- Cummins Group in India
- Cummins India
- Cummins
- Annapurna Vishwanathan
- Earl Newsome
- Global Competency Center
- GCC
- ER&D
Tyre machinery investments during changes in innovations: Overview and mitigation strategy
- By 0
- April 20, 2020
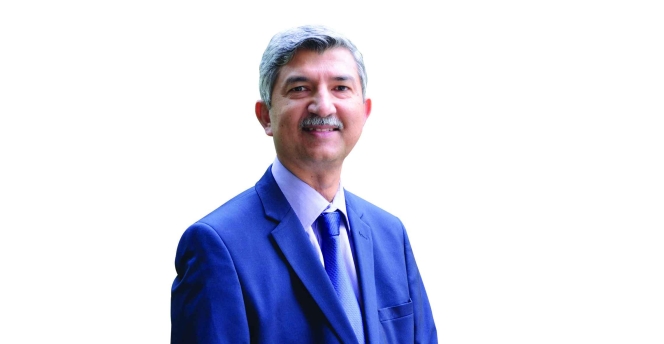
By G Unnikrishnan, Senior Vice President at JK Tyre & Industries Ltd
While relentlessly working to meet these ever-growing demands through the addition of new capacities and capital spending, the tyre industry encounters the additional challenge of having to keep up with even faster advancements in the technology in their products and processes
The global tyre market, with a current production base of about 3 billion units - including replacement and OEM markets - is expected to surpass $300 billion by 2023 with a nearly 5 per cent world average CAGR. This growth is enabled by rising demand, healthy economic trends, vehicle production, and after-market demand from a wide variety of end-users worldwide.
While relentlessly working to meet these ever-growing demands through the addition of new capacities and capital spending, the tyre industry encounters the additional challenge of having to keep up with even faster advancements in the technology in their products and processes. Here are five key drivers coming from different directions for the tyre industry. They are incremental and radical innovations in products, customer demands in performance/delivery, environmental concerns and regulations, and need to improve manufacturing efficiency.
While these developments are promising and bring with them high-growth opportunities, they require tyre manufacturers to continually modify their products and processes to keep up. Tyre producers and, as a consequence, their machine and technology suppliers face a risk of obsolescence of their production assets with each adopted innovation.
Consequently, the future of any tyre or machinery manufacturer hinges on their ability to seamlessly adapt to this plethora of changes and forge ahead to new areas of profit not to be left behind by competitors.
This article is an attempt to understand how the tyre industry can navigate the tricky waves of change such that they not only manage to stay afloat in the industry but also thrive by grasping emerging opportunities. Tyre companies need to deep-dive into the drivers, enablers, and the resulting technological impact on machine manufacturers (see figure 1), and chart a mitigation strategy
Drivers and Enablers
1) Incremental product innovations - evolutionary progression in the industry.
One major area of focus in the tyre sector presently is energy-saving tyres, one that will only increase in prominence in the future. Expanding to energy-saving tyres, however, will prove to be tricky for machinery manufacturers since some of the essential processes involved - Lightweighting, special compounds, and thinner components - put considerable pressure on extrusion, stock preparation, handling, and assembly. Compounding and mixing area will see more of new processes such as liquid phase mixing and advanced materials.
When it comes to truck tyres, wide base technology will gain momentum in low RR radial tyres. As a result, there will be an increased need for tyre building machine to have advanced Centering and Application systems to reduce the impact of splices and improve component Centering for tyre appearance and quality.
2) Radical product innovations: Revolutionary changes in the industry
Profound transformations in the automotive field like smart tyres, electric mobility and autonomous driving call for more innovative concepts in tyre design and production.
Similarly, emerging concepts like run-flat tyres, air-less tyres and 3D printed tyres entail special features in machinery. Any tyre machinery manufacturer that wishes to remain relevant and differentiate globally needs to evolve rapidly, particularly in technology.
3) Changing customer delivery demands: Dynamic in nature
Car models are increasing in number and so is the complexity of tyre designs, resulting in more tyre variety and smaller lot sizes needing more number of moulds and quick changes in different process equipment and moulds. Also, the machines that manufacture should have flexibility and agility features to adapt swiftly to increasing product complexity and customer specifications.
Finally, as a machinery manufacturer, one must ensure the tyres produced using the machinery has the highest manufacturing accuracy and consistency to meet the customers’ specifications meeting overall quality standards and make tyre production competitive in this volatile market developments.
4) Manufacturing efficiency - a perpetual process
Tyre producers will continue to face increased competition on price, quality, delivery and pressure to reduce the tyre development life cycle, perform with fewer employees amid frequently changing product performance demands. Scarcity and growing costs for real estate is another major challenge. Hence enhancing the process efficiency in every stage of their manufacturing process would be an emphasis.
Compounding and Mixing fields bear the most significant potential to enhance efficiency with Liquid phase mixing and Automation. In the curing process, split component curing of tread and carcass separately is foreseen to dominate the industry eventually. So is the shift from mechanical to hydraulic and electric movements. Electric heating and steam elimination are also gaining popularity.
End-to-end traceability of all materials and components throughout the manufacturing and supply chain will be mandatory in the future.
5) Exponential technology: It is Automation Now:
Growing dependence on automation technologies by tyre manufacturers to meet the changing demands by performing operations such as processing, assembly, inspection, or material handling, in some cases accomplishing more than one of these operations in the same system is a welcoming trend. It is needless to state that Automating a manufacturing operation increases production rate, uniformity, conformity to quality specifications, reduction of defect rate, and manufacturing lead time, thereby reducing the work-in-process inventory. Process consistency is another critical area of paramount importance. The work is also made safer.
A higher level of automation in TBM is foreseen while it transports and assembles various components to build green tyres. TBM of the future will be with quicker and more accurate synchronisation system to give better tension control and edge placements, ergonomics and safety. A key role will be played by automated testing and data analysis technologies which can supplement traditional inspection to reduce errors and increase cost-efficiency. Consequently, higher investment in automation has become economically justifiable to replace manual operations.
Industry 4.0 : Quantum Leap in Performance:
In recent years, the traditional manufacturing industry is challenged worldwide with the digital transformation that is accelerated by exponentially growing technologies(e.g. intelligent robots, autonomous drones, sensors, 3D printing). Digitalisation allows easy integration of interconnected smart components inside the shop floor, that is the basis of the so-called Industry 4.0, and that is made possible by the widespread adoption of information and communication technologies by manufacturing companies. Major tyre manufacturers and their suppliers now are fully embracing the opportunities being presented by digital manufacturing taking full advantage of digitalisation and making use of new business models make it possible to get there.
The resulting conflict
The above mentioned best practice technologies representing the diffusion of innovation need to be implemented into the production process regularly and also when making new investment decisions in capital stock. This cycle of regular initiatives will lead to machinery upgrades and fall squarely onto the machinery manufacturers and even obsolescence risk of the current asset of tyre producers.
Machinery manufacturers, on the other hand, foreseeing the emerging challenges from tyre companies, are often confounded when investing in new technology. It is unthinkable to converge both at a breakneck pace. Years pass between the upgrades for both and risk of the business falling behind competitors grows. The goal of tyre producers and machinery manufacturers is to resolve these conflicts by synchronising and converging to meet the demands proactively.
Summarising, it is the brisk pace of change by tyre manufacturers, exponential technologies and automation that is driving tyre machinery manufacturers to invest more in R&D, evolve rapidly in technology that is leading to the obsolescence in capital asset.
A Mitigation Strategy: From Talk to Action
In many cases, the more pragmatic approach for tyre manufacturers would be to mitigate obsolescence risk instead of attempting to eliminate it. Following is a step-by-step method to doing so during this regular cadence of innovation. (Refer to fig 2 for a comprehensive outline)
To reap maximum benefit, tyre manufacturers need to implement their mitigation strategy in the form of an organisation-wide initiative, addressing both new projects (in “structural” approach) and regular operations (in an “infrastructural” approach).
This means that in addition to focusing on mitigation in new projects, tyre manufacturers must also continuously enhance the value of their current assets. Ultimately, they can succeed in building a sustainable ecosystem capable of thriving in an ever-changing industry if they perform a sort of an organisational and cultural transformation of their entire system.
Though specific mitigation strategies will vary from one organisation to another, I have distilled the initiatives into five distinct pillars to prepare the best-practice plan:
1. New Project Philosophy
2. Manufacturing Process Philosophy
3. Organisational Transformation
4. Enhancement of value of current capital assets
5. Product planning
For a good reason, when a company embarks on capacity expansion, it is essential to have a project philosophy to stick to. Such a philosophy involves paying attention to flexibility in process and machinery, scalability, and retrofittability, besides capital productivity and process efficiency. Keeping pace with current trends in machinery and digital technology is also vital. Various disciplines in manufacturing such as Automation, Exponential Technology, OEE, Energy efficiency, smaller equipment footprint, and equipment with Total Cost of Ownership (TCO) need to align well to avert investment risk effectively.
It is imperative to avoid isolated patches of automated systems. Adopting an “Open process automation” (OPA) vision is far easier to maintain and update leads to enhanced value addition. Doing so will gain additional traction to eventually replace large CapEx automation retrofit programs with smaller OpEx programs. Standardisation is another crucial and common layer which cut across machines, parts, processes, materials, components and toolings.
On the manufacturing process philosophy front, using the lean approach to seek opportunities to simplify the process and cut non-value adding steps is a major step for process agility and efficiency. The lean approach through a Near Net Shape process (NNS) by getting rid and combining of process step (for, e.g., calendar-less belt/body ply making), incorporating more concurrent steps and transforming semi-continuous processes to continuous processes is the way.
Tyre companies should seriously consider modularity and flexibility to be amenable for scalability, extensibility, mass customisation, and to reduce the risk of upfront investment. Modularity and flexibility will also enable them to move closer to customers and to have agility. To maximise the benefit, continuous progression in process technology is necessary, which will give inputs to the above project philosophy. Faster adoption of exponential technologies and Industry 4.0 compliance will dramatically boost the effectiveness of the mitigation plan. The loop will be completed when the project plan drives product engineering and eventually aligns products to the finalised plan.
It’s time to realise, also for a good reason, that attention must be paid to organisational transformation initiatives such as co-creation with customers and vendors, speeding-up the technology trend for first-mover advantage and shifting from product features back to service to customers by assisting capability building. Building the ecosystem proactively before product innovations, having technical change as part of investment analysis, moving from CapEx to OpEx by out-sourcing of customised semi-finished stocks (for, e.g., compounds) and components and capability building in emerging technologies by taking full support of machine manufacturer is critical. Another fundamental mindset change needed is valuing “generalists” rather than “specialists” as it is the key to creative breakthroughs involving recombining or reimagining things that already exist. All these initiatives eventually will lead to foreseeing the requirements well in advance and reengineering and upgrading the assets to contemporary level in functionality with minimum investments at a more predictive pace.
I would also like to emphasise that, while investing in the right technology is essential, the biggest challenge is not limited to selection - ultimately success or failure depends on the timing and requires assessing the Technology Readiness Level (TRL) and exploiting the full potential of new technologies.
Additionally, a robust technology forecasting and product/process lifecycle management by creating a “sunset” policy for older products and machinery are paramount to cover investment risks. Another key initiative is on the product front - efforts should be put to increase the market share of current products through value enhancement and penetration of new markets. Product migration using adjacent technologies with appropriate reconfiguration in processes and layout is also vital. These initiatives will enhance the value of current capital assets and as a result, boost risk mitigation.
Now What?
The underlying goal of a mitigation strategy is to quantify the risk involved and determine the measures that make most business sense to soften the impending obsolescence. A phased approach would be to first identify and define the goals and scope of the obsolescence plan with dedicated qualified resources. Next is to prioritise the measures bringing the most value to the business and making sure they are aligned with the company vision.
It would help to initiate pilot projects and capability building to better plan for adopting advancing technology and ease the shift to the next paradigm, allowing you to embrace the future in stride. Make sure company leadership is ready and willing to champion your approach with a broader range of factors in mind focussing on an ecosystem.
Charting an action plan for the investments and technology needed such that there is minimum risk is a demanding task. Doing this will enable them to expand the firm’s productive capacity and produce quality tyres that are cost-competitive by infusion of modern technologies and that meet customer demands. The investment would turn attractive after a reasonable period putting the business on a more robust and competitive footing.
But the optimism is that companies responsive to automotive market trends and fast-changing technologies with a robust risk assessment and technology management will come out on top.
G. Unnikrishnan is a tyre technical professional with over 30 years’ experience. He is currently Senior Vice President at JK Tyre & Industries Ltd. The opinions and observations presented here are his own and do not represent that of any company or organisation
Engineering Giants: OTR Tyres… The Science Behind Extreme Performance
- By Ertugrul Bahan
- August 15, 2025
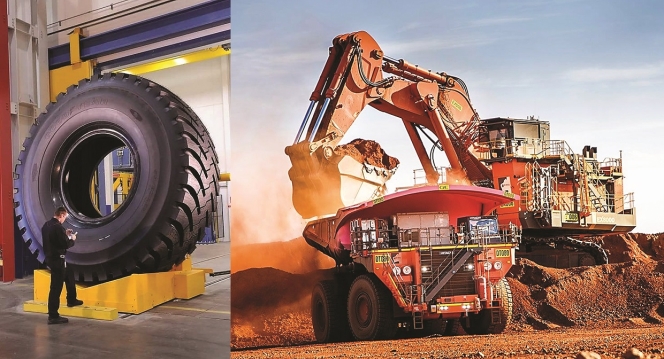
OTR tyres, rugged design and advanced technology that withstand the most demanding conditions... From mining to construction, these giant tyres play a critical role in keeping industries running smoothly.
What does the term ‘off-road tyre’ mean to us? Giant, robust, special and imposing – a tyre for heavy-duty vehicles. While there are already some tracked loaders and cranes on the market, stationary work, excavation, loading and transport are carried out with mobile machinery in open-pit mines or on heavy-duty construction sites. Transport vehicles, cranes and large-capacity loaders are always equipped with robust and durable rubber tyres. The last 50 years have seen a true revolution in the off-road tyre segment, as tyres have become larger every decade. Newer dump trucks have higher load capacities, requiring the installation of larger tyres to meet this growing demand.
Today 3,500-plus hp engine big haulers loaded carriage capacity reaches to 400-plus tonnes equipped with a tyre such as 59/80R63 extra load size. Such trucks are coupled with loaders having a shovel capacity of 60 tonnes on open pit areas. These load capacities are enormous, and the new generation of trucks offers even more. Tyre sizes up to 63/80R63 or some other size combination with low platform and wider dimensions are in the market.
Thirty to 40 years ago, tyre sizes for 50-80-tonne haulers were around 36.00-51 or smaller. Today, we are talking truck carriage capacities of 450-500 tonnes with hybrid engines. More efficient AC electrical drive haulers and having tyre sizes up to 70-inch rim size tyre are on the pipeline. These vehicles will be able to accommodate tyres with a diameter of over four metres, a weight of over 5.5 tonnes and a load capacity of over 120 tonnes per tyre.
High-tensile reinforcement materials and new generation rubber compound technologies play an important role in these revolutionary developments.
Extreme conditions, extreme performance, heat and puncture resistance for uninterrupted operation... This is how OTR tyres master harsh environments (quarries, mines, construction sites).
Tyres for open-pit mining, underground mining and construction remain separate categories. Their dimensions and basic requirements also vary. However, load capacities and the number of autonomous structures with electric motors and ultra-wide tyres are steadily increasing. The use of advanced materials in self-monitoring tyres with integrated pressure and wear sensors will become more widespread. Giant radial tyres for electric vehicles will proliferate on the market.
Tyre demands for extreme load-bearing capacity, improved cut and tear resistance (against sharp, abrasive stones) and improved heat dissipation through deep tread patterns will increasingly prevail, in line with customer demands. While the tread depth of off-road tyres was only 50 to 60 mm in the 1970s, today’s deep-tread off-road tyres reach 100 to 110 mm. Radial construction with new compound and heat dissipation technologies enables off-road tyres with deeper tread patterns, which also represents a significant advantage for the circular economy. Low-temperature off-road tyres also offer higher and multiple retreadability.
Both bias-ply and radial off-road tyres face significant challenges such as heat, abrasion, traction, sidewall cuts and fire protection. Although current off-road tyre technology has advanced significantly compared to earlier radial off-road tyres, some brands use bias-ply reinforcement layers, primarily on the sidewalls or tread, for improved cut resistance. Bias-ply off-road tyres remain preferred for certain applications, particularly forestry and some mining tyres.
Titan International (USA) underscores its strong presence in the truck tyre market with its Mining & Construction Bias division. This underscores the strategic priority of these specific applications in the OTR tyre market. In the US, Titan focuses on cut-resistant compounds and special tread patterns for rock environments that perfectly meet the most stringent performance requirements of bias construction.
Michelin, Bridgestone and Goodyear dominate the OTR tyre market, with demand varying regionally. Large tyres for mining, underground mining and construction require durability, heat resistance and smart technology to meet the changing needs of the industry.
Michelin, Bridgestone and Goodyear dominate the global OTR tyre market, but Continental and BKT are also important players. Titan, Yokohama, the Chinese company ZC Rubber and the Indian company Apollo are other niche players that could disrupt global markets with more affordable alternatives. Furthermore, regional demand varies considerably between Asia, North America and Europe due to different mining, construction and regulatory environments. This benefits the different brands, whose combined commercial and technological strengths differ.
Michelin, Bridgestone and Titan (North America and Australia) produce giant mining tyres up to 63 inches wide. BKT, Apollo and ZC Rubber produce low-cost mining tyres in Africa, Latin America and India. Michelin and Bridgestone generally offer smart, autonomous tyres in North America and Europe. Yokohama and Continental (Japan and Scandinavia) offer underground and speciality tyres.
For open-pit mining, powerful electric-powered dump trucks and wheel loaders will offer exceptional load-bearing capacity (over 100 tonnes per tyre). They feature cut and chip resistance (against sharp, abrasive rocks), heat dissipation and a deep tread pattern, which will become increasingly popular.
Underground mining vehicles with narrow low-profile tyres and dump trucks (LHD), on the other hand, will be equipped with compact, fire-resistant low-profile tyres. Their low flammability, puncture resistance and high manoeuvrability will also be important criteria.
Large Scale Construction vehicles like massive dozers, graders, dumpers, articulated dump trucks and motor graders will need high traction tyres for both mud and loose surfaces with reinforced sidewalls to avoid cuts and having high longevity (mixed on road/off road use).
OTR tyre manufacturers compete on durability, profitability and performance. Their primary challenges are extending tyre life, optimising fuel efficiency and reducing wear.
All of the major OTR tyre manufactures need to compete in this high demanding segment of the tyre industry. The biggest challenge in every segment is achieving a long service life without tyre failure. Improved traction and rolling resistance, as well as reduced maintenance requirements, are real advantages.
The cost of a set of tyres is always divided by the total number of labour hours to determine the unit cost per tyre hour. Various parameters influence tyre and other operating costs. To minimise fuel and tyre costs in mines, better road maintenance, operator training in environmentally friendly driving (acceleration/braking), monitoring tyre pressure and loading and the use of predictive analytics (telematics to measure fuel consumption and tyre wear) are essential.
Overloading increases tyre stress, accelerating wear and fuel consumption. Poor road conditions with potholes and spills lead to more cuts and flat tyres, increased rolling resistance and higher fuel consumption. Harsh acceleration or braking always leads to overheating and faster wear. Although large radial-body trucks cost nearly USD 100,000, every preventative measure and maintenance is essential for business reasons.
Innovations such as RFID, flame-retardant compounds and environmentally friendly materials are driving the industry forward. OTR tyre manufacturers compete with specialised designs: mining tyres must be cut-resistant, earthmoving equipment must be durable and port tyres focus on efficiency.
Tyre manufacturers must survive in this highly competitive and demanding industry. Mining tyres are exposed to extreme conditions and require cut resistance thanks to highly abrasion-resistant compounds and additional steel belt layers. Earthmoving tyres require flexibility and durability thanks to all-season tread compounds and rock-resistant designs. Port logistics tyres feature low rolling resistance and chemical resistance thanks to lightweight steel belts. RFID tracking offers real advantages for tyre tracking.
Innovations for niche applications are also essential for brand building and address specific challenges. Some underground mining tyres feature non-marking and flame-retardant compounds for enhanced safety and performance. Arctic tyres require low-glass transition temperature polymers and microspike technology for better traction in extreme cold. As always, off-road electric tyres require improved efficiency and lower noise levels.
The use of recycled materials poses a real challenge for this segment, but more durable designs certainly reduce waste and replacement frequency. However, bio-based compounds and recycled rubber must be more widely integrated into new products.
Key trends in the OTR tyre segment include intelligent monitoring systems, environmentally friendly compounds and improved reinforcement techniques. Graphene-reinforced tyres promise extremely high strength and heat resistance. Sustainability will be a priority in OTR tyre manufacturing, with a focus on reducing environmental impact through innovative materials and designs.
Why Giant Mining Tyres Cost More Than Car
- By Adam Gosling
- August 14, 2025
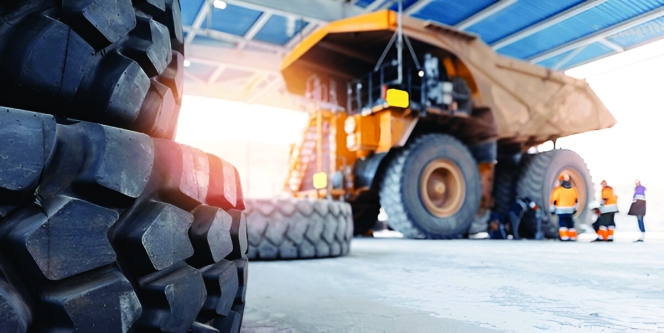
Imagine a giant tyre that weighs twice the weight of your EV, costing as much or more than your EV; you are looking at the largest truck tyres in production. Weighing over 3.5 tonnes and standing better than four metres in diameter, these giants are actually very sensitive.
Such tyres support loads of 100,000 kg; yes, that’s a single tyre. The truck fully loaded is more than 600 tonnes. To put that in perspective, that single tyre supports 50 average cars – that’s 300 cars in a single vehicle.
These tyres have to be managed very carefully to extract the maximum amount of work without destroying them. Overwork the tyres or engage in poor maintenance and the tyre can fail, sometimes catastrophically, and this can happen inside just a few hours of operation.
The OTR (off the road) tyre sector is at the cutting edge of tyre technology. It is paired with the other end of the spectrum being MotoGP tyres, which, whilst a light construction, are exposed to all sorts of side forces as the bikes achieve lean angles of 65 degrees. Both are cutting edge in tyre development.
OTR tyres can have up to 40 different rubber compounds that are required to work in harmony, which is one of the pinnacles of rubber manufacturing. There is deep engineering involved in having different rubber compounds within the one tread package. This happens for select MotoGP circuits where corners one way well outnumbers corners heading in the opposite direction. Your humble daily drive tyre is the result of all the testing and development that occurs within conception of these giant OTR and MotoGP tyres.
The tyre talk within the F1 paddock about tyres is old school for OTR tyres. For many years, a mining circuit was carefully monitored after the theoretical calculations had been made as to how far and fast could these giant haul trucks travel. The reasoning behind these parameters was based around the tread and compound selection. This is known as the tonne kilometre per hour factor. Some operations required a high-speed compound, which was usually less abrasion resistant but have a higher heat capacity. Whilst slower speed operations wore cut-resistant tread packages. Low-speed operations such as underground receive yet different tread patterns and compounds. Then there is the appropriate tread pattern and class to select.
In periods of high demand, there have been many attempts to produce OTR tyres, quite often with limited success. I observed one truck that had been fitted with an emerging manufacturer’s tyres that didn’t even get to the loading point before the whole tread package separated from the carcass. These giant tyres are fragile and sensitive.
Applying appropriate maintenance has been made proactive with the advent of real-time TPMS. Decisions on the vehicle’s duty cycle can be made depending on what level of work the tyre pressures indicate they are experiencing. Just like MotoGP and F1, the tyres are the limiting factor of performance. Even suspension issues can be identified as the load centre shifts towards the weak suspension component.
Unlike on road tyres that have a large safety margin designed into them, OTR tyres are often worked to their maximum, and in early days of mining, well overloaded and over run. When the OTR tyre supply went into shortage, many OTR tyre users realised that without appropriate management, the sustainability of their operation
would be called into question. Tyre costs can easily blow out and cause a lot of economic angst and pain.
Truck and fleet managers who are at the top of their game utilise real time tracking of the vehicles to identify their capacity for work, that is how far and how fast can the truck travel before the tyres become overheated. With a combination of GPS tracking and tyre pressure monitoring, tyres can be observed and the truck reallocated to a shorter lighter haul before the tyre sustains heat damage. A tyre is very much like a loaf bread or a cake; you can overcook it, and alas, the outcomes are not reversible. Once the cake is burnt, it’s ruined; an OTR tyre is no different.
With such an expensive asset, organisations have realised that without tyres, their operations come to a grinding halt. In TyreSafe Australia terms, “if they are not turning, they are not earning” has never been more factual than during an OTR tyre shortage. Executives have come to understand that tyres for a rubber-tyred haulage operation represent a very large cost centre, quite often in the top three or four expenses. There are many aspects to extracting the best performance from these gentle giants, but most importantly, it is the provision of the appropriate volume of inflation medium.
By engaging a tyre data management platform, such performance data and detail can be gleaned and used to programme maintenance and also to provide feedback for the production crews, who ultimately should be the ones paying for the tyre operational costs. A fresh mining area under development may well result in an increased number of cut and damaged tyres. The tyre crews see this on a daily basis as they attend their charges, but the old head in the sand attitude of ‘move more tonnes’ touted by some miners usually ends up being an economic disaster. Having observed operations driven by production tonnages, I have also been witness to the absolute waste of tyres that have been cut and damaged by poor operational practices. Such operations do not usually make a profit.
A tyre manufacturer can produce a superb product that has the potential to achieve best practice life, but if an end user drives over a rock that fatally injures the tyre, how is this reconciled? The tyre manufacturer has no control over what the end user does – the same as your daily drive where tyres are left unattended until there is a failure. Then it is the tyre’s fault, NOT!
The technology involved in being able to manufacture a rubber item with upwards of 36 different rubber compounds within the single tyre is enormous. Each different rubber has different properties the designer is seeking to utilise. Having these compounds adhere to the adjoining rubbers is a scientific mine field; it can work, but it can also come apart quickly.
Using software to design tyres both in constructional terms as well as the actual operational side of the tyre has meant that advances can be made within days rather than months or years. Having been part of a tyre development team, I had to wait for the new design tyres to be designed, then manufactured and shipped to site before being mounted. Only then can they go into operations where the research from the technical design team was proven. The software used today can now simulate the operations and identify any weaknesses in the tyre design even before the physical production mould is created. With CAD/CAM machines, now fine sipes within the tread pattern can be included. John F Sipe must be amazed to see the intricate patterns now being produced. The sipes not only provide better traction for on road tyres but permit a shorter heat path for OTR tyres.
When the tyre is operating, the resultant hysteresis is evidenced by the level of temperature rise within the tread and casing. The interface at the casing tread is the most sensitive and most easily damaged by overwork or overspeed, or under pressure. Excess heat is the mortal enemy of an OTR tyre.
With appropriate management of operational factors, an OTR tyre can be capable of many thousands of hours’ work. With bad management, the tyre may well die within just several hours.
By managing tyre inflation pressures, a sound reflection of the operation’s philosophy towards creating profit can be determined. The easiest way to ensure your tyres perform as the OEM designed is to monitor and maintain the inflation pressure. It’s not that hard, surely?
Take care, stay TyreSafe.
Degrees In Sustainability
- By Adam Gosling
- July 08, 2025
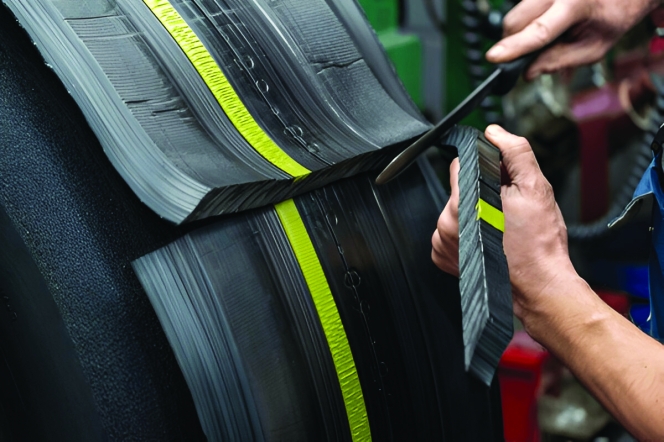
Raw materials and sustainability are symptomatic of a tyre when you think about it.
As a society very dependent upon mobility, our drivers and passengers need to be able to enjoy sustainable service from the tyres our industry produces. To date, primarily raw materials have been used in manufacturing, but there is a paradigm shift underway. The recyclability of tyres is as yet still a question more than a solution, from an economic perspective as well as an environmental approach.
As we are all observing, global economics is entering an interesting phase and hands are being outstretched looking for payment or retribution, or both.
The tiresome question in front of everyone is ‘what is the cost’?
a) Of not doing ‘it’
b) Of attempting to do ‘it’
c) Of being able to enjoy economic success to do ‘it’
d) Having positive outcomes for the environment or at least neutral
e) Option C as well as D, very hard to achieve this balance in my opinion, but nevertheless, is the most desired
The ‘it’ in this case is producing a tyre with no adverse effects or outcomes.
Tyre OEMs are progressing through the issue of designing tyre tread patterns as well as structural casing considerations (even down to acoustic considerations from inside the tyre’s air chamber) as the tyre in motion is now the largest noise generator (no engine or exhaust noise) on a current generation electric vehicle (EV). Having high levels of noise is part of modern life; however, as people, we don’t accept noise intrusion, especially inside the modern auto cocoon, sorry, car. How far do we push sustainability?
A tyre admirably demonstrates there can be reciprocity and sustainability between unlikely companions. Nominally, inflexible steel lives happily with totally flexible rubber whilst the road pavement (bound stone, cement or unsealed) abrades the tread rubber. From an unsustainable perspective, there are the tread road wear particulates (TRWP) that are generated at the tread pavement interface; huge questions here as the yet to be determined answers need to be found.
With more fuel-efficient propulsion systems, greater demands are placed on the humble tyre. Rolling resistance (of the tyre) is a major consumer of energy and now, not forgetting, aerodynamics too.
The global program of ‘safer vehicles’ also has impact on tyre performance not only on the overall life but also the traction / grip aspects. Vehicles that are heavier, faster and more responsive place increased demands on tyre performance.
WANTED: lighter, quieter, more grip in all conditions, longer life, greener, cheaper ... the holy grail.
There is a price to pay; as Isaac Newton stated, ‘to every action, there is always opposite and equal reaction’. This is a basic law of physics, the third law of motion. There is no free lunch; we usually pay in many ways, either in the short term, the medium or the long term, or in all terms.
Retreading is very much a partial solution using the casing of the tyre to yield second, third and more lives. Tyre OEMs have not favoured retreading in past times as for every tyre retreaded, a new virgin tyre was not required. Tyre manufacturing facilities operate on volume; the more they can produce, the lower the cost of each item. Selling more tyres was the only answer. Retreading has many benefits, and with modern electronics, the quality of the product can be as assured as a virgin tyre. In some cases, the performance of the retread can be superior to that of the original tyre. Retreading is a sustainable practise to a point. Eventually, the tyre’s structural casing will fatigue and fail. Commercial aviation tyres are retreaded numerous times as a matter of practise. An aircraft tyre will experience loads well in excess of that your daily drive tyre experiences. When the tread is worn down, it is replaced with a new tread package. The other very important consideration in regards tyre retreading is the reduction in the consumption of raw materials. A tyre is assembled using upwards of 40 percent carbon black. There is about 20 percent steel and fibre product whilst the rubber that converts to a petroleum oil during the pyrolysis process is the remainder. Every casing reused reduces the requirement for fresh raw materials and associated manufacturing.
Whilst recycling offers sustainability in a circular economy scheme, there is a long way to go before sustainability is actually sustainable. With increased recycling and the rise of the circular economy, past attitudes are being revised, modified, changed or rewritten. The prime hurdle to jump for this potentially emerging (recycling) industry is the refining of the end products tyre pyrolysis systems generate. The carbon black has many challenges before re-use for tyres. The oil also requires refining prior to replacing petroleum. What about the byproducts from the refining process? If the pyrolysis product is more expensive than the original raw material, will you as the consumer still buy cheap? If so, why are we, the tyre OEM s, investing in our ESG programme of sustainability?
Repurposing end-of-life tyres has great potential, but there are concerns around the outcomes if such products are used. Ground rubber used in uncaptured soft fall has been outlawed in some jurisdictions; even captured rubber such as in hot mix bitumen has outfalls (TRWP). Geological uses as ground support and river stream bank erosion mitigation are another limited use. The re-use of the raw materials is the ideal outcome, but sustainability is still a process in progress.
All processes are required to extract the highest outcomes from our raw materials as well now (with landfill diminishing capacity), thinking about end-of-life products (not just tyres, think about electronics, for instance, and the list grows), so there is a requirement to promote the recycling, re-purposing and retreading of tyres. The retreading facilities can be localised geographically to reduce the sea transport for virgin tyres from manufacturing facilities to the end destination. Pyrolysis and re-purposing facilities are best locally located, but there has to be a market for the downstream products; this is a crunch point. However, there are advantages that we are currently not availing ourselves of with the many economic benefits seemingly available. With export/import tariffs introduced or even if sea lanes are unable to be used to import/export tyres, then retreading capacity will be a license to print. There must be a strategic deliberation to include tyre retreading in national planning as well. Our mobile society requires tyres; from farm to plate, our food is supported by tyres for much of the journey, then there is the rest of life.
We should not underestimate the critical role tyres play in our global supply chains and mobility; however, the price we pay has to be sustainable in the long term. That means easing our demands on raw materials including the use of recycled products, but we also need to extract better performance not just from the tyres so much but also from the maintenance of the vehicles. In my overviewing large data sets of tyre life performance, it has been noted that ‘we’ use only about 65 to 70 percent of the available tread; many tyres are scrapped earlier than they should be as a result of irregular wear and/or poor maintenance. Considering the aids available today (namely drive over alignment pads, tyre pressure monitoring systems TPMS), there is little excuse for such dubious maintenance decisions stemming from sub-standard economic directions.
The old model of ‘produce more sell more’ has a large price to pay. Sustainability is now becoming a serious issue in our supply chains. We (businesses) have to be able to open the shop doors tomorrow, and that means generating capital reserves that enable us to pay the bills and put food on the table.
What price is sustainability? Are you prepared to pay today for tomorrow’s sake?
- Tyre
- rating
- sustainability
- RR EU
- natural rubber
- Tire Industry Project
- Global Platform for Sustainable Natural Rubber
- Forest Stewardship Council
- Continental
- Bridgestone
- Nokian Tyres
Sustainability… Innovations And Future Outlook
- By Ertugrul Bahan
- July 08, 2025
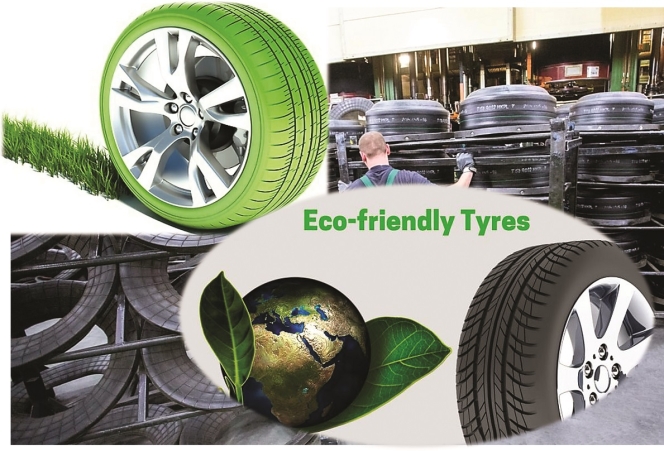
‘Sustainability Rating’ of vehicle tyres will be introduced as the ‘Recyclability Scoring’, i.e. will be more comprehensive than EU RR labelling rating
News, statements and trends from industry players indicate that the ‘Sustainability Rating’ for vehicle tyres will soon become the focus of discussion. This rating will be assessed based on the manufacturer’s carbon footprint, microplastics volume per abrasion percentage and the proportion of sustainable raw materials. In other word, it will be the `Recyclability Scoring` of the tyre itself and its manufacturer. In addition, the mass value of used tyres meanwhile will be assessed based on the sustainability rating of the ELT (end-of-life tyres). So that is why ‘Tire Passport’ label of tyres in the market is currently under regulatory discussion.
Meanwhile, used tyres will become more environmentally friendly in the near future, which will have a significant impact on the improvement of sustainability ratings of ‘end of life tyres’ in the market. The concept of ‘sustainability Rating’ may be a bittersweet experience for most industry players. It is for sure not the same meaning of having `A` grade RR EU labelling rating. However, once sustainability criteria are fully defined on regulatory basis, we should be ready to take a closer look at design, production and disposal requirements.
Tyres with a higher sustainability rating receive the highest rating, meaning they have the best carbon footprint. These tyres contribute more effectively to the carbon neutrality of the entire manufacturing industry due to their near-zero carbon footprint during the production phase.
Regulatory pressures impose tyres industry to radical changes, driven by various dynamics and developments as it traditionally depends heavily on non-renewable petroleum products and natural rubber from rubber trees, which contribute to deforestation.
A significant portion of global CO2 emissions are attributable to the tyre industry as it has long years of weak carbon neutrality and the negative offsetting capability of greenhouse gas emissions released into the atmosphere that should be avoided. Linking to this deficiency, regulatory pressures impose tyres industry to radical changes, driven by various dynamics and developments, including innovations in nanomaterials and the emergence of new environmentally friendly raw materials.
Traditional tyre production relies heavily on non-renewable petroleum products and natural rubber from rubber trees, which contribute to deforestation and resource depletion. The tyre industry has been contributing significantly to environmental pollution, resource depletion and waste accumulation up to now, but sustainable innovations can help reverse these impacts.
Natural rubber, the main material in the tyres industry, is responsible for the deforestation of approximately four million hectares of forest each year in Southeast Asia. Synthetic rubber relies on petroleum and soot emits three tonnes of CO₂ for every tonne of carbon produced. Tyre production releases zinc, lead and sulfur into waterways. New regulations require higher recycled content and stricter emissions standards. Present tyres mostly harm aquatic life and lead to fish mortality.
The tyre industry’s sustainable development momentum is rapidly evolving, driven by regulations, automotive imposements, material innovations and circular economy models.
Manufacturing emissions are significant. However, approximately 70 to 85 percent of a tyre’s total carbon footprint is generated during use but most of this part is unavoidable since tyre itself is a running phenomenon; friction and tractive base drag force is inevitable. So only limited part of it can be regained, but for achieving long-term savings over the tyre’s lifetime, any gain still is important for the total saving. This awareness has led to innovations in tyre design that reduce rolling resistance and improve fuel efficiency, thus delivering significant environmental benefits throughout the product life cycle.
Automakers are also on the line to force all parts manufacturers to compel and demand more environmentally friendly tyres to meet their own sustainability goals. Fleets and transportation companies are seeking fuel-efficient tyres to reduce their operating costs. Sustainable practices often lead to long-term savings through energy efficiency and waste reduction. On the other hand, environmentally conscious retail consumers increasingly prefer sustainable products.
Dandelion rubber is an organic alternative to conventional rubbers. However, some tyre manufacturers use drought-resistant guayule plantations. The attractive point is that some manufacturers already are producing tyres consisting of 50 percent sustainable bio-based raw materials, recycled rubber powder and reclaimed carbon black. Rice husk ash silica is an innovative material that replaces conventional silica, improving sustainability while utilising agricultural waste. Bio-based synthetic rubber is on the way as a source of bio-based material.
What challenges do remain? The transition to bio-based raw materials, recycling and smart tyres is irreversible. Stricter regulations such as bans on tyre wear microplastics and advances in bioengineering are expected to dominate the next decade while sustainability is now a key competitive advantage.
Tyre manufacturers are already working on retreading programmes, devulcanised rubber and pyrolysis outcomes such as rCB, oil and hydrogen – all to improve sustainability. Resource savings through virtual modelling and AI are underway.
Tyre manufacturers are already working on retreading programmes, devulcanised rubber and pyrolysis outcomes such as rCB, oil and hydrogen – all to improve sustainability. Resource savings through virtual modelling and AI are underway.
Real-time data synchronisation, simulation and prediction, known as ‘digital twins’, allow scenarios to be tested before implementing concrete changes. The integration of AI and machine learning improves predictions and eliminates multiple testing steps, resulting in significant resource savings. These advanced technologies promote more sustainable design, production and use.
Sustainability challenges require joint actions. Tyre manufacturers are working together through various initiatives. For example, the Tire Industry Project (TIP) brings together major companies to advance sustainability research programmes. The Global Platform for Sustainable Natural Rubber (GPSNR) promotes responsible rubber sourcing. Other joint technical standardisation efforts include the Carbon Black Recovery Guidelines. This collaboration helps establish common standards, share best practices and accelerate progress across the industry.
Retreading programmes are highly sophisticated and can extend the service life of the original tyres by up to 80 percent. Possible options include 100 percent recycling of used tyres through pyrolysis and devulcanisation. Pyrolysis converts them into recovered carbon black (rCB), which reduces CO₂ emissions by 30 percent. Pyrolysis oil is to be used as synthetic rubber oil or hydrogen (H₂) can be used or stored as a clean fuel for tyres factories after its gasification and purification. Devulcanization of recycled rubber, on the other hand, breaks the sulfur bonds in the rubber so it can be reused in new tyres.
Sustainable practices often lead to long-term savings through energy efficiency, waste reduction and new and futuristic technologies.
While challenges remain, the tyres manufacturers’ shared commitment to ambitious sustainability goals demonstrates that the industry recognises its environmental responsibility and is determined to contribute to the fight against climate change. Thanks to technological advances and the increasing adoption of sustainable practices, the vision of a truly green tyre industry is becoming increasingly clear.
Recently, some tyre manufacturers have begun placing the ‘Forest Stewardship Council (FSC)’ logo and a tree-shaped label on the sidewall and packaging. This globally recognised sustainability logo can influence tyre-purchasing decisions. Some criticise the FSC for its lack of commitment, but an average quarter of the total mass of these tyres is made from sustainable materials to make it less harmful to the planet. This voluntary system encourages companies to go beyond government regulations.
Michelin, Continental and Bridgestone aim to use 100 percent sustainable materials in their tyres by 2050. Nokian Tyres aims for 50 percent renewable or recycled materials by 2030. Continental plans to use more than 40 percent sustainable materials by 2030. Stricter regulatory changes could expedite the fulfilment of these commitments.
Sustainable practices often lead to long-term savings through energy efficiency, waste reduction and new and futuristic technologies. Environmentally friendly production can help tyre manufacturers from the competition and enhance their brand images.
Investments in sustainable development secure the future of companies in the face of stricter regulations. Sustainable materials are now profit drivers and not just only compliance tools. Companies lagging in adoption risk market irrelevance by 2030.
Comments (0)
ADD COMMENT