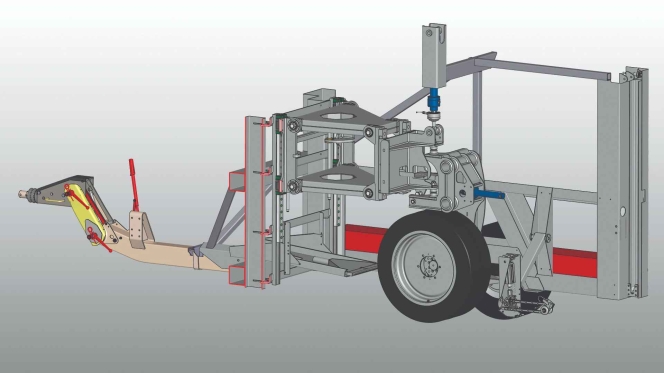
By Ralf Berres and Dr Dieter Barz
The Industry Grip Testing System (IGTS) is a brand new measurement trailer, developed as a joint project between tyre maker Michelin and solution provider Altracon. It comprehends the knowledge of both tyre and measurement equipment experts and represents the technical feasibility in terms of tyre characteristics measurement on the road with state of the art ease of use.
The Altracon Industrial Grip Trailer System IGTS consists of a modular concept design. One development target was to keep the system variable for existing as well as for future test- and measurement tasks and to adapt to any kind of on the road testing requirement.
The IGTS grip testing trailer is built for straight dry and wet-braking tests. The trailer’s frame and wheel load station are optimised by FEM technology for highest stiffness and lowest deformation.
Design features
The trailer is made of a stiff frame with independent wheel suspension for the left and right wheels and is equipped with a variable towing bar to level different heights of the vehicles hitches. It may be pulled from any drawing vehicle with sufficient trailing load and engine torque for the measurements, no matter if it is a Pick-up, SUV, or truck. The IGTS hosts an independent test wheel load station. It is placed in the center of the trailer between the carrying wheels and presses the test wheel to the road surface on a path between the trailer wheels. The test-wheel load station is equipped with a high-performance disk brake to apply the braking torque/ force to the test wheel for grip testing. All functions are independent from the drawing vehicle while it carries all the necessary supplies on board except of the water tank, which is carried by the drawing vehicle.
The concept design is prepared to be extended with dynamic test capability with camber and slip variation, which will be included in the IGTS “Force and Moment” trailer. The test wheel load station and its media supply and control system may also be built into other vehicles such as busses or trucks, which must be prepared accordingly as a matter of course.
The trailer is equipped with a modular undercarriage set-up. The basic trailer requires only one axle to perform grip measurements, which are done straight rolling/ braking. The directional stability of the trailer is enhanced by two additional lift axles, one in front and one behind the carrying axle of the trailer, to run dynamic tests with the IGTS on the road when it is equipped with camber and slip variation functionality. These lift axles are only used during the actual measurement and will be lifted for taxiing and transportation. Both axles use smaller wheels than the carrying axle and also have independent wheel suspension. The wheels of the lift axles are moreover actively steered to balance side forces which may be generated during testing. The drive performance control system adjusts the trailers’ Eigen modes in vertical and lateral direction and significantly improves the directional stability.
The IGTS test wheel load station is light-weight to reduce the effect of mass of inertia. It is equipped with an active wheel load control while previous test trailers just use dead weights. A fully automatic and adjustable damping control at the testing axle adjusts the Eigen mode and cares for smooth running and best precondition for the measurement on any road. The high-performance long-life wheel spindle is specially designed for lowest rolling resistance.
Power supply is done by batteries, which are loaded by generators. These are inbuilt to the carrying axle at each side. The power supply engineering may be designed as 48V DC as well as 240/400 1- or 3-phase AC with converter for special applications.
Compressed air is supplied from an inbuilt compressor with air tank for inflation pressure adjustment or control as well as for connection of air driven tools.
Hydraulic supply from an inbuilt hydraulic pump system with accumulator tank enables dynamic load, brake, and steering function. The high-speed characteristics of the hydraulic supply is suitable to simulate braking performance (ABS) and quick release brake pressure at the test wheel. It allows to run up to 8 repeatable tests per 100 m in a sequence in combination with the high-performance brake-control techniques.
The optional water management system is integrated and allows controlled watering of the test-wheels path. The nozzles are placed in front of the test wheel. Their watering width is adjustable to 420mm and their watering height is controlled by flow-measurement, which is adjustable between 0 and 4mm at maximum speed of 100 km/h. The system is operating with continuous water flow for quickest reaction times. It is pressure-controlled and switches between circulating and spraying mode without any time lag and pressure loss.
Measurements
The trailer speed measurement is precisely done directly at both carrying wheels. Different speeds measured at the left and right side indicate deviation from the straight path. The alignment of the drawing vehicle and the trailer is moreover precisely measured with a laser-based alignment measurement system if the IGTS is equipped with camber and slip variation functionality. Inputs from both, the speed and the alignment measurement system, will generate correction of the directional stability by the control system.
The wheel speed of the test-wheel is precisely measured directly at the test-wheel spindle with an encoder, which also gives information about the braking process of the test wheel.
Forces and moments at the test wheel are synchronously measured in x- and z-direction with 1-component sensors. A multi-component force and moment dynamometer, which may use strain gauge or quartz technology, is optionally available as an alternative. It is integrated to the wheel spindle, fully covered and shielded. However, both set-ups are available either independent or together.
All measurements of motion are done with precision sensors, using various technologies, depending on the entire parameter. For referencing, speed and location recording different control and measurements techniques are used as well.
Ergonomics
The test-wheel carrier design enables to turn the wheel by 90° around its vertical axle for wheel exchange and service. This allows the operator to access the wheel fixation from the back of the trailer.
SUMMARY OF DISTINCTIVE FEATURES
- Light-weight wheel suspension to reduce the mass of inertia
- Low rolling resistance high-performance long-life wheel spindle
- Measurement systems as single axle or with dynamometer technics
- High precise load control designed for equalised axle weight
- Eigen-mode adjustment by fully automatic and adjustable damping control at the testing axle
- Brake system with high speed characteristics hydraulic supply to simulate braking performance (ABS) and quick release brake pressure
- High performance braking control system
- Test sequences with up to 8 tests per 100 m in a row.
- Modular trailer undercarriage for one or three axle systems for characteristics testing including drive performance measurement and control technics to adjust the trailers’ Eigen-mode in vertical and lateral direction
- Integration in existing testing environment and customised data solution
- Different control and measurement technics for referencing, speed and position recording
- Optional water-levelling system to apply an adjustable water film in front of the test-wheel in case of a missing road watering system
Operation Optimisation Is At Risk Sans Data
- By Sharad Matade
- July 03, 2025
The tyre industry faces a significant challenge in data availability with fragmented supply chains, a lack of standardisation and minimal digital infrastructure limiting operational efficiency. Despite the growing importance of predictive maintenance, many manufacturers still rely on manual processes, while competitive concerns and regulatory restrictions further restrict data sharing. This absence of real-time insights hampers decision-making, making operations reactive rather than proactive. However, digitalisation and advanced data analytics are gradually reshaping the landscape. Solutions like HF Xplore aim to bridge this gap, offering real-time monitoring and predictive capabilities that can drive efficiency, sustainability and cost reduction.
Data availability is a challenge in the tyre industry due to fragmented supply chains, lack of standardisation and limited digital infrastructure. Manufacturers, distributors and recyclers operate in silos, making data consolidation difficult. Many businesses still rely on manual processes, while competitive concerns and regulatory restrictions further limit data sharing. Tracking end-of-life tyres (ELTs) is particularly challenging, impacting recycling efficiency.
However, data availability is crucial for optimising operations, sustainability and innovation. Real-time data enables predictive maintenance, helping fleet operators reduce downtime and improve safety.
Accurate tracking of tyre usage and recycling supports circular economy initiatives and regulatory compliance. It also enhances research and development initiatives for advanced tyre materials such as electric vehicles and off-the-road (OTR) tyres, ensuring better performance and durability.
Improved data transparency can drive smarter decision-making, cost efficiency and sustainability in the industry. Digitalisation and data standardisation are key to overcoming these challenges.
However, HF Group’s Global Head of Digital Solutions, Jeremias Neuhaus, told Tyre Trends, “One of the biggest challenges in adopting data-driven solutions in the tyre industry is the availability of data and convincing customers not just of the solution itself but of the value of data transfer and real-time monitoring. Many decisions in the industry are still based on gut feeling rather than data-backed insights. Our focus is to bridge this gap by providing transparency into machine performance, enabling customers to make data-driven decisions instead of relying on intuition. By implementing real-time monitoring, we can significantly reduce downtime and help customers optimise processes. Even in the first step of implementation, simply visualising machine health and performance brings immediate value. Customers receive notifications for potential issues, allowing them to take preventive action before costly breakdowns occur.”
“The biggest opportunity in this space lies in the fact that data-driven insights can drastically improve operational efficiency. Once machines are connected and data is flowing, customers gain a much deeper understanding of the equipment, leading to better decision-making and optimised production cycles. Predictive maintenance and AI-driven analytics will further enhance operations by identifying potential failures before they occur. This is particularly crucial as manufacturers aim to reduce carbon emissions and energy consumption while increasing efficiency. Our approach stepwise towards AI-powered predictive solutions bring even greater efficiency and cost savings,” he added.
A critical concern in the tyre industry is data security and confidentiality, given how secretive manufacturers are about the respective production processes. “We address these concerns by focusing strictly on machine data rather than the proprietary tyre-making process. Our solutions do not need the actual process details to provide valuable insights. Additionally, the real, detailed data remains visible only to the customer, ensuring that they retain full control. In cases where AI-driven analytics are implemented, we collaborate closely with customers to develop models tailored to specific needs without compromising sensitive production data,” revealed Neuhaus.
The company launched the HF Xplore few years ago as a condition monitoring solution purely for curing presses. One of the significant developments following the merger of HF Mixing Group and HF Tire Tech Group has been the integration of previous initiatives into a joint project, creating a common condition monitoring solution. As a result, HF Xplore is now available for both curing presses and mixer lines. This expansion allows the company to offer real-time monitoring and predictive insights across two of the most critical processes in tyre manufacturing curing and mixing.
MONITORING TYRE FORMULATIONS
Curing and mixing are fundamentally different processes in tyre making, which presents a challenge in making HF Xplore compatible with both. The solution is to split monitoring into two layers viz-a-viz a common monitoring framework and machine-specific components.
The common framework includes monitoring cycle times, alarms, key performance indicators (KPIs) and production progress – elements that apply to both curing presses and mixer lines. However, each machine type has unique components that require dedicated monitoring.
For curing presses, especially electric-curing, HF Xplore focuses on monitoring hydraulic power unit and the electric curing, which is a crucial aspect of efficiency and quality control. On the other hand, for mixers, the system focuses on critical mechanical components such as the RAM movement, feeding mechanisms and drop doors, which are key areas that directly impact mixing performance and consistency. The drop doors, for instance, play a crucial role in ensuring a smooth transition of rubber to the downstream process, making their monitoring essential for operational reliability.
The user interface of HF Xplore is designed to maintain familiarity across different machines. The dashboard layout remains consistent, so users who are accustomed to using it for curing presses will find a similar experience when working with mixer lines. This consistency reduces the learning curve and makes the system more intuitive for users handling both curing and mixing equipment.
Behind the scenes, the company is investing heavily in data modelling to refine and improve predictive capabilities. The company is developing individualised, flexible data models tailored to each machine type.
These models analyse operational patterns, detect anomalies and provide real-time insights to minimise downtime. By combining machine-specific expertise with data-driven intelligence, HF Xplore continues to evolve into a powerful predictive maintenance and performance optimisation tool for the tyre manufacturing industry.
INTO DATA MODELS
HF Xplore captures machine data but doesn’t analyse it directly. Instead, the system applies background logic to determine whether values are within acceptable limits. Currently, its primary function is real-time status monitoring, giving users an overview of machine condition. However, future iterations will introduce predictive maintenance capabilities, allowing companies to anticipate and address potential failures before they happen.
“At this stage, HF Xplore detects and predicts issues but does not provide specific solutions. As the technology evolves, it will go beyond identifying potential failures to offering actionable recommendations. This shift will help businesses move from reactive maintenance to a more proactive approach, reducing downtime and improving operational efficiency. To refine predictive maintenance, the system is being trained with large datasets in collaboration with customers. Over time, this will enhance the system’s accuracy, enabling it to not only flag potential issues but also suggest corrective actions,” informed Neuhaus.
AI and machine learning will play a central role in the company’s future roadmap, following a structured three-step approach – visualise, analyse and predict.
The first step will provide real-time machine status and process transparency. In the analyse phase, the company’s solutions will move beyond monitoring to offer deeper insights. The system will evaluate performance trends, identify operational limits and provide status feedback. The final phase will be where AI and machine learning take centre stage by analysing vast amounts of historical and real-time data. AI models will identify patterns, forecast failures and recommend preventive actions.
Commenting on whether implementing HF Xplore for a curing press or a mixing system presents different challenges, he said, “While both require detailed monitoring, mixing systems are more complex due to the interconnected components including upstream and downstream processes. Unlike curing presses, which operate as standalone units, mixing lines require data collection across multiple machines for effective monitoring. However, HF Xplore benefits from deep integration with its own equipment, leveraging PLC data to ensure seamless functionality across different systems.”
But for this to be a reality, different data models are pivotal. “The data model is essential for structuring and standardising the information displayed on the dashboard,” informed Neuhaus.
RETROFITTING HF XPLORE
HF Xplore is compatible with both greenfield and brownfield machines, though older models with outdated PLCs may have limitations. “While we cannot retrofit machines that are using old automation solutions, HF Xplore can be integrated into machines from the past few years, especially for condition monitoring. With electric-curing, it also enables precise tracking of electric curing performance, enabling deeper insights,” informed Neuhaus.
“One key challenge is data governance and security. Traditionally, machine data remained within the plant, but HF Xplore connects operational technology with information technology, raising concerns about data ownership and security. To address this, we have implemented user-based access controls, IP-based security and data encryption,” informed the executive.
For tyre plants with a mix of HF and non-HF machines, HF Xplore offers a custom dashboard creator with low-code functionality, allowing users to integrate and visualise data from different machines in just a few hours. A flexible data model further ensures standardised visualisation, even when machine types vary. While full integration with non-HF machines may require additional work, HF Xplore provides a comprehensive plant-wide monitoring solution for optimising performance.
“HF Xplore can potentially integrate with machines from other companies, but it depends on data accessibility and PLC compatibility”, contended Neuhaus, who highlighted the flexibility and modularity of their solution.
Powering Retrospection In Tyres Through Tags
- By Sharad Matade & Gaurav Nandi
- July 01, 2025
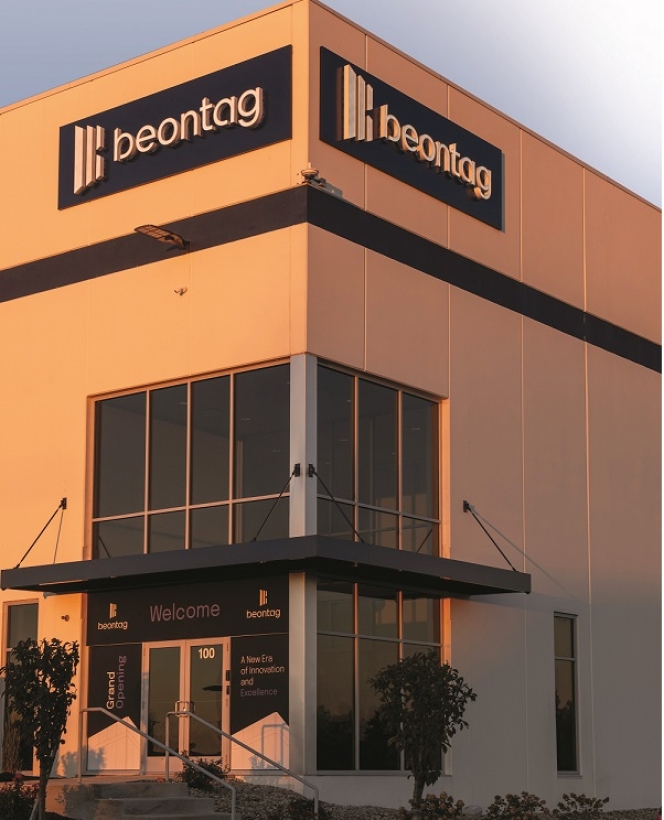
The integration of Radio Frequency Identification (RFID) technology into the tyre industry is gaining momentum, offering solutions for traceability, sustainability and lifecycle management. Beontag, in collaboration with Michelin, is spearheading this innovation by jointly designing specialised RFID tags that can withstand the harsh conditions tyres face, such as extreme heat and pressure. The tags store crucial data, enabling efficient recycling, retreading and warranty management. As the tyre industry evolves, RFID adoption is seen as essential for ensuring authenticity, improving asset management and supporting regulatory frameworks. However, challenges remain in scaling production and increasing industry awareness.
Punch card systems, barcodes, dog tags, biometric scanners etc. are all instruments that offer basic information about humans and commodities for identification, authentication, traceability and retrospection.
The tyre industry is similarly standing at a crossroad where the demand for traceability and retrospection is growing. Tyre manufacturers, retailers, retreaders and recyclers are showing a growing exuberance for digital footprints that can record, summarise and authenticate information related to each existing and new tyres throughout the commodities lifecycle.
And the simple solution catering to such demands is a radio frequency identification (RFID) tags. While the use of RFID tags is new within the global tyre market, these have found a stronghold across retail, logistics, manufacturing, healthcare etc.
The tag is changing the game of traceability within tyre markets as the adoption grows. Technological companies are collaborating with tyre manufacturers to develop tailor-made RFIDs.
International RFID and IoT expert Beontag is one such company that has developed RFID tags for the tyre industry. Divulging deep into the engineering mechanics of the tag, APAC Senior Sales Manager Evelyn Ong told Tyre Trends, “RFID technology used in tyres is significantly different from conventional RFID applications due to the harsh conditions tyres endure, such as high temperature, pressure and wear and tear. Unlike RFID tags used in retail or medical settings, tyre RFID tags must be engineered to survive extreme conditions. As a result, traditional RFID designs, which use PET labels and conductive paste for chip attachment, are unsuitable. Instead, tyre RFID tags rely on a mechanically robust and inductively coupled antenna structure.”
“Designing RFID for tyres required a completely new approach, and the current version (generation four) is believed to be durable enough to last the entire lifecycle of a tyre. This innovation aligns with initiatives like the European Digital Product Passport (DPP), which mandates that products must be identifiable throughout their life cycle. Although RFID chips themselves only store a unique identifier (similar to a FASTag or car license plate), all detailed data such as manufacturing date, plant origin, distribution history, usage, retreading details and material composition is stored in backend software systems. As the tyre moves through the supply chain, each stakeholder adds relevant data to the software based on the RFID, creating a comprehensive database that supports traceability and lifecycle management including recycling or retreading,” she added.
The company’s main RFID tag for the tyre industry includes a chip with memory, enabling it to store data and serve as a digital identifier for the physical tyre using radio waves. This transforms a traditional tyre into a digitally traceable product.
Beontag jointly designed this RFID tag with Michelin, exploring the benefits of embedding a chip in tyres for purposes like asset management and product authentication and was instrumental in driving standardisation across the industry. While Michelin is the first tyre manufacturer to roll out the new ‘smart tyres’ with Beontag technology, the manufacturer recently announced a partnership with Kumho Tire and aims to go into partnership with other brands in the near future.
DEMAND AND SUPPLY
The company recently participated in a global tyre exhibition and rationalised its participation with significant long-term potential of the tyre RFID market. “With over 30 billion tyres in circulation globally, the scale of the opportunity is enormous. Having worked in RFID for over 20 years, the technology excels in applications involving products that are physically similar and difficult to differentiate visually like tyres. This makes tyres an ideal use case for RFID,” said the official.
Ong explained that beyond the European Digital Product Passport regulation, a key driver for embedding RFID in tyres is the fundamental need for every product to have a unique identity, whether through a barcode, QR code or digital tag. In the tyre industry, this need has been especially pressing due to the limitations of traditional identification methods like hot stamping, which often wear off over time and result in a loss of traceability.
She noted that the absence of a durable, readable ID creates challenges in verifying authenticity, determining warranty status and tracing the tyre’s origin. For instance, without a reliable identifier, it becomes difficult to confirm whether a tyre is genuinely from Michelin or to retrieve key manufacturing details such as plant location, batch number or intended distribution path.
By embedding RFID tags with unique digital identities, the industry gains the ability to link every part of the tyre’s lifecycle across the value chain. This ensures consistent traceability, facilitates better inventory and warranty management and combats counterfeiting.
“We are actively engaging with the top 10 global tyre manufacturers in the transition towards RFID-enabled tyres. While the European market is leading adoption driven largely by regulatory frameworks, we are also working with tyres manufacturers across the Asia-Pacific region and beyond.
“Although OEMs like Michelin are beginning to integrate RFID tags, starting with high-end passenger tyres, there is a growing and immediate demand from the aftermarket. This secondary market includes fleet operators, leasing companies and pay-per-use models, where the need for tyre tracking is urgent. These businesses want to monitor retreading cycles, ensure asset recovery and verify ownership, especially to prevent tyre theft or unauthorised replacements,” she added.
According to Ong, some aftermarket players are even looking to embed RFID tags independently rather than waiting for OEMs to standardise the process, underscoring strong demand outside the traditional supply chain.
When asked about growth potential between the passenger and commercial segments, she indicated that although current OEM efforts are focused on high-end passenger tyres, interest from the commercial and aftermarket sectors is strong and could drive faster adoption due to practical and financial incentives.
Furthermore, RFID tags play a key role in sustainability by enabling traceability throughout a tyre’s lifecycle. It allows manufacturers to capture crucial data at the point of manufacture, which is essential for tracking and recycling. With RFID, recycling processes become more efficient because tyres can be easily sorted based on type, size and materials. This minimises waste, reduces sorting time and improves the overall effectiveness of recycling efforts.
HURDLES IN ADOPTION
The executive noted that there are unique challenges of designing an RFID tag for tyres given the nature of its operations. To address these hurdles, the company and Michelin jointly designed and extensively validated a specialised RFID tag consisting of a chip and an antenna, which is fully embedded within the tyre.
This tag is designed to be invisible from the outside and integrated into the tyre structure in a way that ensures durability without compromising performance. The antenna’s spring-like structure allows it to expand and contract along with the tyre’s movement without affecting its function.
Crucially, the connection between the chip module and spring antenna is linkless, using inductive coupling instead of mechanical connection. This inductive mechanism ensures reliability even under extreme conditions like high temperature, pressure and physical deformation.
Although the tag is not constantly read during vehicle operation, it must remain functional and readable during inspections or servicing.
Alluding to broader industry challenges towards adoption, Ong said, “Current challenges centre primarily around a lack of awareness and industrialisation of the production process in existing tyre production lines and factories. Unlike retail, where RFID is well-established, the tyre sector is still in the early stages of adoption. Because of this, there is a need to educate the market, build trust and demonstrate real-world use cases. Potential customers are hesitant to act as first movers and prefer to see proven implementations to reduce perceived risk. A hopeful future challenge would be demand outpacing production capacity. However, a more realistic and significant long-term challenge lies in technological evolution, particularly around IC size, performance development and adding more functionality through sensor information.”
INTEGRATING RFIDS
The RFID chip used in tyres stores a minimum of 96 bits of data, which aligns with the standard size modelled after barcodes. This size is sufficient to encode essential identifying information including a serialised number.
While barcodes only identify products at the SKU level, RFID allows each item to have a unique identifier, making it far more powerful for inventory management. At every stage in the tyre’s lifecycle, it is the responsibility of the user or stakeholder to read the RFID tag and input relevant data into the software system, linking it to the tag’s unique identifier.
One of the most compelling applications of tyre RFID is during the tyre’s second life – especially in retreading. In this stage, the retreader can embed a new RFID tag and effectively reset the tyre’s lifecycle. This allows the retreading company to claim and track the work they’ve done including how many times the tyre has been retreaded and when.
Fleet operators or regulators can use this data to verify authenticity, ensure compliance and manage safety.
At the end of the tyre’s life, especially during the recycling stage, RFID continues to offer value by recording the tyre’s complete journey. Recyclers can access a tyre’s full history by ensuring proper handling and reporting.
The key challenge in placing the RFID tag is ensuring its proper location and integration into the tyre’s structure. This process must be carefully controlled as the tag must not only be positioned in the optimal spot but also withstand the stresses and heat of the curing process. If the tag was placed improperly, it could potentially cause issues with its performance, especially in terms of readability after the tyre is fully cured and ready for use.
COMPETITION AND EVOLUTION
Besides Beontag, there are other companies operating within the tyre RFID space. Alluding to the distinction between them, Ong explained, “The main difference of our product lies in the patented POD design (POD = IC module/package). Our product utilises a special alloy for the antenna, which prevents deformation and ensures consistent diameter and gap size. Additionally, the chip packaging has been specifically designed to offer better protection, reducing the risk of damage and ensuring reliable readings.”
She explained that the company’s business case for RFID technology in the tyre industry is clear and it believes strongly in its potential. She emphasised the importance of spreading awareness about the technology, as Europe will be implementing the technology first, but other regions including APAC and the Americas will be catching up as the technology is proven in the coming years.
NIRA Dynamics Partners BANF Smart Tire System For Advanced Vehicle Safety And Predictive Maintenance
- By TT News
- June 16, 2025
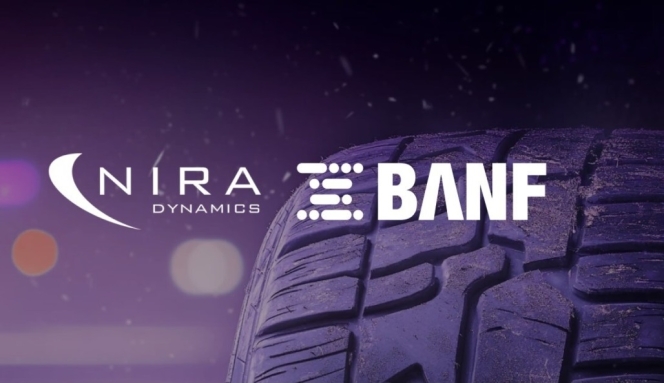
Swedish automotive software leader NIRA Dynamics AB and BANF Smart Tire System of South Korea have announced a new partnership aimed at significantly enhancing vehicle safety and predictive maintenance for commercial vehicles. The collaboration will see BANF integrate its high-frequency tyre sensors into NIRA's established software ecosystem.
This strategic alliance aims to disrupt Tyre Pressure Monitoring Systems (TPMS), providing commercial fleets and automakers with unprecedented real-time insights into tyre health and road safety. NIRA Dynamics, founded in 2001, is a global automotive software powerhouse with its technologies deployed in over 120 million vehicles worldwide, including an indirect TPMS (iTPMS) that has surpassed 110 million units sold.
Under the agreement, NIRA will incorporate BANF's triaxial tyre sensors into its Road Surface Information (RSI) and Wheel Safety Insights (WSI) platforms. These platforms already utilise existing vehicle sensor data and proprietary algorithms for functions like tyre grip estimation, tread wear analysis and loose wheel detection.
BANF's key innovation lies in its Smart Profiler system, which wirelessly powers internal tyre sensors directly from the vehicle battery, overcoming the challenge of continuous power and real-time data transmission from rotating tyres. This integration will significantly enhance NIRA's capabilities, particularly for monitoring commercial vehicle loads and dual-tyre setups, by providing sensor data at high sampling rates of 1kHz and 4kHz.
Otto Johansson, Head of Innovation at NIRA Dynamics, said, "This collaboration accelerates our vision of creating a comprehensive vehicle intelligence network. While our software solutions already process data from millions of vehicles, adding specialised hardware enables new use cases in predictive maintenance and ADAS applications."
NIRA's evolution from software-only tyre pressure monitoring to multi-layered safety systems is evident in its flagship Tyre Pressure Indicator (TPI) technology, which has eliminated the need for physical sensors in many applications, significantly reducing electronic waste. The company has also collaborated with automotive giants like Volkswagen Group on innovations such as Road Surface Alerts.
The partnership also addresses critical safety needs in commercial vehicles. NIRA's Loose Wheel Indicator (LWI), already deployed in Audi vehicles, will now be extended to heavy-duty vehicles through the BANF collaboration, aiming to mitigate the thousands of annual wheel detachment incidents reported.
For fleet operators, the integrated system promises substantial operational benefits. NIRA's Winter Road Insights product, which helps optimise road maintenance, combined with BANF's wear prediction algorithms, is expected to lead to reduced tyre replacement costs and improved fuel efficiency.
Ron Yoogun Lee, Head of Business Development, BANF, said, “Our goal is to enhance cost-effectiveness, save lives and preserve the environment by digitising tyres, which are the last analog domain in the mobility industry.”
Looking ahead, NIRA's technology roadmap includes developing ‘grip maps’ for SAE Level 2-3 autonomous vehicles and leveraging data from millions of vehicles to create AI models for predictive infrastructure maintenance, further solidifying its position at the forefront of automotive innovation.
Anyline Launches TireBuddy App to Streamline Tyre Inspections
- By TT News
- June 13, 2025
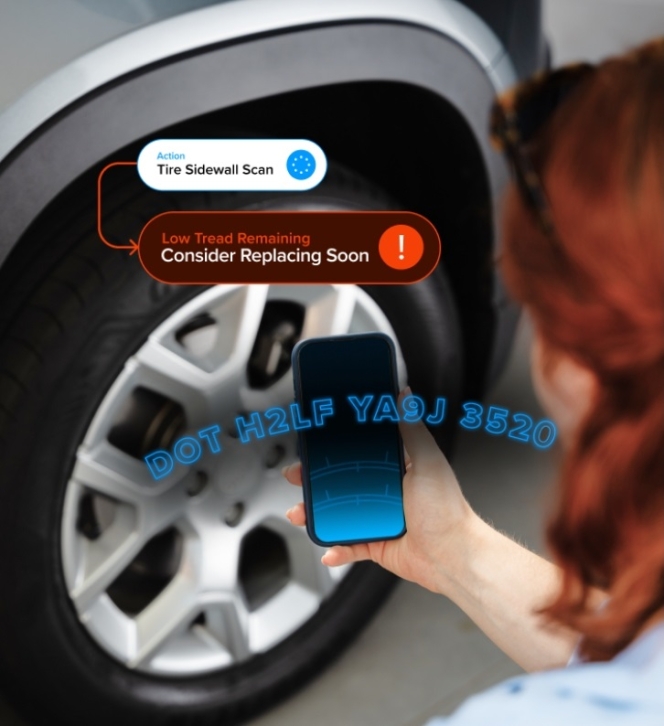
AI-powered mobile data capture company Anyline has launched TireBuddy, a smartphone-based app designed to modernise tyre inspections in automotive service bays. The app replaces traditional, manual inspection methods with a standardised digital workflow that delivers consistent, data-backed results and clear customer reports.
TireBuddy offers technicians tools to detect tread depth issues, tyre age, alignment concerns and sidewall damage using AI-powered analysis and visual reporting – without the need for additional hardware. Reports can be instantly shared in digital or printed formats, helping to reduce manual entry errors and increase customer trust.
The launch comes ahead of National Tire Safety Week (30 June 30 – 4 July), positioning the app as a timely solution for shops preparing for the summer travel season.
Lukas Kinigadner, Co-Chief Executive Officer, Anyline, said, “TireBuddy is not only about faster inspections — it’s about more trustworthy ones. We’re helping garages and service centres replace subjective tyre checks with data-backed insights and visual reporting that both technicians and customers can rely on.”
Frederic Baroin, Global Head of Automotive Business at Anyline, said, “TireBuddy empowers technicians with real-time, reliable data that strengthens recommendations and builds customer confidence. We designed it to deliver clarity, not complexity, in every inspection.”
By enhancing inspection accuracy and transparency, Anyline said TireBuddy can also drive higher service approvals and boost shop revenue.
Comments (0)
ADD COMMENT