GUIDE TO RUBBER SELECTION
- By Dr. Samir Majumdar
- December 29, 2020
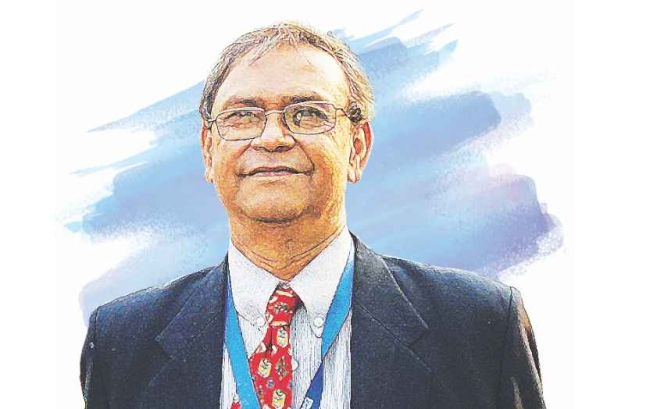
In the 1930s, when rubber became one of the essential commodities, selection was never a problem because we had only Natural Rubber (NR) that time. Today, beyond 2010, there are number of elastomers are being used in the industry and the choice is typically important with respect to the competitive advantage of both, durability in the service and cost.
NR was called rubber because it could have rubbed out pencil mark. When other synthetic rubbers were produced, they had also similar property of rubbing out pencil mark, but were called elastomers because NR was then typically identified as Rubber. However, both NR and other synthetic rubber (SR) together are called elastomers, because they had typical elastic properties and interestingly, all rubber and elastomers are high polymers. From the time 1930 , industries have increased many folds of time. Engineering requirement in the manufacturing industries, with respect to temperature, pressure and durability have also simultaneously increased and our demand on the applications have also been increased.
CAPTION Fig.1: Asia Pacific Total Elastomers (54%), NR+SR
With very competitive demand in the market, all rubber properties cannot be achieved only by NR. Balancing critical demand for rubber applications, that we require in our day to day life, use of SR or blending with SR has become very common practice in the industry today.
For example, other than pneumatic tyre, there is hardly any uses of NR these days in automotive industries. Uses of various grades of EPDM, Silicone rubber (Q), Nitrile rubber(NBR), Fluoro Elastomers (FKM) , Perfluoro Elastomers (FFKM) , Hydrogeneted Nitrile rubber (HNBR), Chlorosulphonated Polyethylen (CSM), Polychloroprene(CR) , Polyurethane Rubber (AU/EU), Fluorosilicone Silicone Rubber (FQ) etc. have been increased due to typical automotive parts requirement. Since automobile spares are now mostly manufactured in Asia Pacific countries, they are the largest consumer of total elastomers (Fig.1).
CAPTION Fig.2: Only SBR is the highest (47%) synthetic rubber
After NR, the next high consuming elastomer is SBR (Fig.2) because of its higher filler and oil loading capability and higher abrasion resistant quality. After SBR, the next high quantity rubber used is BR, followed by IIR (BIIR,CIIR) and EPDM. Recently silicone rubber uses have increased many fold times in Western countries, China, Japan, Korea and in India. However, the total SR uses remains highest in Asia Pacific(Fig.3).
CAPTION Fig.3: Asia Pacific Highest Consumer of SR (48%)
In critical applications, it is therefore, advisable to give considerable thought, or take advice, on the formulation of the compound. As the potential for 'tailoring' compound to specific applications is essentially limitless, it is often advisable to carry out preliminary qualification tests to ensure that the compound chosen will perform as intended by customer need.
A considerable thought in critical applications, for the formulation of the specific compound need considerable experience with selecting raw materials and art of processing. Very common mistakes by rubber compounder is mostly related to incorrect selection of (1) ingredients, (2) their doses, (3) rubber blends and (4) correct machines. Rubber compounding is an art of developing rubber mixtures with suitable raw material and their doses, that will perform in desired services but with minimum cost possible such that product can be competitive in the market and can be processed well in machines without any difficulties faced by man and machines.
There are broadly two classes of Rubbers or elastomers, they are Natural Rubber (NR) and Synthetic Rubber (SR). NR occurs naturally in the plant and hence the name but all synthetic rubbers are man made rubbers and are produced by chemical synthesis. Among the Synthetic elastomers, there is again two category; one is general purpose rubbers (GPR),which can be used as equivalent to NR, e.g., Butadiene Rubber (PBR) and Styrene Butadiene Rubber (SBR) and the other category is specialty elastomers. Specialty elastomers are generally costlier than GPR and are only used in special purpose. Following are the list of specialty elastomers ,which are widely being used in rubber industry beyond 2000:
Butyl Rubber (IIR), Chlorobutyl Rubber (CIIR), Bromobutyl Rubber (BIIR), Chlorinated Polyethylene(CM), Chlorosulphonated Polyethylen (CSM), Ethylene Acrylic(EEA) , Ethylene Propylene Rubber(EPM) , Ethylene Propylene Diene Rubber(EPDM), Fluoro elastomers (FKM), Hydrogenated Nitrile Rubber (HNBR), Isoprene Rubber (IR), Nitrile Rubber(NBR) , Polyacrylic Rubber (ACM), Perfluoro Elastomers (FFKM), Polychloroprene (CR) , Polysulphide Rubber (TR) , Polyolefin Elastomer (POE), Polyurethane Rubber (AU/EU) , Silicone Rubber(Q), Fluorosilicone Silicone Rubber (FQ) etc.
Elastomers having carbon-carbon double bond on the elastomeric backbone could be cross-linked with sulphur and accelerators. Many of these elastomers are also could be cured with organic peroxides, examples are NR,SBR,BR, AU/EU, CM, CR,CSM,EPM,EPDM,FPM,NBR,HNBR,IR,POE,Q,FQ. Elastomers that cannot be cured with organic peroxides are; ACM,IIR,CIIR,BIIR,ECO.
Rubber compounding
Rubber compounding is an art of developing rubber mixtures with suitable raw material and their doses, that will perform in desired services but with minimum cost possible such that product can be competitive in the market and can be processed well in machines without any difficulties faced by man and machines. In all rubber industry today, the biggest challenge is cost reduction of a good quality product. During selecting raw materials, therefore, the cost of these will also play a vital role in compound designing.
A rubber product might require desired physical properties and ageing properties. For this one need to add particular reinforcing filler or a suitable combination of reinforcing fillers to have desired physical properties. The typical ageing resistant property may be achieved with only NR by adding suitable anti-degradants or, NR could also be blended with synthetic elastomers with better ageing resistant property. NR being cheaper and easily available it is the first choice having good strength, abrasion , tear strength and low heat development in dynamic condition. A synthetic rubber product might require good green strength , in that case either NR or blend of rubber is the choice. For example, for better green strength of CIIR, it is often blended with NR.
CAPTION Fig.4: Turn-up Bladders
A rubber product may require a specific need , say air retention property or oil resistance property. For the former case the choice is essentially butyl rubber (or, halobutyl rubber , CIIR,BIIR) and for the later it is usually, NBR/HNBR and for both oil resistance and air impermeability, the usual choice is NBR / HNBR rubber (Turn-up bladder for tyre building operation, Fig.4). For a typical product, if the property demands oil resistance at 200 0C, then the choice is FKM (Fluoroelastomers) or Q. For resistance upto 328 0C , it is FFKM.
CAPTION Fig.5: Typical Industrial Gaskets
Heat resistance property is typically related to product durability and sustainability at desired temperature and is very important for various industrial gaskets (Fig.5). For temperature resistant rubber compounding and following temperature resistance of the polymer is important, NR ~ 65 °C, SBR ~ 75 °C, NBR ~ 110 °C, HNBR ~ 180 °C, Q ~ 200 °C+, FKM ~ 240 °C, FFKM ~ 328 °C. The temperature ranges quoted are only a rough guide, because the temperature resistant property also depend on the typical compound design as well, depends upon the particular application, and may depend on detailed differences between alternative versions of the same rubber.
Rubber compound is always developed as per customer need. For any rubber article, the first choice is the selection of right rubber. Rubber is selected mostly on the basis of :
- Cost
- Heat and/or Oil Resistance
- Temperature Requirements
- Energy Absorption
- Seal Ability
- Flex Resistance
- Water Resistance
- Gas Impermeability
- Electrical Properties
- Abrasion Resistances
- Dynamic Properties
- Flame Resistance
Rubber compound related definitions
- Elastomer, a polymeric material that recovers substantially to its original shape after significant deformation at room temperature.
- Compound, a mixture of elastomer and other materials that is intended to process (mold) satisfactorily and meet end-use specifications.
- Filler, a particulate material added to an elastomer that modifies both the workability and the end-use behavior of the resulting composition.
- Plasticizer, a material added to an elastomer to improve its workability.
- Resins are added to improve rubber tack.
- Waxes also used as plasticizer , are also added for smooth finish of rubber articles.
- Antioxidant, a chemical added to a compound to slow or prevent oxygen attack on the compound.
- Antiozonant, a chemical added to a compound to prevent ozone attack.
- Cross linking agent, a chemical added to a compound to link the long molecules in a polymer together, or to assist in the cross-linking process.
- Accelerator, a chemical added to a compound to increase the rate of cross-linking in the compound.
- For example, sulfur links the long molecules, while an accelerator increases the cross-linking rate.
- Retarder, a material added to an elastomer compound to delay the onset of cross linking (scorch).
- Vulcanization is same as cross-linking but with sulphur.
- Peroxide also helps in cross-linking process.
Elastomer blends
Elastomer blends often creates problem when two different types of unsaturated rubbers are mixed and vulcanized together. For example, NR and IIR have two different unsaturation level and hence both sulphur , ZnO and black flows more towards polar rubber, on NR phase, and results undercure in IIR phase and the resultant blend vulcanizate becomes spongy and cannot be used.
GPR (NR,SBR,BR) rubber could be blended to any proportion. For higher synthetic rubber level (BR,SBR) , accelerators dose is often adjusted to higher side and sulpur level is adjusted to lower side, because for equivalent curing, BR, SBR requires more accelerators as compared to NR. Stearic acid is added 2-3 phr with only synthetic elastomer and for NR, stearic acid dose of 0.5 phr is enough.
CAPTION Fig.6 : Micro Dispersion of Rubber Blends
Practically most of the polymers are not miscible to 100%, polymer blends usually consist of micro-dispersion of one rubber into the other rubber and this results after intensive mixing of these two different polymers. These micro dispersed rubber often has dimensions around 0.1-1.5 nm(Fig.6). When fillers are also mixed into such blends, a situation may develop in which the filler unevenly distributed between two phases. Such uneven distribution of fillers, naturally effects the uniformity of compound physical properties. In most blends the effect on the properties of blended elastomers depend on:
- The polymer compatibility
- Distribution of fillers in different phases and
- The degree of cross-links between rubber phases
Though NR,SBR,BR could be blended to any proportion , yet the blended phases are not compatible to hundred percent and there is also phase separation, where, on proper identification one can witness that there is phase separation with NR & SBR, NR & BR, BR & SBR. However, upon proper mixing these phase differences could be minimized (Fig.7) such that the resultant blend gets cured almost homogeneously . That is why very highly dispersed NR (5 to 10 parts) could also be co-cured with IIR.
CAPTION Fig.7 : Well Dispersed Rubber Blends
IIR cannot be blended with GPR but can be blended with EPDM (having ENB diene content between 2-3 mole%) to any proportion. Higher diene content EPDM rubber (ENB, >9.0% mole) could be well blended with GPR. If high diene content EPDM is blended with IIR, filler, sulphur, accelerator and zinc oxide flows more towards EPDM than IIR. IIR could be blended with CIIR and BIIR to any proportion. Such blend is often used in making tyre inner-tubes and hose jacket compounds. When CIIR and BIIR doses are on the higher side with IIR (>60phr) it is worthwhile that zinc oxide is added in the final batch since zinc oxide is curative for CIIR & BIIR.
Besides zinc oxides, CIIR and BIIR can also be cured with sulphur/accelerator system as well. However, for very good heat resistant property, they are often cured with ZnO. Highly dispersed plastic (LDPE) could also be blended with CIIR/BIIR with no detrimental effect but with improvement on air permeability.
CIIR and BIIR could be blended to any proportion with GPR. Such blend is often used in tyre inner liner. When CIIR and BIIR doses are on the higher side (>60phr) both zinc oxide and amine type anioxidant/antioxonates are added in final batches as these are curatives in CIIR and BIIR.CIIR blend with GPR and EPDM is used in PC sidewall for glossy finish sidewall and addition of CIIR also help to reduce the curing time of PC tyre. Blend of EPDM/NR/SBR and EPDM/NR/SBR/CIIR are often used in tyre side wall compound for better look.
CR rubber is not normally blended in the industry as it is mostly used in adhesive industry. However, they can be blended to any proportion with GPR. In adhesive industry crystallinity is important and CR gives the highest degree of crystallinity among all general-purpose rubber. CR could be blended with IIR , close to 5-15 phr, for bladder making and in general, only 5.0 phr is added in the beginning of the mixing cycle.
In bladder mixing, Zinc oxide could be mixed with CR in master batch. CR is premasticated in mixing mill for making bladder compound, before adding in Banbury.CR/BR blend is used in hose covers.CR could also be blended with GPR at any proportion like CIIR. Both zinc oxide and amine type antioxidant / antioxonates are added in final batches as these are curatives in CR and CIIR.
In general Silicone rubber (MQ,PMQ,VMQ) cannot be blended with any other rubber because of phase difference problem but highly dispersed EPDM could be blended with it upto 10 -15 phr. EPDM/Q blend is used in heat resistant cover roll compound.
EPDM, being a good elastomer as weather resistant and heat resistant is often blended with number of other elastomers to get the benefit of the vulcanisates.
EPDM/CR blend are very popular in making gaskets. EPDM/IR blend is widely used in car wiper rubber blades. EPDM/SBR blends are used in gaskets, sponges and hose stocks. EPDM/CSM blend is used in transmission belt, conveyor belt and in hose covers. EPDM/LDPE blend is very popular in making cable insulation compound.
NBR in general, is not blended with other elastomers as this rubber having higher degree of polarity , is exclusively used for oil resistance property. It may have acrylonitrile content ( ACN) ranging from 18-50%. Incase of higher oil resistance, the elastomeric grade is selected with higher ACN. For better abrasion however, 10-20 phr of BR could be added to NBR with the aid of good dispersing agents , used in shoe sole, high abrasion resistance rolls and in conveyer belts. Higher ACN content will have better abrasion property. NBR could be cured both by sulphur/accelerators or by peroxides. Hydrgenated NBR (HNBR) has emerged into market with better heat resistant property as compared to NBR. For intermediate heat resistant property NBR and HNBR could be blended.
NBR/SBR blends used in hydraulic hose tubes, high pressure hose, belt cover, idler roll compounds and in gasket compounds. NBR/PVC blend and NBR/PVC/BR blend are used for roll cover compound, very popular in electric cable insulation and in closed cell sponge applications in shoe industry. XNBR/PVC blend is used for heavy duty cable jackets, roller cover, belt cover, hose cover stocks etc. NBR/IR blend and NBR/TR blend is popular in colored or non-black roll covers. The later is mostly used in printing roll cover compound.
Lummus Technology And InnoVent Renewables Partner To Advance Global Tyre Pyrolysis Solutions
- By TT News
- June 11, 2025
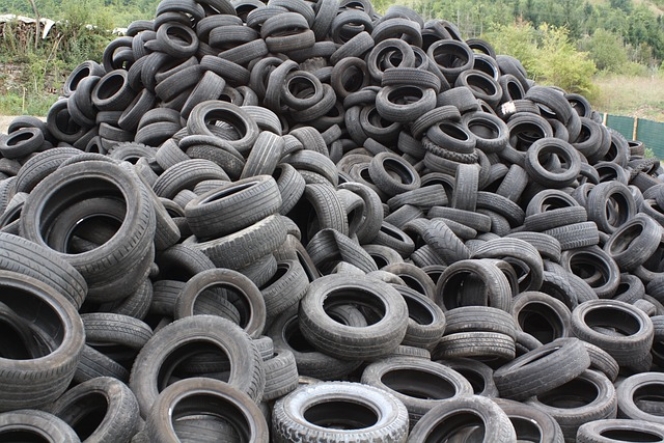
Lummus Technology, a leading provider of process technologies and energy solutions, has signed a memorandum of understanding (MoU) with InnoVent Renewables to collaborate on the global licensing and deployment of InnoVent’s continuous tyre pyrolysis technology.
Under the proposed agreement, Lummus will become the exclusive licensor for InnoVent’s proprietary pyrolysis process, which transforms end-of-life tyres into valuable outputs, including pyrolysis oil, gas, recycled carbon black and steel. Additionally, Lummus will offer integrated technology packages that combine InnoVent’s pyrolysis system with its own downstream processing solutions, enhancing the value of fuel and chemical products derived from waste tyres.
InnoVent’s technology provides a fully scalable, end-to-end solution for converting discarded tyres into renewable fuels and high-value petrochemicals, covering everything from pre-processing to purification. The company currently operates a commercial-scale facility in Monterrey, Mexico, with an annual processing capacity of up to one million passenger tyres, and has the capability to expand further.
Leon de Bruyn, President and Chief Executive Officer, Lummus Technology, said, “This is another significant step in expanding and strengthening our portfolio for the circular economy. By combining InnoVent’s tyre recycling technology with Lummus’ global licensing and engineering expertise, we will be addressing the global challenge of waste tyres and creating new pathways for sustainable product development.”
Vibhu Sharma, Chief Executive Officer, InnoVent Renewables, said, “Partnering with Lummus has the potential to accelerate the global deployment of our technology and help us address the environmental and public health challenges of one billion end-of-life tyres that are disposed of annually. Together, we can transform waste into valuable resources, reduce carbon emissions and support the transition to a more sustainable future.”
Continental Steps Up Shift To Renewable, Recycled Materials In Tyres
- By TT News
- June 10, 2025
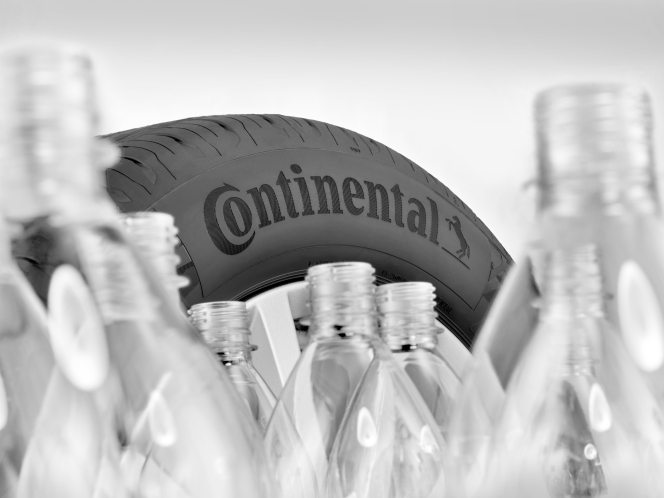
Continental is accelerating its efforts to make tyre production more sustainable, with the German tyre manufacturer expecting the share of renewable and recycled materials in its tyres to rise by up to three percentage points in 2025.
The average share stood at 26 percent in 2024, and Continental said it anticipates a further increase this year due to the expanded use of materials such as synthetic rubber derived from renewable sources, recycled PET polyester, recycled steel, and silica made from rice husk ash — a by-product of rice production.
“We are systematically increasing the share of renewable and recycled materials in our raw material portfolio. In five years, we aim to surpass the 40 percent mark,” said Jorge Almeida, Head of Sustainability at Continental Tires. “To achieve sustainable mobility, we are constantly searching for even more environmentally friendly materials. After extensive testing, we integrate them into production as quickly as possible.”
The company has set a goal of using over 40 percent renewable or recycled materials in its tyres by 2030, without compromising on performance or safety.
A key pillar of this transformation is the adoption of mass balance-certified materials. This approach, certified under ISCC Plus, enables Continental to mix certified and non-certified materials during production while maintaining strict accounting procedures to ensure traceability.
The company has already secured ISCC sustainability certification for its tyre plants in Lousado (Portugal), Hefei (China), Púchov (Slovakia) and Korbach (Germany). Continental is also scaling up its use of recycled steel, silica from rice husk ash, and PET yarns made from recycled plastic bottles via its proprietary ContiRe.Tex process.
Other sustainable innovations include COKOON, an adhesive coating system co-developed with Kordsa that replaces formaldehyde and resorcinol in bonding textile components with rubber. Continental also continues to explore alternative additives derived from renewable sources to improve the tyre vulcanisation process.
“We have developed a comprehensive portfolio of diverse, more sustainable materials and are continuously integrating them into all our products after extensive testing,” Almeida said. “In doing so, we ensure that there is no compromise in safety or performance. With this portfolio, we are getting closer and closer to our ambitious, long-term sustainability goals.”
Zeon Opens Biotech Research Hub In Yamagata To Drive Sustainable Rubber Raw Materials
- By TT News
- June 10, 2025
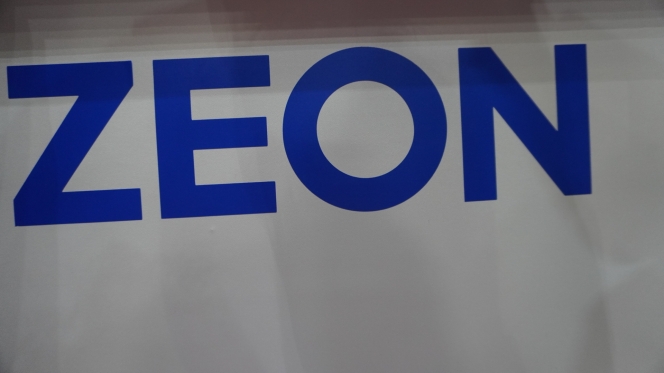
Japan’s Zeon Corp has established a new research facility at its Zeon Chemicals Yonezawa site to develop plant-based production processes for synthetic rubber raw materials as it accelerates efforts to decarbonise its operations and support a circular economy.
The new lab will focus on advancing biofermentation and chemical reaction technologies to produce butadiene and isoprene—key building blocks for synthetic rubber—directly from plant-derived feedstocks.
“This facility will accelerate the development of biotechnology to produce butadiene and isoprene directly... to contribute to the realisation of a circular economy,” the Tokyo-based company said.
The initiative is part of Zeon’s “STAGE30” medium-term business plan, which includes a target to cut group-wide carbon dioxide emissions by 42 percent by fiscal 2030 from 2020 levels. The company has made “Promoting a transformation of monozukuri to realise carbon neutrality and a circular economy” its top strategic priority under the plan.
The research centre, completed on 23 May, spans 590.34 square metres and features laboratories with local exhaust ventilation alongside office and meeting spaces. Yamagata Prefecture partially funded it under its Business Location Promotion Subsidy Programme.
The project is also supported by Japan’s Green Innovation Fund, run by the New Energy and Industrial Technology Development Organization (NEDO), which backs long-term industrial decarbonisation initiatives. Zeon is collaborating with Yokohama Rubber Co and several academic institutions on two key development themes, including the use of plant-based and sustainable materials for producing rubber intermediates.
Zeon said it aims to commercialise the technology for producing butadiene and isoprene from plant sources by 2034.
- Rubber Research Institute of India
- CRISP Mobile App
- Digital University of Kerala
- Good Agricultural Practices
- Rubber Board of India
Rubber Research Institute Of India Launches 'CRISP' Mobile App To Empower Rubber Farmers
- By TT News
- June 08, 2025
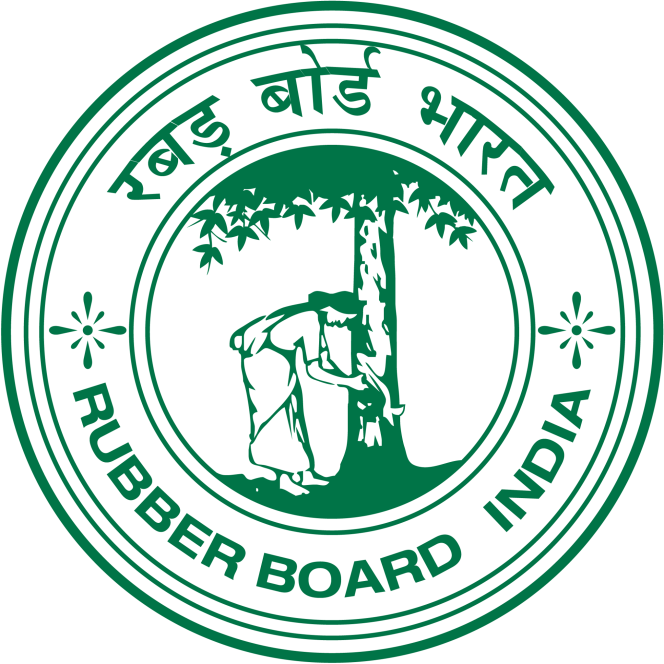
In a landmark initiative to modernise rubber farming, the Rubber Research Institute of India (RRII), in partnership with Digital University of Kerala, has unveiled the Comprehensive Rubber Information System Platform (CRISP) mobile application. This innovative digital solution integrates advanced technologies with agricultural expertise to provide rubber growers with comprehensive, location-specific information at their fingertips.
The CRISP app offers a wealth of valuable features designed to enhance every aspect of rubber cultivation. Farmers can access detailed guidance on optimal farming practices including clone selection tailored to specific locations, scientific fertiliser recommendations and effective methods for controlling diseases and pests. The app also provides crucial knowledge about rubber tapping techniques and processing methods to maximise yield and quality.
Leveraging cutting-edge WebGIS technology, the platform delivers critical geospatial insights by identifying areas vulnerable to landslides and floods. This feature advises farmers on suitable agricultural practices while warning against risky operations in these sensitive zones, enabling better risk management and crop protection.
Beyond cultivation support, CRISP serves as a complete resource hub, offering information about Rubber Producers' Societies, Group Processing Centres, Rubber Board offices and nurseries across the country. Recognising the importance of market intelligence, the app now includes real-time updates on domestic and international prices for various rubber products such as sheet rubber, latex, cup lump and block rubber, benefiting both farmers and traders in making informed decisions.
By seamlessly combining Good Agricultural Practices with Information and Communication Technology, CRISP represents a significant leap forward in digital agriculture. The app bridges the gap between scientific research and practical farming, empowering India's rubber growers with knowledge to improve productivity, ensure sustainable practices and enhance profitability.
Comments (0)
ADD COMMENT