THE TIRE COLOGNE 2020: FORWARD LOOKING CONCEPT, ORIENTATION
- By 0
- April 26, 2020
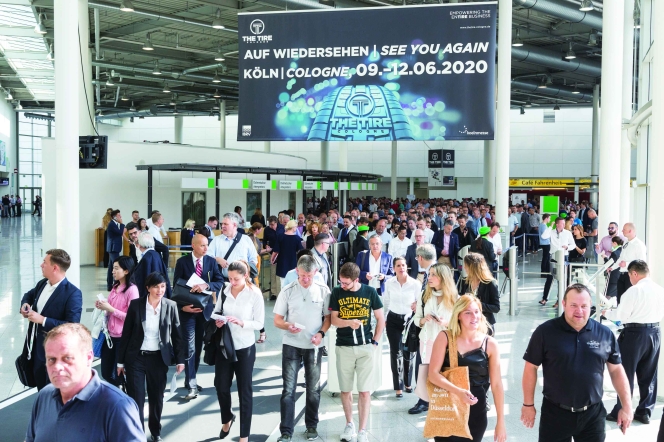
By Gerald Böse, President and CEO, Koelnmesse
The successful premiere of THE TIRE COLOGNE is a confirmation of our long and intensive preparations. After all, from the first announcement in 2014 until the trade fair in 2018, we worked for four years in cooperation with the industry on the concept, services on supporting events, initiated world-wide information and marketing campaigns and incorporated partners for many themes. We have convinced exhibitors and visitors to THE TIRE COLOGNE with our event concept and a new orientation, with the high quality of visitors, a generously dimensioned hall offering and a strong concept in terms of content, and received a unanimous vote from the international tyre and wheel industry: Cologne is the leading international meeting point of the industry right from the start!
However, this doesn't mean we can rest on our laurels. Our thinking and action are oriented to continuing further development: we see ourselves as part of the international tyre and wheel industry, and also want to provide impulses in terms of content that are of use to the industry for future development. Every industry requires perspectives on how the future orientation and potential for further growth can be developed and realised. In our concept we have defined clear strategic and conceptual goals that point out and realise these perspectives.
1. the independent and comprehensive reflection of the industry at all levels, at a glance and at the right time.
2. the internationalisation of all relevant industry segments.
3. the generation of new visitor target groups. In addition to the themes of online commerce and workshop services, we have in this way addressed important target groups like fleet managers and transport companies and attracted them to Cologne. We have also clearly emphasised the theme of recycling, which has to date only been treated inadequately – additional added value for industry and commerce. This has all worked very well, but there is still much more potential for further expansion. Accordingly, we analysed all areas and thematic focuses and verified development potential here and there. For example, we want to expand the Recycling/Retreading, Workshop and Services sections, but also the over arching theme of digitalisation. To this purpose, we are already involved in an intensive exchange with potential exhibitors, organisations and partners.
We have thus already achieved the most important goal of comprehensively reflecting the entire industry. I especially emphasise this because we are now in a two-year cycle. However, the premiere in 2018 had a run up period of nearly four years, extending from the announcement that the industry was switching to Cologne to the first event. Almost five months prior to the opening of the fair, more than 90 per cent of the planned exhibition areas have already been rented -in comparison to the final result of 2018, even almost 95 per cent in comparison with the original planning for 2018. More than 400 companies have already confirmed their participation in THE TIRE COLOGNE 2020, including nearly all well-known key accounts from the focus segments. THE TIRE COLOGNE is thus the world's only B2B platform to present the top brands of the international tyre world. We will be making smaller adjustments, for example, in the hall planning, in order to optimise further here. In concrete terms, this means that the big key players will not exclusively be placed in Halls 6 and 7, but some now also in Hall 8. This ensures even more optimal distribution of visitors to all halls of THE TIRE COLOGNE, and at the same time reinforces the segments of car services and workshop outfitting. Hall 9, with the focus on the themes of tyre remoulding and recycling, will also be made more attractive for exhibitors and visitors, in that the "Global Retreading Conference" and the Recycling Forum will also take place here. In addition, the "Future Mobility" special area will also be realised in Hall 9 for the first time.
With the "Future Mobility" special area, THE TIRE COLOGNE wants to take a look into the future and point to questions that affect the industry: how will mobility change in the future? What impact will changes have on people and society? What does changed mobility mean for the product tyres? And what effect will this have on the tyre industry? Answers to these questions will be provided by, among others, Dr Sascha Peters, one of the most renowned material and technology experts in Europe, who will discuss the theory and practice revolving around the product of tyres and possible changes in the future in the context of the special event. As a highlight and at the same time as a stimulus for active participation, a driving course is being planned for the "Future Mobility" special event, where autonomous or electrically powered vehicles will be in use.
The event programme is oriented to questions that currently affect the industry – whether this involves innovative further developments or a theme that affects every one against the background of climate change: sustainability. With the "Recycling Forum," we offer a complete overview of the decisive aspects in the field of tyre recycling and sustainability. And sustainability of course also plays an important role for the Global Retreading Conference. The conference is a one-time opportunity to take a global look at thedecisive trends and developments of the retreading industry. The focus this time is on "Retreading as Best Practise for the Circular Economy."
An important theme we are emphasising for THE TIRE COLOGNE in a targeted fashion is "digitalisation." Digitalisation affects us all and is causing a dramatic change in all areas of life. The digital transformation opens up big chances for more qualityof life, new business models and more efficient business economy. In the framework of the Digital Strategy, Koelnmesse deals with all aspects of digitalisation that are or might become relevant for the company and the trade fair business. And digitalisation has also long since arrived in the tyre industry. With various sessions on the stage of THE TIRE COLOGNE, we will show what digitalisation already means today for all participants of the tyre industry, and how it can be used for your business.
The digital transformation remains a definitive theme of decisive importance for the future focus at Koelnmesse, but surely also for the tyre and wheel industry. For us as Koelnmesse, digitalisation is the central development programme in the company, on which more than 100 of our own employees are working. The goal is the successful transfer of the core business of the trade fair into the digital world: through the development of digital services and business models, the improvement of internal processes, the digitalisation of the fair grounds and the expansion of the corresponding trade fair themes. The programme includes both projects that have already been in existence for a longer period of time, such as ticket and access systems, or a digital sales system introduced two years ago, but also new themes like the digitalisation of traffic management or digital signage, a joint project with Samsung. It unites route guidance, infotainment and advertising on more than 200 m² of digital area and is currently being further expanded upon – and is of course being used for THE TIRE COLOGNE.
Digitalisation influences markets and needs – as well as our exhibitors and visitors. Digitalisation is therefore a strong aspect for the tyre and wheel industry, because it permeates trends and changes. In order to intensify this understanding and be able to react to possible challenges "just in time," THE TIRE COLOGNE, together with the IFH, the Institut für Handelsforschung in Cologne, has carried out an extensive study and survey of the tyre trade in five core markets - in Germany, the United Kingdom, Italy, France and Poland. The goal of the study is to verify the themes of relevance to the trade in the respective countries, and how it reacts to challenges, whether with regard to digital transformation, digital tools, trends or recruiting staff. Very informative were the findings, and in some cases very different findings in the countries surveyed – also and in particular with regard to the theme of digitalisation and the use of digital tools to address and secure the loyalty of customers.
However, the study is only the first step of this project. We will soon also be offering the specialised trade the possibility to benchmark itself and its service profile against the European average at the website of THE TIRE COLOGNE. With the comparative result of the "Fit forthe Future" test, the participant also immediately receives a brief analysis and possible approaches to solutions, which could be of benefit for the further development of their own business.
The international tyre and wheel industry is strong and has great potential. However, it must at the same time invest in order to assure this potential. THE TIRE COLOGNE will contribute to this development as the leading international industry platform!
( Kindly Note: THE TIRE COLOGNE has been postponed until 2021. The organisers yet to declare new dates)
Extensive study, survey supplemented with Fit for Future test
As the leading platform for tyres and wheels, THE TIRE COLOGNE sees itself not only as a business hub that brings together all relevant players from industry and trade in one place. Much more than this, it sees its task in the presentation of themes and content that benefit the future development of the industry. "We see ourselves as part of the industry and want to point out solutions for the constant market changes, with the goal of setting sustainable impulses for the development of the industry. This is the bar we have set for ourselves. This year we initiated a study in five European core markets, the results of which will provide all market participants with a better understanding of the function of the respective markets and the challenges there. Building on the results of the study, each trader can now check themselves in our downstream "FitforFuture-Test" to find out where they stand and where there is room for improvement," according to Christoph Werner, Senior Vice President Trade Fair Management of Koelnmesse.
Markets are constantly changing and, as a consequence, also the needs of customers. In order to intensify this understanding and be able to react to possible challenges "just in time," THE TIRE COLOGNE, together with the Institut für Handelsforschung in Cologne (IFH Köln), has carried out an extensive study and survey of the tyre trade in five core markets - in Germany, the United Kingdom, Italy, France and Poland. Managing directors, owners and masters from companies in the specialist tyre trade from five countries were surveyed, and secondary research and interviews was carried out. The survey focused on the clusters of digitalisation and digital tools and automobile mega-trends, as well as personnel recruiting and continuing training of staff.
A short summary of the study results:
Digitalisation is bringing big challenges for tyre retailers: The European tyre trade is changing rapidly. This is being propelled by changing customer behaviour. The customers of the tyre trade have considerably higher expectations of service than in the past and expect communication on all channels with coordinated sales and service offerings. Digitalisation is also changing and is placing one sector after the other in question - the tyre trade must keep up with the general digital transformation. The challenges relating to this have for the most part been recognised and tend to be evaluated with reference to the chances. Nonetheless, there are sometimes shortcomings in implementation. The reason: the tyre trade isn't daring enough. The broad portfolio of digital tools has not yet been utilised consistently. In addition to this, mega-trends are classified as science fiction without looking for one's own advantages in the here and now.
Tyre trade will soon face a personnel problem: This is exacerbated by a massive personnel problem - at least in most European countries. The tyre trade is already facing problems recruiting new employees in the core area of the workshop, but also with the acute line of succession. And there are no effective remedies in sight.
What needs to be done?: The tyre trade must develop a certain amount of self-confidence. This must correspond with the core requirements of the digital age - meaning, be present on all channels and be based on smooth and rapid processes. Only then can one provide profitable offerings, products and services. In addition to this, the tyre trade requires a broader portfolio of digital instruments for internal and external use. More practice and continuity in the usage of these instruments is also required. In addition to this, the tyre trade requires creative solutions and must develop convincing arguments extending beyond the standard offerings, in order to find and bind more employees.
FitforFuture test and best practise
All results of the THE TIRE COLOGNE study - complete, as a management summary, but also the evaluations of the individual countries and core topics - are available for download on the website of THE TIRE Cologne at https://www.thetire-cologne.com/the-fair/tireresearch/tireresearch.php . Furthermore, on the website of THE TIRE COLOGNE the FitForFuture test can be used effective immediately to check how one's company is developing in terms of #DigitalTransformation, #DigitalToolbox, #Recruitment/ human resources development and #Trends.
Subsequent to this, he will immediately receive the test results and relevant best practice examples from the aftermarket, but also from other retail industries.
Of course, findings from the study will also play a role in the context of the congress and event programme of THE TIRE COLOGNE, where the four core themes will be discussed with industry participants and experts in special theme forums. Subsequent networking events provide exhibitors and visitors with additional added value while looking at the study and discussion results in greater depth.
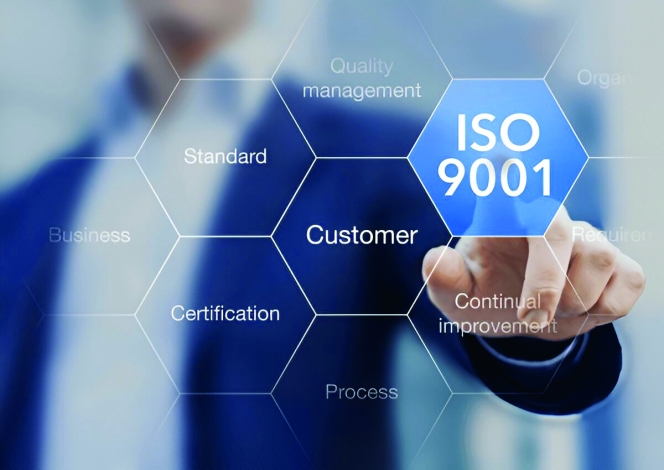
Some exiting insights
I would say that my baptism to ISO 9001 Quality Management Standard (which UpToDate is the most commonly used standard) was in 1999, a little over 25 years ago, at my last work place in Sri Lanka, which at that time was one of the leading tyre retreaders and manufacturers of two/three-wheeler tyres and custom-mixed compounds in our country. Even with my long working association with leading rubber companies, I should say I was amazed, but not in any way bewildered by the vast number of documents and paperwork deployed in establishing and maintaining the Quality Management System (QMS). The 1994 version of ISO 9000 standard used during that period had three versions, namely 9001, 9002 and 9003, adopted for manufacturing industries, service organisations and those engaged in inspection and testing respectively. The 9001-standard recommended 20 mandatory documented procedures, a Quality Manual that was compulsory and the need for work instructions at every conceivable activity. In a way, one cannot be surprised by this apparent proliferation of documentation because the first version of the ISO 9000 QMS standard in 1987 had its origins in the British Military Quality Standard BS 5750, which inherently required a high level of accuracy, precision, consistency and reliability, and hence the necessity for micro detail. Nevertheless, during the gradual evolution of the standard to its current status, one can clearly realise the transformation of the requirements to embrace the changes required for the emerging global needs of the manufacturing and service sectors of the civic society. In this article, I endeavour to bring forth some interesting practical experiences gathered during my working life and consultancy and auditing during the past 25 years with the ISO 9001/14001/and 45001 management systems in the rubber, plastics and other non- related manufacturing and service sector organisations in Sri Lanka.
Out of the numerous definitions of a management system, I find the following as a short, simple and concise and practical one:
A Management System is an organised way of defining, implementing, monitoring and improving an organisation’s operations to meet business goals, comply with regulations and enhance overall performance.
When contemplating deeper in to this apparently simple definition, I feel that it has far-reaching implications about management systems, stretching back to our ancient civilisations. One cannot comprehend how the great architectural designs, religious constructions, irrigation and the water management systems, harmonious with the natural eco-systems, were made possible without well-established management systems, although they would have been conceptually different from the contemporary management systems of the modern times. Just to site one example, during the design phase of the Maduru Oya Irrigation Project in Sri Lanka with the assistance of Canadian government in the late 1960s, the modern agro-engineers unexpectedly discovered the ruins of a centuries old anicut (ancient diversion weir). This remarkable find highlighted the advanced hydrological knowledge of our ancient civilisations, demonstrating their ingenuity in water management. Rather than disregarding the historical structure, the engineers decided to incorporate the principles in to their modern designs. Utilising the cutting-edge technology while respecting the traditional engineering wisdom in to their modern design, they constructed a new anicut that blended past innovations with contemporary advancements, enduring sustainable water distribution for agriculture.
Now coming to the more recent times in history, I can recollect that the rudiments of standard operation procedures (SOPs) and documentation, which are some of the salient features of the modern-day management systems, could be seen at the Bata Shoe Company of Ceylon Ltd, which was one of the blue-chip companies in Sri Lanka (the then Ceylon) in the late sixties, when I joined the company as a young Management Trainee. Standardised production control and hourly progress monitoring of the shoe assembly conveyors was used in the one hundred plus Bata companies spread throughout the globe. The rubber formulae cards also were also of a standard format, showing the issue date, revision status and revising date, and very importantly, the review and approval for use, all of which are key aspects of the control of documented information of the ISO Standards, which were first introduced in 1987. Another good practice used, although I realised the importance of it in later life, was the pre-preparation with the arrangements to ensure the 4Ms, namely men/machines/materials and methods to run the next day’s production, before we go home at the end of the working day. This was, in reality, the addressing of the process risks and taking preventive action to avoid the occurrence of problems, which is covered by ‘risk-based thinking’ or ‘what can go wrong’ in simple jargon and is incorporated in all the ISO Management System Standards in use today. Ironically, from my observations, only very few companies are making use of this golden principle in managing their day-to-day affairs, and hence the need for so many ‘meetings’ and firefighting, which has become a typical feature in many companies nowadays.
The crux of the matter is that management systems, in whichever names or forms they were known, have been used historically in all types of organisations, with varying degrees of success and failures, and hence the concept is nothing new. However, the International Organisation for Stadardisation (ISO), over the past 40 years, has endeavoured to bring together the cotemporary practices and thoughts about managing organisations to achieve desired outcomes in the form of all-encompassing requirements, which are universally applicable, especially in ISO 9001/14001 and 45001.
ISO 9001, the most widely deployed management system standard, was first introduced in 1987 by adopting the British military quality standards (BS5750) and aimed to create a universal approach to quality management. Over the years, ISO 9001 has undergone multiple revisions, in line with the changing global business scenarios, to make it more flexible, customer-focused and risk based, and the latest amendment has accommodated climate change issues. As environmental concerns grew in the late 20th century, the need for a systematic approach to environmental management became evident, and ISO 14001 was introduced in 1996 as response to global sustainability challenges, aligning with the Rio Summit objectives. Its revisions in 2004 and 2015 have strengthened its focus on life cycle thinking and integration into corporate strategy. ISO 45001 released in 2018 and replaced the OHSAS 18001, which has served as the primary occupational health and safety standard since 1999. It was developed to provide a structural framework for organisations to adopt a proactive risk management approach, rather than a reactive compliance-based model.
The adoption of these standards is often seen as a necessity for organisations seeking credibility, regulatory compliance and competitive advantage. Moreover, the possibility of integration of these standards allows businesses to create unified management systems, reducing redundancy and administrative burden. The High-level Structure (HLS), unreproduced by the ISO, is aimed to ensure consistency across the different management system standards.
On looking back, with the knowledge and experience I have gained by associating with the ISO-based management systems from the 1990s, I would say that the decade commencing from the mid-nineties was a period of bee-hive of activities for the manufacturing organisations in Sri Lanka. The tendency to embrace and accept any new methodologies, especially when they are successfully used in other parts of the world, is a natural survival instinct, or what has come to be known as benchmarking in the conventional management jargon, or colloquially ‘keeping up with the Joneses’. Similar trends can be seen during the introduction of other productivity improvement methodologies, such as 5S, Quality Circles, Toyota Production System (TPS), Lean and Kaizen concepts, which trickled down to our part of the world around the same period and caught up like wildfire. A notable deviation which I observed in the later methodologies is that they were directly linked to the operations, whether in manufacturing and service industries, and hence baring the initial mind set and attitudinal issues, it was relatively easier to implement and, in most cases, the results and the outcomes were directly and sometimes instantly visible, especially to the floor level personnel.
On the contrary, ISO-based management systems encompassed a more holistic and inclusive systems approach, which most top management and other managerial personnel naturally found somewhat difficult to grasp, and hence I would say that the learning curve progressed on a slow gradient.
The desire and the willingness to adopt the ISO 9001 system on the one hand and the lack of proper knowhow and experience on the other resulted in the complexity perceived by many companies in those early years. The certification bodies and some management consultancy training providers both locally and from overseas began providing the initial training, and these too were on the early stages of the learning curve due to lack of hands-on and practical experience, although the theoretical knowledge was adequately provided. As in the case pf many new waves of management thought, these conditions were ideal for some consultants to levy exorbitant facilitation fees. The mandatory conformity requirements for documentation, while resulting in the proliferation of paperwork, placed excessive burden and stress on the staff who were involved in the establishment and maintenance of the management systems. In the early years, some of the auditors of the certification bodies also focused too much on documentation and document control, document lists and revision numbering, which made the auditing a somewhat sterile exercise.
However, practically all the companies laid high emphasis on preparing for the audits, especially if they happen to be certification or recertification audits. Complete overhauling of the facilities, colour washing and cleaning up were normally carried out in addition to updating all documents and records, some of which have been neglected or not properly maintained throughout the year. Audit days had a sense of austerity and an aura of its own, which I think was good in a way at least once a year, although it could have sent wrong signals to the employees regarding leadership and management commitment as specified in Clause 5.0 of the standards.
The dichotomy between ISO requirements and the other management functions is still seen in some companies, especially the large organisations, which have management system coordination assigned to a septate department. Although the High-Level Structure of the three standards is intended to facilitate to enable an integrated management system, only a very few companies seem to be doing it effectively.
Despite their wide spread adoption, the real-world application of Management Systems like ISO 9001/14001 and 45001 varies significantly. While some organisations genuinely integrate these systems into their operations, others treat them as bureaucratic hurdles for securing certification for external validation and legal compliance rather than for internal improvement. The question is often raised as to whether businesses are blindly embracing these standards, or are they judiciously adopting them for real impact?
The cost and complexity of implementation can be prohibitive, especially for the small and medium scale enterprises (SMEs), and achieving and maintaining certification requires significant resources, which can divert attention from the core business activities. While the standards provide a good framework, their success largely depends on an organisation’s commitment. A poorly implemented system can lead to inefficiencies, resistance from employees and minimum real-world impact. Furthermore, in some industries, rapid technological advancements outpace the evolution of these standards, making them seem rigid or outdated.
These management systems can be powerful tools for improving quality, sustainability and workplace safety if used correctly. However, their effectiveness depends on how they are implemented. Blind adherence to ISO standards very often causes inefficiencies and a waste of resources, and judicious and strategic adoption can drive real improvements.
I vividly remember an awareness programme organised by the Sri Lanka Standards Institution around the year 2000 to introduce the major changes in the ISO 9001: 2000 Standard. In one of the presentations, ISO 9001-based QMS was depieced as an elephant on which the organisation rides to use the system, while what happens in many a case is the organisation carrying the elephant (QMS) as an extra burden.
Margaret Wolff Hungerford, in her 1878 novel Molly Bawan, first mentioned the famous quote ‘beauty is in the eyes of the beholder’, which augments well to the ISO-based Management System Standards.
At this juncture, I cannot resist citing a Buddhist discourse where the doctrine (Dhamma) is depicted as a piece of gold. For a child it will be a play item, and for investor it is a valuable asset whose value keeps on appreciating with time, while for the jeweller it will be the source material that can be turned into a beautiful necklace.
Management System Standards will continue to play a vital role in helping organisations to systematically manage their activities to the foreseeable future with varying degrees of success along with the appropriate amendments and revisions that may come into effect from time to time.
The author is a Management Counsellor from Sri Lanka.
The Role Change Plays In The Roll Of A Tyre
- By Adam Gosling
- April 21, 2025
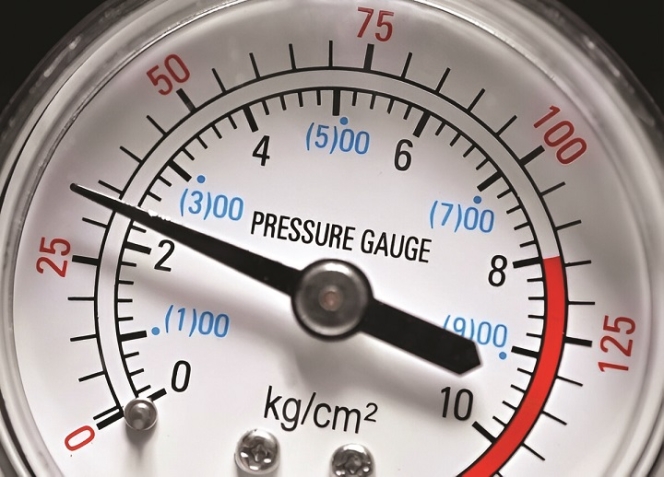
A rolling tyre is everchanging. It is responding to the inputs from the driver, from the vehicle, from the pavement and even from the environment.
As change is the basis of a tyre, why is change strongly resisted by so many?
As the tyre rotates around the contact patch, there are changes in shape of the tyre. As the tyre responds to steering or braking inputs, there are further shape changes; hit a bump or corner in the road and there are further shape changes.
The tyre responds with solid service, providing the driver of the vehicle with dependable responses if the tyre has been appropriately maintained. The reliable service is very much dependent upon the inflation pressure being appropriate for the load and speed the tyre is supporting. This can only be supplied by the humans responsible for the maintenance at this point of tyre development.
Which then leads to the question: If service is so critical, and change is the basis for a tyre’s performance, then why are humans so reluctant to change?
When you pass a trucking stop, note how many drivers are still using a lump of pipe to ‘gauge’ their tyres inflation levels, or at the supermarket car park look at the condition of the tread faces, noting the irregular wear patterns
Then consider why the basic requirement of adequate tyre maintenance has been and is still so hard to change from the ‘tyres don’t exist’ mentality to ‘tyres keep me safe and improve my economics’.
Looking at the highways and freeways, we still observe the ‘gators’ of shredded tyres. The poor tyre has had enough abuse and has gone end of life and disintegrated. NO, these are not just retreaded tyres, most are actually virgin (first life) tyres that have surrendered due to a lack in inflation pressure or overload.
The tyre OEMs work hard to provide a safe and efficient product for the road industries, but once the tyre leaves the shop, there is little if any control the tyre OEM has. The end user assumes all responsibility for the tyre’s performance.
The Clinton (USA) administration recognised this in 2004 with the introduction of the TREAD Act, requiring real-time tyre pressure monitoring (TPMS) to be fitted to passenger vehicles. The EU and other jurisdictions have subsequently followed mandating TPMS, the EU for heavy goods vehicles in 2022 and 2023.
The recognition of the lack of service applied by the end user was the foundation of the TPMS installations; maybe an alert light on the dash will prompt some (now overdue) attention to the tyre’s inability to continue providing the reliable service they are known for.
Supermarkets have introduced self-service check outs, which much to the chagrin of many shoppers, have continued to be used. The shopper is performing the service of the goods provider; airports are seeing the same, so there is evidence that change can happen (for good or bad or other trumped up reasons). There is no doubt many other examples, including the interweb, where all sorts of self-service industries have been created. Many such examples are failing; the quest for ‘new’ is fraught with hazard. The basic tyre has not been changed, more so refined and undergoes constant evolution.
So the question remains, why are tyres on the bottom of the heap when human required service is involved? Could it be that tyres work too well? Do we need to return to the manual checkout style of service to enable tyres to receive the service they require?
Change is not doing what we did yesterday and expecting a different result; someone once muttered that’s the definition of insanity. At the same time, there is little use in trumped up changes for the sake of change, that can be easily evidenced in politics.
Change for change’s sake without any direction is akin to driving on a severely underinflated tyre; you really have no idea of what it will do or where it may take you and how long it will last. Like so many aspects of life, balance is required. For a tyre, that balance is the level of inflation for the load and speed to be experienced; if the pressure is not appropriate, then the end user’s experience may not be what was expected.
Our planet Earth is facing a continuing evolution, which for all intents and purposes seems to be increasing in momentum, like a runaway tyre heading downhill complete with the bumps launching the tyre onto a tangential path. How are we (collectively and individually) going to face these changes is a point of great consternation but a moot point for many.
Our tyre OEMs invest huge sums in testing of tyres both virtually and physically, yet all this effort can be undone at the end user level by lack of knowledge, lack of interest, lack of care or option D (all of the above), which contribute to the detriment of the tyre’s performance.
How do we, as an industry, expand what we understand to be the basic principle of the operation of a tyre (i.e. continuous change) to incorporate the attitude and approach of the end users of the product our industry produces to enhance their safety and economic benefit?
This is a serious test of our industries’ ESG policies, abilities and the desire to provide the highest possible public service.
Stay TyreSafe
Rolling Steady
- By Rajiv Budhraja
- April 21, 2025
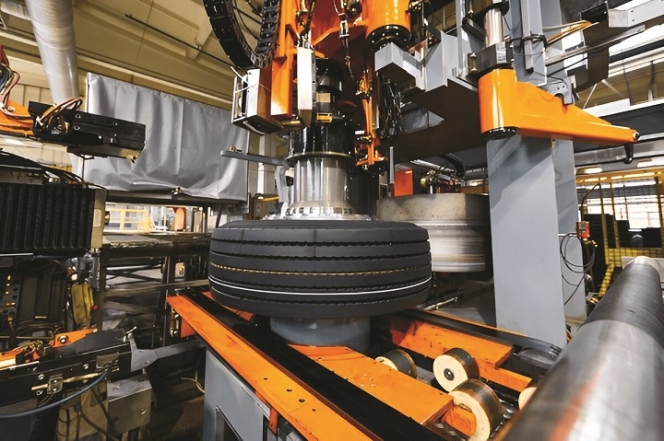
As we wrap up the fiscal year 2024-25, it’s an opportune moment to reflect on the performance of the Indian tyre industry in the year gone by. Since recovering from the Covid-19 pandemic, the industry has maintained a steady upward trajectory, though the momentum has slackened. Challenges such as rising raw material costs and subdued domestic demand posed hurdles, yet the sector saw resilience through growth in exports and strategic expansions by key players.
The industry’s revenue growth in FY 2024-25 has been modest, with projections indicating a 5-6 percent increase much like the previous year. At the same time, natural rubber, constituting nearly 40 percent of the raw material mix for tyre production, saw a price surge due to global shortages caused by adverse weather in major producing nations like Thailand and Vietnam. This sharp rise, coupled with the modest ability to pass on costs to customers, significantly impacted production costs and profitability for tyre manufacturers.
EV adoption is accelerating in India, leading to new challenges and opportunities for tyre manufacturers. EVs exert higher torque and weight, requiring specialised tyres with greater durability. Manufacturers are focusing on developing energy-efficient tyres that reduce rolling resistance, thereby extending EV battery range. Leading tyre companies have introduced EV-specific tyres to cater to this emerging market. While EV penetration is still in its early stages, it is expected to reshape the tyre industry’s R&D priorities in the coming years.
Notwithstanding domestic challenges, the Indian tyre industry achieved notable success in the export market. Tyre exports grew by 11.7 percent in value, reaching INR 121.31 billion during the first half of FY 2024-25. This surge is attributed to investments in research and development, leading to the production of advanced tyres that meet international standards.
However, exports, which constitute around 25 percent of the industry’s sales, are facing headwinds due to weak demand in key markets like North America and Europe, coupled with supply chain disruptions and increased freight costs.
With growing environmental concerns, sustainability and eco-friendly manufacturing have become key priorities. Companies are exploring bio-based alternatives for rubber compounds and recycled raw materials to reduce their carbon footprint. The focus on tyre recycling and circular economy models is increasing. Government policies promoting sustainable mobility and lower emissions are expected to further accelerate these trends.
Government intervention, especially the Make in India push, continues to play a critical role in tyre industry’s growth. The extension of countervailing duties on Chinese radial tyres helped provide a level playing field for domestic manufacturers. The government’s emphasis on strengthening the manufacturing sector through the National Manufacturing Mission, enhancing logistics infrastructure and expanding road networks as outlined in the Union Budget 2025-26 will have a significant positive impact for the tyre industry.
Companies are going for strategic capacity expansions focusing on high-margin segments like radial truck tyres and premium passenger car tyres. The investment in automation and digitisation to improve production efficiency in the face of cost pressures is a key running theme among top players.
High raw material costs, global demand uncertainty and slow domestic OEM growth will remain concerns in the near term. However, the Indian tyre industry continues to demonstrate resilience and adaptability, paving the way for steady growth in the coming years. The continued focus on technological advancements, sustainability initiatives and prudent financial management is expected to steer the industry towards a stable and growth-oriented future.
Rajiv Budhraja is Director General of the New Delhi-based tyre industry association, Automotive Tyre Manufacturers’ Association (ATMA).The views expressed here are personal.
Brand Stands Out By Comprehensive Testing…
- By Ertugrul Bahan
- April 15, 2025
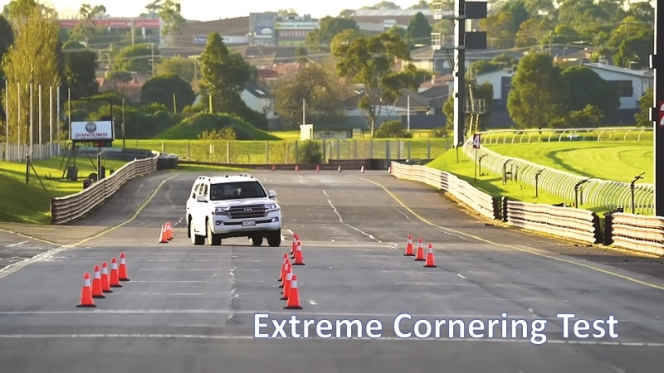
Are tyre failure or lack of control really the driver’s fault or could a better tyre survive?
Catastrophic tyre blowouts occur unexpectedly and pose a significant risk to drivers and passengers. After a tyre blowout, steering becomes difficult to control, the vehicle pulls sharply to the side, fishtailing, and loses stability and control at high speeds.
After a tread detaching, wobbling and vibration in the wheel occurs while pieces of tread are flying off the tyre. When the tyre rotates, a dull noise is produced, which makes traction and vehicle control impossible, especially on wet roads. The sidewall is visibly bulged or split, and the vehicle sags sideways after a tyre blowout. Maintaining control is then difficult, especially when cornering.
Bead unseat or bead burst, overheating and melting, impact breaks, explosive failure in commercial tyres can be added on this list. What about cases where a driver can survive a cornering manoeuvre due to insufficient sidewall stiffness and lateral grip, or could they survive hard braking with a tyre that offers a much shorter stopping distance on wet roads?
Are these failures or lack of control really the driver’s fault or could another tyre survive and you would have the best outcome if you could save your car and your life without being charged as a reckless driver?
Premium tyres are generally safer and offer significantly better performance in almost every metrics.
Tyres are regulatory base tested before releasing to market. If the conducted tests based on legal requirements would be enough safe, customers in the market shouldn’t be faced with unexpected results. In fact, it reminds us the differences of premium tyres! What differences ‘Premium Tyres’ create?
Premium tyres are generally safer and offer significantly better grip in all conditions. They last longer, thus retaining their original performance and generally reducing fuel consumption. They are quieter overall and provide more driving pleasure. Their initial cost proves to be a significant advantage in the long run, as the comprehensive benefits lead to long-term cost savings.
Premium tyres are pushed to their limits in dedicated testing facilities, tested under extreme conditions so intense that most of us will never experience – but for which we all need to be prepared. This is an extremely rigorous process that goes beyond the requirements of European tyre labelling, which is limited to wet braking, fuel consumption and exterior noise levels.
‘Content Marketing’ with relevant sharing through blog posts, videos, infographics and pop-ups takes advantage of sales.
Today, social media is widely accessible for news and tyre test results. This allows drivers to rely on real-world differences from comparison tests of different brands and expert advice to find the right tyres for their budget, rather than relying on external influences.
When considering trends in the tyre industry, the topic of ‘Sustainability’ is becoming increasingly important. The use of bio-based materials will become more widespread. Furthermore, ‘Sensors, IoT technologies and Cloud Systems’ significantly support smart tyre concepts, while drivers can access information about the vehicle and surrounding traffic.
Electric cars, on the other hand, pose a challenge due to their differences. More importantly, current advances in the safety and performance of ultra-high-performance tyres particularly in terms of pattern and compound design are so fine. Their optimal performance in terms of grip, handling, braking, smoothness, rolling resistance and durability are well suiting for electric cars.
Online Retail and ‘Direct-to-Consumer Sales’ are least but never last trends that influence the popularity and ways customers are reached. E-commerce sites offer many opportunities. ‘Content Marketing’ with relevant sharing through blog posts, videos, infographics and pop-ups takes advantage of this. Key product features and benefits are presented in a visually appealing format, helping to increase customer loyalty online and in direct sales.
The safety requirements of each target service and regulatory compliance concerns vary considerably from tyre to tyre. Therefore, testing must be conducted under different conditions. Most cases of loss of control depend heavily on the success of the tests conducted during the design phase.
Of course, compliance with legal regulations is important, and some factors vary from country to country. Therefore, every tyre must meet legal standards, and product compliance is ensured through testing.
Tyre manufacturers conduct extreme tests, or ‘endpoint tests’, to explore the limits of tyre performance, which help to differentiate their products in a highly competitive marketplace.
Transparency about tyre performance is important to inform buyers. Choosing tyres for a specific vehicle and application must be clearly understandable to customers. Consumer confidence is therefore important, and thorough and rigorous testing must be planned and conducted to meet requirements. The data provided must be shared via social media and magazines.
Continuous improvement is essential to meet changing customer needs and technological advances. Tests provide important information for the design and materials of new tyre models. Only the results of carefully conducted tests can help designers achieve further improvements.
Tyre manufacturers conduct extreme tests, or ‘endpoint tests’, to explore the limits of tyre performance. In addition to durability and high-speed testing, track tests that exceed standard testing limits and protocols are conducted. These unique tests often demonstrate their commitment to performance and safety and help differentiate their products in a highly competitive marketplace.
By extreme tyre tests, manufacturers can promise superior performance and safety, thus establishing a selling point in a competitive marketplace.
Tyres undergo rigorous testing under extreme heat and cold conditions, including temperatures well above normal operating temperatures, including plus or minus 40°C. This allows us to understand how tyres behave under thermal stress, wear, tread separation and subsequent failure modes that can occur in extreme environments.
High-speed and endurance testing is primarily conducted in-house at speeds significantly above typical highway speeds, reaching over 200 km/h for extended periods, depending on the tyre’s speed rating. Furthermore, it is possible to evaluate very high threshold performance in terms of stability, wear and potential failure due to centrifugal forces, ensuring tyre integrity at extreme speeds.
In ‘Heavy Load Tests’ testing, tyres are subjected to loads far beyond normal operating conditions, simulating, for example, use on heavy commercial vehicles or overloaded passenger cars. These tests allow the behaviour of tyres under abnormal loads to be determined by evaluating their durability, temperature rise and long-term wear. These tests can be critical for commercial and high-performance vehicles.
‘Abrasion Tests’ simulate extended use on highly abrasive surfaces such as gravel, sand or even artificial surfaces. Tyre durability in harsh environments can be tested, providing concrete results from innovations in tyre compounds, especially for off-road and high-performance tyres.
Other examples of extreme tyre tests include ‘Aquaplaning Tests Beyond Normal Wet Conditions’ conducted in great water depths and under varying pressure conditions; ‘Puncture Resistance Tests’ under extreme conditions; ‘Extreme Terrain Simulation Tests’ on special tracks such as mud, snow or rocky terrain and ‘Fatigue Tests and Life Cycle Analysis’ to check whether performance deteriorates over time.
The ‘Environmental Simulation Chambers’ as internal equipment allow for the simulation of chronic exposure to factors such as UV radiation, ozone and humidity, as well as the evaluation of how external elements contribute to rubber degradation over time. This ensures that the tyre can withstand prolonged exposure to environmental stress without sacrificing performance.
These advanced or extreme tests allow tyre manufacturers to better understand the limits and capabilities of their products. By providing empirical data from these rigorous evaluations, companies can promise superior performance and safety, thus establishing a selling point in a competitive marketplace.
Today’s highly competitive environment requires market differentiation. Superior performance indicators can increase the market appeal of tyres by sharing test results and differentiating a brand’s products. In today’s highly competitive environment, only extensive testing can help brands stand out from the crowd.
Comments (0)
ADD COMMENT