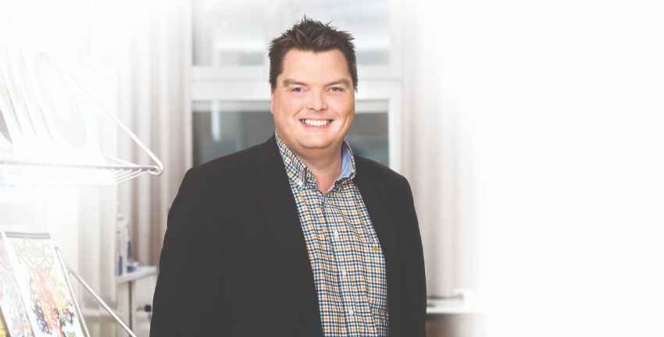
How will the collaboration with Michelin influence the future of the company? What vision do the companies share?
Michelin evaluated our recovered carbon black material in 2016. Since then, they have made significant testing of quite large volumes of our material over time to evaluate its consistency and quality. This is probably the most important parameter for any tyre manufacturer to use recovered carbon black. The interest in the technology itself started to grow as they saw that the performance of the recovered carbon black material was quite impressive. Over time, they started doing due diligence on the technology during those years. We intensified the negotiations in the early stages of 2020 and finally entered into a partnership agreement in April where Michelin invested 20 percent in Enviro. But, that was only one part of the partnership we envisioned. We also had, from the beginning, discussions about how we can provide the technology as a part of their solution to build a business model around mining tyres. This way, they could also offer their mining customers a solution for the recovery of the mining tyres. In that aspect, we negotiated regarding a joint plant project we are currently building in the Antofagasta region of Chile. We are also preparing the permitting for a plant in Uddevalla, Sweden, of 60,000-tonne ELT capacity for car and truck tyres.
In addition to that, we evaluate different technology experiences from both sides where we contribute with our experience in pyrolysis and treating end-of-life tyres in a professional way. Michelin is contributing with their extensive knowledge about developing and innovation into industrial capacity plants. What we have is a very intense collaboration on a more or less daily basis.
Going forward, we see that Michelin has a strategic ambition to replace up to 100 percent of the materials in the tyres with sustainable alternatives. Carbon black is one of the materials where we think that quite large volumes can be replaced over time. They're also involved in replacement and development of different types of oils in the tyres. From Michelin’s side, I think they have a wider interest in the recovery of all the materials in the tyres. This also aligns with our interest since we are recovering tyre pyrolysis oil and doing that quite successfully. We expect more plans in collaboration with Michelin in one way or another. Their investment in our company and the clear engagement in showing the market that they're using our material in motorcycle racing tyres in Moto E and in performance tyres for racing cars is helping us to get the acknowledgement in the market. This is important for our growth and our expansion plan.
How are you matching the quality and consistency of the recovered carbon black to virgin carbon black? Can you also please elaborate on the collaboration with AnvaPolytech, where Enviro completely replaced virgin carbon black used in Volvo's rubber components back in 2015?
We are using our patented batch process, which is a fixed batch process. The technology that we are using was developed for over 20 years to maintain control of the pyrolysis process. We can make sure that the result of the pyrolysis in the material is consistent, which means that we are not creating new carbon, as you easily do when you have a continuous process, and we are making sure that the pyrolysis process has evaporated all the volatiles out of the carbon fraction. This is very important and we control this with the system in multiple parameters that we measure during the process. We also have a significant quality control system downstream. So, in the post process of the pyrolysis, we do multiple quality checks. Before each shipment, we have ASTM standard controls for about 10 different parameters where we compare to the industry ASTM standard normally used for carbon black. There are a few ASTM measurements used for virgin carbon black that are not applicable for all recovered carbon black products, but the majority of the tests can be similar and we keep a very high consistency there. This is also one of the main achievements of the company since January 2016. We made the first commercial delivery to AnvaPolytech and they are a rubber component supplier to Volvo Cars. They have been involved with us before the commercial deliveries in the research and development of the material for rubber components. They were also involved in lots of different types of testing, where meeting the automotive standard for EPDM rubber components was a very significant part, and also got the final approval from Volvo Cars to replace the material. Since 2016, we have replaced 100 percent carbon black in those components with our material. I think it's now more than 100 million components delivered from Anva to Volvo Cars.
The gas produced during the pyrolysis process is used to fuel the machinery itself. Is there a commercial value for the gas in this market and are you exploring those business verticals?
It is a very valid question; we are producing new pyrolysis gas, and in the process, we condense out the oil, but there will be a fraction of gas that is not condensable. That gas is the excess gas that we use for the next pyrolysis phase. In our current plant at Åsensbruk, we use the excess gas and part of the oil to power the main process and the post process for heating purposes. In the new plants we will be building, for instance, one in Sweden, we plan to start production in the fourth quarter of 2023, where we will use green energy from wind, solar, water and waste to provide energy. In this case, the excess gas will be used only to heat the dryer system in the post process. Does it have a commercial value? I think some markets do; it might be used also in-turn to produce energy or electricity, but at the moment, this is not something that we are exploring further in detail.
The company recently received two ISCC certifications, one for the pyrolysis oil and the other for the carbon black. What were the challenges in earning the certifications and are there any other benchmarks that you're targeting for any other product in the future?
We are very proud to be the first to achieve the certification for the recovered carbon black. It is an important step for both the certification and for us as a company. We are already seeing some of the players in the tyre industry looking to certify according to ISCC now. This means that there will be a higher value in connection to using that type of material. There are always challenges with being certified and the most challenging maybe is to follow the certification requirements in terms of how, when and where to measure. We need to make sure that this is something that we can live up to when we are audited annually. We must also commit resources and capabilities to do this. We also needed to involve our supplier of tyre material, which, in Sweden, are Ragn-Sells. They are also audited by the certifier.
Enviro was evaluating business prospects in India. What is the current status of opening a full-size plant? Pyrolysis is banned in India across almost all states by the pollution board, and we're seeing various companies being ordered to shut down plants. Where does Enviro fit in and what are the developments?
Yes, we have been conducting meetings together with the Swedish Energy Agency, Swedish Export Organization, Business Sweden and a few other organisations including India-Sweden Innovations Accelerator and Confederation of Indian Industry in India. We have been exploring the Indian market for many multiple axles, and during the last two years, we are meeting with all the major tyre producers, both local and international. We are meeting with oil companies downstream who are potential customers for oil. We are meeting with waste treatment and tyre treatment companies locally and also making presentations to most local governments. However, we feel it is a bit too early for us to enter India on a more massive basis.
We have decided strategically that we will start with Europe followed by probably the US in the next phase. I think that will help India to monitor what is happening with the technology and how it can be a part of the system in those markets. We can then use that as a showcase for creating a sustainable and long-term system for the Indian market. We hope that this display of the system will be appreciated by the players in India to implement and also be some kind of inspiration to make that happen. In regards to pyrolysis being banned, I think it's probably a very correct decision because the pyrolysis technologies that we have seen being used in India are mainly Chinese versions where the environmental 360-degree impact has not really been considered. I think it was a very necessary decision.
The system for import and collecting for the pyrolysis industry was not really in place at that moment. But I think we can showcase together with a few of our peers in the European market that batch pyrolysis process and pyrolysis in general can be made with a very sustainable and safe technology with the highest possible emission control systems. We are hoping that by setting an example in Europe and showing both the technology and the system, maybe we will enter India in the next five years.
What are some of the constraints that you see in entering the Indian market?
I think one constraint that we are struggling with – mainly in Europe, but also in other markets – is that end-of-life tyres are viewed purely as waste materials. To really get our authorities and government regulators to understand that we are making a transition of waste materials into something that can sustainably replace fossil resources is a challenge. We are in the right direction. ISCC certification is one step.
Reach of the materials is another step. I think that transition to get aligned with the current legislation in many countries is still a hurdle. Even if it's improving, making this kind of large transition of an industry that is not really present at the moment requires financial support. Financial investors need to be willing to take a little bit of a risk to make the industry change as rapidly as it needs to. It's not enough for the tyre industry if there is one company able to provide the small volume to the market; they need multiple suppliers and large volumes to replace larger volumes of virgin material. The volume is a constraint itself. We hope, together with Michelin and other parties that we're working with, to provide larger volumes in the coming 10 years. Our ambition is to establish at least 30 plants globally in the coming decade. We also hope that our competitors are also successful in India.
What potential do you see in the Indian market, being one of the biggest automotive markets in the world, in terms of government support or the infrastructure for the products Enviro produces?
One of the opportunities is the growing automotive market. There is also a foundation of industry there in India for a long time. There is a tradition to produce tyres with a lot of knowledge, research and development around tyres and rubber materials, which I think is a very interesting potential itself. The competence around the materials in India is significant. I think the size of the market itself is an opportunity. If you choose to see the immaturity of the collection system as an opportunity, which I do, I think there is a lot of potential to establish from ground-up, a workable system with different stakeholders where I think local and national government needs to play a role, but it needs to be still on market conditions. I think the model that we will be showcasing in Europe will be attractive for both the government and local private stakeholders like the tyre industry and rubber industry.
In a broader sense, what is the future for the company and what are your goals? What are you excited about?
There are very clear targets from the tyre industry since they are consuming more than 70 to 80 percent of the carbon black material in the world. We have very clear targets for replacing fossil-originated materials with recovered or sustainable materials. We are very excited about the volume potential we see there. We have started to take steps in that direction with multiple tyre producers. The regulation in Europe and other countries to reduce the fossil content in oil products and chemical products is very positive for us. ISCC is a very important tool for the market to implement recovered and bio-based materials which have tax incentives. These enable us to launch our expansion plan, which, as I mentioned, is for the next 10 years to open 30 plants globally. We are excited that we are now in the position to work in establishing one plant with Michelin in Chile and in parallel a plant in Sweden with more or less the same time scheduled to start production. In the pipeline, we have several very interesting projects building up.
Are there other manufacturers or automotive players that are satisfied with the level of quality in your recovered carbon black? Are there any projects in the pipeline?
We have seen the interest significantly increasing in suppliers to the automotive industries and to other core manufacturers since we got the ISCC certificate for our products. But I think that we could better market what we have achieved together with Volvo in order to really get the other car brands into using more of our material. I think we have some homework to do there, because what we do is too little known to them at the moment. So there is work to be done there. We know we can achieve it. We should focus on letting them know what we can do. We are working with some other automotive manufacturers not only for the recovered carbon black but also to help them achieve their zero-emission objectives. So that could be related to oil, carbon black, steel and potentially other materials such as carbon fibre, for instance. (MT)
- Bridgestone
- Bridgestone India
- Bridgestone Tyres
- Nutritional Fruit Orchard Project
- Sustainability
- Women Empowerment
Bridgestone India Launches Women-Led Orchard Project In Madhya Pradesh
- By TT News
- July 05, 2025
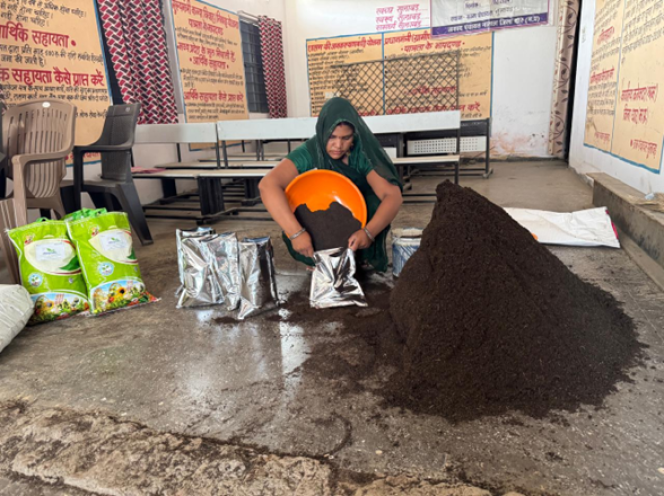
Bridgestone India has joined hands with Sagest (Society for Environment and Agricultural Sustainability) to launch the Nutritional Fruit Orchard Project in Sulawad Village, Madhya Pradesh. This women-led project improves nutrition, fosters livelihood possibilities and supports environmental sustainability. With the help of Bridgestone staff and locals, the orchard, which spans four acres, is home to more than 1,300 fruit trees of more than 15 species. It is grown using sustainable practices.
With a 96 percent survival rate in its first year, the project has enabled women to run a nursery with 1,000 saplings and turn garden waste into organic compost and insecticides, encouraging environmentally responsible farming and generating extra revenue. The ladies who are in charge of the orchard will have a reliable source of income once it is completely developed. By assisting households in growing 251 kitchen gardens, the programme also improves nutrition in Sulawad by guaranteeing that locals have access to fresh, homegrown produce. Frequent training sessions have improved environmental consciousness and community ownership.
This unique project demonstrates multi-stakeholder collaboration – Bridgestone and Sagest lead implementation, the local panchayat provided land, women manage daily operations and a nearby government school assists. By combining environmental conservation, rural development and women’s empowerment, the initiative serves as a replicable model for sustainable corporate-community partnerships.
Hiroshi Yoshizane, Managing Director, Bridgestone India, said, “True sustainability goes beyond business – it’s about empowering communities and protecting the planet. This project shows how women-led, community-driven action can create long-term impact on nutrition, livelihoods and the environment. It’s not just about planting trees; it’s about planting hope, resilience and a better future. This initiative beautifully demonstrates how community-driven, women-led environmental action can improve nutrition, generate income and protect the planet – all at the same time.”
JK Tyre & Industries Appoints Sylvain Sagot As New Director For Quality
- By TT News
- July 04, 2025
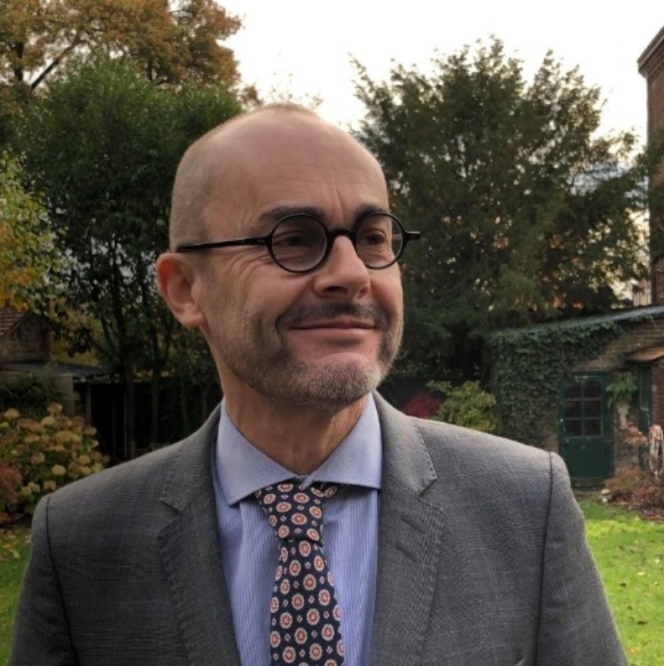
JK Tyre & Industries, one of the leading tyre manufacturers in the country, has announced the appointment of Sylvain Sagot as Director – Quality.
Sagot comes with over three decades of experience in quality assurance, process excellence and operational leadership in the automotive and tyre industry. A French national, he began his career as a Quality Engineer at Michelin Netherlands in 1991.
In 2004, he worked with Renault as a Supplier Development Consultant and went on to grow to the ranks of Supplier Performance Manager for the Renault Nissan Alliance. He also worked with Alstom and Gajah Tunggal, one of the biggest tyre manufacturers in Southeast Asia as QA General Manager & TBR Plant Head in Indonesia for over three years.
Sagot in his last role was the International Truck Trailer Quality & Product Safety Director at Carrier, where he spent over a decade.
JK Tyre & Industries believes that Sagot with deep expertise in supplier development, quality management systems, product safety, and OEM partnerships in large-scale manufacturing environments, will further strengthen its global operations.
Nynas Leads In Sustainability As Independent Study Rates Its Products Highly
- By TT News
- July 04, 2025
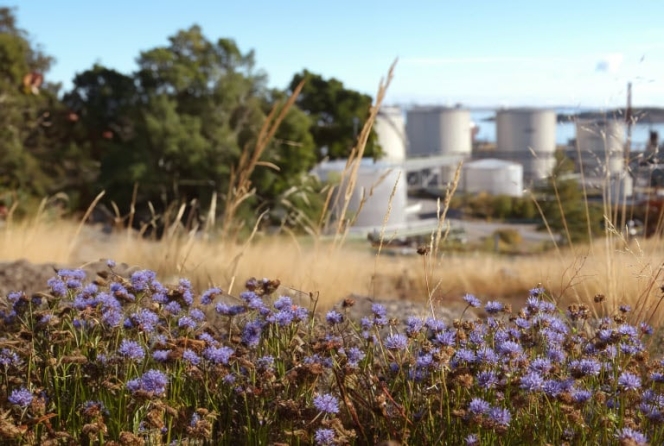
Nynas, with its strong commitment to innovation and product sustainability, recently commissioned an independent study to evaluate the environmental impact of its products across four key application areas: transformer oils, lubricating greases, tyres and bitumen binders. Conducted by Future Earth Analytics, LLC, the research revealed that many Nynas products deliver significant sustainability advantages, often surpassing industry performance benchmarks.
The study highlighted several environmental benefits across different applications. In transformer oils, certain Nynas products improve cooling efficiency and energy transmission, reducing energy losses during operation. For tyres, specific Nynas tyre oils contribute to lower rolling resistance, which helps decrease fuel consumption in vehicles. In lubricating greases, the use of naphthenic base oils reduces reliance on lithium – a resource-intensive material – while also cutting energy consumption during production. Additionally, Nynas’ strategic location near bitumen customers minimises transportation distances, thereby lowering associated emissions.
The findings underscore a substantial environmental impact: had customers opted for alternative products instead of Nynas’ offerings in 2023, an additional 740,000 tonnes of greenhouse gas emissions would have been generated. This saving is equivalent to avoiding the consumption of five million barrels of oil.
To assess these benefits, researchers employed a dual analytical framework combining Life Cycle Assessment (LCA) and Net Energy Analysis (NEA). This approach allowed for a detailed comparison of energy savings and emissions reductions across different lifecycle phases, such as cradle-to-gate and use-phase impacts. By focusing on stages where variations occur, the study provided a quantitative evaluation of how choosing Nynas products can lead to measurable energy and emissions savings compared to market alternatives. The results reinforce Nynas’ leadership in delivering sustainable solutions that support a lower-carbon future.
Marika Rangstedt, Sustainability Manager, said, “The beneficial effects are true not only for our recent circular or renewable products, but also for many of our traditional products. We are leading the way in sustainability and setting new standards for product related environmental responsibility within our industry.”
- Westlake Tyres
- Westlake Performance Tyres
- Westlake Sport RS
- Red Bull Driftbrothers
- Motorsport
- Drifting
- ADAC RAVENOL 24h Nürburgring
Westlake Performance Tyres Becomes Official Tyre Partner Of Red Bull Driftbrothers
- By TT News
- July 03, 2025
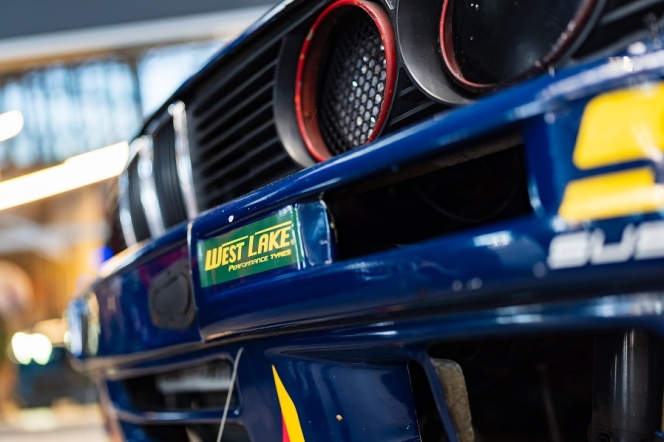
Westlake Performance Tyres, a brand of ZC Rubber, has teamed up with German motorsport team Red Bull Driftbrothers as the new official supplier and tyre partner. The company will supply its Westlake Sport RS tyres for the team’s two 1,000 hp BMW M4s.
Munich marketing agency die agentour was the driving force behind the collaboration. The Red Bull Driftbrothers and ZC Rubber have a long-term cooperation that benefits both parties in many ways. Giving the team tyres will help with technical advancements based on driver Elias Hountondji's input, among other things. The collaboration will also help ZC Rubber spread the word about the Westlake brand throughout the European market. Demonstrating the products' and technologies' performance and quality in harsh environments is also a clear signal to the European OEM and replacement market.
This year's ADAC RAVENOL 24h Nürburgring marked the debut of the new collaboration. The Red Bull Driftbrothers created a stir among the record-breaking audience when they performed a display drift in their recently tyred BMW vehicles during the pre-race of the renowned race. The Westlake Sport RS tires were especially taxed by the high track temperatures.
Henry Shen, Deputy General Manager, Zhongce Rubber Group (ZC Rubber), said, “We’re proud to be the tyre partner of Red Bull Driftbrothers. Their trust in WESTLAKE, especially the performance of our SPORT RS on the demanding drift circuit, is a powerful endorsement. This partnership is built on a shared drive to push boundaries, and we’re excited to support their passion with our technology on the global stage.”
Elias Hountondji, driver and engineer of Red Bull Driftbrothers, said, “We are very excited about the partnership with Westlake Performance Tyres and ZC Rubber. Tyres are crucial for our sport. They have to withstand extreme abuse while providing a consistently high level of grip right to the end. The Westlake Sport RS is the perfect choice for this. It is extremely stable across the entire temperature range and the entire tread depth. Even with a very low tread pattern, you still have complete confidence as a driver.”
Comments (0)
ADD COMMENT