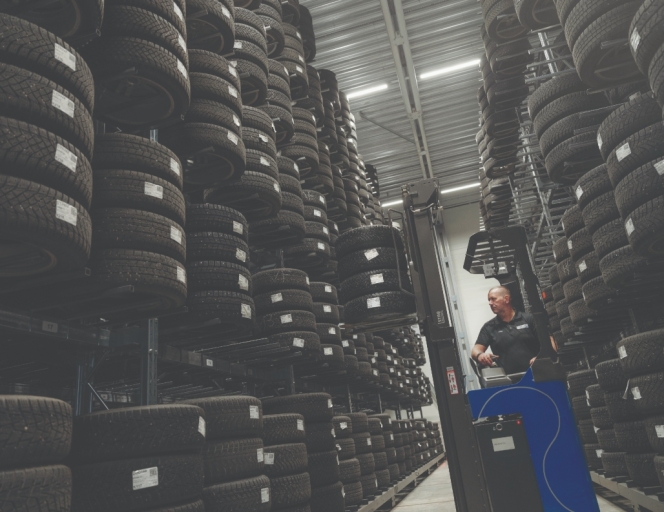
Scandinavian tyre service provider Citira sees robust potential for premium tyres in the Nordic region, driven by seasonal demands and safety priorities. CEO David Boman highlights that premium tyres including Pirelli’s offerings hold a significant share in passenger car, light truck and truck tyre segments supported by harsh winter conditions that emphasise performance and reliability. Despite a slight recent decline amid broader economic pressures and rising price sensitivity, premium brands remain relevant. Citira’s new long-term partnership with Pirelli and acquisition of Dackia AB aims to consolidate and optimise premium tyre distribution across Sweden.
Scandinavian tyre service company Citira recently told Tyre Trends that Nordic countries have excellent potential for premium tyres during a discussion over its partnership with Italian tyre major Pirelli.
Speaking on the market potential, Chief Executive Officer David Boman said, “When it comes to the Nordic markets, Scandinavia in particular has a relatively high share of premium tyres across categories including passenger car, light truck and TBR segments. Compared to other global regions, the demand for premium tyres here is notably strong.
“One of the main reasons for this is the seasonal nature of our market. Winter tyres, in particular, drive a more premium-oriented approach because of the need for high performance and safety under harsh conditions. While we’ve observed a slight decline in the premium tyre share over the past few years, it still holds a significant portion of the market. This demand is closely tied to seasonal safety concerns, especially in winter, autumn and early spring. Drivers here prioritise safety and reliability, which naturally supports the continued relevance of premium brands like Pirelli.”
He noted that the decline is likely tied to broader financial challenges in the market, especially following the Covid period. Both consumers and companies have become more price-sensitive, making cost a bigger factor in purchase decisions.
As a result, there’s been a gradual increase in demand for lower-cost, imported non-European tyre brands, while the market share of European premium tyre brands has slightly decreased.
Pirelli and Citira have entered a long-term strategic partnership aimed at enhancing their market presence in Sweden. As part of the deal, Citira will acquire Dackia AB that has a network of 102 retail outlets from Pirelli.
In return, Pirelli and Dackia have signed a supply agreement extending to 2030, ensuring Pirelli remains the main tyre supplier. The transaction, pending regulatory approval, is expected to close by 2025. The partnership will boost Pirelli’s distribution and market coverage while supporting Citira’s goal of expanding a sustainable, flexible and high-quality customer service network.
THE PACT
Citira currently runs over 50 tyre shops and over five retreading units across Scandinavia and Poland. “Citira is actively working towards creating a more efficient and consolidated tyre market. While our current focus is primarily on the Scandinavian region, it’s not out of the question that we may consider expanding beyond this geographic perimeter in the future. This agreement is part of a broader industry trend where partnerships and acquisitions are used to enhance efficiency, strengthen distribution networks and provide end customers with better service coverage,” revealed Boman.
Nonetheless, the deal specifically pertains to the Swedish market, and as part of the regulatory process, Citira has conducted a market analysis to understand the potential implications on market share. However, the specifics of that study were said to be confidential and could not be disclosed prior to the official closing of the deal.
Explaining how this partnership will influence the supply chain of premium tyre in the Nordics, Boman said, “We do anticipate some changes, particularly within Citira. We operate a number of logistics centres, and this partnership presents an opportunity to optimise our overall supply chain setup. Enhancing logistics will be a key enabler of better service and responsiveness in premium tyre distribution.”
He added, “This particular deal is unlikely to have a direct or immediate impact on independent retailers or smaller distributors. More broadly, the Scandinavian tyre retail sector is undergoing consolidation. Several players are actively reshaping the competitive landscape and that trend could gradually influence the positioning of independents. But again, this specific acquisition is not a disruptive event in that context.”
Alluding to the current demand for replacement tyres, he said, “In general, the tyre market has proven to be quite non-cyclical. Even in challenging economic conditions, it tends to remain stable. That said, I believe we’re entering a phase where circularity and life-extension solutions will gain more momentum. We’re likely to see increased focus on services that extend tyre life, especially for larger fleets. This shift won’t just be driven by cost or fleet uptime concerns but increasingly by environmental responsibilities.”
THE BUSINESS
According to Boman, Pirelli represents a very minimal share of Citira’s overall sales, currently. However, the strategic partnership mainly revolves around Dackia and Pirelli, and the former is intended to become part of the Citira Group. “Moving forward, there is definitely an opportunity to deepen the collaboration with Pirelli and potentially grow their share within our overall brand mix,” added Boman.
Citira currently follows a multi-brand strategy and will continue with it even after closing of the deal. Besides, it is also involved in process and sales of retreaded TBR tyres and wheel rims.
“We operate a facility in Poland where we refurbish truck and bus rims. The process involves media blasting and repainting the rims to restore its appearance and functionality. The logic behind it is quite similar to retreading. In most cases, the structural integrity of the rim is still intact; it’s just the surface or aesthetics that degrade over time. By restoring these rims, we’re able to extend the life and reduce waste,” said Boman.
The company operates five retreading facilities collectively, located in Finland, Sweden and Poland. It uses both hot-cure and cold-cure retreading methods. Hot-cure is used in Poland and cold retreading in Finland and Sweden. Annually, it retreads around 160,000 tyres, averaging about 13,000 per month. While its current focus is on retreading, Citira is actively exploring expansion into tyre recycling as part of a broader push towards sustainability and circularity.
The company also manages tyre distribution for fleets across countries. Its circular tyre distribution approach involves not only delivering new tyres to customers but also collecting used tyre casings from them. These casings are then sent back to its retreading facilities, creating a closed-loop system. Besides, Citira has different suppliers across Europe for sourcing tyres for retreading.
MARKET WATCH
Citira sees a strong willingness in the market for consolidation and it has already engaged in several partnerships. Commenting on market challenges, Boman said, “One key challenge is the need for a player capable of driving consolidation at a larger scale. In the Scandinavian markets, this kind of brand-independent consolidation hasn’t really taken place over the last 10 to 15 years. Previously, consolidation efforts were primarily led by tyre manufacturers or affiliate networks players. However, consolidation has largely been on hold recently, leaving space for an independent actor to step in. We see that opportunity clearly and believe it is well received both by other market participants and customers. The challenge lies in successfully executing this consolidation while maintaining trust and delivering value across a diverse market.”
Commenting on the demand for retreading, he said, “The Scandinavian market has a long tradition of retreading heavy vehicle tyres. Currently, there is a growing shift towards pay-per-kilometre or tyre-as-a-service models, especially among large fleets like bus companies and hauliers. Notably, public tenders increasingly require a certain share of retreaded tyres, reflecting a strong environmental focus. Retreading extends the life of a tyre by reusing about 70 percent of its original material, making it a significant sustainability tool. The market share of retreaded tyres is gradually increasing with expectations that the retread market will grow faster than the new tyre market in the coming years.”
“The main challenges for the retreading industry lie in overcoming the longstanding perception that retreaded tyres are merely a low-cost option rather than an environmentally friendly and sustainable product. This is mostly prevalent is Scandinavia and it is crucial to shift this mindset by educating customers and the broader market about the true benefits of retreading. Moving away from a purely price-driven sales approach to one that highlights quality, durability and positive environmental impact remains a significant hurdle for the industry,” he added.
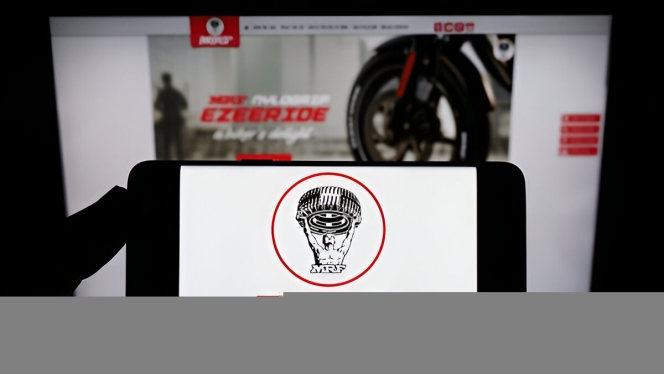
MRF reported a 12 percent decline in first-quarter consolidated net profit as rising input costs offset a 7percent increase in total income.
Consolidated net profit fell to INR 5 billion for the quarter ended 30 June from INR 5.7 billion a year earlier, the Chennai-based company said in a statement. Total income rose to INR 70.82 billion from INR 72.80 billion in the same period last year.
Profit before tax dropped to INR 6.7 billion from INR 7.6 billion year-on-year, with the company booking a tax provision of INR 1.7 billion for the quarter.
“Despite the increase in total income, profits for the quarter ended 30 June 2025 declined due to an increase in input costs,” MRF said in its press release.
The results come amid challenging market conditions that weighed on demand. “April 2025 started with a tariff issue, which was followed by a war in May and then early monsoons. This led to subdued market sentiments,” the company said.
Original equipment (OE) vehicle sales across most categories were either negative or flat, except for the farm segment, which remained unaffected by the disruptions, MRF noted.
Despite the headwinds, the company posted nine percent quarter-on-quarter growth in total income compared to the previous three-month period.
Comments (0)
ADD COMMENT