Davanti Tyres will set up a new innovative European Development Centre at Applus+ IDIADA in Spain, which will be used for its next-generation tyre design.
The British tyre company said the hi-tech facility will allow the company’s research and development team to experiment more with innovative new designs and materials, speed up new product development and enhance ongoing testing and improvement of its existing range.
With greater access to IDIADA’s world-leading proving grounds all year round, Davanti will be able to push the boundaries of innovation further than ever, utilising year-round wet and dry testing facilities to develop new products, solve challenges facing the whole tyre industry and strategically plan new developments further into the future to expand Davanti’s product offering.
“This is the biggest step Davanti has taken since we brought our first tyre - the DX390 - to market,” said Davanti Tyres General Manager Peter Cross. “We will now be able to physically trial a greater number of prototypes at an earlier development stage in order to ensure our next generation of products establish a new benchmark for excellence.
“Successful products require extensive development testing on proving grounds. Having our own facility on-site at IDIADA will allow us to gather a much greater amount of data on what developments work well and what do not in a way that we could never learn purely from computer simulations or lab results.
“Investing in the European Development Centre gives us a platform to be a driving force in the development of next-generation tyres. As environmental regulations change and the way vehicles are designed and built evolves, tyres will need to adapt.
“We're a dynamic brand and we need the bandwidth in our testing and development capabilities to match our expansion plans for the medium and long term.
“This facility gives us the flexibility to continue to be innovative and disruptive within the market. To think boldly and ensure Davanti is at the forefront of tyre innovation at a time of significant change.”
Davanti has equipped the facility with a suite of cutting edge tyre analysis and design equipment and it will be the brand’s hub for all prototype engineering and testing.
It will also open up the site for its customers, allowing them to see Davanti’s research and development processes first-hand and giving engineers a direct line of communication to the market to help steer development to suit changing customer demand.
Davanti has also committed significant investment to the project despite the ongoing global pandemic. According to Peter, waiting to develop driver safety and tyre efficiency was not considered an option.
“Covid has presented every industry in the world with challenges this year,” he said. “But what it has shown is innovation, investing in ideas, is always a good investment.
“Throughout 2020’s cycle of lockdowns and restrictions people have still needed to use the roads safely. Davanti’s primary commitment has always been road safety and we remain dedicated to improving that in everything we do.
“Our team will now be able to explore what the market needs from our next generation of tyres. How to optimise performance, enhance safety and develop a range of tyres which meets the needs and expectations of not just the drivers of today, but the drivers of tomorrow.”
BendPak Launches Compact 10AP-SRT Two-Post Lift For Specialised Service Shops
- By TT News
- August 19, 2025
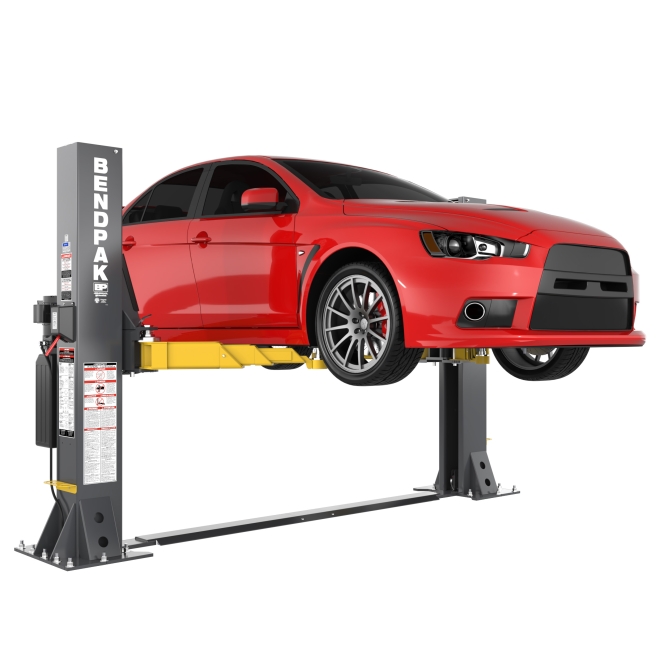
BendPak has added a 10,000-pound capacity model to its innovative AP-SRT Series of short-rise two-post lifts, following the successful launch of the 12,000-pound 12AP-SRT earlier this year. Designed for tyre shops, brake service centres and detailing operations where full-height lifts are unnecessary, these compact solutions combine productivity with space efficiency.
Standing just 93.5 inches tall with a 46.25-inch maximum lift height, the AP-SRT Series enables ergonomic vehicle access without the bulk of traditional lifts. The new 10AP-SRT features BendPak’s triple-telescoping swing arms for versatile positioning and low pad heights, while the Automatic Swing Arm Restraint System (ASARS) ensures stability with 2,000+ pounds of locking force.
Optimised for fast-paced environments, the lift’s high-performance power unit accelerates cycle times, and its symmetric/asymmetric configuration options accommodate diverse vehicles. ALI Gold Certified for safety, the 10AP-SRT comes with BendPak’s 5-2-1 Warranty, covering structural components for five years, hydraulics for two and parts/labour for one.
Sean Price, Director of Product Development, BendPak, said, “Many shops lift vehicles only partway, yet they’re forced to buy full-rise lifts that cost more, take up more space and get used at half capacity. Our 10AP-SRT and 12AP-SRT models are purpose-built to fill that gap – giving shops a cleaner layout, better efficiency and a safer overall working environment. From sedans to light-duty trucks, the BendPak 10AP-SRT delivers the performance, efficiency and safety today’s shops demand, without the excess height or cost of a full-rise lift.”
The Last Man Standing: How A Perth Startup Became The Mining Industry’s Tyre Whisperer
- By Sharad Matade
- August 13, 2025

Vehicle Management Corporation survived industry consolidation to dominate a USD 1.5 billion niche managing mining’s most expensive consumables.
More than 30 years after its modest beginnings, Fernie’s Vehicle Management Corporation (VMC) now leads the global independent tyre management software sector. The company oversees USD 1.5 billion in tyre and rim assets across 480 mining sites on multiple continents. With individual mining tyres costing upward of USD 50,000, VMC’s enTIRE software has become critical for operators aiming to maximise the value of their most expensive consumables.
“We don’t sell tyres or offer tyre services – software is our sole focus,” Fernie said. This specialisation has been VMC’s core competitive strength and a key reason it outlasted larger, better-funded competitors during two decades of industry consolidation.
VMC’s journey from a single-client DOS application to managing billions of dollars in assets demonstrates how even small software firms can thrive by addressing highly specialised industry needs that larger solutions often overlook.
THE CONSOLIDATION SURVIVOR
VMC’s fierce independence stands out in a tyre industry where consolidation is accelerating. While giants like Bridgestone and Michelin snapped up rivals – Otraco and Klinge, respectively – VMC has held the line, rebuffing takeover interest and prioritising customer relationships over shareholder pressure or supplier alliances.
“With Bridgestone acquiring Otraco and Michelin purchasing Klinge, VMC became the only independent, commercially viable tyre management software provider remaining,” Fernie explained. “Developing a competitive independent system today would require USD 5+ million in funding and years of field testing, making our market position difficult to replicate and any alternatives difficult to justify.”
This independence is now central to VMC’s appeal for multinational miners working with multiple suppliers. Unlike manufacturer-backed software, VMC’s enTIRE system is completely agnostic, allowing clients to base their purchasing decisions solely on performance data and cost-effectiveness.
That strategy has earned VMC unusually durable client ties. Its three-decade partnership with Freeport Indonesia – one of the world’s largest mining operations –underscores the appeal of a model that favours operational flexibility over vendor lock-in, a growing concern among customers wary of manufacturer-driven ecosystems.
“Most of our clients are long-term,” Fernie noted, emphasising how this stability has become increasingly valuable as mining companies seek to avoid the disruption and data loss that often accompanies vendor changes in manufacturer-controlled systems.
BEYOND COST CUTTING: SAFETY AND ENVIRONMENTAL IMPACT
While cost reductions – often 10 percent to 30 percent within three years – drive initial adoption, VMC’s impact extends far beyond savings. In nonstop mining environments, where tyre failures can lead to life-threatening accidents, safety and uptime are equally vital.
“Operating tyres outside pressure or load specs increases blowout risks,” Fernie said, emphasising safety. enTIRE tracks rim certifications and keeps failure histories, supporting safety protocols. “Rim accidents are very dangerous, potentially fatal.”
Environmental benefits have also emerged as an increasingly important value proposition for mining companies under growing pressure to reduce their carbon footprints and waste generation. By extending tyre life and dramatically reducing premature failures, mining operations generate substantially less waste while simultaneously improving fuel efficiency through optimised tyre pressure monitoring systems.
“Optimising pressure with TPMS can extend tyre life by 20–30 percent, reduce rolling resistance and lower fuel consumption by up to three percent – a substantial saving in mining operations,” Fernie explained. In an industry where fuel costs represent significant operational expenses and environmental regulations continue to tighten, these seemingly modest percentage improvements compound into substantial savings and meaningful reductions in environmental impact.
The environmental mathematics are compelling: operators can achieve approximately 30 percent increases in tyre life through proper lifecycle management, directly reducing landfill waste, shipping requirements and manufacturing demands – collectively helping reduce the carbon footprint of tyre procurement and disposal across the mining sector.
THE TECHNOLOGY EVOLUTION
VMC’s technological evolution, from humble beginnings as a basic DOS program to advanced, cloud-based solutions, reflects the broader digitisation revolution in factory operations that began in the early 1990s. The firm’s flagship enTIRE software began as a Windows product with what Fernie recounts with clear pride as a ‘pioneering drag-and-drop interface’ in the early 1990s – a cutting-edge user experience design that was decades ahead of its time.
The platform has progressed steadily through several generations of technology, transitioning from Microsoft Access databases to high-performance SQL Server implementations, which have significantly improved performance and scalability. It introduced full multi-site support features in 2001 and incrementally incorporated tyre pressure monitoring systems (TPMS) from seven sensor vendors starting in 2007. The software industry award was presented in 2005, when the system was named the Financial Review Australian Information Industry Association’s ‘Best Industrial Software Application’.
Recent development efforts focus heavily on artificial intelligence integration for enhanced analytics capabilities and predictive maintenance functionalities. “We’re actively using AI to streamline development and support,” Fernie said, outlining the company’s forward-looking technology strategy. “We expect AI will significantly enhance predictive analytics, client dashboards and user interfaces, improving how data is interpreted and acted upon.”
The integration of multiple TPMS systems represents a particular competitive advantage. “enTIRE PressureNet is sensor brand-agnostic and integrates with multiple sensor types, unlike many manufacturer-locked systems,” Fernie explained. “Our independence allows clients to choose or switch sensor brands without losing backend compatibility.”
FIGHTING FRAUD IN HIGH-STAKES OPERATIONS
In addition to optimising operations and pre-emptive maintenance, enTIRE is an advanced fraud detection and prevention solution in settings where a single tyre costs more than high-end cars. The software’s detailed tracking identifies many forms of theft, tampering and misbehaviour that afflict the high-end tyre market throughout global mining operations.
“Tyre fitters may scrap a near-new tyre (if not tracked) and then this tyre would be picked up from the scrap location and resold,” Fernie explained, detailing one common fraud scheme. “In mining, each tyre can be worth up to USD 50,000. This potential additional income is very significant in developing countries.” The financial incentives for such fraud are substantial, making comprehensive tracking systems essential for asset protection.
Beyond simple theft, the system prevents more sophisticated data manipulation during high-stakes contract negotiations. “If a tyre supply contract is worth USD 100 million, there can be significant pressure placed on operators of any tyre management system to ‘modify’ tyre performance in a supplier’s favour,” Fernie said, highlighting the system’s role in maintaining data integrity. “enTIRE has very strong internal systems to prevent internal tampering.”
Other fraud prevention features involve detecting unauthorised tyre replacement in off-site fleet operations, where drivers may sell new tyres and substitute them with less expensive ones, and preventing early scrapping of tyres that can otherwise be retreaded or reallocated for a longer service life.
ORGANIC GROWTH STRATEGY AND MARKET POSITION
VMC has achieved its market-leading position without relying on venture capital investment or large corporate sponsorship; instead, it has relied on diligent organic growth fuelled by strong customer relationships, word-of-mouth referrals and relentless reinvestment in product development. The firm purposefully reinvested earnings in automation technologies and enhanced software capabilities, rather than engaging in fervent hiring or costly promotional campaigns, while maintaining lean operations and establishing increasingly refined development capabilities.
“When large manufacturers’ systems failed with over-engineered projects, clients often came to us for reliable replacements,” Fernie said, describing a pattern that has accelerated during recent supply chain disruptions when tyre shortages made lifecycle extension critical for maintaining operational continuity.
The company’s fundamental growth strategy centres on systematic data accumulation and market share expansion. “Our strategy, early on, has always been to increase market share as we realised that the more tyre performance data our systems controlled, the more valuable we would become,” Fernie explained, articulating a network effect strategy that becomes more powerful with scale.
This field-tested software, combined with deep industry connections and vast databases, now creates major entry barriers that would require competitors years and millions to overcome.
DIVERSE APPLICATIONS AND INDUSTRY DIFFERENCES
VMC software supports significantly disparate operating models in mining and transport industries, each with dissimilar tracking demands and cost-justification criteria. Mining applications typically involve high-cost, low-volume tyres that are closely monitored by operating hours. In contrast, transport fleets manage high-volume, lower-cost tyres, which are tracked by kilometres and frequently shared across interchanging trailers pulled by various prime movers.
“Mining justifies the cost of extensive data entry based on the large cost savings, while the transport industry is more careful regarding tracking cost,” Fernie explained, highlighting how economic incentives drive different implementation approaches across industries.
Its flexibility in covering these differing operational needs while ensuring consistent data quality and analytical functionality across both industries is possible with the software.
GLOBAL EXPANSION AND CULTURAL ADAPTATION
VMC continues to expand its global presence, with a specific emphasis on high-growth regions such as Africa, Indonesia, India, Eastern Europe and Latin America, where a large demand for advanced asset management solutions arises from growing mining activities and infrastructure projects.
The firm has local teams offering multilingual support capabilities. However, cultural adjustment remains a continuing challenge in emerging markets as they transition from legacy manual systems to online platforms.
“We adapt training and user interfaces to local literacy and workflow styles,” Fernie said. “Regional teams help bridge gaps in communication, training and change management, ensuring smoother adoption.”
Main entry barriers in emerging markets include the absence of sound local technical support, the scarcity of internet infrastructure in geographically remote mining sites, the reluctance to change due to entrenched manual systems and administrative hurdles involving payment reliability and bureaucratic delays.
FUTURE TECHNOLOGY AND INDUSTRY TRENDS
Future software updates mirror industry-wide trends towards greater automation and the integration of artificial intelligence. On the horizon are planned improvements, including richer analytical dashboards, enhanced cloud analytics capabilities, mobile inspection tools with integrated image capture capabilities and AI-driven notification systems for predictive maintenance notifications.
As autonomous and electric cars increasingly penetrate mining fleets, VMC’s strategic emphasis on tyre and rim information, rather than vehicle powertrains, places the company well-positioned to meet emerging transportation technologies without necessitating drastic system architecture adjustments.
“enTIRE tracks data independently of vehicle type, so electric vehicles are managed the same as diesel fleets,” Fernie explained. “Our focus is on tyre and rim data accuracy – not the powertrain.”
INDUSTRY CHALLENGES AND MARKET OUTLOOK
The tyre management industry faces ongoing challenges related to data accuracy and actionable insights. “The industry’s main challenge is accurate and actionable data,” Fernie observed. “Successful tyre management operations start with accurate data collection, management and transparent reporting.”
Supply chain disruptions have strengthened demand for VMC’s services as tyre shortages heighten the importance of lifecycle extension and predictive maintenance. “Our strongest growth has been when there have been tyre shortages and clients want to extend their current tyre life as much as possible,” Fernie noted.
For Fernie, who brings over 30 years of experience in tyre management software development to the industry, VMC’s continued success validates the strategic decision to remain independent in an increasingly consolidated market. “Just ‘being there’ and remaining independent will always attract customers from non-independent tyre management systems over time,” he said, expressing confidence in the company’s long-term competitive position.
In an industry where margins of operation are crucial and safety must not be compromised, VMC has established a highly profitable niche by addressing complex problems that most individuals never even consider – until a USD 50,000 tyre blows on a distant mining operation thousands of miles from the nearest replacement. For mining operators globally with billions of dollars in mobile equipment, that specialised expertise and uncompromising independence have been worth their weight in gold.
Comerio Ercole Participates In Oerlikon Nonwoven Event
- By TT News
- August 12, 2025
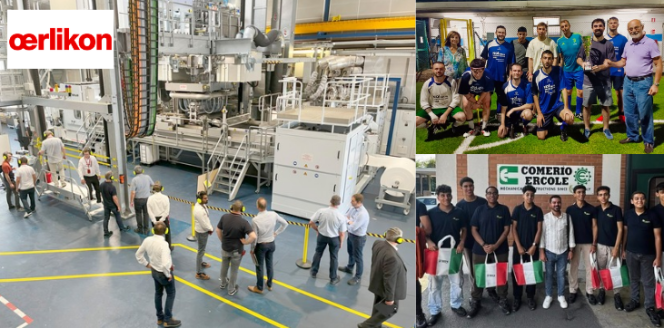
Comerio Ercole participated in Oerlikon Nonwoven's exclusive Technology Centre Open House in Neumünster, Germany, on 2-3 July 2025. The event attracted over 50 industry professionals for interactive demonstrations and technical discussions on nonwoven manufacturing innovations.
As a key partner, Comerio Ercole presented its latest calendering solutions, highlighting their role in enhancing finishing processes through precision engineering and energy-efficient designs. The company emphasised its collaborative approach in developing customised systems tailored to industry needs.
Attendees observed live demonstrations of Oerlikon Neumag's hydro-charging technology for meltblown media and spunbond production lines for specialty materials. Partner companies contributed additional insights across the production chain, from fibre treatment to final winding solutions.
The event showcased how strategic partnerships drive progress in nonwoven manufacturing, with Comerio Ercole demonstrating its commitment to integrated, innovative production technologies.
The Comerio Ercole team said, “We believe that delivering value to our customers means not only providing advanced machines but also being part of a well-coordinated and forward-thinking network.”
BendPak Launches Ranger RB30T Hybrid Wheel Balancer For Truck And Bus Wheels
- By TT News
- August 07, 2025
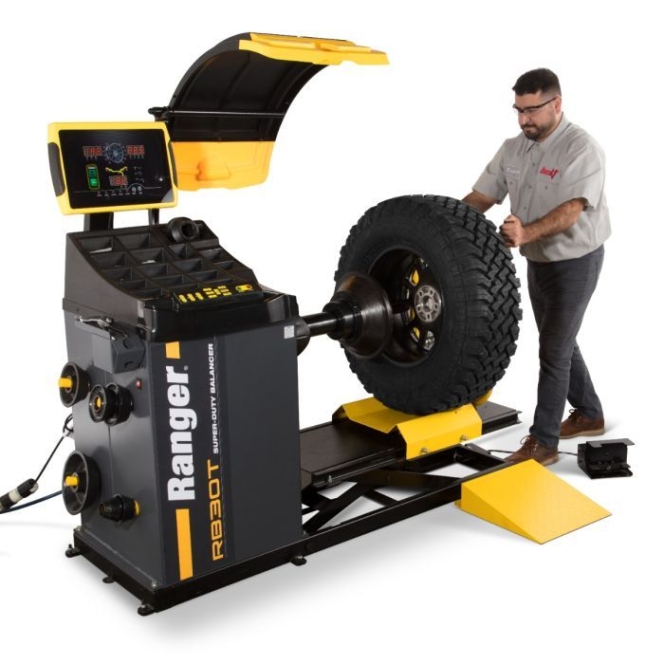
Designed to tackle the largest truck and bus wheels while maintaining precision for passenger vehicles, the RB30T Hybrid Wheel Balancer from Ranger (a BendPak division) delivers power and versatility. Switching between heavy-duty and light-duty applications is effortless, requiring just a button press. Its integrated pneumatic wheel lift enhances safety and ergonomics by minimising manual handling and reducing injury risks.
Capable of balancing wheels for buses, semi-trucks, OTR vehicles, light trucks and cars, the RB30T ensures fast, accurate results without recalibration. Its re-engineered platform supports wheels up to 330 lbs (approx. 150 kg), 49.25 inches in diameter and 20 inches wide, with rapid cycle times – seven seconds for car wheels and around 20 seconds for full truck assemblies. At its core, the Ranger Drive-Check system uses advanced 64-bit processing and quartz piezoelectric sensors to detect even the slightest imbalances across multiple axes. This smart technology simulates real-world driving conditions, identifying vibrations before they become road issues and automatically recommending optimal corrections.
Built for durability, the RB30T features a ribbed nylon-fibre drive belt, counter-weighted flywheel system and a three-phase motor with solid-state phase conversion for smooth, high-torque operation under heavy loads. The balancer comes ready to use with a commercial mounting kit, including cones and adapters, while its spacious top tray and side shelves keep wheel weights and tools organised for efficient workflow.
Available as a standalone unit or with the Ranger Select package – which includes professional installation and training – the RB30T is a robust solution for shops handling diverse wheel balancing needs.
Sean Price, Director of Product Development, said, “The new RB30T wheel balancer can do it all. Its versatility makes the RB30T a great choice not just for heavy-duty fleets and repair garages but also for high-volume tyre shops and mixed fleets.”
Comments (0)
ADD COMMENT