eKanban takes on-time process visibility to the next level
- By Aki Nurminen
- December 30, 2020
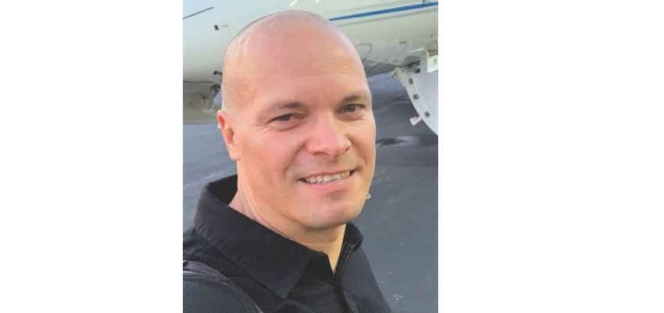
The praised solution has been in use at Eurl Saterex-Iris in Algeria since autumn 2019. Eurl Saterex-Iris is the third biggest tyre manufacturing plant in Africa, serving both local and export markets. The modern plant was mainly designed and constructed by Black Donuts Engineering and its international partner network. Black Donuts is also responsible for production management, which applies the core principles of Lean Management and focuses on reducing the interim stocks to the bare minimum according to the pull method. To enhance this, the company developed an RFID-based electronic eKanban solution together with Toptunniste.
“The eKanban project started from a need to improve production management. The first acute challenge we met was the lack of adequate and accurate information on the overall production status,” Solution Manager Aki Nurminen recalls.
Originally, there were nine Kanban boards located all over the two-floor factory. One had to check each board manually, so it took time and effort to capture a complete view of the production status.
Another deficit concerned the insufficient information provided on manufacturing schedules. The old Kanban boards did not give enough information on when certain materials were supposed to be in production.
The returned cards included no accurate time markings, so it was hard to stay updated, notice stock alerts and to respond on time.
Real-time production status
New technology was needed to solve the problem. It became clear that initiating remote monitoring would require electronic boards instead of the traditional ones. Black Donuts contacted another Finnish technology company, Toptunniste, to present the idea and search for a way to actualise it. The solution was simple: adding RFID features to an existing Kanban board would upgrade it to a more accurate, more informative, and easy-to-use eKanban board. Next, the old cards were replaced by RFID tagged cards, readable through RFID technology.
Now, all nine eKanban boards are online in Saterex’s internal data system and easily monitored from any computer. Consequently, an up-to-date overall view of the entire production is now always at hand.
The eKanban solution enables better and real-time tracking of overall production status and enhances the supervision of production processes.
It adds the time markings automatically to each card on return, keeps account, and establishes automatic triggers to replenish stock when predefined minimums are reached for each inventory item.
The system also calculates and presents the estimated time left before reaching the pre-defined minimum of each item in the downstream processes. This is the lens that helps us prioritize and schedule the production runs.
Optimised processes
The new eKanban boards were taken into use at Saterex tyre plant in fall 2019. For the users operating in the production lines, the new solution has not brought any changes in their daily routines, but the Kanban boards are used the same way as before. For the supervisors and factory management, the new system enables a remote and real-time view of the production status through a web interface.
The new solution helps in prioritizing the tasks and shortens the reaction time to different problems arising in production. eKanban is also a great planning tool, as it gives us a complete process overview, Aki explains.
The eKanban system gets all the production information it needs straight from the company’s MES, where the daily consumption levels of each process, as well as the minimum and maximum storage levels, are defined. Separate eKanban views, visualizing the interim storage levels, can be reviewed through MES which enables effective inventory management.
The eKanban solution is designed for tracking the production, not to automatically assign anything. It is always the team, the people, who make the decisions based on the information they receive. However, the solution helps to improve tracking and optimizing operations, Aki says.
Advanced work management
Moreover, the eKanban solution enhances work management.
Compared to manual Kanban systems, eKanban gives additional information on storage unit rotations, events and even stock rotation history. It is valuable information for both follow-ups and for managing transportation activities and best working methods. Earlier, the material transportation could idle, and the return of cards to the Kanban boards be irregular, which caused various scheduling challenges, stockouts and unexpected changes in demand.
It was nearly impossible to find the root cause for problems and consequently improve it. Thanks to the digitised solution, we can now track every event, which supports work development and feedback giving.
While the manual Kanban boards already gave a good boost for companies in optimizing production, the new eKanban solution brings monitoring, tracking and optimizing to a remarkably higher level.
eKanban is an excellent example of how we can improve proven old methods during digital transformation.
eKanban was designed to add a remarkable value to the supply chain support operations. This was accomplished by optimizing cost-effectiveness, efficiency, and the movement of materials. Currently, Aki’s team is already developing the next generation eKanban solution, one without any physical cards or printed labels and boards. This will serve the needs of the highest automation solutions, which require visual identification instead of manual labelling or printed cards.
The operators do not even need to touch the storage units anymore, but the Electronic Shelf Label (ESL) completes the visual identification. Electronic Shelf Label is automatically updated during the manufacturing processes and events referring to RFID identifications and data communication. This way, the labels are never missing, old or wrong, and they are readable in all occasions and all the time, Aki explains.
- Bridgestone
- Bridgestone India
- Bridgestone Tyres
- Nutritional Fruit Orchard Project
- Sustainability
- Women Empowerment
Bridgestone India Launches Women-Led Orchard Project In Madhya Pradesh
- By TT News
- July 05, 2025
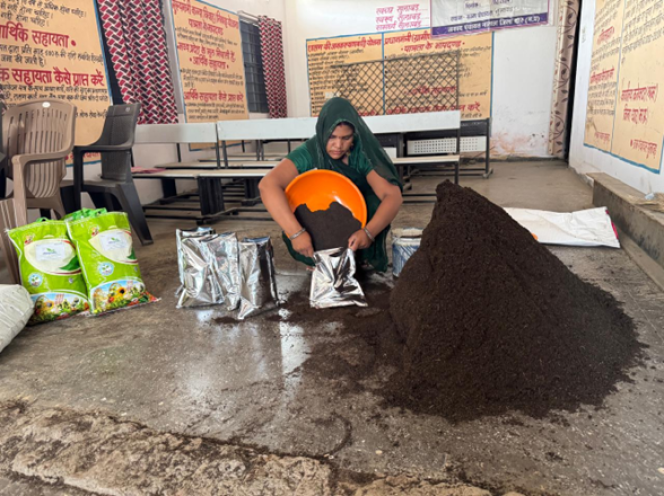
Bridgestone India has joined hands with Sagest (Society for Environment and Agricultural Sustainability) to launch the Nutritional Fruit Orchard Project in Sulawad Village, Madhya Pradesh. This women-led project improves nutrition, fosters livelihood possibilities and supports environmental sustainability. With the help of Bridgestone staff and locals, the orchard, which spans four acres, is home to more than 1,300 fruit trees of more than 15 species. It is grown using sustainable practices.
With a 96 percent survival rate in its first year, the project has enabled women to run a nursery with 1,000 saplings and turn garden waste into organic compost and insecticides, encouraging environmentally responsible farming and generating extra revenue. The ladies who are in charge of the orchard will have a reliable source of income once it is completely developed. By assisting households in growing 251 kitchen gardens, the programme also improves nutrition in Sulawad by guaranteeing that locals have access to fresh, homegrown produce. Frequent training sessions have improved environmental consciousness and community ownership.
This unique project demonstrates multi-stakeholder collaboration – Bridgestone and Sagest lead implementation, the local panchayat provided land, women manage daily operations and a nearby government school assists. By combining environmental conservation, rural development and women’s empowerment, the initiative serves as a replicable model for sustainable corporate-community partnerships.
Hiroshi Yoshizane, Managing Director, Bridgestone India, said, “True sustainability goes beyond business – it’s about empowering communities and protecting the planet. This project shows how women-led, community-driven action can create long-term impact on nutrition, livelihoods and the environment. It’s not just about planting trees; it’s about planting hope, resilience and a better future. This initiative beautifully demonstrates how community-driven, women-led environmental action can improve nutrition, generate income and protect the planet – all at the same time.”
JK Tyre & Industries Appoints Sylvain Sagot As New Director For Quality
- By TT News
- July 04, 2025
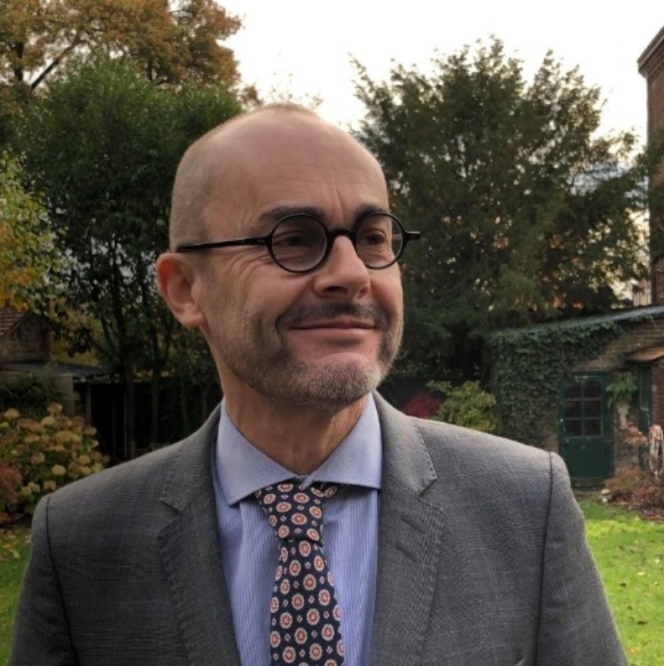
JK Tyre & Industries, one of the leading tyre manufacturers in the country, has announced the appointment of Sylvain Sagot as Director – Quality.
Sagot comes with over three decades of experience in quality assurance, process excellence and operational leadership in the automotive and tyre industry. A French national, he began his career as a Quality Engineer at Michelin Netherlands in 1991.
In 2004, he worked with Renault as a Supplier Development Consultant and went on to grow to the ranks of Supplier Performance Manager for the Renault Nissan Alliance. He also worked with Alstom and Gajah Tunggal, one of the biggest tyre manufacturers in Southeast Asia as QA General Manager & TBR Plant Head in Indonesia for over three years.
Sagot in his last role was the International Truck Trailer Quality & Product Safety Director at Carrier, where he spent over a decade.
JK Tyre & Industries believes that Sagot with deep expertise in supplier development, quality management systems, product safety, and OEM partnerships in large-scale manufacturing environments, will further strengthen its global operations.
Nynas Leads In Sustainability As Independent Study Rates Its Products Highly
- By TT News
- July 04, 2025
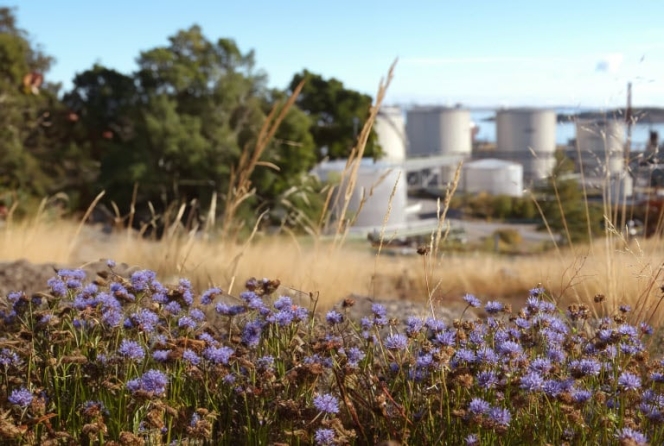
Nynas, with its strong commitment to innovation and product sustainability, recently commissioned an independent study to evaluate the environmental impact of its products across four key application areas: transformer oils, lubricating greases, tyres and bitumen binders. Conducted by Future Earth Analytics, LLC, the research revealed that many Nynas products deliver significant sustainability advantages, often surpassing industry performance benchmarks.
The study highlighted several environmental benefits across different applications. In transformer oils, certain Nynas products improve cooling efficiency and energy transmission, reducing energy losses during operation. For tyres, specific Nynas tyre oils contribute to lower rolling resistance, which helps decrease fuel consumption in vehicles. In lubricating greases, the use of naphthenic base oils reduces reliance on lithium – a resource-intensive material – while also cutting energy consumption during production. Additionally, Nynas’ strategic location near bitumen customers minimises transportation distances, thereby lowering associated emissions.
The findings underscore a substantial environmental impact: had customers opted for alternative products instead of Nynas’ offerings in 2023, an additional 740,000 tonnes of greenhouse gas emissions would have been generated. This saving is equivalent to avoiding the consumption of five million barrels of oil.
To assess these benefits, researchers employed a dual analytical framework combining Life Cycle Assessment (LCA) and Net Energy Analysis (NEA). This approach allowed for a detailed comparison of energy savings and emissions reductions across different lifecycle phases, such as cradle-to-gate and use-phase impacts. By focusing on stages where variations occur, the study provided a quantitative evaluation of how choosing Nynas products can lead to measurable energy and emissions savings compared to market alternatives. The results reinforce Nynas’ leadership in delivering sustainable solutions that support a lower-carbon future.
Marika Rangstedt, Sustainability Manager, said, “The beneficial effects are true not only for our recent circular or renewable products, but also for many of our traditional products. We are leading the way in sustainability and setting new standards for product related environmental responsibility within our industry.”
- Westlake Tyres
- Westlake Performance Tyres
- Westlake Sport RS
- Red Bull Driftbrothers
- Motorsport
- Drifting
- ADAC RAVENOL 24h Nürburgring
Westlake Performance Tyres Becomes Official Tyre Partner Of Red Bull Driftbrothers
- By TT News
- July 03, 2025
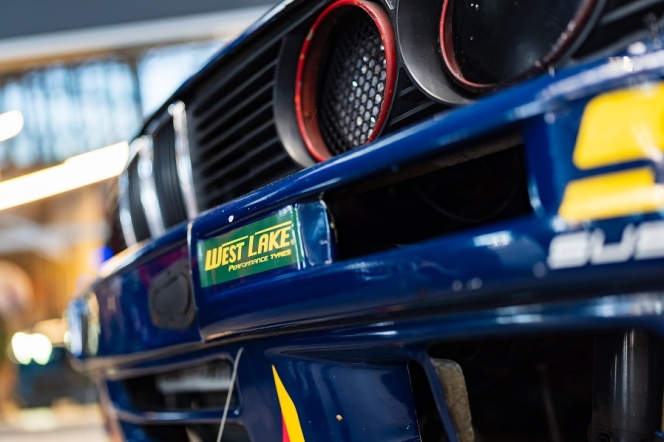
Westlake Performance Tyres, a brand of ZC Rubber, has teamed up with German motorsport team Red Bull Driftbrothers as the new official supplier and tyre partner. The company will supply its Westlake Sport RS tyres for the team’s two 1,000 hp BMW M4s.
Munich marketing agency die agentour was the driving force behind the collaboration. The Red Bull Driftbrothers and ZC Rubber have a long-term cooperation that benefits both parties in many ways. Giving the team tyres will help with technical advancements based on driver Elias Hountondji's input, among other things. The collaboration will also help ZC Rubber spread the word about the Westlake brand throughout the European market. Demonstrating the products' and technologies' performance and quality in harsh environments is also a clear signal to the European OEM and replacement market.
This year's ADAC RAVENOL 24h Nürburgring marked the debut of the new collaboration. The Red Bull Driftbrothers created a stir among the record-breaking audience when they performed a display drift in their recently tyred BMW vehicles during the pre-race of the renowned race. The Westlake Sport RS tires were especially taxed by the high track temperatures.
Henry Shen, Deputy General Manager, Zhongce Rubber Group (ZC Rubber), said, “We’re proud to be the tyre partner of Red Bull Driftbrothers. Their trust in WESTLAKE, especially the performance of our SPORT RS on the demanding drift circuit, is a powerful endorsement. This partnership is built on a shared drive to push boundaries, and we’re excited to support their passion with our technology on the global stage.”
Elias Hountondji, driver and engineer of Red Bull Driftbrothers, said, “We are very excited about the partnership with Westlake Performance Tyres and ZC Rubber. Tyres are crucial for our sport. They have to withstand extreme abuse while providing a consistently high level of grip right to the end. The Westlake Sport RS is the perfect choice for this. It is extremely stable across the entire temperature range and the entire tread depth. Even with a very low tread pattern, you still have complete confidence as a driver.”
Comments (0)
ADD COMMENT