- Yokohama Rubber
- Zeon Corporation
- Butadiene
- Ethanol
- New Energy and Industrial Technology Development Organization
- Sustainable Materials
- Polybutadiene Rubber
Yokohama Rubber & Zeon Join Hands For Production Of Plant-Based Butadiene
- By TT News
- February 18, 2025
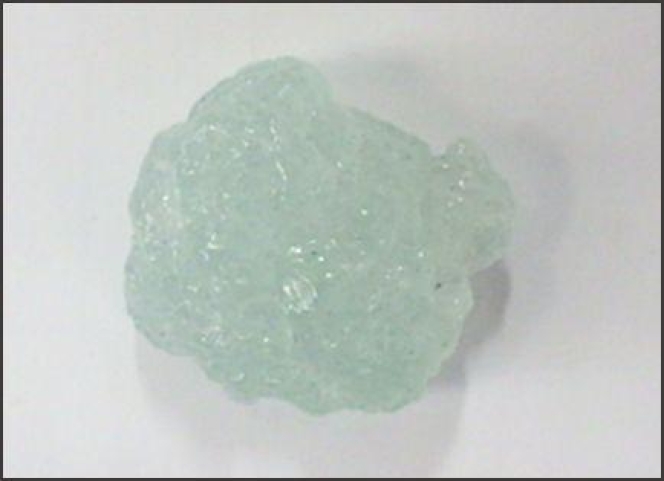
The Yokohama Rubber Co., Ltd. and Zeon Corporation have decided to work together to build a bench facility to showcase technologies for efficiently making butadiene from ethanol made from plant-based and other sustainable sources. Zeon's Tokuyama Plant in Sunan City, Yamaguchi Prefecture, will house the plant, which is expected to start up in 2026. It will make it possible to produce a specific quantity of butadiene and make it easier to gather the many types of data needed to develop mass manufacturing.
The New Energy and Industrial Technology Development Organisation (NEDO) chose two research and development themes in 2022 for its project, ‘Development of Technology for Producing Raw Materials for Plastics Using CO2 and Other Sources’, which is one of the Green Innovation Fund Projects of NEDO. This initiative is in line with one of those themes. The National Institute of Advanced Industrial Science and Technology (AIST), National University Corporation Institute of Science Tokyo (formerly Tokyo Institute of Technology) and the national research and development agency RIKEN are working together to develop two technologies that will allow for the highly efficient production of butadiene and isoprene from plant-based and other sustainable materials in the 2030s. Zeon and Yokohama Rubber are working towards the social implementation of these technologies. The bench facility to be installed at the Zeon plant is part of initiatives based on the theme ‘Highly Efficient Butadiene Synthesis Using Ethanol’.
The experiment at the new bench facility will show how to use a very effective catalyst to turn ethanol made from plant-based and other sustainable materials into butadiene. This will be the first stage in establishing the technology's use for the large-scale manufacturing of synthetic rubber from plant-based and other sustainable ingredients. From the butadiene produced at the bench facility, Zeon will create a prototype polybutadiene rubber (butadiene rubber). Yokohama Rubber will use the butadiene rubber to create prototype tyres and test the tyres' performance to gather information for a larger-scale technology demonstration.
Kuraray's Rubber Business Faces Headwinds As First-Half Profit Tumbles On Weak Demand
- By TT News
- August 13, 2025
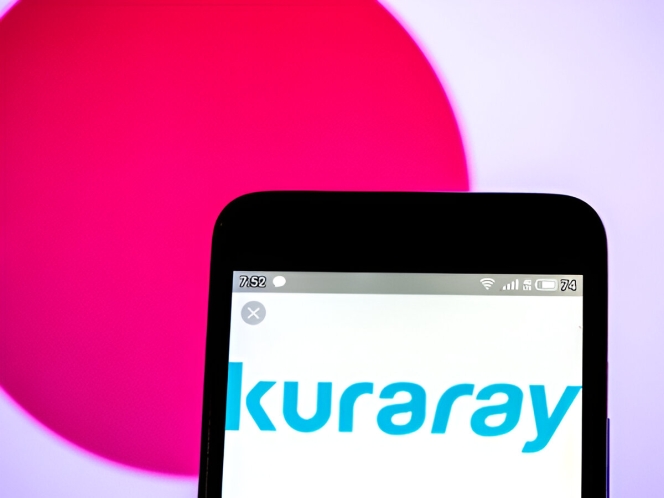
Japan's Kuraray Co Ltd reported a 42 percent plunge in first-half operating profit as its rubber and speciality chemicals business grappled with weakened European demand and inventory valuation losses, prompting the company to slash its full-year earnings forecast.
The Okayama-based manufacturer, known for its synthetic rubber and speciality polymers used in automotive and industrial applications, posted operating income of 26.3 billion yen for the six months ended June 30, down from 45.5 billion yen a year earlier.
Net sales slipped 2.7 percent to 400.0 billion yen, with the company's flagship vinyl acetate segment - which includes rubber-related products - bearing the brunt of the downturn as volumes declined across key markets.
"Sales volume did not increase as much as expected due to the European economic stagnation and other factors, and overall segment income decreased due to the negative impact of inventory valuation differences and higher raw material and fuel prices," the company said in its earnings statement.
The vinyl acetate division, Kuraray's largest revenue contributor, saw operating income tumble 31.9 percent to 29.9 billion yen despite maintaining sales of 202.9 billion yen. The segment includes the company's EVAL barrier resins used in food packaging and automotive fuel tanks, as well as polyvinyl alcohol (PVOH) resins with rubber-like properties for industrial applications.
Kuraray's isoprene chemicals and elastomers business, which produces synthetic rubber compounds, showed signs of recovery with operating losses narrowing to 1.3 billion yen from 4.0 billion yen a year earlier. Sales volumes increased as demand remained firm, particularly in Europe and the United States, whilst operations at the company's Thai manufacturing base stabilised.
However, the broader economic malaise weighed heavily on performance. Rising natural gas costs in the US and Europe - key raw materials for rubber production - further squeezed margins. US natural gas prices averaged USD 3.69 per MMBtu compared with USD 2.21 a year earlier, whilst European gas costs climbed to 41 euros per MWh from 30 euros.
The disappointing first-half results prompted Kuraray to revise down its full-year operating income forecast to 75.0 billion yen from an earlier projection of 90.0 billion yen, though it maintained its annual dividend at 54 yen per share.
Chief Financial Officer Hitoshi Kawamura highlighted inventory valuation differences as a significant drag on earnings, particularly affecting the company's rubber and polymer segments, where raw material price volatility has been pronounced.
Looking ahead, Kuraray expects second-half performance to improve, with operating income projected at 48.7 billion yen compared with 26.3 billion yen in the first half. The company is banking on a gradual recovery in European demand and the benefits of recent capacity optimisations.
The firm is also pursuing strategic shifts in its portfolio, including plans to expand its optical-use PVOH film production line and the acquisition of US-based Nelumbo Inc, whilst discontinuing production of certain acrylic polymers and polyester-related products.
CARBIOS Strikes Multi-Year Deal With Indorama Ventures For Tyre Textile Recycling
- By TT News
- August 07, 2025
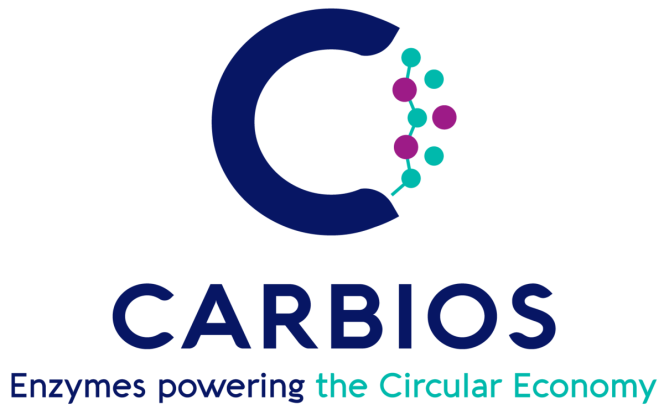
French biotech firm expands into industrial fabrics market through enzymatic PET recycling technology
French biotechnology company CARBIOS has signed a multi-year commercial agreement with Thailand's Indorama Ventures to supply recycled materials for tyre manufacturing, marking the firm's expansion into the industrial fabrics sector.
Under the deal, CARBIOS will provide biorecycled monomers from its planned Longlaville industrial plant to Indorama Ventures, the world's largest polyester producer. The Thai company will transform these materials into recycled polyethylene terephthalate (r-PET) filaments for use in tyre reinforcement by French tyre manufacturer Michelin.
The partnership represents CARBIOS's entry into a new market segment beyond its existing focus on cosmetic packaging applications. The company uses proprietary enzymatic recycling technology to break down complex PET waste into high-quality recycled materials.
"This commercial agreement with Indorama Ventures marks a new step in the realisation of our industrial project," said Vincent Kamel, chief executive of CARBIOS. "It confirms the trust of Indorama Ventures and Michelin in our PET biorecycling technology."
The deal comes weeks after CARBIOS signed its first sales contracts for biorecycled PET with two unnamed global cosmetics companies, as the firm builds momentum ahead of the commercial launch of its Longlaville facility.
Michelin, which has committed to using 100 percent renewable and recycled materials by 2050, said the partnership advances its circular economy objectives.
"This partnership is a tangible expression of our commitment to turning complex waste into high-performance materials," said Fabien Gaboriaud, director of circularity and renewable & recycled materials at Michelin Group. "By integrating enzymatically recycled r-PET into our tyres, we are marking a new milestone on our journey toward achieving 100 percent renewable and recycled materials by 2050."
Indorama Ventures, which generated $15.4 billion in revenue last year, said the alliance underscores its commitment to circular economy principles. The company employs approximately 25,000 people across manufacturing operations in Europe, Africa, the Americas, and Asia Pacific.
"This alliance with both, CARBIOS and Michelin, underlines our commitment to plan ahead and take a leading role in shifting the industry towards circularity," said Renato Boaventura, global market head mobility at Indorama Ventures.
CARBIOS, founded in 2011, has developed enzyme-based biological processes to break down plastics as part of efforts to prevent plastic pollution and accelerate the transition to a circular economy. The company operates an industrial demonstration plant for biorecycling that has been operational since 2021.
Construction of what the company describes as the world's first biorecycling plant is expected to resume in the second half of 2025, subject to securing additional funding.
Cabot Launches LITX 95F Conductive Carbon For Energy Storage Systems
- By TT News
- August 06, 2025
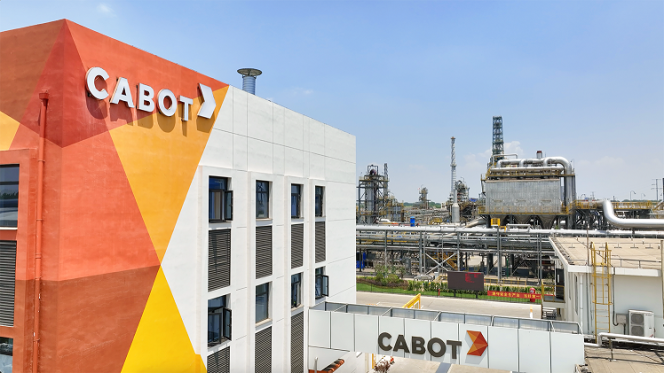
Cabot Corporation has launched LITX 95F, a high-performance conductive carbon additive designed for lithium-ion batteries in energy storage systems (ESS). Optimised for residential, commercial and industrial ESS applications, this advanced material enhances conductivity, extends cycle life and improves processability – critical for systems requiring durability under frequent charging and discharging.
With the global ESS market expanding due to renewable energy adoption and demand for grid stability, battery manufacturers need cost-effective, high-performance solutions. LITX 95F meets these needs by boosting energy density and cycle life while maintaining stability. Pouch cell tests with thick electrodes confirm its superior capacity retention, offering manufacturers greater flexibility in ESS design.
The material’s high-structure morphology strengthens conductivity and stability over repeated cycles. Additionally, its compatibility with thick cathode designs helps lower material costs without sacrificing performance. This innovation supports the growing ESS sector by enabling more efficient, reliable and scalable battery solutions.
Jeff Zhu, Executive Vice President and President, Carbon & Silica Technologies, Battery Materials and Asia Pacific Region, said, “As the global energy landscape continues to evolve, the ESS market requires advanced materials that deliver both performance and efficiency. Our new LITX 95F product is a direct response to the needs of the market and our battery customers – leveraging our deep industry expertise with proven performance to help scale ESS applications faster and more efficiently. This launch reflects our commitment to enabling a more sustainable future by delivering innovative solutions for battery technologies that support the energy transition at a global scale.”
- Association of Natural Rubber Producing Countries
- ANRPC
- Monthly NR Statistical Report
- Natural Rubber
ANRPC Publishes Monthly NR Statistical Report For June 2025
- By TT News
- August 06, 2025
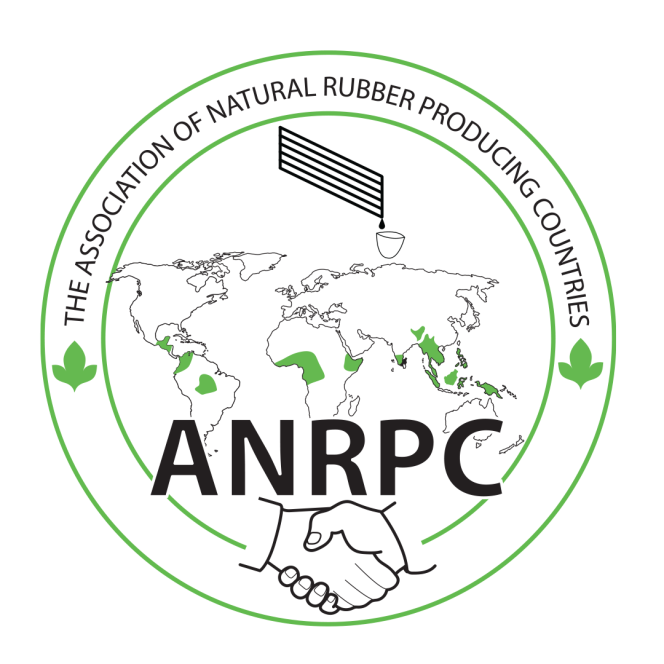
The Association of Natural Rubber Producing Countries (ANRPC) has released its Monthly NR Statistical Report for June 2025, providing an overview of key developments in the global natural rubber sector. The latest data indicates a sustained downward price trend, primarily driven by improving supply conditions in major producing nations, elevated stockpiles at key ports and ongoing trade policy uncertainties.
Market analysts attribute the bearish sentiment to a combination of factors, including increased output from leading rubber-producing countries and subdued industrial demand, particularly from tyre manufacturers. These conditions have contributed to mounting pressure on prices, with limited signs of immediate recovery. The ANRPC notes that while production levels remain stable, cautious demand projections persist due to broader macroeconomic concerns, including potential trade disruptions and slowing global economic growth.
Projections for 2025 suggest a modest 0.5 percent increase in worldwide natural rubber production compared to the previous year. Meanwhile, consumption is anticipated to grow by 1.3 percent, reflecting a slight but uneven recovery across key markets. However, analysts warn that external factors, such as shifting US tariff policies and weaker-than-expected industrial activity, could further dampen demand growth in the coming months.
Comments (0)
ADD COMMENT